Development of a layer leveling technology that reduces the energy intensity of the processes of mixing and drying the fodder mass
DOI:
https://doi.org/10.15587/1729-4061.2023.286325Keywords:
grinder-mixer-dryer, leveling device, required power, forage mass, layer to be removedAbstract
The object of the study is to determine the required power leveling device grinder-mixer-dryer. When operating equipment that combines grinding, mixing and drying in one device, there are such problems as energy intensity, the lack of calculation formulas for the theoretical determination of the required power, which makes it difficult to plan the energy intensity of the equipment. As a result of the research, a constructive-technological scheme of the grinder-mixer-dryer equipped with a leveling device was developed. The leveling device, rotating in opposite directions, moves the raised fodder mass to the end walls of the bunker. The operation of the screed tines eliminates excessive forage lift and speeds up the mixing process by moving the forage evenly across the entire width of the bin. The acceleration of the drying process of wet food is explained by the fact that new portions of wet food are constantly exposed to hot air. As a result of theoretical studies an analytical expression was obtained to determine the required power for the process of leveling the layer of forage mass and the required power for the process of leveling the layer of forage mass NТ=0.286 kW was determined. The results of the experimental determination of the required power for the process of leveling the forage mass layer showed the following value NЕ=0.273 kW, i.e. the difference between theoretical and actual value is only 4.76 %. This proves the reliability of the obtained analytical expression, which provides the definition of the main parameter of the grinder-mixer-dryer, i.e. required power leveling device. The proposed device and the resulting analytical expression can also be used in feed mixers
Supporting Agency
- This research has been/was/is funded by the Science Committee of the Ministry of Education and Science of the Republic of Kazakhstan (Grant No. AP09259673).
References
- Rajendran, D., Ezhuthupurakkal, P. B., Lakshman, R., Gowda, N. K. S., Manimaran, A., Rao, S. B. (2022). Application of encapsulated nano materials as feed additive in livestock and poultry: a review. Veterinary Research Communications, 46 (2), 315–328. doi: https://doi.org/10.1007/s11259-022-09895-7
- Iskakov, R., Sugirbay, A. (2023). Technologies for the Rational Use of Animal Waste: A Review. Sustainability, 15 (3), 2278. doi: https://doi.org/10.3390/su15032278
- Konstantinovskaya, M. A. (2016). Polucheniye tekhnologii gidrolizatov i kormovoy biomassy iz otkhoda proizvodstva kostnoy muki. Shchelkovo, 23.
- Hendriks, W. H., Butts, C. A., Thomas, D. V., James, K. A. C., Morel, P. C. A., Verstegen, M. W. A. (2002). Nutritional Quality and Variation of Meat and Bone Meal. Asian-Australasian Journal of Animal Sciences, 15 (10), 1507–1516. doi: https://doi.org/10.5713/ajas.2002.1507
- Jia, S., Li, X., He, W., Wu, G. (2021). Protein-Sourced Feedstuffs for Aquatic Animals in Nutrition Research and Aquaculture. Recent Advances in Animal Nutrition and Metabolism, 237–261. doi: https://doi.org/10.1007/978-3-030-85686-1_12
- Farmanesh, A., Mohtasebi, S. S., Omid, M. (2019). Optimization of rendering process of poultry by-products with batch cooker model monitored by electronic nose. Journal of Environmental Management, 235, 194–201. doi: https://doi.org/10.1016/j.jenvman.2019.01.049
