Building a model of the abrasion grinding mechanism in a tumbling mill based on data visualization
DOI:
https://doi.org/10.15587/1729-4061.2024.301653Keywords:
tumbling mill, intra-chamber loading, grinding by abrasion, granular temperature, grinding performanceAbstract
The object of this study is the grinding process in a tumbling mill when the mechanism of destruction by abrasion is implemented, which is caused by the mechanism of shear loading. The abrasive effect due to the impulse interaction during the mutual chaotic movement of granular particles in the shear layer of loading, characterized by the granular temperature, is taken into account.
The task solved was determining the parameters of the shear interaction, which is caused by the difficulties of modeling and complexity of the hardware analysis of behavior of the internal loading in the mill.
A mathematical model was built based on data visualization for the abrasion grinding mechanism.
The power of the shear interaction forces was taken as an analog of the grinding performance. The initial shear characteristic was considered to be the average value of the shear velocity gradient in the central averaged normal section of the shear layer. The impact on productivity of the granular temperature and mass fraction of the shear layer and loading turnover was taken into account.
The effect of rotation speed on performance was evaluated by experimental modeling at a chamber filling degree of 0.45 and a relative particle size of 0.0104. The maximum value of the energy and productivity of grinding by abrasion was established at the relative speed of rotation ψω=0.55–0.6.
The results have made it possible to establish a rational speed when grinding by abrasion, ψω=0.5–0.6. This value is smaller in comparison with grinding by crushing ψω=0.55–0.65 and breaking ψω=0.75–0.9. The established effect is explained by the detected activation of the chaotic quasi-thermodynamic movement of particles of the shear layer at slow rotation.
The model built makes it possible to predict rational technological parameters of the energy-saving process of fine grinding in a tumbling mill by abrasion
References
- Gupta, V. K. (2020). Energy absorption and specific breakage rate of particles under different operating conditions in dry ball milling. Powder Technology, 361, 827–835. https://doi.org/10.1016/j.powtec.2019.11.033
- Góralczyk, M., Krot, P., Zimroz, R., Ogonowski, S. (2020). Increasing Energy Efficiency and Productivity of the Comminution Process in Tumbling Mills by Indirect Measurements of Internal Dynamics – An Overview. Energies, 13 (24), 6735. https://doi.org/10.3390/en13246735
- Tavares, L. M. (2017). A Review of Advanced Ball Mill Modelling. KONA Powder and Particle Journal, 34, 106–124. https://doi.org/10.14356/kona.2017015
- Semsari Parapari, P., Parian, M., Rosenkranz, J. (2020). Breakage process of mineral processing comminution machines – An approach to liberation. Advanced Powder Technology, 31 (9), 3669–3685. https://doi.org/10.1016/j.apt.2020.08.005
- Napier-Munn, T. J., Morrell, S., Morrison, R. D., Kojovic, T. (1996). Mineral comminution circuits: their operation and optimisation. JKMRC Monograph series in mining and mineral processing, 2.
- Ye, X., Gredelj, S., Skinner, W., Grano, S. R. (2010). Regrinding sulphide minerals — Breakage mechanisms in milling and their influence on surface properties and flotation behaviour. Powder Technology, 203 (2), 133–147. https://doi.org/10.1016/j.powtec.2010.05.002
