Визначення параметрів газу в резонансних трубах та каналах двигунів з періодичним робочим процесом методом поршневої аналогії
DOI:
https://doi.org/10.15587/1729-4061.2023.288520Ключові слова:
пульсуючий двигун, резонансна труба, моделювання течії, метод «рідкого» поршня, поршнева аналогіяАнотація
Досліджується процес течії газу в резонансній трубі двигуна з періодичним робочим процесом. Аналіз різних моделей течії та порівняння відомих даних показали, що залишаються не вирішені до кінця проблеми побудови замкнутих 0-мірних моделей робочого циклу для деяких типів двигунів. Відповідно до цього виникає питання про розмірність моделей окремих елементів двигунів, включаючи модель резонансної труби, які необхідно включити в загальну модель циклу, особливо, на початковому етапі її розробки.
Для розв'язання виявлених проблем удосконалено математичну модель течії газу, побудовану на базі аналогії з «рідким» поршнем. На відміну від відомих, модель поршневої аналогії дозволяє розраховувати миттєву швидкість газу, опосередковану за довжиною труби, за допомогою чисельного рішення диференціального рівняння для швидкості.
Для перевірки розробленої моделі обрано альтернативну кінцево-різницеву 1-мірну газодинамічну модель, за допомогою якої виконано тестове моделювання течії повітря в трубі. Встановлено, що поршнева модель дозволяє знайти швидкість течії з точністю до 5 % для перепаду тиску, що змінюється за синусоїдальним законом. Знайдено допустимі межі зміни частоти коливань та довжини труби, при яких поршнева модель має мінімальну помилку порівняно з 1-мірною моделлю.
За результатами дослідження зроблено висновок у тому, що при невеликій масі та інерції рідкого поршня пропонована модель дає результати, близькі до тих, які забезпечують складніші моделі з вищою розмірністю. Це вказує на можливість застосування поршневої моделі елементів типу труб у складі 0-мірної термодинамічної моделі двигунів з періодичним робочим процесом як на наближену альтернативу традиційним 1-мірним моделям течії
Посилання
- Gupta, H. N. (2012). Fundamentals of Internal Combustion Engines. PHI Learning Pvt. Ltd., 676.
- Munjal, M. L. (2014). Acoustics of Ducts and Mufflers. John Wiley & Sons, 416.
- Ismail, R. S., Jailani, A., Haron, M. A. (2017). Kadenancy effect, acoustical resonance effect valveless pulse jet engine. AIP Conference Proceedings. doi: https://doi.org/10.1063/1.5002230
- Salih, A. (2016). Method of Characteristics. Available at: https://www.iist.ac.in/sites/default/files/people/IN08026/MoC_0.pdf
- Kim, K.-H., Kong, K.-J. (2021). 1D–3D Coupling for Gas Flow Analysis of the Air-Intake System in a Compression Ignition Engine. Journal of Marine Science and Engineering, 9 (5), 553. doi: https://doi.org/10.3390/jmse9050553
- Onorati, A., Montenegro, G. (2020). 1D and Multi-D Modeling Techniques for IC Engine Simulation. SAE International, 550. doi: https://doi.org/10.4271/9780768099522
- Kumar, S., Prasad, S. S., Krishna, V. (2014). Design of Pulse Jet Engine for UAV. International Journal of Engineering Research & Technology (IJERT), 3 (9), 670–675. Available at: https://www.ijert.org/research/design-of-pulse-jet-engine-for-uav-IJERTV3IS090544.pdf
- Ganesan, V. (2000). Computer Simulation of Compression-Ignition Engine Processes. Universities Press, 523.
