Building a model of the compression grinding mechanism in a tumbling mill based on data visualization
DOI:
https://doi.org/10.15587/1729-4061.2023.287565Keywords:
tumbling mill, intra-chamber loading, compressive loading, destruction by crushing, grinding performanceAbstract
The object of the study reported here is the grinding process in a tumbling mill where the mechanism of destruction by crushing is implemented, which is caused by the mechanism of compression loading. The compressive interaction in the active zone of the lower end of the granular loading chamber of the rotating drum at the transition of the shear layer to the solid zone was taken into account.
The task to determine the parameters of the compressive action was solved, which was caused by the difficulties of modeling and the complexity of the hardware analysis of the behavior of the internal loading of the mill.
A mathematical model was built based on data visualization for the compression grinding mechanism.
The power of compressive forces was taken as an analog of grinding performance. The initial characteristic of compression was considered to be the mean speed of movement in the central averaged normal cross-section of the shear layer. The influence on the performance of the mass fraction of the shear layer and the reversibility of loading was taken into account.
The effect of rotation speed on productivity was evaluated by experimental modeling at a chamber filling degree of 0.45 and a relative size of grinding bodies of 0.0104. The maximum value of energy and grinding productivity was established at a relative speed of rotation ψω=0.6–0.65. The maximum value of the share of the shear layer loading was found at ψω=0.4–0.45.
The results have made it possible to establish a rational speed during crushing by compression, ψω=0.55–0.65. This value was smaller in comparison with impact crushing, ψω=0.75–0.9. The observed effect is explained by the detected activation for the shear loading layer during slow rotation, in contrast to the fast rotation for the drop zone.
The model built makes it possible to predict rational technological parameters of the process of medium and fine grinding in a tumbling mill by compression.
References
- Deniz, V. (2013). Comparisons of Dry Grinding Kinetics of Lignite, Bituminous Coal, and Petroleum Coke. Energy Sources, Part A: Recovery, Utilization, and Environmental Effects, 35 (10), 913–920. doi: https://doi.org/10.1080/15567036.2010.514591
- Gupta, V. K. (2020). Energy absorption and specific breakage rate of particles under different operating conditions in dry ball milling. Powder Technology, 361, 827–835. doi: https://doi.org/10.1016/j.powtec.2019.11.033
- Góralczyk, M., Krot, P., Zimroz, R., Ogonowski, S. (2020). Increasing Energy Efficiency and Productivity of the Comminution Process in Tumbling Mills by Indirect Measurements of Internal Dynamics – An Overview. Energies, 13 (24), 6735. doi: https://doi.org/10.3390/en13246735
- Golpayegani, M. H., Rezai, B. (2022). Modelling the power draw of tumbling mills: A comprehensive review. Physicochemical Problems of Mineral Processing, 58 (4). doi: https://doi.org/10.37190/ppmp/151600
- Govender, I., Powell, M. S. (2006). An empirical power model derived from 3D particle tracking experiments. Minerals Engineering, 19 (10), 1005–1012. doi: https://doi.org/10.1016/j.mineng.2006.03.017
- Bbosa, L. S., Govender, I., Mainza, A. N., Powell, M. S. (2011). Power draw estimations in experimental tumbling mills using PEPT. Minerals Engineering, 24 (3-4), 319–324. doi: https://doi.org/10.1016/j.mineng.2010.10.005
- Bbosa, L. S., Govender, I., Mainza, A. (2016). Development of a novel methodology to determine mill power draw. International Journal of Mineral Processing, 149, 94–103. doi: https://doi.org/10.1016/j.minpro.2016.02.009
- Tohry, A., Chehreh Chelgani, S., Matin, S. S., Noormohammadi, M. (2020). Power-draw prediction by random forest based on operating parameters for an industrial ball mill. Advanced Powder Technology, 31 (3), 967–972. doi: https://doi.org/10.1016/j.apt.2019.12.012
- Tavares, L. M. (2017). A Review of Advanced Ball Mill Modelling. KONA Powder and Particle Journal, 34, 106–124. doi: https://doi.org/10.14356/kona.2017015
- Kelly, E. G., Spottiswood, D. J. (1982). Introduction to mineral processing. Wiley, 491.
