Визначення впливу мікро-двоетапного точкового зварювання тертям з перемішуванням з варіаційним часом витримування на різномірні латунь CuZn30-алюміній AA1100
DOI:
https://doi.org/10.15587/1729-4061.2023.276484Ключові слова:
точкове зварювання тертям, mTS-RFSSW, латунь CuZn30, AA1100, час витримкиАнотація
Зварювання та з’єднання латуні CuZn30-алюміній AA1100 було отримано за допомогою мікро-двоетапного точкового зварювання тертям з перемішуванням (mTS-RFSSW), яке було виконано для усунення отворів, утворених процесом точкового зварювання з мікротертям (mFSSW). Процес mTS-RFSSW починається з процесу зварювання mFSSW з використанням інструментів із внутрішнім діаметром штифта 2,69 мм, зовнішнім діаметром штифта 1,811 мм і діаметром плеча 4,954 мм, після чого йде другий етап процесу, який називається mTS-RFSSW, який є закриттям отвору за допомогою інструменту з безштифтовим інструментом з діаметром плеча 4,954 мм. Це дослідження мало на меті визначити вплив другої стадії витримки на механічні властивості, отримані за допомогою технології зварювання mTS-RFSSW з використанням латуні CuZn30 та алюмінію AA1100 товщиною 0,42 мм. У цьому дослідженні змінним параметром є час витримки другого етапу, який змінюється від 3 с, 4 с, 5 с і 6 с відповідно. Оптичний мікроскоп, який має на меті спостерігати за макроструктурою, показує, що в кожному процесі з’єднання утворюється висхідний гачок. Згідно зі скануючою електронною мікрофотографією, результуюче утворення різних інтерметалічних сполук (IMC) із різною товщиною відбувається в кожному варіанті часу перебування. Великий час витримки вказує на припинення IMC, що впливає на силу розтягування. В IMC, що утворюється на межі латуні CuZn30 та алюмінію AA1100, переважає понад 30 % Cu. Найвище значення твердості знаходиться в зоні перемішування, тому що утворення інтерметалічних сполук впливає на подрібнене зерно. Було отримано найвищу максимальну силу зсуву та поперечну силу розтягу 371,35 Н та 54,88 Н відповідно за час витримки 3 с. Результати властивостей руйнування після випробування на зсув внапуск показують наявність невеликих ямок з мікротріщинами, які вказують на крихке руйнування
Посилання
- Garg, A., Bhattacharya, A. (2017). Similar and dissimilar joining of AA6061-T6 and copper by single and multi-spot friction stirring. Journal of Materials Processing Technology, 250, 330–344. doi: https://doi.org/10.1016/j.jmatprotec.2017.07.029
- Irawan, Y. S., Choiron, M. A., Suprapto, W. (2021). Tensile strength and thermal cycle analysis of AA6061 friction weld joints with different diameters and various friction times. Eastern-European Journal of Enterprise Technologies, 2 (12 (110)), 15–21. doi: https://doi.org/10.15587/1729-4061.2021.227224
- Darmadi, D. B., Abdillah, F. N., Raharjo, R. (2019). Controlling the pressure force to obtain a better quality of aluminum 6061 friction stir welded joint. Eastern-European Journal of Enterprise Technologies, 3 (1 (99)), 6–10. doi: https://doi.org/10.15587/1729-4061.2019.159286
- Sajed, M. (2016). Parametric study of two-stage refilled friction stir spot welding. Journal of Manufacturing Processes, 24, 307–317. doi: https://doi.org/10.1016/j.jmapro.2016.09.011
- Chen, K., Liu, X., Ni, J. (2017). Keyhole refilled friction stir spot welding of aluminum alloy to advanced high strength steel. Journal of Materials Processing Technology, 249, 452–462. doi: https://doi.org/10.1016/j.jmatprotec.2017.06.039