- Kalikatzarakisa, M., Coraddua, A., Theotokatosa, G., Oneto, L. (2021). Development of a zero-dimensional model and application on a medium-speed marine four-stoke diesel engine. 3rd International Conference on Modelling and Optimisation of Ship Energy Systems (MOSES2019). Available at: https://www.researchgate.net/publication/352119154_Development_of_a_zero-dimensional_model_and_application_on_a_medium-speed_marine_four-stoke_diesel_engine
- Khrulev, A., Saraiev, O. (2022). Building a mathematical model of the destruction of a connecting rod-piston group in the car engine at hydraulic lock. Eastern-European Journal of Enterprise Technologies, 3 (7 (117)), 40–49. doi: https://doi.org/10.15587/1729-4061.2022.259454
- Khrulev, A. (2023). Analysis of pneumatic catapult launch system parameters, taking into account engine and UAV characteristics. Advanced UAV, 3 (1), 10–24. Available at: https://publish.mersin.edu.tr/index.php/uav/article/view/1045
- Bellér, G., Árpád, I., Kiss, J. T., Kocsis, D. (2021). AVL Boost: a powerful tool for research and education. Journal of Physics: Conference Series, 1935 (1), 012015. doi: https://doi.org/10.1088/1742-6596/1935/1/012015
- Cordon, D., Dean, Ch., Steciak, J., Beyerlein, S. (2007). One-Dimensional Engine Modeling and Validation using Ricardo WAVE. Final Report KLK434-B, N07-09. National Institute for Advanced Transportation Technology, University of Idaho. Available at: https://www.academia.edu/18805887/ONE_DIMENSIONAL_ENGINE_MODELING_AND_VALIDATION_USING_RICARDO_WAVE
- Aradhye, O., Bari, S. (2017). Continuously Varying Exhaust Pipe Length and Diameter to Improve the Performance of a Naturally Aspirated SI Engine. ASME 2017 International Mechanical Engineering Congress and Exposition. doi: https://doi.org/10.1115/imece2017-70638
- Borowski, G., Ghazal, O. (2019). Use of Water Injection Technique to Improve the Combustion Efficiency of the Spark-Ignition Engine: A Model Study. Journal of Ecological Engineering, 20 (2), 226–233. doi: https://doi.org/10.12911/22998993/99689
- Magdas, V. B., Mastan, D. C., Burnete, N. (2020). Simulation possibilities of the internal combustion engine management elements using Lotus Engine Simulation software. IOP Conference Series: Materials Science and Engineering, 997 (1), 012121. doi: https://doi.org/10.1088/1757-899x/997/1/012121
- Thompson, B., Yoon, H.-S. (2020). Internal Combustion Engine Modeling Framework in Simulink: Gas Dynamics Modeling. Modelling and Simulation in Engineering, 2020, 1–16. doi: https://doi.org/10.1155/2020/6787408
- Kong, K.-J., Jung, S.-H., Jeong, T.-Y., Koh, D.-K. (2019). 1D-3D coupling algorithm for unsteady gas flow analysis in pipe systems. Journal of Mechanical Science and Technology, 33 (9), 4521–4528. doi: https://doi.org/10.1007/s12206-019-0848-2
- Chiodi, M. (2011). An Innovative 3D-CFD-Approach towards Virtual Development of Internal Combustion Engines. Springer, Wiesbaden, 245. doi: https://doi.org/10.1007/978-3-8348-8131-1
- Mohsen, K. K., Hussain, Z. H. (2021). Numerical Comparison between Two Tailpipe Shapes of Valved Pulsejet Engine. IOP Conference Series: Materials Science and Engineering, 1094 (1), 012001. doi: https://doi.org/10.1088/1757-899x/1094/1/012001
- Melo, A. S. M. (2019). Pulsejet Engine Performance Estimation (Versão Revista Após Discussão). Covilhã, 72. Available at: https://web.archive.org/web/20200709134701/https://ubibliorum.ubi.pt/bitstream/10400.6/8866/1/6820_14614.pdf
- Isac, J. K. R., Mohanraj, L., Sai, E. S., Kannan, V. K. (2014). Numerical simulation of a hydrocarbon fuelled valveless pulsejet. Propulsion and Power Research, 3 (2), 90–95. doi: https://doi.org/10.1016/j.jppr.2014.05.004
- Smajevic, I. (2010). Experimental Study and Computational Modelling of Gas-Fired Pulse Combustion. International Journal of Automotive and Mechanical Engineering, 1, 1–12. doi: https://doi.org/10.15282/ijame.1.2010.1.0001
- Van Heerbeek, P. A. (2008). Mathematical Modelling of a Pulse Combustor of the Helmholtz-type. Delft, 146. Available at: https://diamhomes.ewi.tudelft.nl/~kvuik/numanal/heerbeek_afst.pdf
- Anand, R., Kukar, N., Kumar, V., Nandakumar, K. (2011). Design and realization of a valveless pulsejet engine to demonstrate pulse mode combustion. 25th National Convention of Aerospace Engineering (NCAE 2011). Ranchi.
- Anand, V., Jodele, J., Shaw, V., Russell, A., Prisell, E., Lyrsell, O., Gutmark, E. (2020). Visualization of Valved Pulsejet Combustors and Evidence of Compression Ignition. Flow, Turbulence and Combustion, 106 (3), 901–924. doi: https://doi.org/10.1007/s10494-020-00203-4
- Anand, V., Jodele, J., Prisell, E., Lyrsell, O., Gutmark, E. (2020). Dynamic Features of Internal and External Flowfields of Pulsejet Engines. AIAA Journal, 58 (10), 4204–4211. doi: https://doi.org/10.2514/1.j059685
- Roache, P. J. (1998). Fundamentals of Computational Fluid Dynamics. Hermosa Pub, 648.
