Determining the pattern of loose material movement in screw and tubular-comb feeders
DOI:
https://doi.org/10.15587/1729-4061.2023.291680Keywords:
loose material, tubular-comb feeder, discrete element method, DEM, pulsations of loose materialAbstract
The object of this study is the relationship between the structural and technological parameters of feeders for loose materials and the characteristics of particle flows at their outlet, namely: productivity and the magnitude of pulsations. The existing designs of this type of equipment were analyzed, and the most common methods for simulating their operation were determined. A structure of a tubular-comb feeder has been proposed, the performance of which is compared with the well-known screw feeder. Computer models of both structures were built based on the discrete element method. The simulation was carried out in the EDEM 2017 software environment. It was established that the resulting models take into account the discrete nature of the movement of loose materials and allow conducting research taking into account the physical and mechanical properties of individual particles.
An experimental bench was fabricated for experimental verification of the modes of operation of the tubular-comb feeder. The performance of this type of feeder was determined for two pipe rotation speeds (6 and 10 rad/s). The amount of material flow pulsations in the outlet nozzle was also determined. The correspondence of the results of calculations based on the computer model to the real process was confirmed. The current study was carried out the steady modes of operation.
It was established that with equal overall dimensions and speeds of rotation of the working bodies, the productivity of the screw feeder is 5...5.2 times greater than that of the tubular-comb feeder. But the latter provides 7.3...16.4 times smaller magnitude of pulsations of the flow of loose material. This makes it possible to reduce the heterogeneity of mixtures, especially in the case of using such feeders as part of continuous mixing systems.
The results make it possible to analyze the operation of bulk material feeders and reduce their design time
References
- Burmistenkov, O. P. et al. (2007). Vyrobnytstvo lytykh detalei ta vyrobiv z polimernykh materialiv u vzuttieviy ta shkirhalantereinii promyslovosti. Khmelnytskyi: [b.v.], 255.
- Beloshenko, V., Voznyak, Y., Voznyak, A., Savchenko, B. (2017). New approach to production of fiber reinforced polymer hybrid composites. Composites Part B: Engineering, 112, 22–30. doi: https://doi.org/10.1016/j.compositesb.2016.12.030
- Kulik, T., Synyuk, O., Zlotenko, B. (2017). Modeling a process of filling the mold during injection molding of polymeric parts. Eastern-European Journal of Enterprise Technologies, 5 (1 (89)), 70–77. doi: https://doi.org/10.15587/1729-4061.2017.110820
- Statsenko, V., Burmistenkov, O., Bila, T., Statsenko, D. (2019). Determining the motion character of loose materials in the system of continuous action «hopper – reciprocating plate feeder». Eastern-European Journal of Enterprise Technologies, 2 (1 (98)), 21–28. doi: https://doi.org/10.15587/1729-4061.2019.163545
- Zheng, Q. J., Xu, M. H., Chu, K. W., Pan, R. H., Yu, A. B. (2017). A coupled FEM/DEM model for pipe conveyor systems: Analysis of the contact forces on belt. Powder Technology, 314, 480–489. doi: https://doi.org/10.1016/j.powtec.2016.09.070
- Toson, P., Khinast, J. G. (2023). A DEM model to evaluate refill strategies of a twin-screw feeder. International Journal of Pharmaceutics, 641, 122915. doi: https://doi.org/10.1016/j.ijpharm.2023.122915
- Santos, L. S., Macêdo, E. N., Ribeiro Filho, P. R. C. F., Cunha, A. P. A., Cheung, N. (2023). Belt Rotation in Pipe Conveyors: Failure Mode Analysis and Overlap Stability Assessment. Sustainability, 15 (14), 11312. doi: https://doi.org/10.3390/su151411312
- Karwat, B., Machnik, R., Niedźwiedzki, J., Nogaj, M., Rubacha, P., Stańczyk, E. (2019). Calibration of bulk material model in Discrete Element Method on example of perlite D18-DN. Eksploatacja i Niezawodność – Maintenance and Reliability, 21 (2), 351–357. doi: https://doi.org/10.17531/ein.2019.2.20
- Cleary, P. W. (2007). DEM modelling of particulate flow in a screw feeder Model description. Progress in Computational Fluid Dynamics, An International Journal, 7 (2/3/4), 128. doi: https://doi.org/10.1504/pcfd.2007.013005
