Optimization of resistance spot welding with surface roughness dissimilar mild steel with stainless steel
DOI:
https://doi.org/10.15587/1729-4061.2023.285711Keywords:
resistance spot welding, dissimilar material, mild steel, stainless steel, surface roughness treatmentAbstract
Resistance spot welding plays a critical role in the manufacture dissimilar material industry. However, there are differences in mechanical properties between mild steel and satinless steel so as to reduce the quality of welded joints. In order for differences in mechanical properties to be corrected, surface roughness was treated. The aim of this study was to optimize the welding parameters of DRSW with surface roughness by analysis using the Taguchi and Anova Methods. In this study discusses about investigates the Resistance spot welding parameters on weld geometry, mechanical properties, and SEM EDS on dissimilar materials of mild steel and stainless steel. The material thickness of the mild steel and stainless steel are 1 mm, respectively. The process parameters of the resistance spot welding joint used, example; surface roughness, current, welding time, and electrode force. Quality welding joint test results include weld geometry, mechanical properties, and SEM EDS. Weld geometry testing to determine the weld nugget profile. The mechanical properties test was shear tensile test, while the SEM EDS included macrostruture and microstructure observations. The results showed the highest nugget diameter 6.65 mm highest shear tensile strength 7.66 kN. The most influential parameter is current by 75.08 %, then surface roughness by 12.35 %. The highest tensile strength has fewer defects. Surface roughness treatment before welding is very good to make welding quality joints between mild steel and quality stainless steel increase. Surface roughness treatment was very good to be included when making welding procedures for welding engineers for welding processes resistance spot welding dissimilar mild steel with stainless steel.
Supporting Agency
- We are grateful for the financial assistance and facilities to the ATI Makassar Polytechnic, Welding Workshop, SEM-EDS laboratory of the Indonesian Muslim University.
References
- Feujofack Kemda, B. V., Barka, N., Jahazi, M., Osmani, D. (2019). Optimization of resistance spot welding process applied to A36 mild steel and hot dipped galvanized steel based on hardness and nugget geometry. The International Journal of Advanced Manufacturing Technology, 106 (5-6), 2477–2491. doi: https://doi.org/10.1007/s00170-019-04707-w
- Bozkurt, F., Çakır, F. H. (2021). An experimental design of spot welding of Ti6Al4V sheets and numerical modeling approach. Welding in the World, 65 (5), 885–898. doi: https://doi.org/10.1007/s40194-020-01054-3
- Hu, S., Haselhuhn, A. S., Ma, Y., Li, Y., Carlson, B. E., Lin, Z. (2021). Sensitivity of dissimilar aluminum to steel resistance spot welds to weld gun deflection. Journal of Manufacturing Processes, 68, 534–545. doi: https://doi.org/10.1016/j.jmapro.2021.05.059
- Das, T., Das, R., Paul, J. (2020). Resistance spot welding of dissimilar AISI-1008 steel/Al-1100 alloy lap joints with a graphene interlayer. Journal of Manufacturing Processes, 53, 260–274. doi: https://doi.org/10.1016/j.jmapro.2020.02.032
