The filament winding method’s finishing process impact on high-fidelity specimens: homogenity of density, fiber volume fraction, outer surface roughness and tensile strength
DOI:
https://doi.org/10.15587/1729-4061.2023.288025Keywords:
filament winding, CFRP, surface roughness, fabrication, fiber fraction, Void, Tensile strengthAbstract
Filament winding is a widely used method for producing tubes and pressure vessels from composite materials. However, overlapping of fibers during the winding process can lead to rough surface and increased voids in the finished product. To improve the quality of CFRP materials produced through filament winding, the structure is cured either at room temperature or in an oven with a controlled heat profile, depending on the type of resin used. Various finishing techniques, including shrink tape, compression molding, and vacuum compression molding, have been attempted to improve the quality of the specimen. Among these techniques, vacuum compression molding has been found to deliver the best results in terms of surface roughness, with average roughness (Ra) values of 0.35 μm in the fiber direction and 0.61 μm in the transverse direction. This level of roughness is comparable to that achieved through milling machine manufacturing. Moreover, this technique ensures uniformity in fiber composition and volume fraction, achieving a homogeneous density of 1364.49 kg/m3 and the highest fiber volume fraction of 63 %. As a result, remarkable mechanical attributes, such as a tensile strength of 926.07 MPa and a stiffness of 21.35 GPa, can be obtained. In addition, by utilizing various finishing techniques, the tensile strength of these properties can be increased by up to 80 %. CFRP is a versatile material with unique characteristics, and selecting appropriate finishing techniques such as vacuum compression molding can significantly enhance its overall quality and mechanical properties. However, one drawback of the filament winding method is the poor outer surface finish which can be improved by vacuum compression molding
Supporting Agency
- This study was conducted with the framework of a funded scientific project by the Ministry of Research, Technology, and Higher Education of the Republic of Indonesia. The study Conducted in the laboratory of the National Research and Innovation Agency.
References
- Gay, D. (2014). Composite materials: design and applications. Boca Raton: CRC Press, 635. doi: https://doi.org/10.1201/b17106
- Kaw, A. K. (2006). Mechanics of composite materials. Boca Raton, FL: Taylor & Francis. Available at: https://sarrami.iut.ac.ir/sites/sarrami.iut.ac.ir/files/files_course/01-mechanics_of_composite_materials_sbookfi.org_.pdf
- Quanjin, M., Rejab, M. R. M., Kaige, J., Idris, M. S., Harith, M. N. (2018). Filament winding technique, experiment and simulation analysis on tubular structure. IOP Conference Series: Materials Science and Engineering, 342 (1), 012029. doi: https://doi.org/10.1088/1757-899x/342/1/012029
- Sherif, G., Chukov, D., Tcherdyntsev, V., Torokhov, V. (2019). Effect of Formation Route on the Mechanical Properties of the Polyethersulfone Composites Reinforced with Glass Fibers. Polymers, 11 (8), 1364. doi: https://doi.org/10.3390/polym11081364
- Sun, G., Yu, H., Wang, Z., Xiao, Z., Li, Q. (2019). Energy absorption mechanics and design optimization of CFRP/aluminium hybrid structures for transverse loading. International Journal of Mechanical Sciences, 150, 767–783. doi: https://doi.org/10.1016/j.ijmecsci.2018.10.043
- Davies, P. (2016). Behavior of marine composite materials under deep submergence. Marine Applications of Advanced Fibre-Reinforced Composites, 125–145. doi: https://doi.org/10.1016/b978-1-78242-250-1.00006-5
