Uplifting the study of the inline inspection technique on the buckling pipelines in pipeline integrity management strategy
DOI:
https://doi.org/10.15587/1729-4061.2024.301542Keywords:
pipeline integrity management, inline inspection, internal and external corrosion, pull-through test, collapsibility test, asset integrity, pipeline dentAbstract
This work reports the development of inline inspection (ILI) methodology to enhance the pigging activity for the dented pipeline, facilitate the pigging process to prevent Pipeline Inspection Gauge (PIG) from getting stuck and improve the safety passage for buckled pipelines. The recent report unveils the condition of the UNPIGGABLE pipelines, which reduce the inner diameter of pipelines to 257.51 mm, equivalent to 27.58 % of the initial diameter and restricts the pigging activity. In this report, the pull-through test coupled with the collapsibility test was conducted. The success of the test above allows the ILI equipment based on the magnetic flux leakage (MFL) technique to record the internal and external wall loss inwardly and geometric defect on diameter of the pipelines. The prepared artificial dented pipeline was made before it underwent several tests. Based on the pull-through test, the maximum force of 27000 N is more significant than the pipeline operating pressure to enable the MFL tool to pass through the pipelines despite exhibiting the geometry anomaly. Compressing the opposite magnetic yoke of the collapsibility test is critical, showing that the ILI MFL tool reaches its maximum compression of 242 mm. The value is lower than the minimum internal diameter of 257 mm. The ILI results show that the highest metal loss was achieved at 73 % at 15504 m at the bottom of the inspected pipelines. At the same time, the dented area reduces to more than 6 % of the pipelines’ nominal outer diameter and imposes the pipe’s integrity status to red. The distinctive result of the research can be used to model the future unprecedented pigging process when buckles appear in pipelines
References
- Khan, F. I., Haddara, M. M., Bhattacharya, S. K. (2005). Risk‐Based Integrity and Inspection Modeling (RBIIM) of Process Components/System. Risk Analysis, 26 (1), 203–221. https://doi.org/10.1111/j.1539-6924.2006.00705.x
- Ismail, W. M. M. W., Napiah, M. N. M. A., Zabidi, M. Z. M., Tuselim, A. S. M. (2020). Managing Risk: Effective Use of Structural Reliability Assessment (SRA) and Quantitative Risk Assessment (QRA) for Sabah-Sarawak Gas Pipeline (SSGP). Pipeline Integrity Management Under Geohazard Conditions (PIMG), 387–394. https://doi.org/10.1115/1.861998_ch41
- Aditiyawarman, T., Kaban, A. P. S., Soedarsono, J. W. (2022). A Recent Review of Risk-Based Inspection Development to Support Service Excellence in the Oil and Gas Industry: An Artificial Intelligence Perspective. ASCE-ASME Journal of Risk and Uncertainty in Engineering Systems, Part B: Mechanical Engineering, 9 (1). https://doi.org/10.1115/1.4054558
- Aditiyawarman, T., Soedarsono, J. W., Kaban, A. P. S., Riastuti, R., Rahmadani, H. (2022). The Study of Artificial Intelligent in Risk-Based Inspection Assessment and Screening: A Study Case of Inline Inspection. ASCE-ASME Journal of Risk and Uncertainty in Engineering Systems, Part B: Mechanical Engineering, 9 (1). https://doi.org/10.1115/1.4054969
- Zhao, H. S., Lie, S. T., Zhang, Y. (2017). Elastic-plastic fracture analyses for misaligned clad pipeline containing a canoe shape surface crack subjected to large plastic deformation. Ocean Engineering, 146, 87–100. https://doi.org/10.1016/j.oceaneng.2017.09.058
- Yuan, L., Zhou, J., Yu, Z., Xu, W. (2023). Numerical investigation of buckling behavior of dented lined pipe under bending. International Journal of Pressure Vessels and Piping, 205, 104997. https://doi.org/10.1016/j.ijpvp.2023.104997
- Du, F., Li, C., Wang, W. (2023). Development of Subsea Pipeline Buckling, Corrosion and Leakage Monitoring. Journal of Marine Science and Engineering, 11 (1), 188. https://doi.org/10.3390/jmse11010188
- L. G. Brazier (1927). On the flexure of thin cylindrical shells and other "thin" sections. Proceedings of the Royal Society of London. Series A, Containing Papers of a Mathematical and Physical Character. https://doi.org/10.1098/rspa.1927.0125
- Ju, G. T., Kyriakides, S. (1992). Bifurcation and localization instabilities in cylindrical shells under bending – II. Predictions. International Journal of Solids and Structures, 29 (9), 1143–1171. https://doi.org/10.1016/0020-7683(92)90140-o
- Iflefel, I. B., Moffat, D. G., Mistry, J. (2005). The interaction of pressure and bending on a dented pipe. International Journal of Pressure Vessels and Piping, 82 (10), 761–769. https://doi.org/10.1016/j.ijpvp.2005.06.002
- DNVGL-ST-F101 Submarine pipeline systems. Dnvgl-St-F101 (2017).