- Hasan, M., Palaniandy, S., Hilden, M., Powell, M. (2017). Calculating breakage parameters of a batch vertical stirred mill. Minerals Engineering, 111, 229–237. https://doi.org/10.1016/j.mineng.2017.06.024
- Chen, X., Peng, Y., Bradshaw, D. (2014). The effect of particle breakage mechanisms during regrinding on the subsequent cleaner flotation. Minerals Engineering, 66-68, 157–164. https://doi.org/10.1016/j.mineng.2014.04.020
- Wills, B. A., Finch, J. (2015). Wills’ Mineral Processing Technology. Butterworth-Heinemann. https://doi.org/10.1016/c2010-0-65478-2
- Naumenko, Y., Deineka, K. (2023). Building a model of the compression grinding mechanism in a tumbling mill based on data visualization. Eastern-European Journal of Enterprise Technologies, 5 (1 (125)), 64–72. https://doi.org/10.15587/1729-4061.2023.287565
- Naumenko, Y., Deineka, K. (2023). Building a model of the impact grinding mechanism in a tumbling mill based on data visualization. Eastern-European Journal of Enterprise Technologies, 3 (7 (123)), 65–73. https://doi.org/10.15587/1729-4061.2023.283073
- Morrison, A. J., Govender, I., Mainza, A. N., Parker, D. J. (2016). The shape and behaviour of a granular bed in a rotating drum using Eulerian flow fields obtained from PEPT. Chemical Engineering Science, 152, 186–198. https://doi.org/10.1016/j.ces.2016.06.022
- de Klerk, D. N., Govender, I., Mainza, A. N. (2019). Geometric features of tumbling mill flows: A positron emission particle tracking investigation. Chemical Engineering Science, 206, 41–49. https://doi.org/10.1016/j.ces.2019.05.020
- Jaeger, H. M., Nagel, S. R., Behringer, R. P. (1996). Granular solids, liquids, and gases. Reviews of Modern Physics, 68 (4), 1259–1273. https://doi.org/10.1103/revmodphys.68.1259
- Forterre, Y., Pouliquen, O. (2008). Flows of Dense Granular Media. Annual Review of Fluid Mechanics, 40 (1), 1–24. https://doi.org/10.1146/annurev.fluid.40.111406.102142
- Forterre, Y., Pouliquen, O. (2011). Granular Flows. Glasses and Grains, 77–109. https://doi.org/10.1007/978-3-0348-0084-6_4
- Brown, R. L., Richards, J. C. (2016). Principles of powder mechanics: essays on the packing and flow of powders and bulk solids. Elsevier. https://doi.org/10.1016/c2013-0-01576-9
- Savage, S. B. (1984). The Mechanics of Rapid Granular Flows. Advances in Applied Mechanics, 289–366. https://doi.org/10.1016/s0065-2156(08)70047-4
- Campbell, C. (1990). Rapid Granular Flows. Annual Review of Fluid Mechanics, 22 (1), 57–92. https://doi.org/10.1146/annurev.fluid.22.1.57
- Campbell, C. S. (2006). Granular material flows – An overview. Powder Technology, 162 (3), 208–229. https://doi.org/10.1016/j.powtec.2005.12.008
- Jiang, Y., Liu, M. (2009). Granular solid hydrodynamics. Granular Matter, 11 (3), 139–156. https://doi.org/10.1007/s10035-009-0137-3
- Ogawa, S. (1978). Multitemperature theory of granular materials. Proc. of the US-Japan Seminar on Continuum Mechanical and Statistical Approaches in the Mechanics of Granular Materials, 208–217.
- Ogawa, S., Umemura, A., Oshima, N. (1980). On the equations of fully fluidized granular materials. Zeitschrift Für Angewandte Mathematik Und Physik ZAMP, 31 (4), 483–493. https://doi.org/10.1007/bf01590859
- Sun, Q., Song, S., Jin, F., Jiang, Y. (2012). Entropy productions in granular materials. Theoretical and Applied Mechanics Letters, 2 (2), 021002. https://doi.org/10.1063/2.1202102