- Rajak, D. K., Wagh, P. H., Linul, E. (2021). Manufacturing Technologies of Carbon/Glass Fiber-Reinforced Polymer Composites and Their Properties: A Review. Polymers, 13 (21), 3721. doi: https://doi.org/10.3390/polym13213721
- Vasiliev, V. V., Krikanov, A. A., Razin, A. F. (2003). New generation of filament-wound composite pressure vessels for commercial applications. Composite Structures, 62 (3-4), 449–459. doi: https://doi.org/10.1016/j.compstruct.2003.09.019
- Wang, R., Jiao, W., Liu, W., Yang, F., He, X. (2011). Slippage coefficient measurement for non-geodesic filament-winding process. Composites Part A: Applied Science and Manufacturing, 42 (3), 303–309. doi: https://doi.org/10.1016/j.compositesa.2010.12.002
- Wang, Z., Almeida, J. H. S., Ashok, A., Wang, Z., Castro, S. G. P. (2022). Lightweight design of variable-angle filament-wound cylinders combining Kriging-based metamodels with particle swarm optimization. Structural and Multidisciplinary Optimization, 65 (5). doi: https://doi.org/10.1007/s00158-022-03227-8
- Goodship, V., Middleton, B., Cherrington, R. (2016). Design and Manufacture of Plastic Components for Multifunctionality. Elsevier. doi: https://doi.org/10.1016/c2014-0-00223-7
- Quanjin, M., Rejab, M. R. M., Idris, M. S., Zhang, B., Kumar, N. M. (2019). Filament Winding Technique: SWOT Analysis and Applied Favorable Factors. SCIREA Journal of Mechanical Engineering, 3 (1). Available at: https://www.researchgate.net/publication/332329420_Filament_winding_technique_SWOT_analysis_and_applied_favorable_factors
- Lasn, K., Mulelid, M. (2020). The effect of processing on the microstructure of hoop-wound composite cylinders. Journal of Composite Materials, 54 (26), 3981–3997. doi: https://doi.org/10.1177/0021998320923139
- Fernlund, G., Wells, J., Fahrang, L., Kay, J., Poursartip, A. (2016). Causes and remedies for porosity in composite manufacturing. IOP Conference Series: Materials Science and Engineering, 139, 012002. doi: https://doi.org/10.1088/1757-899x/139/1/012002
- Scott, A. E., Sinclair, I., Spearing, S. M., Mavrogordato, M. N., Hepples, W. (2014). Influence of voids on damage mechanisms in carbon/epoxy composites determined via high resolution computed tomography. Composites Science and Technology, 90, 147–153. doi: https://doi.org/10.1016/j.compscitech.2013.11.004
- Liu, L., Zhang, B.-M., Wang, D.-F., Wu, Z.-J. (2006). Effects of cure cycles on void content and mechanical properties of composite laminates. Composite Structures, 73 (3), 303–309. doi: https://doi.org/10.1016/j.compstruct.2005.02.001
- Ekuase, O. A., Anjum, N., Eze, V. O., Okoli, O. I. (2022). A Review on the Out-of-Autoclave Process for Composite Manufacturing. Journal of Composites Science, 6 (6), 172. doi: https://doi.org/10.3390/jcs6060172
- Harshe, R. (2015). A Review on Advanced Out-of-Autoclave Composites Processing. Journal of the Indian Institute of Science, 95 (3), 207–220. Available at: https://www.researchgate.net/publication/283229706_A_Review_on_Advanced_Out-of-Autoclave_Composites_Processing
- Peters, S. T. (Ed.) (2011). Composite filament winding. ASM International. doi: https://doi.org/10.31399/asm.tb.cfw.9781627083386
- Quanjin, M., Rejab, M. R. M., Idris, M. S., Bachtiar, B., Siregar, J. P., Harith, M. N. (2017). Design and optimize of 3-axis filament winding machine. IOP Conference Series: Materials Science and Engineering, 257, 012039. doi: https://doi.org/10.1088/1757-899x/257/1/012039
- Krysiak, P., Kaleta, J., Gąsior, P., Błachut, A., Rybczyński, R. (2017). Identification of strains in a multilayer composite pipe. Journal of Science of the Gen. Tadeusz Kosciuszko Military Academy of Land Forces, 186 (4), 272–282. doi: https://doi.org/10.5604/01.3001.0010.7233
