Formation of conjugate curved surfaces that exclude interference
DOI:
https://doi.org/10.15587/1729-4061.2023.292431Keywords:
invariant method, cutting tool, mating surfaces, tooth interference, linear contactAbstract
The object of the study is the method of geometric design of conjugate curved surfaces. The subject of the study is the possibility of achieving the absence of interference of the designed surfaces of kinematic pairs of technical structures, for example, products in mechanical engineering (cutting tools, gearing), based on an invariant method. This problem is of significant importance for a wide class of products, but especially for gears from the point of view of the precision of manufacturing the tooth surface, load-bearing capacity, and, consequently, the reliability and durability of the transmission. When calculating the strength, each tooth of the gear can be considered as a cantilever beam, loaded at the free end by the force of interaction with the second gear wheel. In the presence of interference (for trimming gears), not only the shape of the tooth surface is disrupted, but also the cross-sectional area of the tooth base is significantly reduced. Therefore, solving such a problem is important when designing and manufacturing gears. That is why, when forming the initial curved tool surface of a cutting tool, the conjugacy condition between the points of the product and the tool is taken into account.
As a result, when designing a cutting tool using the proposed invariant method using a unified methodology, a wide class of complex curved surfaces can be formed. In particular, this applies to technological operations on numerically controlled machines. The generated conjugate curvilinear transformations of the cutting tool using an invariant method make it possible to avoid interference of mating surfaces at the design stage. At the same time, the curvilinear characteristics of surfaces are analyzed, defining a family of normals as common to two conjugate surfaces with linear contact, which is essential for the design process
References
- Podkorytov, A. M. (2000). Iteratsiynyi metod ta alhorytm vykliuchennia interferentsiyi skladnykh spriazhenykh poverkhon za napered zadanymy umovamy. Prykladna heometriya ta inzhenerna hrafika. Mizhvidomcha naukovo-tekhnichna zbirka, 64, 109–113.
- Havrylenko, Y., Kholodniak, Y., Vershkov, O., Naidysh, A. (2018). Development of the method for the formation of one-dimensional contours by the assigned interpolation accuracy. Eastern-European Journal of Enterprise Technologies, 1 (4 (91)), 76–82. doi: https://doi.org/10.15587/1729-4061.2018.123921
- Jacob, D. V., Ramana, K. V., Rao, P. V. M. (2004). Automated manufacturability assessment of rotational parts by grinding. International Journal of Production Research, 42 (3), 505–519. doi: https://doi.org/10.1080/00207540310001613674
- Abdel-Baky, R. A., Al-Ghefari, R. A. (2012). On the kinematic geometry of relative screw motions. Journal of Mechanical Science and Technology, 26 (8), 2497–2503. doi: https://doi.org/10.1007/s12206-012-0624-z
- Saghafi, A., Farshidianfar, A. (2016). An analytical study of controlling chaotic dynamics in a spur gear system. Mechanism and Machine Theory, 96, 179–191. doi: https://doi.org/10.1016/j.mechmachtheory.2015.10.002