- Gupta, A., Yan, D. (2016). Mineral processing design and operations: An introduction. Elsevier. doi: https://doi.org/10.1016/c2014-0-01236-1
- Wills, B. A., Finch, J. (2015). Wills’ mineral processing technology: an introduction to the practical aspects of ore treatment and mineral recovery. Butterworth-Heinemann. doi: https://doi.org/10.1016/c2010-0-65478-2
- King, R. P. (2001). Modeling and simulation of mineral processing systems. Butterworth-Heinemann. doi: https://doi.org/10.1016/c2009-0-26303-3
- Chieregati, A. C., Delboni Júnior, H. (2001). Novo método de caracterização tecnológica para cominuição de minérios. São Paulo: EPUSP.
- Malyarov, P., Dolgov, O., Kovalev, P. (2020). Mineral raw material disintegration mechanisms in ball mills and distribution of grinding energy between sequential stages. Mining of Mineral Deposits, 14 (2), 25–33. doi: https://doi.org/10.33271/mining14.02.025
- Azooz, K. (2021). Improving productivity based on the movement of materials inside a grinding cement mill. Kufa Journal of Engineering, 10 (4), 1–15. doi: https://doi.org/10.30572/2018/kje/100401
- Boemer, D., Ponthot, J.-P. (2016). DEM modeling of ball mills with experimental validation: influence of contact parameters on charge motion and power draw. Computational Particle Mechanics, 4 (1), 53–67. doi: https://doi.org/10.1007/s40571-016-0125-4
- Naumenko, Y., Deineka, K. (2023). Building a model of the impact grinding mechanism in a tumbling mill based on data visualization. Eastern-European Journal of Enterprise Technologies, 3 (7 (123)), 65–73. doi: https://doi.org/10.15587/1729-4061.2023.283073
- Napier-Munn, T. J., Morrell, S., Morrison, R. D., Kojovic, T. (1996). Mineral comminution circuits: Their operation and optimisation. Vol. 2. Julius Kruttschnitt Mineral Research Centre, University of Queensland, 413.
- Powell, M. S., McBride, A. T. (2004). A three-dimensional analysis of media motion and grinding regions in mills. Minerals Engineering, 17 (11-12), 1099–1109. doi: https://doi.org/10.1016/j.mineng.2004.06.022
- Morrison, A. J., Govender, I., Mainza, A. N., Parker, D. J. (2016). The shape and behaviour of a granular bed in a rotating drum using Eulerian flow fields obtained from PEPT. Chemical Engineering Science, 152, 186–198. doi: https://doi.org/10.1016/j.ces.2016.06.022
- de Klerk, D. N., Govender, I., Mainza, A. N. (2019). Geometric features of tumbling mill flows: A positron emission particle tracking investigation. Chemical Engineering Science, 206, 41–49. doi: https://doi.org/10.1016/j.ces.2019.05.020
- Cleary, P. W. (2001). Recent advances in dem modelling of tumbling mills. Minerals Engineering, 14 (10), 1295–1319. doi: https://doi.org/10.1016/s0892-6875(01)00145-5
- Wang, M. H., Yang, R. Y., Yu, A. B. (2012). DEM investigation of energy distribution and particle breakage in tumbling ball mills. Powder Technology, 223, 83–91. doi: https://doi.org/10.1016/j.powtec.2011.07.024