- Sun, Q., Song, S., Liu, J., Fei, M., Jin, F. (2013). Granular materials: Bridging damaged solids and turbulent fluids. Theoretical and Applied Mechanics Letters, 3 (2), 021008. https://doi.org/10.1063/2.1302108
- Sun, Q., Jin, F., Wang, G., Song, S., Zhang, G. (2015). On granular elasticity. Scientific Reports, 5 (1). https://doi.org/10.1038/srep09652
- Yang, H., Li, R., Kong, P., Sun, Q. C., Biggs, M. J., Zivkovic, V. (2015). Avalanche dynamics of granular materials under the slumping regime in a rotating drum as revealed by speckle visibility spectroscopy. Physical Review E, 91 (4). https://doi.org/10.1103/physreve.91.042206
- Li, R., Yang, H., Zheng, G., Zhang, B. F., Fei, M. L., Sun, Q. C. (2016). Double speckle-visibility spectroscopy for the dynamics of a passive layer in a rotating drum. Powder Technology, 295, 167–174. https://doi.org/10.1016/j.powtec.2016.03.031
- Yang, H., Zhang, B. F., Li, R., Zheng, G., Zivkovic, V. (2017). Particle dynamics in avalanche flow of irregular sand particles in the slumping regime of a rotating drum. Powder Technology, 311, 439–448. https://doi.org/10.1016/j.powtec.2017.01.064
- Li, R., Yang, H., Zheng, G., Sun, Q. C. (2018). Granular avalanches in slumping regime in a 2D rotating drum. Powder Technology, 326, 322–326. https://doi.org/10.1016/j.powtec.2017.12.032
- Yang, H., Zhu, Y., Li, R., Sun, Q. (2020). Kinetic granular temperature and its measurement using speckle visibility spectroscopy. Particuology, 48, 160–169. https://doi.org/10.1016/j.partic.2018.07.011
- Jing, Z., Yang, H., Wang, S., Chen, Q., Li, R. (2021). Comparison of granular temperature measured by SVS and DEM in the rotating cylinder. Powder Technology, 380, 282–287. https://doi.org/10.1016/j.powtec.2020.11.073
- Dolgunin, V. N., Ivanov, O. O., Akopyan, S. A. (2020). Quasithermal Effects During Rapid Gravity Flow of a Granular Medium. Advanced Materials & Technologies, 3 (19), 047–055. https://doi.org/10.17277/amt.2020.03.pp.047-055
- Li, S., Yao, Q., Chen, B., Zhang, X., Ding, Y. L. (2007). Molecular dynamics simulation and continuum modelling of granular surface flow in rotating drums. Chinese Science Bulletin, 52 (5), 692–700. https://doi.org/10.1007/s11434-007-0069-4
- Yin, H., Zhang, M., Liu, H. (2014). Numerical simulation of three-dimensional unsteady granular flows in rotary kiln. Powder Technology, 253, 138–145. https://doi.org/10.1016/j.powtec.2013.10.044
- Yang, S., Sun, Y., Zhang, L., Chew, J. W. (2017). Segregation dynamics of a binary-size mixture in a three-dimensional rotating drum. Chemical Engineering Science, 172, 652–666. https://doi.org/10.1016/j.ces.2017.07.019
- Yang, S., Wang, H., Wei, Y., Hu, J., Chew, J. W. (2020). Flow dynamics of binary mixtures of non-spherical particles in the rolling-regime rotating drum. Powder Technology, 361, 930–942. https://doi.org/10.1016/j.powtec.2019.10.110
- Longo, S., Lamberti, A. (2002). Grain shear flow in a rotating drum. Experiments in Fluids, 32 (3), 313–325. https://doi.org/10.1007/s003480100359
- Chou, H.-T., Lee, C.-F. (2008). Cross-sectional and axial flow characteristics of dry granular material in rotating drums. Granular Matter, 11 (1), 13–32. https://doi.org/10.1007/s10035-008-0118-y
- Chou, S. H., Hsiau, S. S. (2011). Experimental analysis of the dynamic properties of wet granular matter in a rotating drum. Powder Technology, 214 (3), 491–499. https://doi.org/10.1016/j.powtec.2011.09.010
