Comparison of chemical composition and wear of iron and nickel aluminide coatings applied by plasma spraying
DOI:
https://doi.org/10.15587/1729-4061.2023.286198Keywords:
iron aluminide, nickel aluminide, plasma spraying of coatings, dry frictionAbstract
Given such properties as wear resistance, corrosion resistance, heat resistance, contact and cyclic strength, iron and nickel aluminides can be used as coatings in friction pairs for various purposes. The object of research is the process of obtaining plasma-sprayed coatings from powders based on iron and nickel aluminides. The task of research is the determination and comparison of the structure, chemical composition, and wear resistance of coatings from powders of iron aluminide and nickel aluminide, obtained by the method of atmospheric plasma spraying. To reduce the oxidation of powders during spraying, the conditions for generating a laminar plasma jet were created. Such conditions were provided by the specially developed structure of the electric arc plasma gun and the operating parameters of coating spraying. As a result of the correct choice of spraying modes, completely melted splats were formed during the collision of powder particles with the surface. The resulting coatings had a layered microstructure with microcracks and peeling. The porosity and characteristics of the delamination of the coatings depend on both the modes and the spraying technology. Tribological tests of the coatings were carried out under conditions of dry metal-on-metal sliding friction in a pair with high-speed steel. It is shown that the wear of nickel aluminide coatings under these conditions is 2–2.5 times lower than that of iron aluminide coatings. The coefficient of friction of iron aluminide coatings is slightly lower than that of nickel aluminide coatings. The wear of samples made of 30CrMnSi steel is 3–4 times higher than samples with coatings. The difference in the wear of the coatings is explained by the more intense oxidation of iron aluminide in the friction process. Conclusions were drawn regarding the possibility of using the investigated coatings in various friction pairs of structural elements, in particular in the automotive industry
References
- Chen, H., Fan, M., Zhu, W., Norton, A. D. (2020). High temperature oxidation behaviour of combustion flame sprayed CoNiCrAlY coatings. Surface and Coatings Technology, 385, 125431. doi: https://doi.org/10.1016/j.surfcoat.2020.125431
- Rachidi, R., El Kihel, B., Delaunois, F. (2019). Microstructure and mechanical characterization of NiCrBSi alloy and NiCrBSi-WC composite coatings produced by flame spraying. Materials Science and Engineering: B, 241, 13–21. doi: https://doi.org/10.1016/j.mseb.2019.02.002
- Grigoriev, O. N., Shvets, V. A., Podchernyaeva, I. A., Yurechko, D. V., Vedel, D. V., Zubarev, A. A. et al. (2020). Electrochemical Corrosion of Composite Ceramics and Thermal Spray Coatings in the ZrB2–SiC–AlN System. Powder Metallurgy and Metal Ceramics, 59 (7-8), 394–400. doi: https://doi.org/10.1007/s11106-020-00173-2
- Lyashenko, B. A., Veremchuk, V. S., Dolgov, N. A., Ivanov, V. M. (1996). Strength and deformation properties of compositions with plasma-sprayed coatings. Strength of Materials, 28 (6), 452–454. doi: https://doi.org/10.1007/bf02209316