- The American Petroleum Institute. API RP 1111 4th edition-design, construction, operation, and maintenance of offshore hydrocarbon pipelines (2009)
- Obeid, O., Alfano, G., Bahai, H., Jouhara, H. (2018). Mechanical response of a lined pipe under dynamic impact. Engineering Failure Analysis, 88, 35–53. https://doi.org/10.1016/j.engfailanal.2018.02.013
- Zhu, X.-K. (2023). A verification study of fatigue-based methods in API RP 1183 for estimating fatigue life of pipeline dents. International Journal of Pressure Vessels and Piping, 205, 104969. https://doi.org/10.1016/j.ijpvp.2023.104969
- Chen, B.-Q., Zhang, X., Guedes Soares, C. (2022). The effect of general and localized corrosions on the collapse pressure of subsea pipelines. Ocean Engineering, 247, 110719. https://doi.org/10.1016/j.oceaneng.2022.110719
- Kaban, A. P. S., Ridhova, A., Priyotomo, G., Elya, B., Maksum, A., Sadeli, Y. et al. (2021). Development of white tea extract as green corrosion inhibitor in mild steel under 1 M hydrochloric acid solution. Eastern-European Journal of Enterprise Technologies, 2 (6 (110)), 6–20. https://doi.org/10.15587/1729-4061.2021.224435
- Beltrán-Zúñiga, M. A., Rivas-López, D. I., Dorantes-Rosales, H. J., González-Zapatero, W., Ferreira-Palma, C., López-Hirata, V. M., Hernández-Santiago, F. (2023). Fatigue life assessment of low carbon API 5L X52 pipeline steels retired from long-term service. Engineering Failure Analysis, 143, 106769. https://doi.org/10.1016/j.engfailanal.2022.106769
- Zhang, L., Hu, Z., Li, H., She, H., Wang, X. (2023). Impact of water delivery pipeline leakage on collapsible loess foundations and treatment methods. Case Studies in Construction Materials, 19, e02341. https://doi.org/10.1016/j.cscm.2023.e02341
- Jiang, M., Liu, J., Li, T., Lei, H., Wu, X., Cao, P. (2020). DEM analyses of constant stress ratio compression and collapsibility tests on unsaturated structural loess. Japanese Geotechnical Society Special Publication, 8 (6), 227–230. https://doi.org/10.3208/jgssp.v08.c42
- Olugboji, O. A., Abolarin, M. S., Adedipe, O., Ajani, C., Atolagbe, G., Aba, E. N. (2022). Pipeline inspection using a low-cost Wi-Fi based intelligent pigging solution. Nigerian Journal of Technology, 41 (5), 844–853. https://doi.org/10.4314/njt.v41i5.4
- Hendrix, M. H. W., Graafland, C. M., van Ostayen, R. A. J. (2018). Frictional forces for disc-type pigging of pipelines. Journal of Petroleum Science and Engineering, 171, 905–918. https://doi.org/10.1016/j.petrol.2018.07.076
