Identifying the influence of design parameters of a hydrostatic bearing in an aircraft fuel pump on its static characteristics
DOI:
https://doi.org/10.15587/1729-4061.2023.289426Keywords:
hydrostatic bearing, gear pump, load-bearing capacity, flow balance, temperature regimeAbstract
The object of this study is hydrostatic processes in the sliding bearings of gear-type aviation fuel pumps.
The problem of the influence of the design parameters of the fuel pump bearing on its static characteristics was solved. Load-bearing capacity, lubricant consumption, and operating temperature conditions were considered as static characteristics. The determination of these characteristics was based on the pressure distribution function in the working fluid layer. An option was adopted with two load-bearing chambers located on the working surface of the hydrostatic bearing. Three options for the circumferential arrangement of chambers relative to the line of action of the external load were studied. A quantitative assessment of the effect of increasing the temperature of the working fluid on the consumption of lubricant and bearing capacity is given.
It has been established that with an increase in the angle of position of chambers relative to the line of action of the external load, the flow rate of the working fluid in the bearing increases, and its load-bearing capacity decreases. With a clearance in the bearing of 0.0225 mm, with an increase in the angle of the chambers from 30° to 40°, the flow of working fluid through the bearing increases by approximately 1.64 times. When the gap increases to 0.0425 mm and the angle of the chambers changes from 30° to 40°, the flow rate of the working fluid increases by approximately 1.2 times. The load-bearing capacity of the bearing with an increase in the chamber position angle from 30° to 40° decreases with a gap of 0.0225 mm by approximately 1.6 times, and with a gap of 0.0425 mm by approximately 1.93 times.
An increase in the temperature of the working fluid leads to a decrease in the load-bearing capacity of the bearing by 2.5 % and an increase in the flow rate of the working fluid in the bearing by 4.6 %.
The results allow for more rational design of hydrostatic bearings for fuel gear pumps.
References
- Huang, B., Yun, Y., Pu, K., Zhao, B., Wu, K. (2023). Lubrication performance analysis of Lead-Bismuth Internal-Feedback bearings in the nuclear main pump system. Annals of Nuclear Energy, 192, 109936. doi: https://doi.org/10.1016/j.anucene.2023.109936
- Tacconi, J., Shahpar, S., King, A., Olufeagba, J. P., Khan, R., Sant, I., Yates, M. (2021). Elasto-Hydrodynamic Model of Hybrid Journal Bearings for Aero-Engine Gear Fuel Pump Applications. Journal of Tribology, 144 (3). doi: https://doi.org/10.1115/1.4052479
- Gu, Y., Wang, D., Cheng, L., Schimpf, A., Böhle, M. (2023). A Novel Method to Achieve Fast Multi-Objective Optimization of Hydrostatic Porous Journal Bearings Used in Hydraulic Turbomachine. Journal of Fluids Engineering, 145 (5). doi: https://doi.org/10.1115/1.4057003
