Forecasting the cutting force in end milling
DOI:
https://doi.org/10.15587/1729-4061.2024.303791Keywords:
cutting force, end milling, digital simulation, empirical model identificationAbstract
The object of this study is the process of end milling, taking into account the discontinuity of the process, simultaneous cutting with several flutes arranged in a spiral, tool runout, and feedback in the elastic machining system, in particular, for the depth of cutting. The subject of the study is the cutting force and identification of its empirical model. During identification, the cutting force coefficient is automatically determined when matching the theoretical and experimental oscillograms of the cutting force component. The reported results related to forecasting the cutting force at end milling are based on a mechanistic approach and involve the process modeling method for forecasting. The simulation uses an algorithm for representing the interaction of the cutter flutes workpiece engagement, based on the scan of the cutter according to the rotation angle coordinate. The algorithm makes it possible to identify empirical coefficients and exponents of the cutting force model based on experimental oscillograms of cutting force components. The built model is implemented in an application program and owing to the representation of the machining system in the form of a closed structural diagram, it allows predicting the elastic displacement, which will determine the actual cutting depth. The developed program under an interactive mode using digital files of experimental cutting force components makes it possible to perform model identification and predict cutting force components with an error of 4.6 %. The adequacy of the algorithms was confirmed by measuring the profile of the machined surface in the places where the cutting mode changed with the feed stopped. The developed simulation algorithm makes it possible to take into account the simultaneous cutting by several flutes arranged in a spiral, the runout of the tool, and the feedback in the elastic machining system, in particular, the depth of cutting
References
- CNC Machining For Aerospace Industry: Complete Guide To Know. Available at: https://waykenrm.com/blogs/cnc-machining-for-aerospace-industry/
- Joshi, S. N., Bolar, G. (2020). Influence of End Mill Geometry on Milling Force and Surface Integrity While Machining Low Rigidity Parts. Journal of The Institution of Engineers (India): Series C, 102 (6), 1503–1511. https://doi.org/10.1007/s40032-020-00608-0
- Altintas, Y. (2012). Manufacturing Automation. Cambridge University Press. https://doi.org/10.1017/cbo9780511843723
- Perez, H., Diez, E., Marquez, J. J., Vizan, A. (2013). An enhanced method for cutting force estimation in peripheral milling. The International Journal of Advanced Manufacturing Technology, 69 (5-8), 1731–1741. https://doi.org/10.1007/s00170-013-5153-0
- Liu, S., Jin, S. (2020). Predicting milling force variation in time and space domain for multi-toothed face milling. The International Journal of Advanced Manufacturing Technology, 108 (7-8), 2269–2283. https://doi.org/10.1007/s00170-020-05319-5
- Janota, M., Kolar, P., Sulitka, M. (2019). Operational method for identification of specific cutting force during milling. MM Science Journal, 2019 (04), 3250–3257. https://doi.org/10.17973/mmsj.2019_11_2019078
- Duan, Z., Li, C., Ding, W., Zhang, Y., Yang, M., Gao, T., Cao, H. et al. (2021). Milling Force Model for Aviation Aluminum Alloy: Academic Insight and Perspective Analysis. Chinese Journal of Mechanical Engineering, 34 (1). https://doi.org/10.1186/s10033-021-00536-9
- Kaneko, K., Shimizu, J., Shirase, K. (2022). A Voxel-Based End Milling Simulation Method to Analyze the Elastic Deformation of a Workpiece. Journal of Manufacturing Science and Engineering, 145 (1). https://doi.org/10.1115/1.4055794
- Denkena, B., Dahlmann, D., Boujnah, H. (2017). Tool Deflection Control by a Sensory Spindle Slide for Milling Machine Tools. Procedia CIRP, 62, 329–334. https://doi.org/10.1016/j.procir.2016.06.059
- Petrakov, Y., Romanov, Y. (2023). Ensuring accuracy of contour milling on CNC machines. Mechanics and Advanced Technologies, 7 (1), 51–60. https://doi.org/10.20535/2521-1943.2023.7.1.276162
