Effect of the technological parameters of plasma-arc spraying of flux-cored wire on the structure and properties of intermetallide coatings based on Fe3Al
DOI:
https://doi.org/10.15587/1729-4061.2023.274062Keywords:
plasma-arc spraying, flux-cored wires, intermetallide type coatings, corrosion resistanceAbstract
Existing techniques for applying intermetallide layers are characterized by low productivity, difficulties associated with the maintenance and operation of technological equipment, as well as significant costs for the purchase of materials for spraying. Therefore, modern science shows considerable interest in the development of new, highly effective technologies to form intermetallide coatings on the surface of articles. Such promising techniques include the technology of plasma-arc spraying (PAS) of flux-cored wires.
This technique has a number of significant advantages, namely high performance, relative simplicity, as well as the affordability of equipment and materials for coating. This paper reports a study into the structure and properties of coatings obtained by flux-cored wire PAS, in which the steel sheath and aluminum powder filler interact when heated with the exothermic effect of Fe3Al synthesis. The influence of technological parameters of PAS process on the structure and properties of Fe-Al coatings was investigated by means of mathematical planning of the experiment. It was found that in all samples the main phase is an intermetallide of the Fe3Al type. Tests for gas-abrasive wear resistance at room temperature showed that the wear resistance of coatings exceeds the stability of steel S235 by an average of 2 times. As a result of studying the electrochemical properties in a 3-% aqueous solution of NaCl and in a 0.5-% solution of H2SO4, the score of corrosion resistance for these media was determined, which was, respectively, 4 and 5 (coatings belong to the group of "resistant"). In this regard, the practical use of coatings based on the Fe3Al intermetallide is recommended for protection against oxidation, corrosion, and gas-abrasive wear of components and assemblies in the heat power industry (heat exchanger pipes, catalytic converters, steam turbine blades, shut-off valves, etc.)
References
- Aliofkhazraei, M. (Ed.) (2018). Intermetallic Compounds - Formation and Applications. IntechOpen. doi: https://doi.org/10.5772/intechopen.68256
- Zamanzade, M., Barnoush, A., Motz, C. (2016). A Review on the Properties of Iron Aluminide Intermetallics. Crystals, 6 (1), 10. doi: https://doi.org/10.3390/cryst6010010
- Borisov, Yu. S., Borisova, A. L., Vigilianska, N. V., Grіshchenko, О. P., Kolomytsev, M. V. (2020). Coatings based on Fe–Al intermetallics produced by the methods of plasma and supersonic air-gas plasma spraying. Automatic Welding, 7, 32–40. doi: https://doi.org/10.37434/as2020.07.04
- Palm, M., Stein, F., Dehm, G. (2019). Iron Aluminides. Annual Review of Materials Research, 49 (1), 297–326. doi: https://doi.org/10.1146/annurev-matsci-070218-125911
- Deevi, S. C. (2021). Advanced intermetallic iron aluminide coatings for high temperature applications. Progress in Materials Science, 118, 100769. doi: https://doi.org/10.1016/j.pmatsci.2020.100769
- Pougoum, F., Qian, J., Martinu, L., Klemberg-Sapieha, J., Zhou, Z., Li, K. Y. et al. (2019). Study of corrosion and tribocorrosion of Fe3Al-based duplex PVD/HVOF coatings against alumina in NaCl solution. Surface and Coatings Technology, 357, 774–783. doi: https://doi.org/10.1016/j.surfcoat.2018.10.060
- Enayati, M. H., Karimzadeh, F., Jafari, M., Markazi, A., Tahvilian, A. (2014). Microstructural and wear characteristics of HVOF-sprayed nanocrystalline NiAl coating. Wear, 309 (1-2), 192–199. doi: https://doi.org/10.1016/j.wear.2013.10.015
- Chmielewski, T., Siwek, P., Chmielewski, M., Piątkowska, A., Grabias, A., Golański, D. (2018). Structure and Selected Properties of Arc Sprayed Coatings Containing In-Situ Fabricated Fe-Al Intermetallic Phases. Metals, 8 (12), 1059. doi: https://doi.org/10.3390/met8121059
- Borisov, Yu. S., Borisova, A. L., Vihilianska, N. V., Demianov, I. A., Burlachenko, O. M. (2021). Electric arc spraying of intermetalic Fe–Al coatings using different solid and powder wires. Automatic Welding, 3, 17–22. doi: https://doi.org/10.37434/as2021.03.03
- Ndumia, J. N., Kang, M., Gbenontin, B. V., Lin, J., Nyambura, S. M. (2021). A Review on the Wear, Corrosion and High-Temperature Resistant Properties of Wire Arc-Sprayed Fe-Based Coatings. Nanomaterials, 11 (10), 2527. doi: https://doi.org/10.3390/nano11102527
- Korzhik, V. N., Korob, M. F. (2012). Mekhanizirovannaya liniya Plazer 30PL-W dlya plazmenno-dugovogo provolochnogo napyleniya pokrytiy na krupnogabaritnye detali tipa «val». Svarschik, 4, 13–15.