- Zhang, J., Shen, Y., Gan, M., Su, Q., Lyu, F., Xu, B., Chen, Y. (2022). Multi-objective optimization of surface texture for the slipper/swash plate interface in EHA pumps. Frontiers of Mechanical Engineering, 17 (4). doi: https://doi.org/10.1007/s11465-022-0704-4
- Shutin, D., Kazakov, Y. (2023). Theoretical and Numerical Investigation of Reduction of Viscous Friction in Circular and Non-Circular Journal Bearings Using Active Lubrication. Lubricants, 11 (5), 218. doi: https://doi.org/10.3390/lubricants11050218
- Chellapandi, P., Rao, C. L. (2022). Development and application of a numerical analysis method for investigating hydro static and hydrodynamic responses of pocket bearing rotor systems. Journal of Fluids and Structures, 109, 103484. doi: https://doi.org/10.1016/j.jfluidstructs.2021.103484
- Liu, S., Yu, C., Ai, C., Zhang, W., Li, Z., Zhang, Y., Jiang, W. (2023). Impact Analysis of Worn Surface Morphology on Adaptive Friction Characteristics of the Slipper Pair in Hydraulic Pump. Micromachines, 14 (3), 682. doi: https://doi.org/10.3390/mi14030682
- Truijen, D. P. K., De Kooning, J. D. M., Fauconnier, D., Vansompel, H., Sergeant, P., Stockman, K. (2022). Axial Flux PMSM Power Take-Off for a Rim-Driven Contra-Rotating Pump-Turbine. 2022 IEEE PES 14th Asia-Pacific Power and Energy Engineering Conference (APPEEC). doi: https://doi.org/10.1109/appeec53445.2022.10072056
- Yu, Z., Shevchenko, S., Radchenko, M., Shevchenko, O., Radchenko, A. (2022). Methodology of Designing Sealing Systems for Highly Loaded Rotary Machines. Sustainability, 14 (23), 15828. doi: https://doi.org/10.3390/su142315828
- Nazin, V. (2023). Revealing the influence of structural and operational parameters of a hydrostatic bearing in a gear-type fuel pump on its main characteristics. Eastern-European Journal of Enterprise Technologies, 2 (1 (122)), 92–98. doi: https://doi.org/10.15587/1729-4061.2023.277755
- Wang, K., Fu, J., Wei, S., Wei, P., Li, T., Jiang, Y. (2022). Lubrication Performance Analysis of Fuel Gear Pump Sliding Bearing under High Speed and Wide Temperature Range. 2022 13th International Conference on Mechanical and Aerospace Engineering (ICMAE). doi: https://doi.org/10.1109/icmae56000.2022.9852503
- Guan, D., Zhou, Z., Zhang, C. (2021). Hydrostatic Bearing Characteristics Investigation of a Spherical Piston Pair with an Annular Orifice Damper in Spherical Pump. Coatings, 11 (8), 1007. doi: https://doi.org/10.3390/coatings11081007
- Fritz, M., Groeb, M. (2021). Increasing performance and energy efficency of a machine tool through hydrostatic linear guideways with single digit micrometre fluid film thickness. MM Science Journal, 2021 (5), 5241–5246. doi: https://doi.org/10.17973/mmsj.2021_11_2021175
- Gao, N., Li, H., Hong, L., Cao, R., Fu, J. (2022). Reliability analysis of journal bearings inside aero-gear pump based on AK-IS method. Journal of Beijing University of Aeronautics and Astronautics, 48 (6), 1057–1064.
- Wei, S., Wang, J., Cui, J., Song, S., Li, H., Fu, J. (2022). Online monitoring of oil film thickness of journal bearing in aviation fuel gear pump. Measurement, 204, 112050. doi: https://doi.org/10.1016/j.measurement.2022.112050
- Bogdanov, O. N., D'yachenko, S. K. (1966). Raschet opor skol'zheniya. Kyiv: Tekhnika, 242.