- Sunar Baskoro, A., Azwar Amat, M., Andre Widiyanto, M. (2019). Effect of Tools Geometry and Dwell Time on Mechanical Properties and Macrograph of Two-Stage Refilled Friction Stir Spot Micro Weld. MATEC Web of Conferences, 269, 02002. doi: https://doi.org/10.1051/matecconf/201926902002
- Esmaeili, A., Sbarufatti, C., Hamouda, A. M. S. (2019). Characteristics of Intermetallic Compounds in Dissimilar Friction Stir Welding: A Review. Metallography, Microstructure, and Analysis, 8 (4), 445–461. doi: https://doi.org/10.1007/s13632-019-00557-w
- Zhou, L., Zhang, R. X., Li, G. H., Zhou, W. L., Huang, Y. X., Song, X. G. (2018). Effect of pin profile on microstructure and mechanical properties of friction stir spot welded Al-Cu dissimilar metals. Journal of Manufacturing Processes, 36, 1–9. doi: https://doi.org/10.1016/j.jmapro.2018.09.017
- Rupajati, P., Clarissa, K. G., Baskoro, A. S., Kiswanto, G., Winarto, W. (2021). Characteristics of Mechanical Properties and Microstructure of Micro Friction Stir Spot Welding of AA1100 and Brass. International Journal of Technology, 12 (6), 1302. doi: https://doi.org/10.14716/ijtech.v12i6.5214
- Shen, Z., Ding, Y., Chen, J., Amirkhiz, B. S., Wen, J. Z., Fu, L., Gerlich, A. P. (2019). Interfacial bonding mechanism in Al/coated steel dissimilar refill friction stir spot welds. Journal of Materials Science & Technology, 35 (6), 1027–1038. doi: https://doi.org/10.1016/j.jmst.2019.01.001
- Li, P., Chen, S., Dong, H., Ji, H., Li, Y., Guo, X. et al. (2020). Interfacial microstructure and mechanical properties of dissimilar aluminum/steel joint fabricated via refilled friction stir spot welding. Journal of Manufacturing Processes, 49, 385–396. doi: https://doi.org/10.1016/j.jmapro.2019.09.047
- Hsieh, M.-J., Lee, R.-T., Chiou, Y.-C. (2017). Friction stir spot fusion welding of low-carbon steel to aluminum alloy. Journal of Materials Processing Technology, 240, 118–125. doi: https://doi.org/10.1016/j.jmatprotec.2016.08.034
- Garg, A., Bhattacharya, A. (2017). Strength and failure analysis of similar and dissimilar friction stir spot welds: Influence of different tools and pin geometries. Materials & Design, 127, 272–286. doi: https://doi.org/10.1016/j.matdes.2017.04.084
- Dong, Z., Song, Q., Ai, X., Lv, Z. (2019). Effect of joining time on intermetallic compound thickness and mechanical properties of refill friction stir spot welded dissimilar Al/Mg alloys. Journal of Manufacturing Processes, 42, 106–112. doi: https://doi.org/10.1016/j.jmapro.2019.04.013
- Shen, Z., Ding, Y., Guo, W., Hou, W., Liu, X., Chen, H. et al. (2021). Refill Friction Stir Spot Welding Al Alloy to Copper via Pure Metallurgical Joining Mechanism. Chinese Journal of Mechanical Engineering, 34 (1). doi: https://doi.org/10.1186/s10033-021-00593-0
- Xue, P., Xiao, B. L., Ma, Z. Y. (2015). Effect of Interfacial Microstructure Evolution on Mechanical Properties and Fracture Behavior of Friction Stir-Welded Al-Cu Joints. Metallurgical and Materials Transactions A, 46 (7), 3091–3103. doi: https://doi.org/10.1007/s11661-015-2909-1
- Zhou, L., Li, G. H., Zhang, R. X., Zhou, W. L., He, W. X., Huang, Y. X., Song, X. G. (2019). Microstructure evolution and mechanical properties of friction stir spot welded dissimilar aluminum-copper joint. Journal of Alloys and Compounds, 775, 372–382. doi: https://doi.org/10.1016/j.jallcom.2018.10.045