- Nishida, I., Okumura, R., Sato, R., Shirase, K. (2018). Cutting Force and Finish Surface Simulation of End Milling Operation in Consideration of Static Tool Deflection by Using Voxel Model. Procedia CIRP, 77, 574–577. https://doi.org/10.1016/j.procir.2018.08.218
- Petrakov, Y., Ohrimenko, O., Sikailo, M. (2023). Ensuring the stability of machining when using end mills. Eastern-European Journal of Enterprise Technologies, 5 (1 (125)), 73–80. https://doi.org/10.15587/1729-4061.2023.287009
- Mamedov, A., Layegh K., S. E., Lazoglu, I. (2013). Machining Forces and Tool Deflections in Micro Milling. Procedia CIRP, 8, 147–151. https://doi.org/10.1016/j.procir.2013.06.080
- Kaneko, K., Inui, M., Nishida, I. (2023). Fast simulation of machining error induced by elastic deformation of tool system in end milling. Journal of Advanced Mechanical Design, Systems, and Manufacturing, 17 (3), JAMDSM0035–JAMDSM0035. https://doi.org/10.1299/jamdsm.2023jamdsm0035
- Zhou, L., Yang, C., Peng, F., Yan, R., Deng, B., Liu, M. (2018). Prediction of flexible cutting forces and tool deflections for general micro end mill considering tool run-out and deflection feedback. The International Journal of Advanced Manufacturing Technology, 96 (1-4), 1415–1428. https://doi.org/10.1007/s00170-018-1693-7
- Petrakov, Y., Okhrimenko, O., Sikailo, M., Myhovych, A. (2023). Cutting Forces Simulation for End Milling. Journal of Engineering Sciences, 10 (2), A27–A33. https://doi.org/10.21272/jes.2023.10(2).a4
- Cai, H., Mao, X., Li, B., Luo, B. (2014). Estimation of FRFs of machine tools in output-only modal analysis. The International Journal of Advanced Manufacturing Technology, 77 (1-4), 117–130. https://doi.org/10.1007/s00170-014-6439-6
- Machining handbook: the companion for every machining professional. Available at: https://www.hoffmann-group.com/GB/en/houk/know-how/machining-handbook/e/61245/
- Saffar, R. J., Razfar, M. R. (2010). Simulation of end milling operation for predicting cutting forces to minimize tool deflection by genetic algorithm. Machining Science and Technology, 14 (1), 81–101. https://doi.org/10.1080/10910340903586483
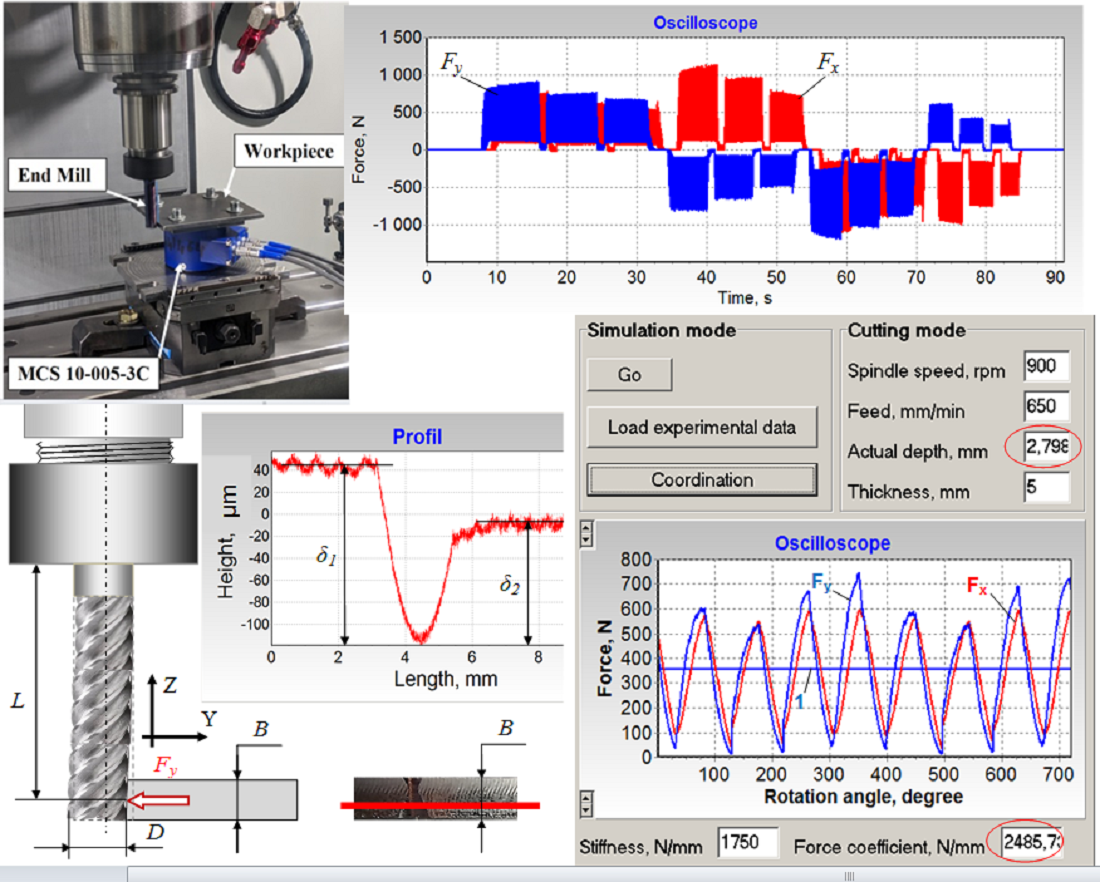
Downloads
Published
How to Cite
Issue
Section
License
Copyright (c) 2024 Yuri Petrakov, Olexander Ohrimenko, Maksym Gladskyi

This work is licensed under a Creative Commons Attribution 4.0 International License.
The consolidation and conditions for the transfer of copyright (identification of authorship) is carried out in the License Agreement. In particular, the authors reserve the right to the authorship of their manuscript and transfer the first publication of this work to the journal under the terms of the Creative Commons CC BY license. At the same time, they have the right to conclude on their own additional agreements concerning the non-exclusive distribution of the work in the form in which it was published by this journal, but provided that the link to the first publication of the article in this journal is preserved.
A license agreement is a document in which the author warrants that he/she owns all copyright for the work (manuscript, article, etc.).
The authors, signing the License Agreement with TECHNOLOGY CENTER PC, have all rights to the further use of their work, provided that they link to our edition in which the work was published.
According to the terms of the License Agreement, the Publisher TECHNOLOGY CENTER PC does not take away your copyrights and receives permission from the authors to use and dissemination of the publication through the world's scientific resources (own electronic resources, scientometric databases, repositories, libraries, etc.).
In the absence of a signed License Agreement or in the absence of this agreement of identifiers allowing to identify the identity of the author, the editors have no right to work with the manuscript.
It is important to remember that there is another type of agreement between authors and publishers – when copyright is transferred from the authors to the publisher. In this case, the authors lose ownership of their work and may not use it in any way.