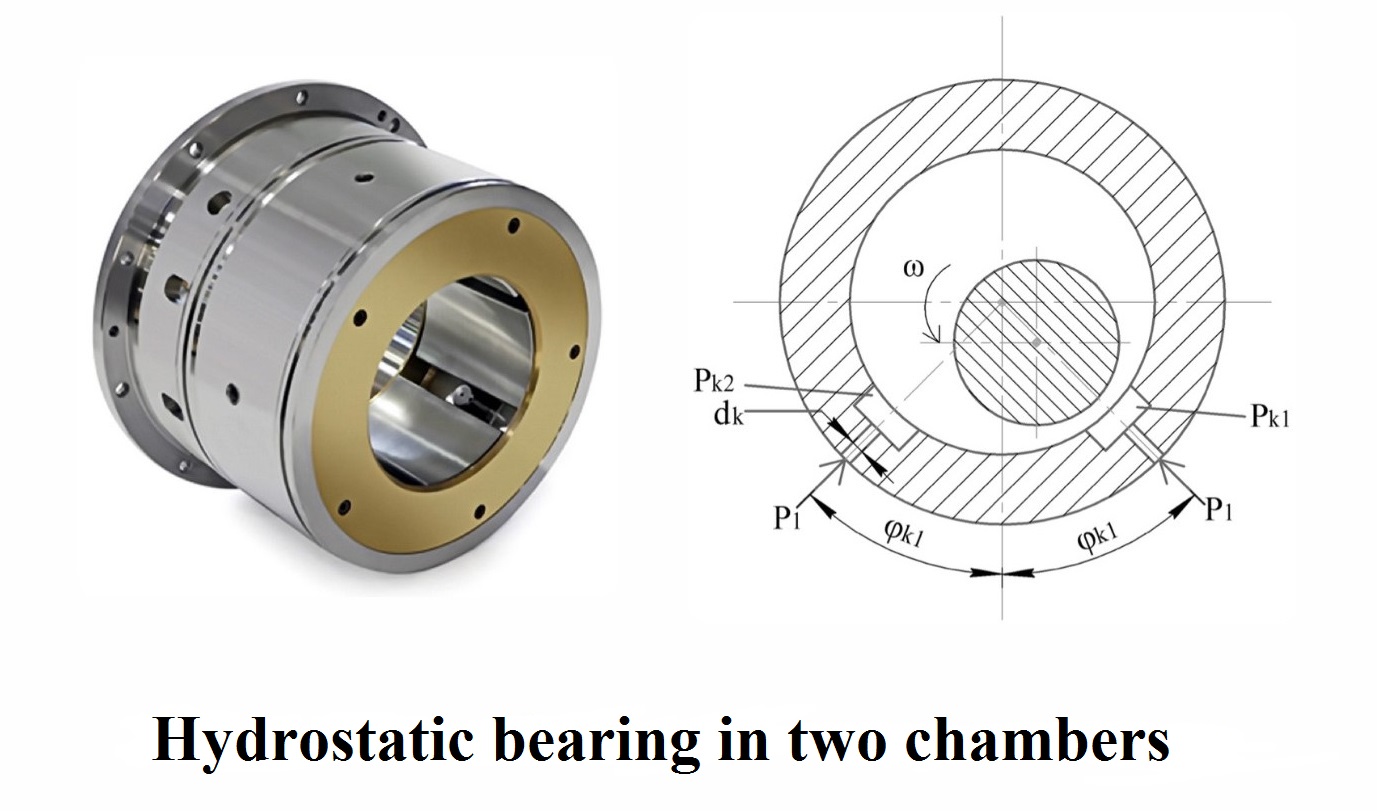
Downloads
Published
How to Cite
Issue
Section
License
Copyright (c) 2023 Vladimir Nazin

This work is licensed under a Creative Commons Attribution 4.0 International License.
The consolidation and conditions for the transfer of copyright (identification of authorship) is carried out in the License Agreement. In particular, the authors reserve the right to the authorship of their manuscript and transfer the first publication of this work to the journal under the terms of the Creative Commons CC BY license. At the same time, they have the right to conclude on their own additional agreements concerning the non-exclusive distribution of the work in the form in which it was published by this journal, but provided that the link to the first publication of the article in this journal is preserved.
A license agreement is a document in which the author warrants that he/she owns all copyright for the work (manuscript, article, etc.).
The authors, signing the License Agreement with TECHNOLOGY CENTER PC, have all rights to the further use of their work, provided that they link to our edition in which the work was published.
According to the terms of the License Agreement, the Publisher TECHNOLOGY CENTER PC does not take away your copyrights and receives permission from the authors to use and dissemination of the publication through the world's scientific resources (own electronic resources, scientometric databases, repositories, libraries, etc.).
In the absence of a signed License Agreement or in the absence of this agreement of identifiers allowing to identify the identity of the author, the editors have no right to work with the manuscript.
It is important to remember that there is another type of agreement between authors and publishers – when copyright is transferred from the authors to the publisher. In this case, the authors lose ownership of their work and may not use it in any way.