- Zhang, H., Chen, X., Gong, Y., Tian, Y., McDonald, A., Li, H. (2020). In-situ SEM observations of ultrasonic cavitation erosion behavior of HVOF-sprayed coatings. Ultrasonics Sonochemistry, 60, 104760. doi: https://doi.org/10.1016/j.ultsonch.2019.104760
- Raza, A., Ahmad, F., Badri, T. M., Raza, M. R., Malik, K. (2022). An Influence of Oxygen Flow Rate and Spray Distance on the Porosity of HVOF Coating and Its Effects on Corrosion—A Review. Materials, 15 (18), 6329. doi: https://doi.org/10.3390/ma15186329
- Pawlowski, L. (2008). The Science and Engineering of Thermal Spray Coatings. John Wiley & Sons. doi: https://doi.org/10.1002/9780470754085
- Smyrnov, I. V., Chornyi, A. V., Kopylov, V. I. (2020). Effect of Nanodispersed Ingredients on the Properties of Plasma Coatings. Metallofizika I Noveishie Tekhnologii, 42 (6), 797–814. doi: https://doi.org/10.15407/mfint.42.06.0797
- Gérard, B. (2006). Application of thermal spraying in the automobile industry. Surface and Coatings Technology, 201 (5), 2028–2031. doi: https://doi.org/10.1016/j.surfcoat.2006.04.050
- Gudz, G., Zakhara, I., Voitsikhovska, T., Vytvytskyi, V., Ropyak, L. (2022). Temperature Distribution in Parts of the Vehicle Disk Brake. Lecture Notes in Mechanical Engineering, 517–529. doi: https://doi.org/10.1007/978-3-031-16651-8_49
- Aranke, O., Algenaid, W., Awe, S., Joshi, S. (2019). Coatings for Automotive Gray Cast Iron Brake Discs: A Review. Coatings, 9 (9), 552. doi: https://doi.org/10.3390/coatings9090552
- Cinca, N., Lima, C. R. C., Guilemany, J. M. (2013). An overview of intermetallics research and application: Status of thermal spray coatings. Journal of Materials Research and Technology, 2 (1), 75–86. doi: https://doi.org/10.1016/j.jmrt.2013.03.013
- Wang, H., An, F., Bai, X., Yao, H., Zhang, M., Chen, Q. et al. (2023). Improvement of Microstructure and Sliding Wear Property of Cold-Sprayed FeAl Intermetallic Compound Coating by Annealing Treatment. Coatings, 13 (7), 1260. doi: https://doi.org/10.3390/coatings13071260
- Chrostek, T. (2021). Tribological wear of Fe-Al coatings applied by gas detonation spraying. Technical Sciences, 24 (1), 245–256. doi: https://doi.org/10.31648/ts.7129
- Senderowski, C., Bojar, Z., Wołczyński, W Pawłowski, A. (2010). Microstructure characterization of D-gun sprayed Fe–Al intermetallic coatings. Intermetallics, 18 (7), 1405–1409. doi: https://doi.org/10.1016/j.intermet.2010.01.015
- Vijaya Lakshmi, D., Suresh Babu, P., Rama Krishna, L., Vijay, R., Srinivasa Rao, D., Padmanabham, G. (2021). Corrosion and erosion behavior of iron aluminide (FeAl(Cr)) coating deposited by detonation spray technique. Advanced Powder Technology, 32 (7), 2192–2201. doi: https://doi.org/10.1016/j.apt.2021.04.032
- Senapati, P., Sutar, H., Murmu, R., Gupta, S. (2022). Slurry Erosion Behaviour of HVOF-Sprayed NiAl Composite Coating. Lecture Notes in Mechanical Engineering, 623–629. doi: https://doi.org/10.1007/978-981-16-9057-0_68
- Starosta, R. (2009). Properties of Thermal Spraying Ni-Al Alloy Coatings. Advances in Materials Sciences, 9 (1). doi: https://doi.org/10.2478/v10077-009-0004-2
