Sealing effect on corrosion resistance of boric sulfuric acid anodizing on AA2024
DOI:
https://doi.org/10.15587/1729-4061.2023.277961Keywords:
corrosion resistance, acetic acid, AA2024, boric sulfuric acid anodizationAbstract
Aluminum is widely used due to its excellent properties, lightweight and thermal conductivity. However, when used in aircraft applications, it can cause corrosion and sticking, compromising safety. To address this issue, anodizing is used to improve aluminum's corrosion resistance and adhesion. In this study, the AA2024 material was anodized using the boron-sulfuric acid anodization (BSAA) process, followed by a sealing process using acetic acid. This sealing process forms an oxide layer on the aluminum's surface, which reduces the corrosion rate. The study investigated the effects of anodization voltage and time on the results of BSAA anodization through quantitative and qualitative measurements, including corrosion resistance, potentiodynamic polarization, scanning electron microscopy (SEM), and energy dispersive X-ray spectroscopy (EDS). The results showed that samples anodized with a gasket could reduce the corrosion rate by up to 85 % compared to those without a gasket and substrate. The most significant reduction in corrosion rates occurred at an anodization voltage of 10 V and an anodization time of 15 min. The potentiodynamic test results indicated that the Tafel plot during sealing lies in the cathodic region where the corrosion current density decreases with increasing voltage. SEM observations revealed that the anodizing process could provide an oxide layer on the samples' surface, while the sealing process creates a smooth surface. EDS analysis showed that an oxide compound was formed in an oxide bond state after the sample surface was subjected to the sealing treatment. Overall, the study demonstrates the effectiveness of BSAA anodization in improving corrosion resistance and highlights the importance of considering the anodization parameters
Supporting Agency
- This research is supported by the Mechanical Engineering Laboratory, Hasanuddin University.
References
- Prasad, N. E., Wanhill, R. J. H. (Eds.) (2017). Aerospace Materials and Material Technologies. Springer. doi: https://doi.org/10.1007/978-981-10-2134-3
- Tunes, M. A., Stemper, L., Greaves, G., Uggowitzer, P. J., Pogatscher, S. (2020). Prototypic Lightweight Alloy Design for Stellar‐Radiation Environments. Advanced Science, 7 (22), 2002397. doi: https://doi.org/10.1002/advs.202002397
- Iglesias-Rubianes, L., Garcia-Vergara, S. J., Skeldon, P., Thompson, G. E., Ferguson, J., Beneke, M. (2007). Cyclic oxidation processes during anodizing of Al–Cu alloys. Electrochimica Acta, 52 (24), 7148–7157. doi: https://doi.org/10.1016/j.electacta.2007.05.052
- Hamsir, H., Sutresman, O., Arsyad, H., Syahid, M., Widyianto, A. (2022). Suppression of corrosion on stainless steel 303 with automatic impressed current cathodic protection (a-ICCP) method in simulated seawater. Eastern-European Journal of Enterprise Technologies, 6 (12 (120)), 13–21. doi: https://doi.org/10.15587/1729-4061.2022.267264
- Subbotinа, V., Sоbоl, O., Belozerov, V., Subbotin, A., Smyrnova, Y. (2020). A study of the phase-structural engineering possibilities of coatings on D16 alloy during micro-arc oxidation in electrolytes of different types. Eastern-European Journal of Enterprise Technologies, 4 (12 (106)), 14–23. doi: https://doi.org/10.15587/1729-4061.2020.209722
- Polmear, I. J. (2004). Aluminium Alloys – A Century of Age Hardening. Materials Forum. Available at: https://www.researchgate.net/publication/279898292_Aluminium_Alloys_-_A_Century_of_Age_Hardening
- Bensalah, W., Feki, M., Wery, M., Ayedi, H. F. (2011). Chemical dissolution resistance of anodic oxide layers formed on aluminum. Transactions of Nonferrous Metals Society of China, 21 (7), 1673–1679. doi: https://doi.org/10.1016/s1003-6326(11)60913-8
- Stevenson, M. F. (2013). Anodizing.