- Govender, I., Richter, M. C., Mainza, A. N., De Klerk, D. N. (2016). A positron emission particle tracking investigation of the scaling law governing free surface flows in tumbling mills. AIChE Journal, 63 (3), 903–913. doi: https://doi.org/10.1002/aic.15453
- Yin, Z., Peng, Y., Li, T., Wu, G. (2018). DEM Investigation of Mill Speed and Lifter Face Angle on Charge Behavior in Ball Mills. IOP Conference Series: Materials Science and Engineering, 394, 032084. doi: https://doi.org/10.1088/1757-899x/394/3/032084
- Naumenko, Y. (2017). Modeling a flow pattern of the granular fill in the cross section of a rotating chamber. Eastern-European Journal of Enterprise Technologies, 5 (1 (89)), 59–69. doi: https://doi.org/10.15587/1729-4061.2017.110444
- Naumenko, Y. (2017). Modeling of fracture surface of the quasi solid-body zone of motion of the granular fill in a rotating chamber. Eastern-European Journal of Enterprise Technologies, 2 (1 (86)), 50–57. doi: https://doi.org/10.15587/1729-4061.2017.96447
- Naumenko, Y., Sivko, V. (2017). The rotating chamber granular fill shear layer flow simulation. Eastern-European Journal of Enterprise Technologies, 4 (7 (88)), 57–64. doi: https://doi.org/10.15587/1729-4061.2017.107242
- Deineka, K., Naumenko, Y. (2019). Revealing the effect of decreased energy intensity of grinding in a tumbling mill during self-excitation of auto-oscillations of the intrachamber fill. Eastern-European Journal of Enterprise Technologies, 1 (1), 6–15. doi: https://doi.org/10.15587/1729-4061.2019.155461
- Deineka, K., Naumenko, Y. (2019). Establishing the effect of a decrease in power intensity of self-oscillating grinding in a tumbling mill with a reduction in an intrachamber fill. Eastern-European Journal of Enterprise Technologies, 6 (7 (102)), 43–52. doi: https://doi.org/10.15587/1729-4061.2019.183291
- Deineka, K., Naumenko, Y. (2020). Establishing the effect of decreased power intensity of self-oscillatory grinding in a tumbling mill when the crushed material content in the intra-chamber fill is reduced. Eastern-European Journal of Enterprise Technologies, 4 (1 (106)), 39–48. doi: https://doi.org/10.15587/1729-4061.2020.209050
- Deineka, K., Naumenko, Y. (2021). Establishing the effect of a simultaneous reduction in the filling load inside a chamber and in the content of the crushed material on the energy intensity of self-oscillatory grinding in a tumbling mill. Eastern-European Journal of Enterprise Technologies, 1 (1 (109)), 77–87. doi: https://doi.org/10.15587/1729-4061.2021.224948
- Deineka, K., Naumenko, Y. (2022). Revealing the mechanism of stability loss of a two-fraction granular flow in a rotating drum. Eastern-European Journal of Enterprise Technologies, 4 (1 (118)), 34–46. doi: https://doi.org/10.15587/1729-4061.2022.263097
- Deineka, K. Yu., Naumenko, Yu. V. (2018). The tumbling mill rotation stability. Scientific Bulletin of National Mining University, 1, 60–68. doi: https://doi.org/10.29202/nvngu/2018-1/10