- Garbatov, Y., Guedes Soares, C. (2017). Fatigue reliability of dented pipeline based on limited experimental data. International Journal of Pressure Vessels and Piping, 155, 15–26. https://doi.org/10.1016/j.ijpvp.2017.07.001
- Mueller, E., Liu, X., Chhatre, R., Lamm, A. (2017). Investigation and Recommendations on Bottom-Dented Petroleum Pipelines. Journal of Failure Analysis and Prevention, 18 (1), 66–74. https://doi.org/10.1007/s11668-017-0381-5
- Zhang, H., Gao, M.-Q., Tang, B., Cui, C., Xu, X.-F. (2022). Dynamic characteristics of the pipeline inspection gauge under girth weld excitation in submarine pipeline. Petroleum Science, 19 (2), 774–788. https://doi.org/10.1016/j.petsci.2021.09.044
- Chen, Z., Qiu, X., Yang, L. (2022). Deformation and stress analysis of cup on pipeline inspection gauge based on reverse measurement. Energy Science & Engineering, 10 (7), 2509–2526. https://doi.org/10.1002/ese3.1241
- Solomon, E., Massie-Schuh, E., Moore, M., Moran, R., Paschoalino, M., Moore, J., Wunch, K. (2020). Development of a Rapid Method for Measuring Preservative Biocide Performance in Hydraulic Fracturing. SPE Annual Technical Conference and Exhibition. https://doi.org/10.2118/201523-ms
- Pereira, J. C., Borovkov, H., Zubiri, F., Guerra, M. C., Caminos, J. (2021). Optimization of Thin Walls with Sharp Corners in SS316L and IN718 Alloys Manufactured with Laser Metal Deposition. Journal of Manufacturing and Materials Processing, 5 (1), 5. https://doi.org/10.3390/jmmp5010005
- Daniyan, I., Balogun, V., Oladapo, B., Ererughurie, O. K., Daniyan, O. L. (2021). Development of an Inline Pipe Inspection Robot for the Oil and Gas Industry. International Journal of Automation and Smart Technology, 12 (1), 2251–2251. https://doi.org/10.5875/ausmt.v12i1.2251
- Aslanov, H., Novruzov, A., Harun, A. (2019). Managing Wax-Deposition Risks in Oil Subsea Pipelines by Integrating Wax Modeling and Pigging Performance. SPE Production & Operations, 34 (03), 625–634. https://doi.org/10.2118/194506-pa
- Okoloekwe, C., Fowler, M., Virk, A., Yoosef-Ghodsi, N., Kainat, M. (2020). Reliability-Based Assessment of Safe Excavation Pressure for Dented Pipelines. Volume 1: Pipeline and Facilities Integrity. https://doi.org/10.1115/ipc2020-9399
- Cui, L., Kang, W., You, H., Cheng, J., Li, Z. (2020). Experimental Study on Corrosion of J55 Casing Steel and N80 Tubing Steel in High Pressure and High Temperature Solution Containing CO2 and NaCl. Journal of Bio- and Tribo-Corrosion, 7 (1). https://doi.org/10.1007/s40735-020-00449-5