- Awasthi, K. S., Gopireddy, S. R., Scherließ, R., Urbanetz, N. A. (2019). Numerical Investigation of Screw Design Influence on Screw Feeding in a Roller Compactor. 6th International Conference on Particle-Based Methods. Fundamentals and Applications, Particles, 444–455. Available at: https://upcommons.upc.edu/bitstream/handle/2117/186638/Particles_2019-41-Numerical%20investigation%20of%20screw.pdf?sequence=1&isAllowed=y
- Abilzhanuly, T., Iskakov, R., Abilzhanov, D., Darkhan, O. (2023). Determination of the average size of preliminary grinded wet feed particles in hammer grinders. Eastern-European Journal of Enterprise Technologies, 1 (1 (121)), 34–43. doi: https://doi.org/10.15587/1729-4061.2023.268519
- Al-Souti, A., Gallardo, W., Claereboudt, M., Mahgoub, O. (2019). Attractability and palatability of formulated diets incorporated with chicken feather and algal meals for juvenile gilthead seabream, Sparus aurata. Aquaculture Reports, 14, 100199. doi: https://doi.org/10.1016/j.aqrep.2019.100199
- Vasilenko, V. N., Frolova, L. N., Mikhailova, N. A., Dragan, I. V. (2021). Innovative technology to obtain forage flour from keratin-containing waste by extrusion. IOP Conference Series: Earth and Environmental Science, 640 (2), 022010. doi: https://doi.org/10.1088/1755-1315/640/2/022010
- Castro-Bedriñana, J., Chirinos-Peinado, D. (2021). Nutritional value of some raw materials for guinea pigs (Cavia porcellus) feeding. Translational Animal Science, 5 (2). doi: https://doi.org/10.1093/tas/txab019
- Li, S., Li, H., He, Z. (2017). Optimization of preparation process of nanometer rabbit bone meal by ball milling. Nongye Gongcheng Xuebao/Transactions of the Chinese Society of Agricultural Engineering, 33 (14), 300–306.
- Pavlov, I. N., Kunichan, V. A., Kosmina, I. V. (2008). Technology of Thermo-Hydro Grinding when Drying Non-Rigid Mass in Blade Mixer. Transactions TSTU, 14 (3), 630–631. Available at: https://cyberleninka.ru/article/n/tehnologiya-termovlazhnostnogo-izmelcheniya-pri-sushke-nezhestkih-mass-v-lopastnom-smesitele/viewer
- Savinyh, P., Isupov, A., Ivanov, I., Ivanovs, S. (2021). Research in centrifugal rotary grinder of forage grain. Engineering for Rural Development. doi: https://doi.org/10.22616/erdev.2021.20.tf044
- Iskakov, R. M., Iskakova, A. M., Nurushev, M. Z., Khaimuldinova, A. K., Karbayev, N. K. (2021). Method for the Production of Fat from Raw Materials and Animal Waste. Journal of Pure and Applied Microbiology, 15 (2), 716–724. doi: https://doi.org/10.22207/jpam.15.2.23
- Manzhosov, V. K., Novikova, O. D., Novikov, A. A. (2011). Teoreticheskaya mekhanika. Chast' II. Dinamika. Analiticheskaya mekhanika. Ul'yanovsk: UlGTU, 194.
- Osipov, A. V. (2014). Lektsii po vysshey matematike. Sankt-Peterburg: «Lan'», 320.
- Gur'yanova, K. N. (2014). Matematicheskiy analiz. Ekaterinburg: Uralskyi universitet, 330.
- Usmanov, A. S. (2010). Mashiny dlya agropromyshlennogo kompleksa. Almaty: Inzhu Marzhan, 500.
- Pat. No. 0219RK00538. Razrabotka tekhnologiy i opytnogo obraztsa peredvizhnogo minikormotsekha dlya prigotovleniya i razdachi kormosmesey v melkikh krest'yanskikh khozyaystvakh (2019). No. 0118RK00987.
- Abilzhanov, D. T., Abilzhanuly, T., Uteshev, V. L., Smagulov, T. A., Golikov, V. A., Seipataliyev, O. Y. (2022). Pat. No. 35587KZ. Feed mixer. published: 08.05.2022.
