Heat flow density measurement during non-destructive testing
DOI:
https://doi.org/10.15587/1729-4061.2024.304597Keywords:
heat flow meter, thermoelectric battery converter, copper-constantan thermocouple, non-destructive methodAbstract
The object of the study is the development of a device capable of accurately and reliably measuring heat flux density in various environments. The development of a heat flux density meter designed for non-destructive analysis of thermal processes in various fields of application is presented.
The developed device is intended for evaluating the thermal insulation condition of underground pipelines. The functionality of the heat flow device relies on comparing standard temperature values with experimental ones measured on the soil surface. To ensure accurate and reliable measurement of heat flux density, the basis is a thermoelectric battery converter, which uses the auxiliary wall method. The heat flow density measuring device is constructed in the shape of a restricted cylinder, with one base serving as the working surface, while the second base establishes thermal contact with the body at ambient temperature. Embedded heaters enable the generation of heat flow through the thermoelectric sensor in directions perpendicular to its base. For calibrating the heat flux device, experiments were conducted using a standard copper-constantan calibration table. Temperature increments were determined from thermo electromotive force, and tests were performed on an existing heating network. The conducted measurements validate the fundamental feasibility of employing the proposed device for implementing the non-destructive thermal testing method on underground heating mains.
The results of the experiment can be used not only for research, but also for monitoring and regulating processes in various fields of science and technology. The developed heat flux meter promises a significant contribution to the development of modern methods for analyzing thermal processes.
The dimensions of the thermoelectric battery converter are also determined and the coefficient (kq) should be in the range from 4.0 to 12.0 W/(m2⋅mV), and the electrical resistance should be in the range of 12–20 kOhm
References
- Peter, L. (2020). Development of a non-destructive testing method for thermal assessment of a district heating network. Chalmers University of Technology, 34. Available at: https://research.chalmers.se/publication/515569/file/515569_Fulltext.pdf
- Standard Test Method for Steady-State Heat Flux Measurements and Thermal Transmission Properties by Means of the Guarded-Hot-Plate Apparatus: ASTM C177-10.
- McAfee, K., Sunderland, P. B., Rabin, O. (2023). A heat flux sensor leveraging the transverse Seebeck effect in elemental antimony. Sensors and Actuators A: Physical, 363, 114729. https://doi.org/10.1016/j.sna.2023.114729
- Pullins, C. A., Diller, T. E. (2010). In situ High Temperature Heat Flux Sensor Calibration. International Journal of Heat and Mass Transfer, 53 (17-18), 3429–3438. https://doi.org/10.1016/j.ijheatmasstransfer.2010.03.042
- Saidi, A., Kim, J. (2004). Heat flux sensor with minimal impact on boundary conditions. Experimental Thermal and Fluid Science, 28 (8), 903–908. https://doi.org/10.1016/j.expthermflusci.2004.01.004
- Akoshima, M. (2021). Developement of an apparatus for practical calibration of heat flux sensors. Measurement: Sensors, 18, 100343. https://doi.org/10.1016/j.measen.2021.100343
- Pountney, O. J., Patinios, M., Tang, H., Luberti, D., Sangan, C. M., Scobie, J. A. et al. (2021). Calibration of thermopile heat flux gauges using a physically-based equation. Proceedings of the Institution of Mechanical Engineers, Part A: Journal of Power and Energy, 235 (7), 1806–1816. https://doi.org/10.1177/0957650920982103
- Fralick, G., Wrbanek, J., Blaha, C. (2002). Thin Film Heat Flux Improved Design. National Aeronautics and Space Administration, 211566. Available at: https://ntrs.nasa.gov/api/citations/20020082950/downloads/20020082950.pdf
- Azerou, B., Garnier, B., Lahmar, J. (2012). Thin film heat flux sensors for accurate transient and unidirectional heat transfer analysis. Journal of Physics: Conference Series, 395, 012084. https://doi.org/10.1088/1742-6596/395/1/012084
- Kava, M. P., Patel, A. (2023). Design Development and Performance of a Heat Flux Meter Subjected to a Steady State Heat Flux Conditions. Vol. IV Mechanical Engineering, Metallurgical & Materials Engineering, Textile Engineering. Maharaja Sayajirao University of Baroda. Available at: https://www.researchgate.net/publication/370074617_Design_Development_and_Performance_of_a_Heat_Flux_Meter_Subjected_to_a_Steady_State_Heat_Flux_Conditions
- Diller, T. E. (2015). Heat Flux Measurement. Mechanical Engineers’ Handbook, 1–27. https://doi.org/10.1002/9781118985960.meh407
- Ewing, J., Gifford, A., Hubble, D., Vlachos, P., Wicks, A., Diller, T. (2010). A direct-measurement thin-film heat flux sensor array. Measurement Science and Technology, 21 (10), 105201. https://doi.org/10.1088/0957-0233/21/10/105201
- Karabekova, D. Zh., Kissabekova, P. A., Khassenov, A. K., Azatbek, Sh. (2021). Pat. No. 6393 RK. A device for measuring heat flow. No. 021/0315.2; declareted: 01.04.2021; published: 03.09.2021.