- Farshidianfar, A., Saghafi, A. (2014). Identification and control of chaos in nonlinear gear dynamic systems using Melnikov analysis. Physics Letters A, 378 (46), 3457–3463. doi: https://doi.org/10.1016/j.physleta.2014.09.060
- Zheng, F., Hua, L., Han, X., Li, B., Chen, D. (2016). Linkage model and manufacturing process of shaping non-circular gears. Mechanism and Machine Theory, 96, 192–212. doi: https://doi.org/10.1016/j.mechmachtheory.2015.09.010
- Liu, X., Yang, Y., Zhang, J. (2016). Investigation on coupling effects between surface wear and dynamics in a spur gear system. Tribology International, 101, 383–394. doi: https://doi.org/10.1016/j.triboint.2016.05.006
- Ismailova, N., Bogach, V., Lebedev, B. (2020). Development of a technique for the geometrical modeling of conjugated surfaces when determining the geometrical parameters of an engagement surface contact in kinematic pairs. Eastern-European Journal of Enterprise Technologies, 4 (1 (106)), 17–22. doi: https://doi.org/10.15587/1729-4061.2020.209108
- Ismailova, N., Bogach, V., Lebedev, B., Oliinyk, N., Manakov, S. (2021). Modeling mated surfaces with the required parameters. Eastern-European Journal of Enterprise Technologies, 2 (1 (110)), 21–26. doi: https://doi.org/10.15587/1729-4061.2021.227691
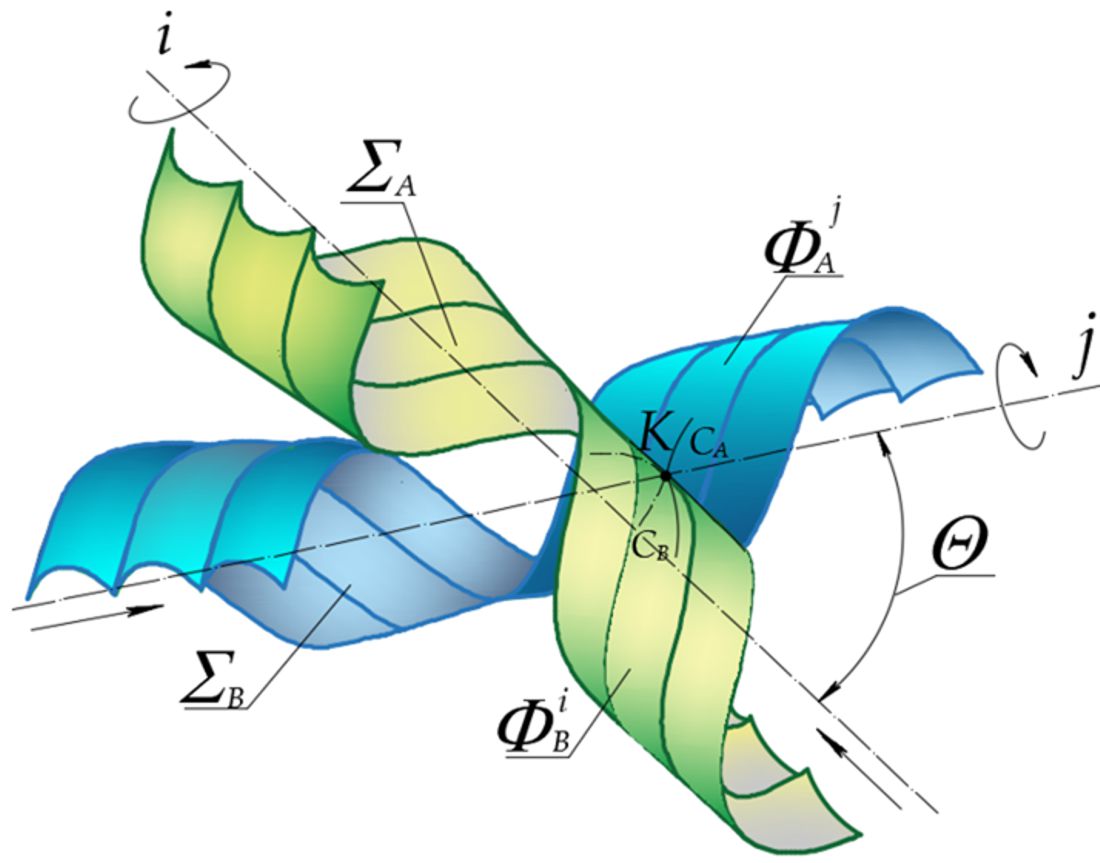
Downloads
Published
How to Cite
Issue
Section
License
Copyright (c) 2023 Nelli Ismailova, Tatiana Mohylianets

This work is licensed under a Creative Commons Attribution 4.0 International License.
The consolidation and conditions for the transfer of copyright (identification of authorship) is carried out in the License Agreement. In particular, the authors reserve the right to the authorship of their manuscript and transfer the first publication of this work to the journal under the terms of the Creative Commons CC BY license. At the same time, they have the right to conclude on their own additional agreements concerning the non-exclusive distribution of the work in the form in which it was published by this journal, but provided that the link to the first publication of the article in this journal is preserved.
A license agreement is a document in which the author warrants that he/she owns all copyright for the work (manuscript, article, etc.).
The authors, signing the License Agreement with TECHNOLOGY CENTER PC, have all rights to the further use of their work, provided that they link to our edition in which the work was published.
According to the terms of the License Agreement, the Publisher TECHNOLOGY CENTER PC does not take away your copyrights and receives permission from the authors to use and dissemination of the publication through the world's scientific resources (own electronic resources, scientometric databases, repositories, libraries, etc.).
In the absence of a signed License Agreement or in the absence of this agreement of identifiers allowing to identify the identity of the author, the editors have no right to work with the manuscript.
It is important to remember that there is another type of agreement between authors and publishers – when copyright is transferred from the authors to the publisher. In this case, the authors lose ownership of their work and may not use it in any way.