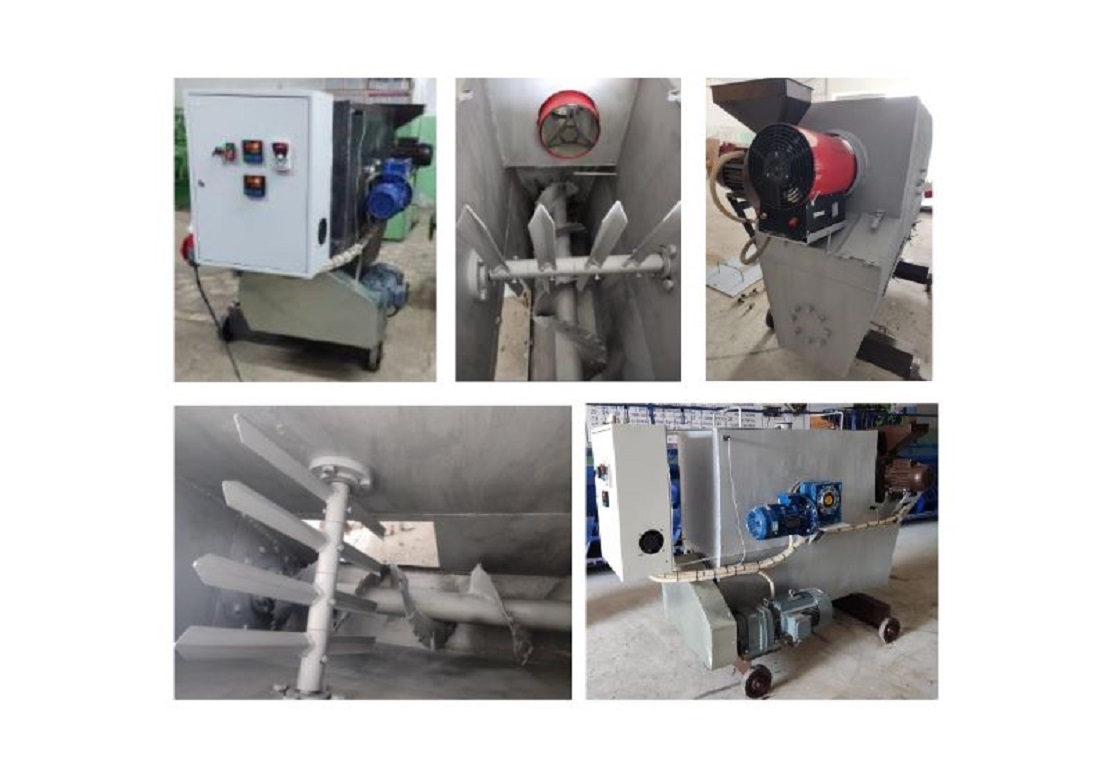
Downloads
Published
How to Cite
Issue
Section
License
Copyright (c) 2023 Tokhtar Abilzhanuly, Ruslan Iskakov, Sultanbek Issenov, Gulmira Kubentaeva, Indira Mamyrbayeva, Daniyar Abilzhanov, Altyngul Khaimuldinova, Nurakhmet Khamitov

This work is licensed under a Creative Commons Attribution 4.0 International License.
The consolidation and conditions for the transfer of copyright (identification of authorship) is carried out in the License Agreement. In particular, the authors reserve the right to the authorship of their manuscript and transfer the first publication of this work to the journal under the terms of the Creative Commons CC BY license. At the same time, they have the right to conclude on their own additional agreements concerning the non-exclusive distribution of the work in the form in which it was published by this journal, but provided that the link to the first publication of the article in this journal is preserved.
A license agreement is a document in which the author warrants that he/she owns all copyright for the work (manuscript, article, etc.).
The authors, signing the License Agreement with TECHNOLOGY CENTER PC, have all rights to the further use of their work, provided that they link to our edition in which the work was published.
According to the terms of the License Agreement, the Publisher TECHNOLOGY CENTER PC does not take away your copyrights and receives permission from the authors to use and dissemination of the publication through the world's scientific resources (own electronic resources, scientometric databases, repositories, libraries, etc.).
In the absence of a signed License Agreement or in the absence of this agreement of identifiers allowing to identify the identity of the author, the editors have no right to work with the manuscript.
It is important to remember that there is another type of agreement between authors and publishers – when copyright is transferred from the authors to the publisher. In this case, the authors lose ownership of their work and may not use it in any way.