- Fratila-Apachitei, L. E., Apachitei, I., Duszczyk, J. (2006). Thermal effects associated with hard anodizing of cast aluminum alloys. Journal of Applied Electrochemistry, 36 (4), 481–486. doi: https://doi.org/10.1007/s10800-005-9102-y
- Poinern, G. E. J., Ali, N., Fawcett, D. (2011). Progress in Nano-Engineered Anodic Aluminum Oxide Membrane Development. Materials, 4 (3), 487–526. doi: https://doi.org/10.3390/ma4030487
- Zhang, L., Thompson, G. E., Curioni, M., Skeldon, P. (2013). Anodizing of Aluminum in Sulfuric Acid/Boric Acid Mixed Electrolyte. Journal of The Electrochemical Society, 160 (4), C179–C184. doi: https://doi.org/10.1149/2.032306jes
- Sanyal, S., Kim, T., Rabelo, M., Pham, D. P., Yi, J. (2022). Application of noble cerium-based anti-corrosion sealing coating approach applied on electrical insulators installed in industrial regions. Royal Society Open Science, 9 (4). doi: https://doi.org/10.1098/rsos.211786
- Haruna, T., Ikeda, T., Miyazaki, M., Nishimoto, A., Hirohata, Y. (2015). Correlation between Bound Water and Stability of Anodic Oxide Film on Aluminum. MATERIALS TRANSACTIONS, 56 (12), 2000–2005. doi: https://doi.org/10.2320/matertrans.l-m2015831
- Shen, Y. Z., Li, H. G., Tao, H. J., Ling, J., Wang, T., Tao, J. (2015). Effect of anodic films on corrosion resistance and fatigue crack initiator of 2060-T8 Al-Li alloy. International Journal of Electrochemical Science, 10 (1), 938–946. Available at: https://www.researchgate.net/publication/281996844_Effect_of_anodic_films_on_corrosion_resistance_and_fatigue_crack_initiator_of_2060-T8_Al-Li_alloy
- Veys-Renaux, D., Chahboun, N., Rocca, E. (2016). Anodizing of multiphase aluminium alloys in sulfuric acid: in-situ electrochemical behaviour and oxide properties. Electrochimica Acta, 211, 1056–1065. doi: https://doi.org/10.1016/j.electacta.2016.06.131
- Mukhurov, N. I., Zhvavyi, S. P., Terekhov, S. N., Panarin, A. Yu., Kotova, I. F., Pershukevich, P. P. et al. (2008). Influence of electrolyte composition on photoluminescent properties of anodic aluminum oxide. Journal of Applied Spectroscopy, 75 (2), 214–218. doi: https://doi.org/10.1007/s10812-008-9026-5
- Pooladi, R., Rezaei, H., Aezami, M., Sayyar, M. R. (2009). Fabrication of anodic aluminum oxide nanotemplate and investigation of their anodization parameters. Transactions of the Indian Institute of Metals, 62 (3), 241–244. doi: https://doi.org/10.1007/s12666-009-0026-9
- Fotovvati, B., Namdari, N., Dehghanghadikolaei, A. (2019). On Coating Techniques for Surface Protection: A Review. Journal of Manufacturing and Materials Processing, 3 (1), 28. doi: https://doi.org/10.3390/jmmp3010028
- Wang, R., Wang, L., He, C., Lu, M., Sun, L. (2019). Studies on the sealing processes of corrosion resistant coatings formed on 2024 aluminium alloy with tartaric-sulfuric anodizing. Surface and Coatings Technology, 360, 369–375. doi: https://doi.org/10.1016/j.surfcoat.2018.12.092
- Gonzalez, J. A., Lopez, V., Otero, E., Bautista, A., Lizarbe, R., Barba, C., Baldonedo, J. L. (1997). Overaging of sealed and unsealed aluminium oxide films. Corrosion Science, 39 (6), 1109–1118. doi: https://doi.org/10.1016/s0010-938x(97)00019-x
- Yu, S., Wang, L., Wu, C., Feng, T., Cheng, Y., Bu, Z., Zhu, S. (2020). Studies on the corrosion performance of an effective and novel sealing anodic oxide coating. Journal of Alloys and Compounds, 817, 153257. doi: https://doi.org/10.1016/j.jallcom.2019.153257
- Zhang, L. M., Zhang, S. D., Ma, A. L., Hu, H. X., Zheng, Y. G., Yang, B. J., Wang, J. Q. (2018). Influence of sealing treatment on the corrosion behavior of HVAF sprayed Al-based amorphous/nanocrystalline coating. Surface and Coatings Technology, 353, 263–273. doi: https://doi.org/10.1016/j.surfcoat.2018.08.086
- Hu, N., Dong, X., He, X., Browning, J. F., Schaefer, D. W. (2015). Effect of sealing on the morphology of anodized aluminum oxide. Corrosion Science, 97, 17–24. doi: https://doi.org/10.1016/j.corsci.2015.03.021