- Karabekova, D. Zh., Kissabekova, P. A., Kucheruk, V. Yu., Mussenova, E. K., Azatbek, Sh. (2022). Main characteristics of the heat flow meter. Eurasian Physical Technical Journal, 19 (2 (40)), 71–74. https://doi.org/10.31489/2022no2/71-74
- Karabekova, D. Zh., Kissabekova, P. A., Nussupbekov, B. R., Khassenov, A. K. (2021). Analysis of the Insulation State of Underground Pipelines in the Heating Network. Thermal Engineering, 68 (10), 802–805. https://doi.org/10.1134/s0040601521100013
- Kissabekova, P. A., Karabekova, D. Zh., Khassenov, A. K., Kucheruk, V. Yu., Kudusov, A. S., Kyzdarbekova, Sh. S. (2023). Theoretical foundations of the construction of the operation of heat flow devices. Bulletin of the Karaganda University “Physics Series,” 1 (109), 80–87. https://doi.org/10.31489/2023ph1/80-87
- Nussupbekov, B. R., Karabekova, D. Zh., Khassenov, A. K., Nussupbekov, U. B. (2016). Pat. No. 1588 RK. Heat flow meter. published: 29.07.2016.
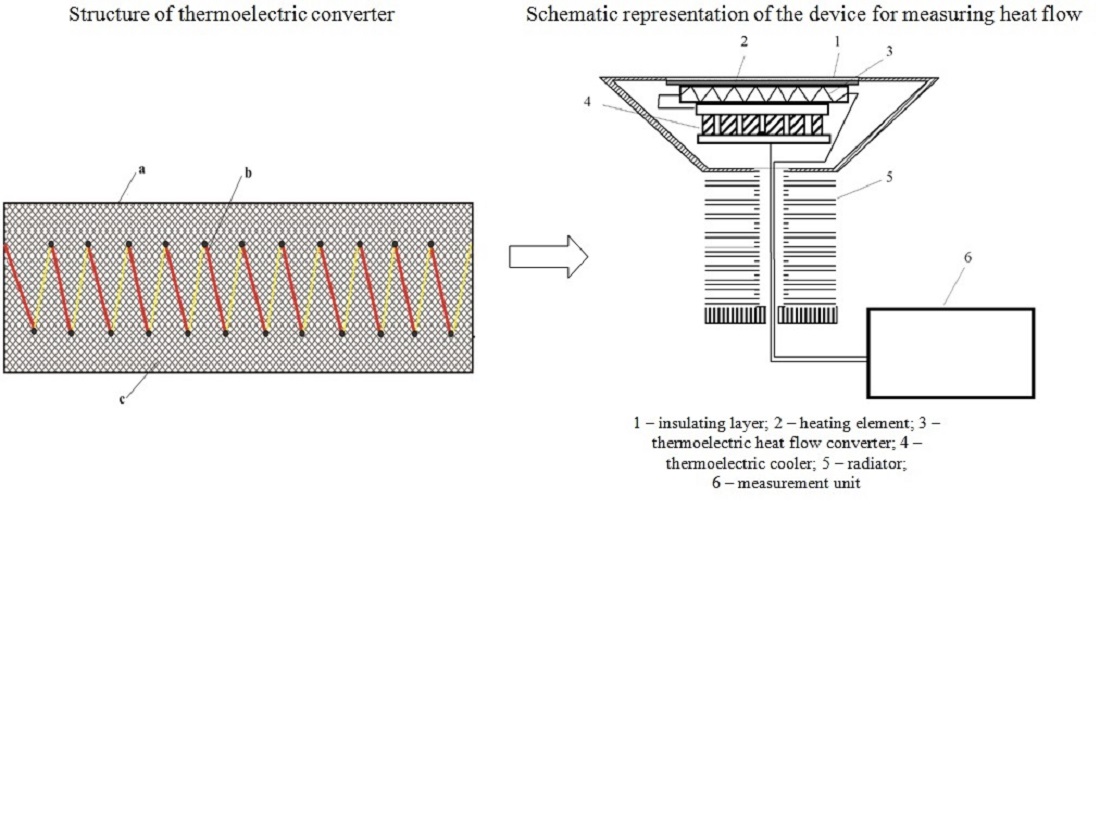
Downloads
Published
How to Cite
Issue
Section
License
Copyright (c) 2024 Dana Karabekova, Perizat Kissabekova, Ayanbergen Khassenov, Volodymyr Kucheruk, Arystan Kudussov

This work is licensed under a Creative Commons Attribution 4.0 International License.
The consolidation and conditions for the transfer of copyright (identification of authorship) is carried out in the License Agreement. In particular, the authors reserve the right to the authorship of their manuscript and transfer the first publication of this work to the journal under the terms of the Creative Commons CC BY license. At the same time, they have the right to conclude on their own additional agreements concerning the non-exclusive distribution of the work in the form in which it was published by this journal, but provided that the link to the first publication of the article in this journal is preserved.
A license agreement is a document in which the author warrants that he/she owns all copyright for the work (manuscript, article, etc.).
The authors, signing the License Agreement with TECHNOLOGY CENTER PC, have all rights to the further use of their work, provided that they link to our edition in which the work was published.
According to the terms of the License Agreement, the Publisher TECHNOLOGY CENTER PC does not take away your copyrights and receives permission from the authors to use and dissemination of the publication through the world's scientific resources (own electronic resources, scientometric databases, repositories, libraries, etc.).
In the absence of a signed License Agreement or in the absence of this agreement of identifiers allowing to identify the identity of the author, the editors have no right to work with the manuscript.
It is important to remember that there is another type of agreement between authors and publishers – when copyright is transferred from the authors to the publisher. In this case, the authors lose ownership of their work and may not use it in any way.