- Gulyaev, I. P., Dolmatov, A. V., Kharlamov, M. Yu., Gulyaev, P. Yu., Jordan, V. I., Krivtsun, I. V. et al. (2015). Arc-Plasma Wire Spraying: An Optical Study of Process Phenomenology. Journal of Thermal Spray Technology, 24 (8), 1566–1573. doi: https://doi.org/10.1007/s11666-015-0356-6
- Kharlamov, M. Yu., Krivtsun, I. V., Korzhyk, V. N. (2013). Dynamic Model of the Wire Dispersion Process in Plasma-Arc Spraying. Journal of Thermal Spray Technology, 23 (3), 420–430. doi: https://doi.org/10.1007/s11666-013-0027-4
- Kharlamov, M. Yu., Krivtsun, I. V., Korzhyk, V. N., Ryabovolyk, Y. V., Demyanov, O. I. (2015). Simulation of Motion, Heating, and Breakup of Molten Metal Droplets in the Plasma Jet at Plasma-Arc Spraying. Journal of Thermal Spray Technology, 24 (4), 659–670. doi: https://doi.org/10.1007/s11666-015-0216-4
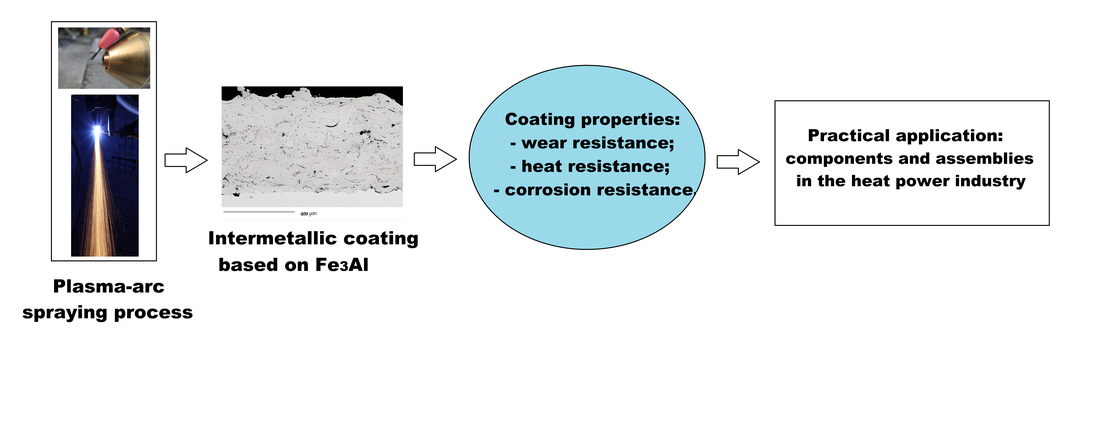
Downloads
Published
How to Cite
Issue
Section
License
Copyright (c) 2023 Volodymyr Korzhyk, Oleksii Burlachenko, Dmytro Strohonov, Nataliia Fialko, Maksym Kharlamov, Oleksandr Grishchenko, Sviatoslav Peleshenko

This work is licensed under a Creative Commons Attribution 4.0 International License.
The consolidation and conditions for the transfer of copyright (identification of authorship) is carried out in the License Agreement. In particular, the authors reserve the right to the authorship of their manuscript and transfer the first publication of this work to the journal under the terms of the Creative Commons CC BY license. At the same time, they have the right to conclude on their own additional agreements concerning the non-exclusive distribution of the work in the form in which it was published by this journal, but provided that the link to the first publication of the article in this journal is preserved.
A license agreement is a document in which the author warrants that he/she owns all copyright for the work (manuscript, article, etc.).
The authors, signing the License Agreement with TECHNOLOGY CENTER PC, have all rights to the further use of their work, provided that they link to our edition in which the work was published.
According to the terms of the License Agreement, the Publisher TECHNOLOGY CENTER PC does not take away your copyrights and receives permission from the authors to use and dissemination of the publication through the world's scientific resources (own electronic resources, scientometric databases, repositories, libraries, etc.).
In the absence of a signed License Agreement or in the absence of this agreement of identifiers allowing to identify the identity of the author, the editors have no right to work with the manuscript.
It is important to remember that there is another type of agreement between authors and publishers – when copyright is transferred from the authors to the publisher. In this case, the authors lose ownership of their work and may not use it in any way.