- Hou, Q. F., Dong, K. J., Yu, A. B. (2014). DEM study of the flow of cohesive particles in a screw feeder. Powder Technology, 256, 529–539. doi: https://doi.org/10.1016/j.powtec.2014.01.062
- Kretz, D., Callau-Monje, S., Hitschler, M., Hien, A., Raedle, M., Hesser, J. (2016). Discrete element method (DEM) simulation and validation of a screw feeder system. Powder Technology, 287, 131–138. doi: https://doi.org/10.1016/j.powtec.2015.09.038
- Owen, P. J., Cleary, P. W. (2009). Prediction of screw conveyor performance using the Discrete Element Method (DEM). Powder Technology, 193 (3), 274–288. doi: https://doi.org/10.1016/j.powtec.2009.03.012
- Shi, Q., Sakai, M. (2022). Recent progress on the discrete element method simulations for powder transport systems: A review. Advanced Powder Technology, 33 (8), 103664. doi: https://doi.org/10.1016/j.apt.2022.103664
- Statsenko, V., Burmistenkov, O., Bila, T., Demishonkova, S. (2021). Determining the loose medium movement parameters in a centrifugal continuous mixer using a discrete element method. Eastern-European Journal of Enterprise Technologies, 3 (7 (111)), 59–67. doi: https://doi.org/10.15587/1729-4061.2021.232636
- Statsenko, V., Burmistenkov, O., Bila, T., Statsenko, D. (2022). Determining the relationship between the simulation duration by the discrete element method and the computer system technical characteristics. Eastern-European Journal of Enterprise Technologies, 6 (4 (120)), 32–39. doi: https://doi.org/10.15587/1729-4061.2022.267033
- Discrete Element Modeling - DEM Software | Altair EDEM. Available at: https://altair.com/edem
- Mindlin, R. D., Deresiewicz, H. (1953). Elastic Spheres in Contact Under Varying Oblique Forces. Journal of Applied Mechanics, 20 (3), 327–344. doi: https://doi.org/10.1115/1.4010702
- Python programming language. Available at: https://www.python.org/
- NumPy. The fundamental package for scientific computing with Python. Available at: https://numpy.org/
- Project Jupyter. Available at: https://jupyter.org/
- Screw feeder – 4 models from D10 to D13. Available at: https://www.palamaticprocess.com/bulk-handling-equipment/screw-feeder
- Screw Feeders. Available at: https://www.screwconveyorbega.com/volumetric-screw-conveyor
- Bunker-zhyvylnyk dlia ekstrudera, hranuliatora. Available at: https://tehnomashstroy.com.ua/ua/p43633546-bunker-pitatel-dlya.html
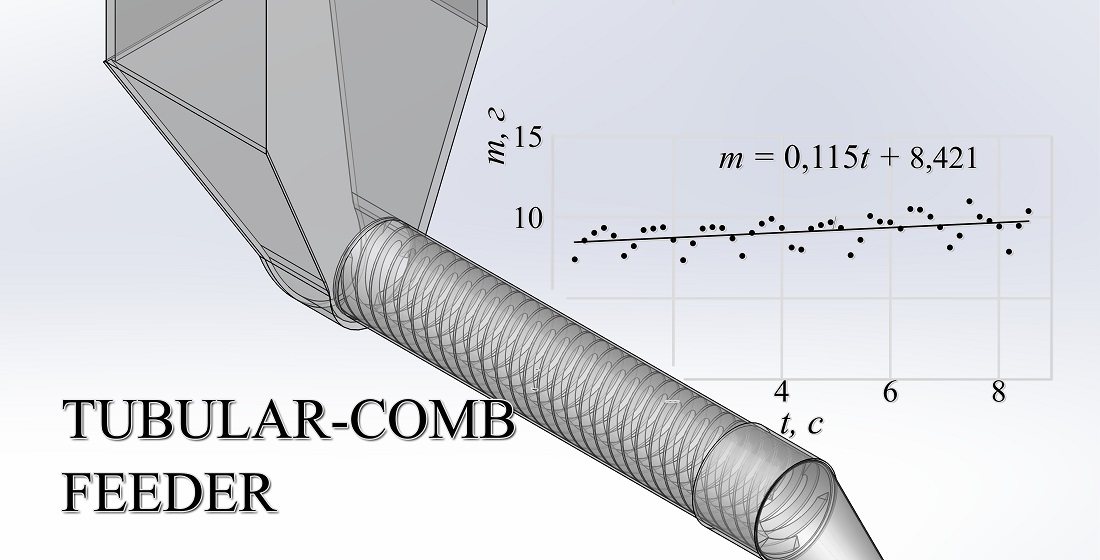
Downloads
Published
How to Cite
Issue
Section
License
Copyright (c) 2023 Volodymyr Nychehlod, Oleksandr Burmistenkov, Volodymyr Statsenko, Tetiana Bila, Dmytro Statsenko

This work is licensed under a Creative Commons Attribution 4.0 International License.
The consolidation and conditions for the transfer of copyright (identification of authorship) is carried out in the License Agreement. In particular, the authors reserve the right to the authorship of their manuscript and transfer the first publication of this work to the journal under the terms of the Creative Commons CC BY license. At the same time, they have the right to conclude on their own additional agreements concerning the non-exclusive distribution of the work in the form in which it was published by this journal, but provided that the link to the first publication of the article in this journal is preserved.
A license agreement is a document in which the author warrants that he/she owns all copyright for the work (manuscript, article, etc.).
The authors, signing the License Agreement with TECHNOLOGY CENTER PC, have all rights to the further use of their work, provided that they link to our edition in which the work was published.
According to the terms of the License Agreement, the Publisher TECHNOLOGY CENTER PC does not take away your copyrights and receives permission from the authors to use and dissemination of the publication through the world's scientific resources (own electronic resources, scientometric databases, repositories, libraries, etc.).
In the absence of a signed License Agreement or in the absence of this agreement of identifiers allowing to identify the identity of the author, the editors have no right to work with the manuscript.
It is important to remember that there is another type of agreement between authors and publishers – when copyright is transferred from the authors to the publisher. In this case, the authors lose ownership of their work and may not use it in any way.