- Gupta, V. K., Sharma, S. (2014). Analysis of ball mill grinding operation using mill power specific kinetic parameters. Advanced Powder Technology, 25 (2), 625–634. doi: https://doi.org/10.1016/j.apt.2013.10.003
- Hanumanthappa, H., Vardhan, H., Mandela, G. R., Kaza, M., Sah, R., Shanmugam, B. K. (2020). A comparative study on a newly designed ball mill and the conventional ball mill performance with respect to the particle size distribution and recirculating load at the discharge end. Minerals Engineering, 145, 106091. doi: https://doi.org/10.1016/j.mineng.2019.106091
- ISO 924:1989. Coal preparation plant – Principles and conventions for flowsheets. Available at: https://www.iso.org/standard/5340.html
- Maschinen für die mechanische Aufbereitung von Mineralien und ähnlichen festen Stoffen - Sicherheit - Teil 3: Spezifische Anforderungen für Brecher und Mühlen; Deutsche Fassung EN 1009-3:2020. Available at: https://www.din.de/de/mitwirken/normenausschuesse/nam/veroeffentlichungen/wdc-beuth:din21:316006092
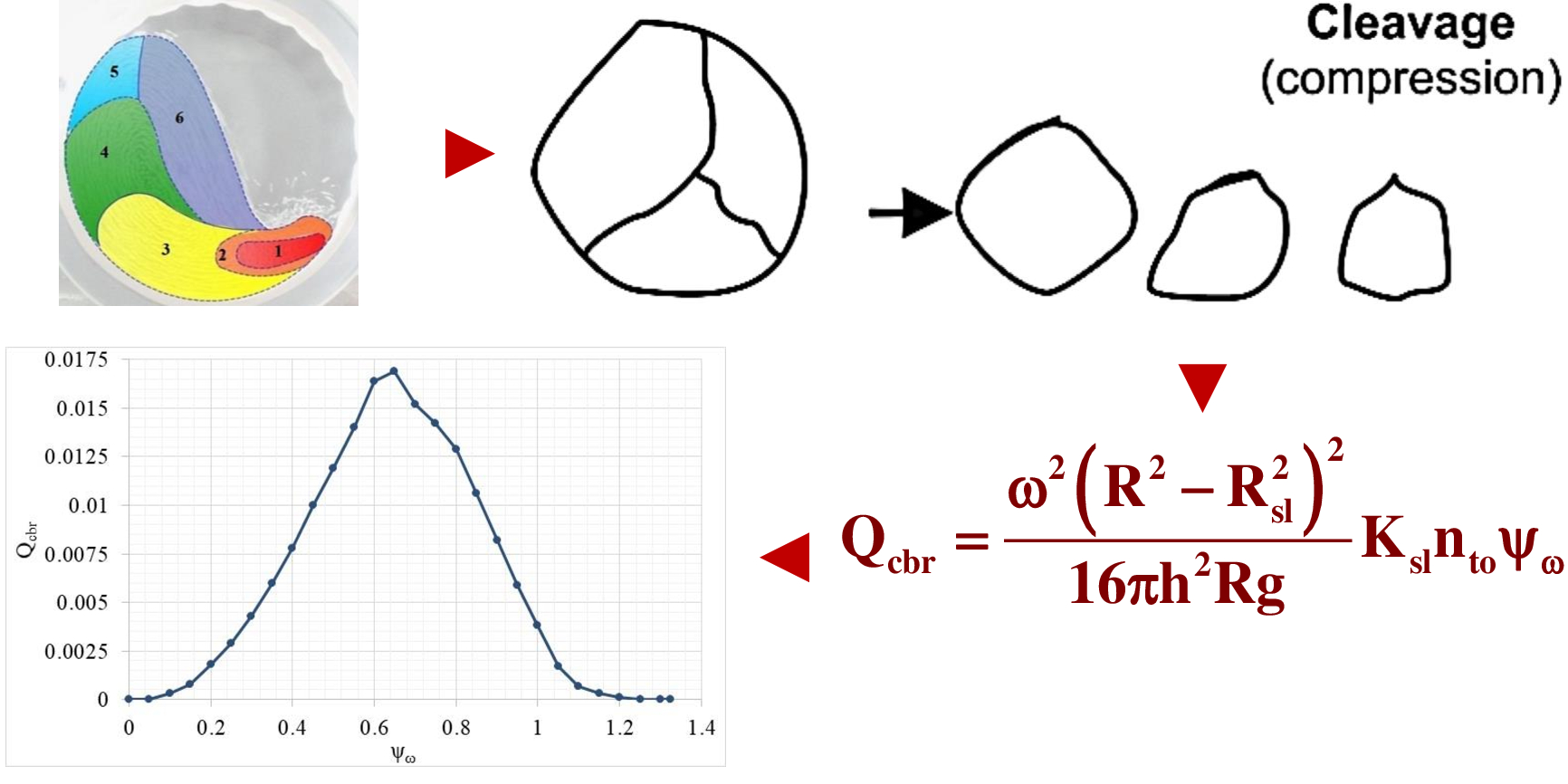
Downloads
Published
How to Cite
Issue
Section
License
Copyright (c) 2023 Yuriy Naumenko, Kateryna Deineka

This work is licensed under a Creative Commons Attribution 4.0 International License.
The consolidation and conditions for the transfer of copyright (identification of authorship) is carried out in the License Agreement. In particular, the authors reserve the right to the authorship of their manuscript and transfer the first publication of this work to the journal under the terms of the Creative Commons CC BY license. At the same time, they have the right to conclude on their own additional agreements concerning the non-exclusive distribution of the work in the form in which it was published by this journal, but provided that the link to the first publication of the article in this journal is preserved.
A license agreement is a document in which the author warrants that he/she owns all copyright for the work (manuscript, article, etc.).
The authors, signing the License Agreement with TECHNOLOGY CENTER PC, have all rights to the further use of their work, provided that they link to our edition in which the work was published.
According to the terms of the License Agreement, the Publisher TECHNOLOGY CENTER PC does not take away your copyrights and receives permission from the authors to use and dissemination of the publication through the world's scientific resources (own electronic resources, scientometric databases, repositories, libraries, etc.).
In the absence of a signed License Agreement or in the absence of this agreement of identifiers allowing to identify the identity of the author, the editors have no right to work with the manuscript.
It is important to remember that there is another type of agreement between authors and publishers – when copyright is transferred from the authors to the publisher. In this case, the authors lose ownership of their work and may not use it in any way.