- Hawk, J. A., Alman, D. E. (1997). Abrasive wear of intermetallic-based alloys and composites. Materials Science and Engineering: A, 239-240, 899–906. doi: https://doi.org/10.1016/s0921-5093(97)00681-3
- Меlnik, О. В., Smirnov, I. V., Labunets, V. F., Сhorniy, A. V. (2020). Research of wear resistance of plasma coatings in the conditions of abrasive wear. Problems of Friction and Wear, 3 (88), 126–131. doi: https://doi.org/10.18372/0370-2197.3(88).14928
- Ghosh, G., Korniyenko, K., Velikanova, T., Sidorko, V. (2008). Aluminium – Chromium – Iron. Landolt-Börnstein - Group IV Physical Chemistry, 44–87. doi: https://doi.org/10.1007/978-3-540-69761-9_5
- Thiem, P. G., Chornyi, A., Smirnov, I. V., Krüger, M. (2017). Comparison of microstructure and adhesion strength of plasma, flame and high velocity oxy-fuel sprayed coatings from an iron aluminide powder. Surface and Coatings Technology, 324, 498–508. doi: https://doi.org/10.1016/j.surfcoat.2017.06.016
- Neiser, R. A., Smith, M. F., Dykhuizen, R. C. (1998). Oxidation in Wire HVOF-Sprayed Steel. Journal of Thermal Spray Technology, 7 (4), 537–545. doi: https://doi.org/10.1361/105996398770350765
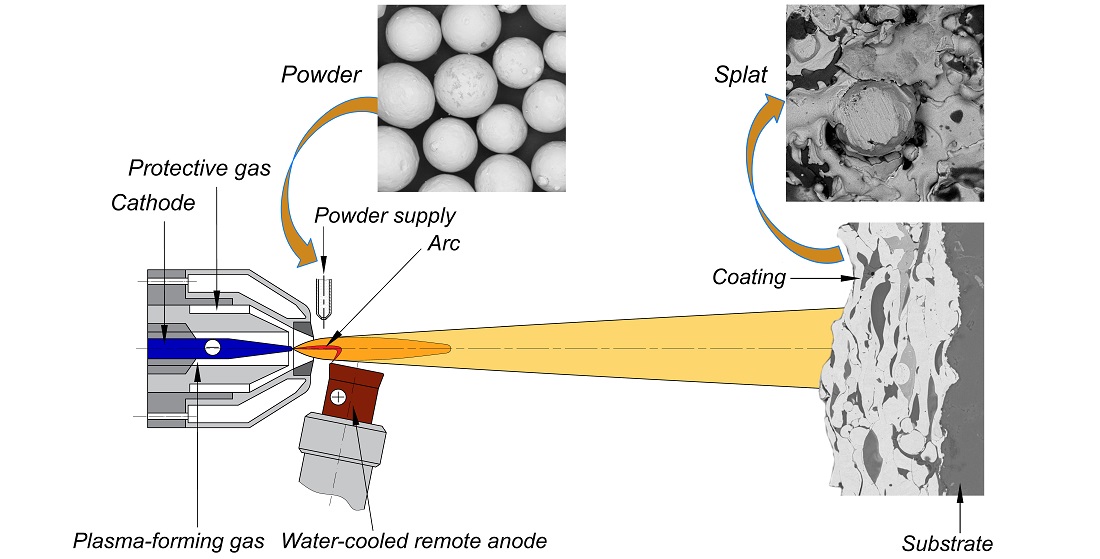
Downloads
Published
How to Cite
Issue
Section
License
Copyright (c) 2023 Igor Smirnov, Andrii Chornyi, Volodymyr Lysak, Nikolay Dolgov, Ihor Sіеliverstov, Kostiantyn Parshenko

This work is licensed under a Creative Commons Attribution 4.0 International License.
The consolidation and conditions for the transfer of copyright (identification of authorship) is carried out in the License Agreement. In particular, the authors reserve the right to the authorship of their manuscript and transfer the first publication of this work to the journal under the terms of the Creative Commons CC BY license. At the same time, they have the right to conclude on their own additional agreements concerning the non-exclusive distribution of the work in the form in which it was published by this journal, but provided that the link to the first publication of the article in this journal is preserved.
A license agreement is a document in which the author warrants that he/she owns all copyright for the work (manuscript, article, etc.).
The authors, signing the License Agreement with TECHNOLOGY CENTER PC, have all rights to the further use of their work, provided that they link to our edition in which the work was published.
According to the terms of the License Agreement, the Publisher TECHNOLOGY CENTER PC does not take away your copyrights and receives permission from the authors to use and dissemination of the publication through the world's scientific resources (own electronic resources, scientometric databases, repositories, libraries, etc.).
In the absence of a signed License Agreement or in the absence of this agreement of identifiers allowing to identify the identity of the author, the editors have no right to work with the manuscript.
It is important to remember that there is another type of agreement between authors and publishers – when copyright is transferred from the authors to the publisher. In this case, the authors lose ownership of their work and may not use it in any way.