- Sokkalingam, R., Pravallika, B., Sivaprasad, K., Muthupandi, V., Prashanth, K. G. (2021). Dissimilar welding of high-entropy alloy to Inconel 718 superalloy for structural applications. Journal of Materials Research, 37 (1), 272–283. doi: https://doi.org/10.1557/s43578-021-00352-w
- Biradar, A. K., Dabade, B. M. (2020). Optimization of resistance spot welding process parameters in dissimilar joint of MS and ASS 304 sheets. Materials Today: Proceedings, 26, 1284–1288. doi: https://doi.org/10.1016/j.matpr.2020.02.256
- Mishra, D., Rajanikanth, K., Shunmugasundaram, M., Kumar, A. P., Maneiah, D. (2021). Dissimilar resistance spot welding of mild steel and stainless steel metal sheets for optimum weld nugget size. Materials Today: Proceedings, 46, 919–924. doi: https://doi.org/10.1016/j.matpr.2021.01.067
- Hellberg, S., Hummel, J., Krooß, P., Niendorf, T., Böhm, S. (2020). Microstructural and mechanical properties of dissimilar nitinol and stainless steel wire joints produced by micro electron beam welding without filler material. Welding in the World, 64 (12), 2159–2168. doi: https://doi.org/10.1007/s40194-020-00991-3
- Baek, S., Go, G. Y., Park, J.-W., Song, J., Lee, H., Lee, S.-J. et al. (2022). Microstructural and interface geometrical influence on the mechanical fatigue property of aluminum/high-strength steel lap joints using resistance element welding for lightweight vehicles: experimental and computational investigation. Journal of Materials Research and Technology, 17, 658–678. doi: https://doi.org/10.1016/j.jmrt.2022.01.041
- Ariyanto, Arsyad, H., Syahid, M., Ilyas, R. (2022). Optimization of Welding Parameters for Resistance Spot Welding with Variations in the Roughness of the Surface of the AISI 304 Stainless Steel Joint to Increase Joint Quality. International Journal of Mechanical Engineering and Robotics Research, 11 (11), 877–883. doi: https://doi.org/10.18178/ijmerr.11.11.877-883
- Shin, S., Park, D.-J., Yu, J., Rhee, S. (2019). Resistance Spot Welding of Aluminum Alloy and Carbon Steel with Spooling Process Tapes. Metals, 9 (4), 410. doi: https://doi.org/10.3390/met9040410
- Kar, A., Kailas, S. V., Suwas, S. (2019). Effect of Mechanical Mixing in Dissimilar Friction Stir Welding of Aluminum to Titanium with Zinc Interlayer. Transactions of the Indian Institute of Metals, 72 (6), 1533–1536. doi: https://doi.org/10.1007/s12666-019-01643-x
- Mirmahdi, E. (2020). Numerical and Experimental Modeling of Spot Welding Defects by Ultrasonic Testing on Similar Sheets and Dissimilar Sheets. Russian Journal of Nondestructive Testing, 56 (8), 620–634. doi: https://doi.org/10.1134/s1061830920080069
- Peethala, A. K., D, B. N., Rao. K, S., G, R. (2023). Optimization of welding parameters and study on mechanical and pitting corrosion behavior of dissimilar stainless steel GTA welds. Chemical Data Collections, 43, 100978. doi: https://doi.org/10.1016/j.cdc.2022.100978
- Dhawale, P. A., Ronge, B. P. (2019). Parametric optimization of resistance spot welding for multi spot welded lap shear specimen to predict weld strength. Materials Today: Proceedings, 19, 700–707. doi: https://doi.org/10.1016/j.matpr.2019.07.756