- XLfit. Expanding the Power of Excel. Industry standard models built-in with support for designing and sharing your own models. Available at: https://www.idbs.com/xlfit/
- Geng, T., Paxson, D., Zheng, F., Kuznetsov, A., Roberts, W. (2008). Comparison Between Numerically Simulated and Experimentally Measured Flowfield Quantities Behind a Pulsejet. 44th AIAA/ASME/SAE/ASEE Joint Propulsion Conference & Exhibit. doi: https://doi.org/10.2514/6.2008-5046
- Idelchik, I. E. (1966). Handbook of Hydraulic Resistance. Coefficients of Local Resistance and of Friction. Israel Program for Scientific Translations Ltd., 517. Available at: https://www.nrc.gov/docs/ML1220/ML12209A041.pdf
- Biringen, S., Chow, C. (2011). An Introduction to Computational Fluid Mechanics by Example. John Wiley & Sons, Inc. doi: https://doi.org/10.1002/9780470549162
- Pearson, R. J., Bassett, M. D., Fleming, N. P., Rodemann, T. (2002). Lotus Engineering Software – An Approach to Model-Based Design. The 2002 North American ADAMS Conference in Scottsdale. Arizona. Available at: https://ru.scribd.com/document/215011237/Lotus-Paper
- Blackstock, D. T. (2000). Fundamentals of Physical Acoustics. Wiley-Interscience, 560.
- Moussou, P., Testud, Ph., Aure´gan, Y., Hirschberg, A. (2007). An Acoustic Criterion for the Whistling of Orifices in Pipes. ASME 2007 Pressure Vessels and Piping Conference. doi: https://doi.org/10.1115/pvp2007-26157
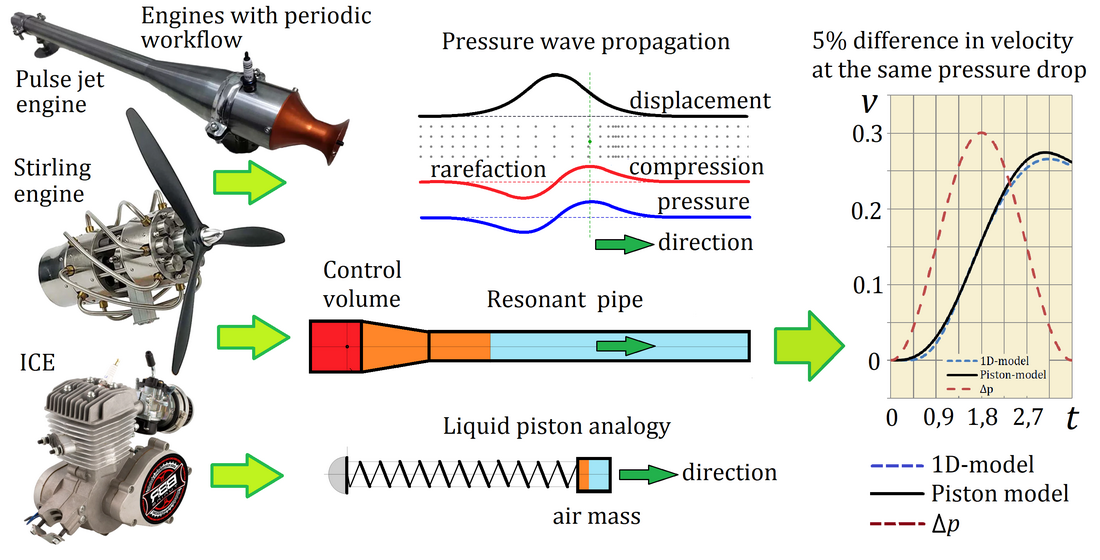
##submission.downloads##
Опубліковано
Як цитувати
Номер
Розділ
Ліцензія
Авторське право (c) 2023 Alexander Khrulev

Ця робота ліцензується відповідно до Creative Commons Attribution 4.0 International License.
Закріплення та умови передачі авторських прав (ідентифікація авторства) здійснюється у Ліцензійному договорі. Зокрема, автори залишають за собою право на авторство свого рукопису та передають журналу право першої публікації цієї роботи на умовах ліцензії Creative Commons CC BY. При цьому вони мають право укладати самостійно додаткові угоди, що стосуються неексклюзивного поширення роботи у тому вигляді, в якому вона була опублікована цим журналом, але за умови збереження посилання на першу публікацію статті в цьому журналі.
Ліцензійний договір – це документ, в якому автор гарантує, що володіє усіма авторськими правами на твір (рукопис, статтю, тощо).
Автори, підписуючи Ліцензійний договір з ПП «ТЕХНОЛОГІЧНИЙ ЦЕНТР», мають усі права на подальше використання свого твору за умови посилання на наше видання, в якому твір опублікований. Відповідно до умов Ліцензійного договору, Видавець ПП «ТЕХНОЛОГІЧНИЙ ЦЕНТР» не забирає ваші авторські права та отримує від авторів дозвіл на використання та розповсюдження публікації через світові наукові ресурси (власні електронні ресурси, наукометричні бази даних, репозитарії, бібліотеки тощо).
За відсутності підписаного Ліцензійного договору або за відсутністю вказаних в цьому договорі ідентифікаторів, що дають змогу ідентифікувати особу автора, редакція не має права працювати з рукописом.
Важливо пам’ятати, що існує і інший тип угоди між авторами та видавцями – коли авторські права передаються від авторів до видавця. В такому разі автори втрачають права власності на свій твір та не можуть його використовувати в будь-який спосіб.