- Chou, S. H., Hu, H. J., Hsiau, S. S. (2016). Investigation of friction effect on granular dynamic behavior in a rotating drum. Advanced Powder Technology, 27 (5), 1912–1921. https://doi.org/10.1016/j.apt.2016.06.022
- Liao, C.-C., Lan, H.-W., Hsiau, S.-S. (2016). Density-induced granular segregation in a slurry rotating drum. International Journal of Multiphase Flow, 84, 1–8. https://doi.org/10.1016/j.ijmultiphaseflow.2016.04.015
- Liao, C.-C. (2019). Effect of dynamic properties on density-driven granular segregation in a rotating drum. Powder Technology, 345, 151–158. https://doi.org/10.1016/j.powtec.2018.12.093
- Liao, C.-C., Ou, S.-F., Chen, S.-L., Chen, Y.-R. (2020). Influences of fine powder on dynamic properties and density segregation in a rotating drum. Advanced Powder Technology, 31 (4), 1702–1707. https://doi.org/10.1016/j.apt.2020.02.006
- Chung, Y.-C., Liao, C.-C., Zhuang, Z.-H. (2021). Experimental investigations for the effect of fine powders on size-induced segregation in binary granular mixtures. Powder Technology, 387, 270–276. https://doi.org/10.1016/j.powtec.2021.04.034
- Govender, I., Richter, M. C., Mainza, A. N., De Klerk, D. N. (2016). A positron emission particle tracking investigation of the scaling law governing free surface flows in tumbling mills. AIChE Journal, 63 (3), 903–913. https://doi.org/10.1002/aic.15453
- Xiu, W., Li, R., Chen, Q., Sun, Q., Zivkovic, V., Yang, H. (2023). Prediction of segregation characterization based on granular velocity and concentration in rotating drum. Particuology, 73, 17–25. https://doi.org/10.1016/j.partic.2022.03.008
- Naumenko, Y. (2017). Modeling a flow pattern of the granular fill in the cross section of a rotating chamber. Eastern-European Journal of Enterprise Technologies, 5 (1 (89)), 59–69. https://doi.org/10.15587/1729-4061.2017.110444
- Naumenko, Y. (2017). Modeling of fracture surface of the quasi solid-body zone of motion of the granular fill in a rotating chamber. Eastern-European Journal of Enterprise Technologies, 2 (1 (86)), 50–57. https://doi.org/10.15587/1729-4061.2017.96447
- Naumenko, Y., Sivko, V. (2017). The rotating chamber granular fill shear layer flow simulation. Eastern-European Journal of Enterprise Technologies, 4 (7 (88)), 57–64. https://doi.org/10.15587/1729-4061.2017.107242
- Deineka, K., Naumenko, Y. (2019). Revealing the effect of decreased energy intensity of grinding in a tumbling mill during self-excitation of auto-oscillations of the intrachamber fill. Eastern-European Journal of Enterprise Technologies, 1 (1 (97)), 6–15. https://doi.org/10.15587/1729-4061.2019.155461
- Deineka, K., Naumenko, Y. (2019). Establishing the effect of a decrease in power intensity of self-oscillating grinding in a tumbling mill with a reduction in an intrachamber fill. Eastern-European Journal of Enterprise Technologies, 6 (7 (102)), 43–52. https://doi.org/10.15587/1729-4061.2019.183291
- Deineka, K., Naumenko, Y. (2020). Establishing the effect of decreased power intensity of self-oscillatory grinding in a tumbling mill when the crushed material content in the intra-chamber fill is reduced. Eastern-European Journal of Enterprise Technologies, 4 (1 (106)), 39–48. https://doi.org/10.15587/1729-4061.2020.209050
- Deineka, K., Naumenko, Y. (2021). Establishing the effect of a simultaneous reduction in the filling load inside a chamber and in the content of the crushed material on the energy intensity of self-oscillatory grinding in a tumbling mill. Eastern-European Journal of Enterprise Technologies, 1 (1 (109)), 77–87. https://doi.org/10.15587/1729-4061.2021.224948