- Guzanová, A., Brezinová, J., Varga, J., Džupon, M., Vojtko, M., Janoško, E. et al. (2023). Experimental Study of Steel–Aluminum Joints Made by RSW with Insert Element and Adhesive Bonding. Materials, 16 (2), 864. doi: https://doi.org/10.3390/ma16020864
- Taufiqurrahman, I., Lenggo Ginta, T., Mustapha, M. (2021). The effect of holding time on dissimilar resistance spot welding of stainless steel 316L and Ti6Al4V titanium alloy with aluminum interlayer. Materials Today: Proceedings, 46, 1563–1568. doi: https://doi.org/10.1016/j.matpr.2020.07.237
- Choi, D.-Y., Sharma, A., Uhm, S.-H., Jung, J. P. (2018). Liquid Metal Embrittlement of Resistance Spot Welded 1180 TRIP Steel: Effect of Electrode Force on Cracking Behavior. Metals and Materials International, 25 (1), 219–228. doi: https://doi.org/10.1007/s12540-018-0180-x
- Hassoni, S. M., Barrak, O. S., Ismail, M. I., Hussein, S. K. (2022). Effect of Welding Parameters of Resistance Spot Welding on Mechanical Properties and Corrosion Resistance of 316L. Materials Research, 25. doi: https://doi.org/10.1590/1980-5373-mr-2021-0117
- Sejc, P., Gábrišová, Z. (2018). Optimization of RSW parameters by joining galvanized steel HZ 220 BD-Z100 MB with aluminium AV 1050A. Metallic Materials, 56 (03), 145–152. doi: https://doi.org/10.4149/km_2018_3_145
- Mahmood, N. Y. (2020). Prediction of the optimum tensile - shear strength through the experimental results of similar and dissimilar spot welding joints. Archive of Mechanical Engineering, 67 (2), 197–210. doi: https://doi.org/10.24425/ame.2020.131690
- Curiel, F. F., García, R., López, V. H., García, M. A., Contreras, A., García, M. A. (2021). The Effect of Applying Magnetic Fields During Welding AISI-304 Stainless Steel on Stress Corrosion Cracking. International Journal of Electrochemical Science, 16 (3), 210338. doi: https://doi.org/10.20964/2021.03.31
- Ren, S., Ma, Y., Saeki, S., Iwamoto, Y., Ma, N. (2020). Numerical analysis on coaxial one-side resistance spot welding of Al5052 and CFRP dissimilar materials. Materials & Design, 188, 108442. doi: https://doi.org/10.1016/j.matdes.2019.108442
- Zhang, T., Wang, W., Zhou, J., Yan, Z., Zhang, J. (2019). Interfacial characteristics and nano-mechanical properties of dissimilar 304 austenitic stainless steel/AZ31B Mg alloy welding joint. Journal of Manufacturing Processes, 42, 257–265. doi: https://doi.org/10.1016/j.jmapro.2019.04.031
- Özen, F., Aslanlar, S. (2021). Mechanical and microstructural evaluation of resistance spot welded dissimilar TWIP/martensitic steel joints. The International Journal of Advanced Manufacturing Technology, 113 (11-12), 3473–3489. doi: https://doi.org/10.1007/s00170-021-06848-3
- Ariyanto, Renreng, I., Arsyad, H., Syahid, M. (2023). Optimization parameter resistance spot welding dissimilar material-a review. AIP Conference Proceedings. doi: https://doi.org/10.1063/5.0126219
- Nagatsuka, K., Xiao, B., Wu, L., Natata, K., Saeki, S., Kitamoto, Y., Iwamoto, Y. (2018). Dissimilar materials joining of metal/carbon fibre reinforced plastic by resistance spot welding. Welding International, 32 (7), 505–512. doi: https://doi.org/10.1080/01431161.2017.1346889