- Kocabaş, M., Örnek, C., Curioni, M., Cansever, N. (2019). Nickel fluoride as a surface activation agent for electroless nickel coating of anodized AA1050 aluminum alloy. Surface and Coatings Technology, 364, 231–238. doi: https://doi.org/10.1016/j.surfcoat.2019.03.003
- Hao, X.-L., Zhao, N., Jin, H.-H., Ma, W., Zhang, D.-H. (2020). Nickel-free sealing technology for anodic oxidation film of aluminum alloy at room temperature. Rare Metals, 40 (4), 968–974. doi: https://doi.org/10.1007/s12598-020-01410-8
- Whelan, M., Cassidy, J., Duffy, B. (2013). Sol–gel sealing characteristics for corrosion resistance of anodised aluminium. Surface and Coatings Technology, 235, 86–96. doi: https://doi.org/10.1016/j.surfcoat.2013.07.018
- Capelossi, V. R., Poelman, M., Recloux, I., Hernandez, R. P. B., de Melo, H. G., Olivier, M. G. (2014). Corrosion protection of clad 2024 aluminum alloy anodized in tartaric-sulfuric acid bath and protected with hybrid sol–gel coating. Electrochimica Acta, 124, 69–79. doi: https://doi.org/10.1016/j.electacta.2013.09.004
- Huang, T.-C., Lin, C.-Y., Liao, K.-C. (2022). Sealing performance assessments of PTFE rotary lip seals based on the elasto-hydrodynamic analysis with the modified archard wear model. Tribology International, 176, 107917. doi: https://doi.org/10.1016/j.triboint.2022.107917
- Abd-Elnaiem, A. M., Abbady, G., Ali, D., Asafa, T. B. (2019). Influence of anodizing voltage and electrolyte concentration on Al-1 wt% Si thin films anodized in H2SO4. Materials Research Express, 6 (8), 086468. doi: https://doi.org/10.1088/2053-1591/ab2848
- Park, J., Son, K., Lee, J., Kim, D., Chung, W. (2021). Effects of Anodizing Conditions on Thermal Properties of Al 20XX Alloys for Aircraft. Symmetry, 13 (3), 433. doi: https://doi.org/10.3390/sym13030433
- Araoyinbo, A. O., Noor, A. F. M., Sreekantan, S., Aziz, A. (2010). Voltage Effect on Electrochemical Anodization of Aluminum at Ambient Temperature. International Journal of Mechanical and Materials Engineering, 5 (1), 53–58. Available at: https://www.researchgate.net/publication/265811751_Voltage_effect_on_electrochemical_anodization_of_aluminum_at_ambient_temperature
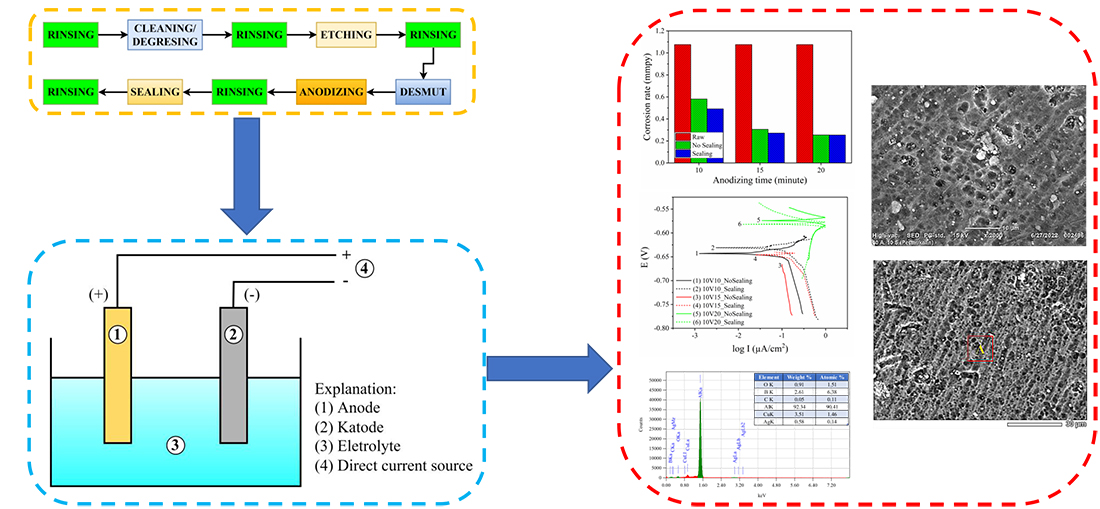
Downloads
Published
How to Cite
Issue
Section
License
Copyright (c) 2023 Muhammad Zuchry, Ilyas Renreng, Hairul Arsyad, Lukmanul Hakim Arma, Agus Widyianto

This work is licensed under a Creative Commons Attribution 4.0 International License.
The consolidation and conditions for the transfer of copyright (identification of authorship) is carried out in the License Agreement. In particular, the authors reserve the right to the authorship of their manuscript and transfer the first publication of this work to the journal under the terms of the Creative Commons CC BY license. At the same time, they have the right to conclude on their own additional agreements concerning the non-exclusive distribution of the work in the form in which it was published by this journal, but provided that the link to the first publication of the article in this journal is preserved.
A license agreement is a document in which the author warrants that he/she owns all copyright for the work (manuscript, article, etc.).
The authors, signing the License Agreement with TECHNOLOGY CENTER PC, have all rights to the further use of their work, provided that they link to our edition in which the work was published.
According to the terms of the License Agreement, the Publisher TECHNOLOGY CENTER PC does not take away your copyrights and receives permission from the authors to use and dissemination of the publication through the world's scientific resources (own electronic resources, scientometric databases, repositories, libraries, etc.).
In the absence of a signed License Agreement or in the absence of this agreement of identifiers allowing to identify the identity of the author, the editors have no right to work with the manuscript.
It is important to remember that there is another type of agreement between authors and publishers – when copyright is transferred from the authors to the publisher. In this case, the authors lose ownership of their work and may not use it in any way.