- Wadeson, D. A., Zhou, X., Thompson, G. E., Skeldon, P., Oosterkamp, L. D., Scamans, G. (2006). Corrosion behaviour of friction stir welded AA7108 T79 aluminium alloy. Corrosion Science, 48 (4), 887–897. https://doi.org/10.1016/j.corsci.2005.02.020
- Gu, J., Zhang, H., Chen, L., Lian, S. (2019). The Application of the Big Data Algorithm for Pipeline Lifetime Analysis. 2019 Chinese Automation Congress (CAC). https://doi.org/10.1109/cac48633.2019.8996228
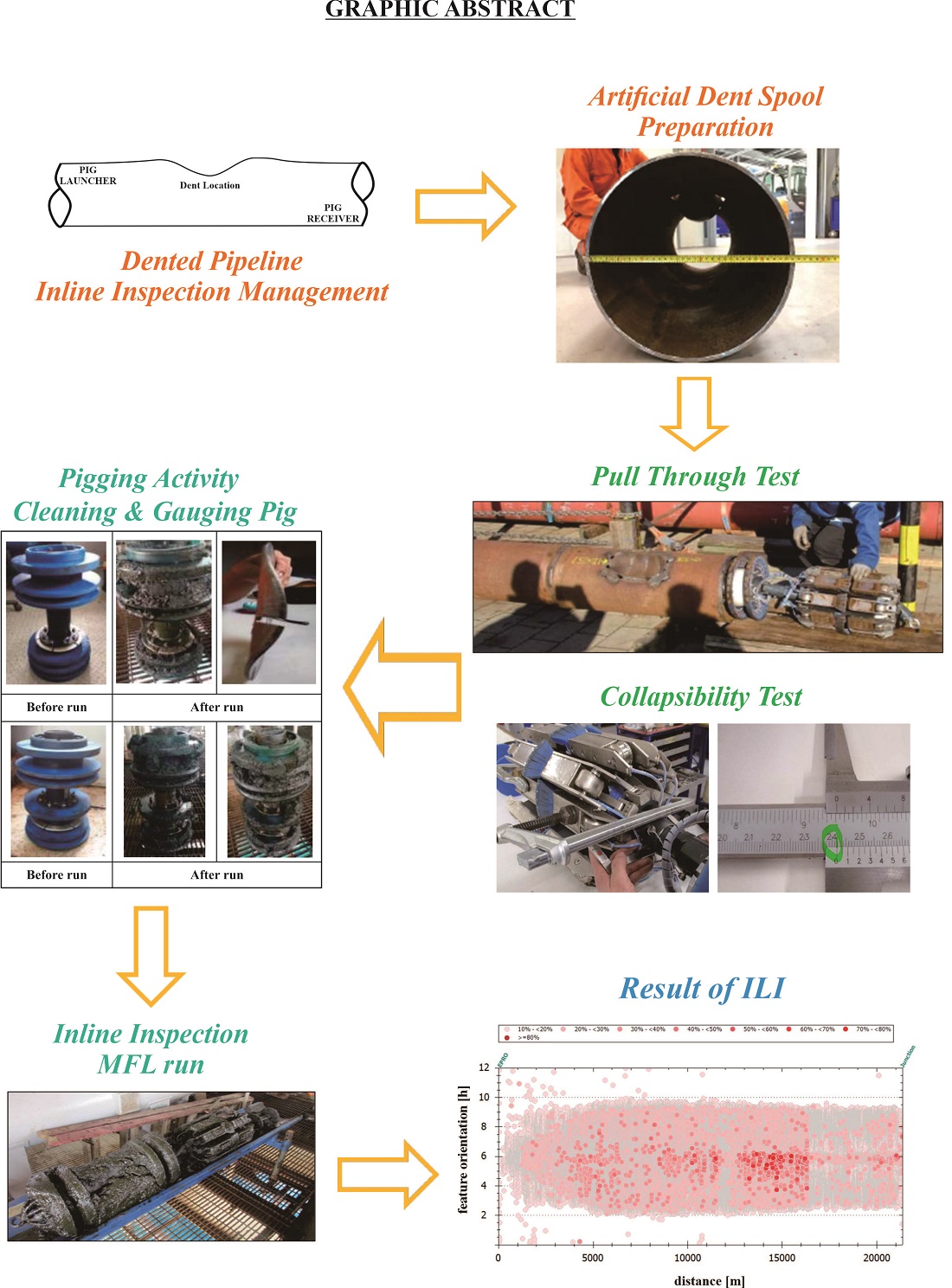
Downloads
Published
How to Cite
Issue
Section
License
Copyright (c) 2024 Dony Soelistiyono, Johny Wahyuadi Soedarsono, Badrul Munir, Michael Oktavianes, Agus Paul Setiawan Kaban, Sidhi Aribowo, Dedy Iskandar

This work is licensed under a Creative Commons Attribution 4.0 International License.
The consolidation and conditions for the transfer of copyright (identification of authorship) is carried out in the License Agreement. In particular, the authors reserve the right to the authorship of their manuscript and transfer the first publication of this work to the journal under the terms of the Creative Commons CC BY license. At the same time, they have the right to conclude on their own additional agreements concerning the non-exclusive distribution of the work in the form in which it was published by this journal, but provided that the link to the first publication of the article in this journal is preserved.
A license agreement is a document in which the author warrants that he/she owns all copyright for the work (manuscript, article, etc.).
The authors, signing the License Agreement with TECHNOLOGY CENTER PC, have all rights to the further use of their work, provided that they link to our edition in which the work was published.
According to the terms of the License Agreement, the Publisher TECHNOLOGY CENTER PC does not take away your copyrights and receives permission from the authors to use and dissemination of the publication through the world's scientific resources (own electronic resources, scientometric databases, repositories, libraries, etc.).
In the absence of a signed License Agreement or in the absence of this agreement of identifiers allowing to identify the identity of the author, the editors have no right to work with the manuscript.
It is important to remember that there is another type of agreement between authors and publishers – when copyright is transferred from the authors to the publisher. In this case, the authors lose ownership of their work and may not use it in any way.