- Raturi, M., Garg, A., Bhattacharya, A. (2019). Joint strength and failure studies of dissimilar AA6061-AA7075 friction stir welds: Effects of tool pin, process parameters and preheating. Engineering Failure Analysis, 96, 570–588. doi: https://doi.org/10.1016/j.engfailanal.2018.12.003
- Patel, N. P., Parlikar, P., Singh Dhari, R., Mehta, K., Pandya, M. (2019). Numerical modelling on cooling assisted friction stir welding of dissimilar Al-Cu joint. Journal of Manufacturing Processes, 47, 98–109. doi: https://doi.org/10.1016/j.jmapro.2019.09.020
- Aizuddin, Z. A. Z., Aminudin, B. A., Sanda, P. S., Zetty, R. M. S. (2016). Resistance Spot Welding Process Optimization Using Taguchi Robust Method for Joining Dissimilar Material. Applied Mechanics and Materials, 835, 248–253. doi: https://doi.org/10.4028/www.scientific.net/amm.835.248
- Mohammed, S. M. A. K., Dash, S. S., Jiang, X. Q., Li, D. Y., Chen, D. L. (2019). Ultrasonic spot welding of 5182 aluminum alloy: Evolution of microstructure and mechanical properties. Materials Science and Engineering: A, 756, 417–429. doi: https://doi.org/10.1016/j.msea.2019.04.059
- Wang, Y., Yang, S. (2022). Effects of Electrode Combinations on RSW of 5182-O/AlSi10MnMg Aluminum. Welding Journal, 101 (2), 54–66. doi: https://doi.org/10.29391/2022.101.005
- Wei, F., Zhu, Y., Tian, Y., Liu, H., Zhou, Y., Zhu, Z. (2022). Resistance Spot-Welding of Dissimilar Metals, Medium Manganese TRIP Steel and DP590. Metals, 12 (10), 1596. doi: https://doi.org/10.3390/met12101596
- Liu, X., Wei, Y., Wu, H., Zhang, T. (2020). Factor analysis of deformation in resistance spot welding of complex steel sheets based on reverse engineering technology and direct finite element analysis. Journal of Manufacturing Processes, 57, 72–90. doi: https://doi.org/10.1016/j.jmapro.2020.06.028
- Podgornik, B., Kafexhiu, F., Nevosad, A., Badisch, E. (2020). Influence of surface roughness and phosphate coating on galling resistance of medium-grade carbon steel. Wear, 446-447, 203180. doi: https://doi.org/10.1016/j.wear.2019.203180
- Ariyanto, A., A. Assagaf, I. P., Ramadhan Latief, R., Maulana, F. R., Gusrifar, G., Fitrah, M. A., Ikhsan, M. (2023). Prototype of Resistance Spot Welding Material Preparation to Improve the Quality of Welding Joints. International Journal of Engineering Business and Social Science, 1 (04), 283–289. doi: https://doi.org/10.58451/ijebss.v1i04.58
- Hvalec, M., Gorc, A., En-, C. (1993). Taguchi Method Applied To the Crystallization Processes. Vol. 1. Prentice Hall.
- Lin, H. C., Hsu, C. A., Lee, C. S., Kuo, T. Y., Jeng, S. L. (2018). Effects of zinc layer thickness on resistance spot welding of galvanized mild steel. Journal of Materials Processing Technology, 251, 205–213. doi: https://doi.org/10.1016/j.jmatprotec.2017.08.035
- Kishore, K., Kumar, P., Mukhopadhyay, G. (2021). Microstructure, Tensile and Fatigue Behaviour of Resistance Spot Welded Zinc Coated Dual Phase and Interstitial Free Steel. Metals and Materials International, 28 (4), 945–965. doi: https://doi.org/10.1007/s12540-020-00939-8
- Wan, X., Wang, Y., Fang, C. (2014). Welding Defects Occurrence and Their Effects on Weld Quality in Resistance Spot Welding of AHSS Steel. ISIJ International, 54 (8), 1883–1889. doi: https://doi.org/10.2355/isijinternational.54.1883