- Mansour, G., Kyratsis, P., Korlos, A., Tzetzis, D. (2021). Investigation into the Effect of Cutting Conditions in Turning on the Surface Properties of Filament Winding GFRP Pipe Rings. Machines, 9 (1), 16. doi: https://doi.org/10.3390/machines9010016
- Schorník, V., Daňa, M., Zetková, I. (2015). The Influence of the Cutting Conditions on the Machined Surface Quality when the CFRP is Machined. Procedia Engineering, 100, 1270–1276. doi: https://doi.org/10.1016/j.proeng.2015.01.493
- Lehtiniemi, P., Dufva, K., Berg, T., Skrifvars, M., Järvelä, P. (2011). Natural fiber-based reinforcements in epoxy composites processed by filament winding. Journal of Reinforced Plastics and Composites, 30 (23), 1947–1955. doi: https://doi.org/10.1177/0731684411431019
- Henninger, F., Friedrich, K. (2002). Thermoplastic filament winding with online-impregnation. Part A: process technology and operating efficiency. Composites Part A: Applied Science and Manufacturing, 33 (11), 1479–1486. doi: https://doi.org/10.1016/s1359-835x(02)00135-5
- Andrianov, A., Tomita, E. K., Veras, C. A. G., Telles, B. (2022). A Low-Cost Filament Winding Technology for University Laboratories and Startups. Polymers, 14 (5), 1066. doi: https://doi.org/10.3390/polym14051066
- Geier, N., Pereszlai, C. (2019). Analysis of Characteristics of Surface Roughness of Machined CFRP Composites. Periodica Polytechnica Mechanical Engineering, 64 (1), 67–80. doi: https://doi.org/10.3311/ppme.14436
- Yao, Y., Chen, S. (2012). The effects of fiber’s surface roughness on the mechanical properties of fiber-reinforced polymer composites. Journal of Composite Materials, 47 (23), 2909–2923. doi: https://doi.org/10.1177/0021998312459871
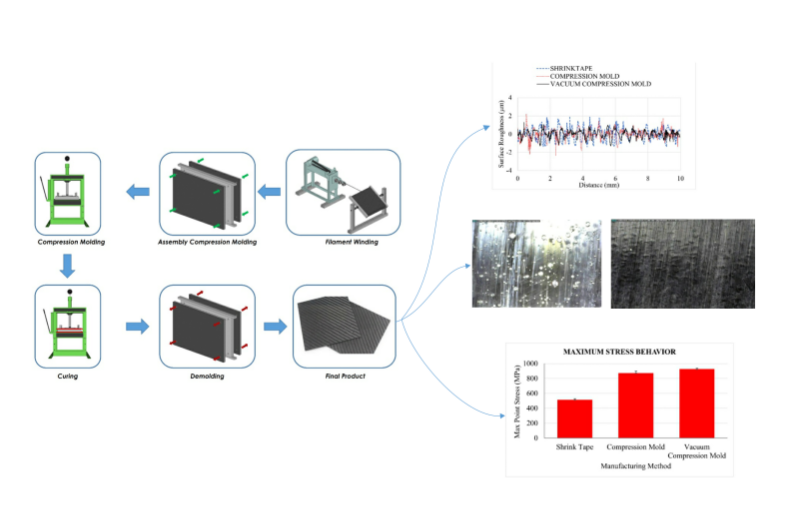
Downloads
Published
How to Cite
Issue
Section
License
Copyright (c) 2023 Herry Purnomo, Tresna Priyana Soemardi, Hendri D.S. Budiono, Heri Budi Wibowo, Mahfud Ibadi

This work is licensed under a Creative Commons Attribution 4.0 International License.
The consolidation and conditions for the transfer of copyright (identification of authorship) is carried out in the License Agreement. In particular, the authors reserve the right to the authorship of their manuscript and transfer the first publication of this work to the journal under the terms of the Creative Commons CC BY license. At the same time, they have the right to conclude on their own additional agreements concerning the non-exclusive distribution of the work in the form in which it was published by this journal, but provided that the link to the first publication of the article in this journal is preserved.
A license agreement is a document in which the author warrants that he/she owns all copyright for the work (manuscript, article, etc.).
The authors, signing the License Agreement with TECHNOLOGY CENTER PC, have all rights to the further use of their work, provided that they link to our edition in which the work was published.
According to the terms of the License Agreement, the Publisher TECHNOLOGY CENTER PC does not take away your copyrights and receives permission from the authors to use and dissemination of the publication through the world's scientific resources (own electronic resources, scientometric databases, repositories, libraries, etc.).
In the absence of a signed License Agreement or in the absence of this agreement of identifiers allowing to identify the identity of the author, the editors have no right to work with the manuscript.
It is important to remember that there is another type of agreement between authors and publishers – when copyright is transferred from the authors to the publisher. In this case, the authors lose ownership of their work and may not use it in any way.