- Deineka, K., Naumenko, Y. (2022). Revealing the mechanism of stability loss of a two-fraction granular flow in a rotating drum. Eastern-European Journal of Enterprise Technologies, 4 (1 (118)), 34–46. https://doi.org/10.15587/1729-4061.2022.263097
- Deineka, K. Yu., Naumenko, Yu. V. (2018). The tumbling mill rotation stability. Scientific Bulletin of National Mining University, 1, 60–68. https://doi.org/10.29202/nvngu/2018-1/10
- Gupta, V. K., Sharma, S. (2014). Analysis of ball mill grinding operation using mill power specific kinetic parameters. Advanced Powder Technology, 25 (2), 625–634. https://doi.org/10.1016/j.apt.2013.10.003
- Hanumanthappa, H., Vardhan, H., Mandela, G. R., Kaza, M., Sah, R., Shanmugam, B. K. (2020). A comparative study on a newly designed ball mill and the conventional ball mill performance with respect to the particle size distribution and recirculating load at the discharge end. Minerals Engineering, 145, 106091. https://doi.org/10.1016/j.mineng.2019.106091
- ISO 924:1989. Coal preparation plant. Principles and conventions for flowsheets. Available at: https://www.iso.org/standard/5340.html
- DIN EN 1009-3. Maschinen für die mechanische Aufbereitung von Mineralien und ähnlichen festen Stoffen - Sicherheit - Teil 3: Spezifische Anforderungen für Brecher und Mühlen; Deutsche Fassung EN 1009-3:2020. Available at: https://www.din.de/de/mitwirken/normenausschuesse/nam/veroeffentlichungen/wdc-beuth:din21:316006092
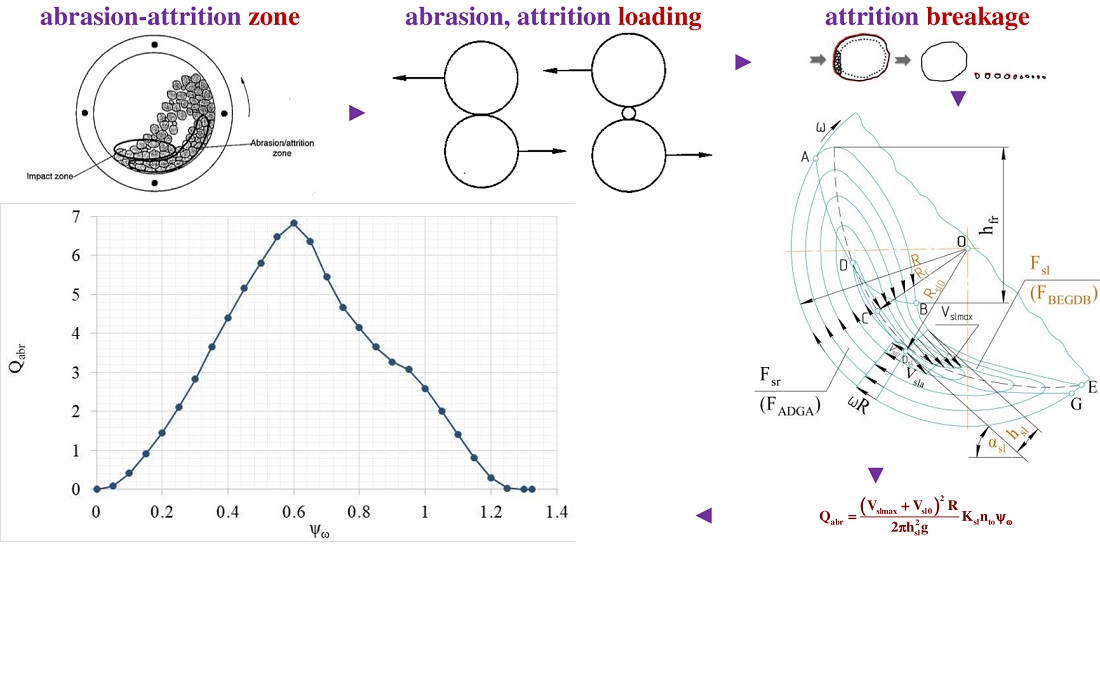
Downloads
Published
How to Cite
Issue
Section
License
Copyright (c) 2024 Yuriy Naumenko, Kateryna Deineka, Serhii Zabchyk

This work is licensed under a Creative Commons Attribution 4.0 International License.
The consolidation and conditions for the transfer of copyright (identification of authorship) is carried out in the License Agreement. In particular, the authors reserve the right to the authorship of their manuscript and transfer the first publication of this work to the journal under the terms of the Creative Commons CC BY license. At the same time, they have the right to conclude on their own additional agreements concerning the non-exclusive distribution of the work in the form in which it was published by this journal, but provided that the link to the first publication of the article in this journal is preserved.
A license agreement is a document in which the author warrants that he/she owns all copyright for the work (manuscript, article, etc.).
The authors, signing the License Agreement with TECHNOLOGY CENTER PC, have all rights to the further use of their work, provided that they link to our edition in which the work was published.
According to the terms of the License Agreement, the Publisher TECHNOLOGY CENTER PC does not take away your copyrights and receives permission from the authors to use and dissemination of the publication through the world's scientific resources (own electronic resources, scientometric databases, repositories, libraries, etc.).
In the absence of a signed License Agreement or in the absence of this agreement of identifiers allowing to identify the identity of the author, the editors have no right to work with the manuscript.
It is important to remember that there is another type of agreement between authors and publishers – when copyright is transferred from the authors to the publisher. In this case, the authors lose ownership of their work and may not use it in any way.