- Kubit, A., Trzepiecinski, T., Faes, K., Drabczyk, M., Bochnowski, W., Korzeniowski, M. (2019). Analysis of the effect of structural defects on the fatigue strength of RFSSW joints using C‐scan scanning acoustic microscopy and SEM. Fatigue & Fracture of Engineering Materials & Structures, 42 (6), 1308–1321. doi: https://doi.org/10.1111/ffe.12984
- Bodu, S., Andrieiev, V., Novoshytskyi, A. (2023). Strengthening of friction surfaces by using geomodifiers based on serpentines from the Dashukivka deposit. Eastern-European Journal of Enterprise Technologies, 3 (12 (123)), 38–47. doi: https://doi.org/10.15587/1729-4061.2023.283441
- Sulfiana, E., Sonjaya, M. L., Ariyanto, Fitrah, M. A., Assagaf, I. P. A., Baharuddin, A. V., Arifin, A. N. (2023). Material preparation with sanding machine against welding nugget diameter, penetration and surface roughness on spot welding resistance connections. AIP Conference Proceedings. doi: https://doi.org/10.1063/5.0142307
- Salimi Beni, S., Atapour, M., Salmani, M. R., Ashiri, R. (2019). Resistance Spot Welding Metallurgy of Thin Sheets of Zinc-Coated Interstitial-Free Steel. Metallurgical and Materials Transactions A, 50 (5), 2218–2234. doi: https://doi.org/10.1007/s11661-019-05146-8
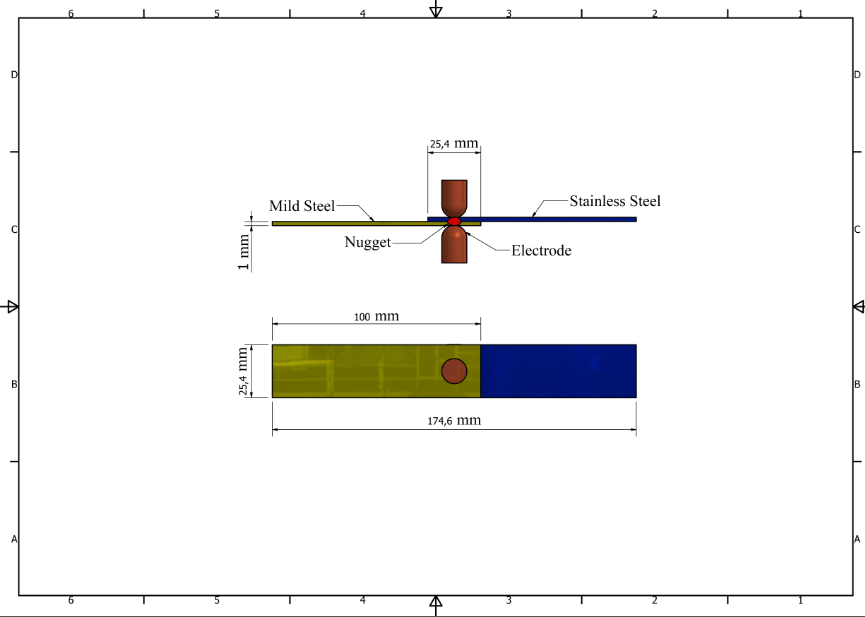
Downloads
Published
How to Cite
Issue
Section
License
Copyright (c) 2023 Ariyanto, Muhammad Setiawan Sukardin, Ilyas Renreng, Hairul Arsyad, Muhammad Syahid, Muhammad Alwi

This work is licensed under a Creative Commons Attribution 4.0 International License.
The consolidation and conditions for the transfer of copyright (identification of authorship) is carried out in the License Agreement. In particular, the authors reserve the right to the authorship of their manuscript and transfer the first publication of this work to the journal under the terms of the Creative Commons CC BY license. At the same time, they have the right to conclude on their own additional agreements concerning the non-exclusive distribution of the work in the form in which it was published by this journal, but provided that the link to the first publication of the article in this journal is preserved.
A license agreement is a document in which the author warrants that he/she owns all copyright for the work (manuscript, article, etc.).
The authors, signing the License Agreement with TECHNOLOGY CENTER PC, have all rights to the further use of their work, provided that they link to our edition in which the work was published.
According to the terms of the License Agreement, the Publisher TECHNOLOGY CENTER PC does not take away your copyrights and receives permission from the authors to use and dissemination of the publication through the world's scientific resources (own electronic resources, scientometric databases, repositories, libraries, etc.).
In the absence of a signed License Agreement or in the absence of this agreement of identifiers allowing to identify the identity of the author, the editors have no right to work with the manuscript.
It is important to remember that there is another type of agreement between authors and publishers – when copyright is transferred from the authors to the publisher. In this case, the authors lose ownership of their work and may not use it in any way.