- Mubiayi, M. P., Akinlabi, E. T. (2016). Evolving properties of friction stir spot welds between AA1060 and commercially pure copper C11000. Transactions of Nonferrous Metals Society of China, 26 (7), 1852–1862. doi: https://doi.org/10.1016/s1003-6326(16)64296-6
- Zareie Rajani, H. R., Esmaeili, A., Mohammadi, M., Sharbati, M., Givi, M. K. B. (2012). The role of Metal-Matrix Composite development During Friction Stir Welding of Aluminum to Brass in Weld Characteristics. Journal of Materials Engineering and Performance, 21 (11), 2429–2437. doi: https://doi.org/10.1007/s11665-012-0178-3
- Bisadi, H., Tavakoli, A., Tour Sangsaraki, M., Tour Sangsaraki, K. (2013). The influences of rotational and welding speeds on microstructures and mechanical properties of friction stir welded Al5083 and commercially pure copper sheets lap joints. Materials & Design, 43, 80–88. doi: https://doi.org/10.1016/j.matdes.2012.06.029
- Shiraly, M., Shamanian, M., Toroghinejad, M. R., Ahmadi Jazani, M. (2013). Effect of Tool Rotation Rate on Microstructure and Mechanical Behavior of Friction Stir Spot-Welded Al/Cu Composite. Journal of Materials Engineering and Performance, 23 (2), 413–420. doi: https://doi.org/10.1007/s11665-013-0768-8
- Li, G., Zhou, L., Zhou, W., Song, X., Huang, Y. (2019). Influence of dwell time on microstructure evolution and mechanical properties of dissimilar friction stir spot welded aluminum–copper metals. Journal of Materials Research and Technology, 8 (3), 2613–2624. doi: https://doi.org/10.1016/j.jmrt.2019.02.015
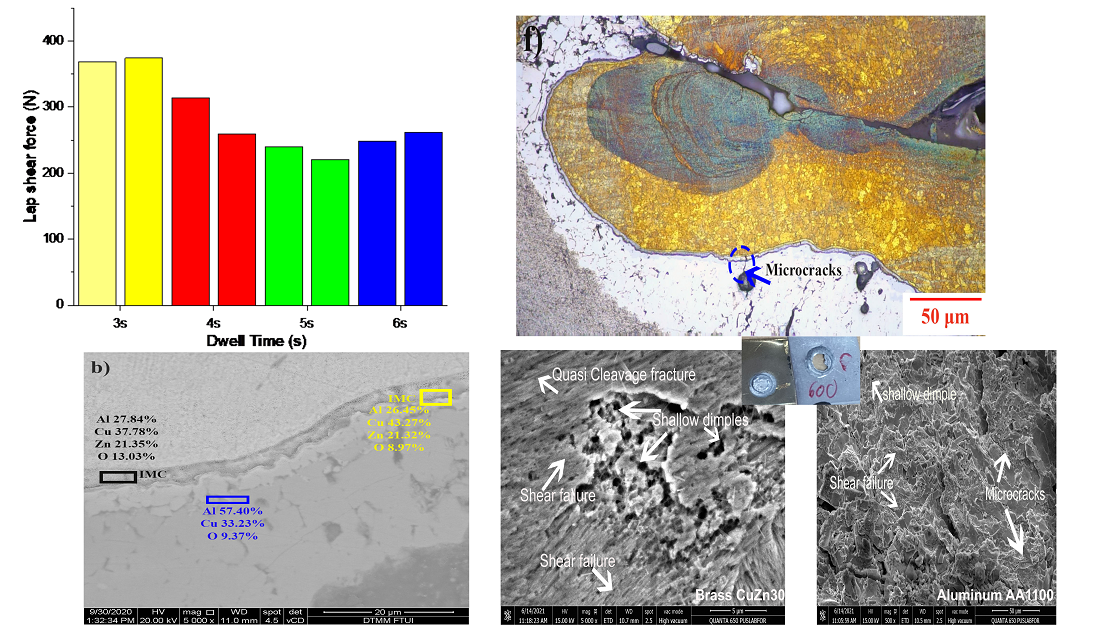
##submission.downloads##
Опубліковано
Як цитувати
Номер
Розділ
Ліцензія
Авторське право (c) 2023 Pathya Rupajati, Ario Sunar Baskoro, Latitia Dhayita Pramudito, Laksita Aji Safitri, Mohammad Azwar Amat, Gandjar Kiswanto

Ця робота ліцензується відповідно до Creative Commons Attribution 4.0 International License.
Закріплення та умови передачі авторських прав (ідентифікація авторства) здійснюється у Ліцензійному договорі. Зокрема, автори залишають за собою право на авторство свого рукопису та передають журналу право першої публікації цієї роботи на умовах ліцензії Creative Commons CC BY. При цьому вони мають право укладати самостійно додаткові угоди, що стосуються неексклюзивного поширення роботи у тому вигляді, в якому вона була опублікована цим журналом, але за умови збереження посилання на першу публікацію статті в цьому журналі.
Ліцензійний договір – це документ, в якому автор гарантує, що володіє усіма авторськими правами на твір (рукопис, статтю, тощо).
Автори, підписуючи Ліцензійний договір з ПП «ТЕХНОЛОГІЧНИЙ ЦЕНТР», мають усі права на подальше використання свого твору за умови посилання на наше видання, в якому твір опублікований. Відповідно до умов Ліцензійного договору, Видавець ПП «ТЕХНОЛОГІЧНИЙ ЦЕНТР» не забирає ваші авторські права та отримує від авторів дозвіл на використання та розповсюдження публікації через світові наукові ресурси (власні електронні ресурси, наукометричні бази даних, репозитарії, бібліотеки тощо).
За відсутності підписаного Ліцензійного договору або за відсутністю вказаних в цьому договорі ідентифікаторів, що дають змогу ідентифікувати особу автора, редакція не має права працювати з рукописом.
Важливо пам’ятати, що існує і інший тип угоди між авторами та видавцями – коли авторські права передаються від авторів до видавця. В такому разі автори втрачають права власності на свій твір та не можуть його використовувати в будь-який спосіб.