Electrochemical characteristic and microstructure of Ti-6Al-7Nb alloy by centrifugal casting for orthopedic implant based on ageing time variations
DOI:
https://doi.org/10.15587/1729-4061.2024.302614Keywords:
orthopedic implant, titanium alloy, ageing time, microstructure, corrosion resistanceAbstract
The alternative Ti-6Al-7Nb alloy has gained extensive progression due to its ability to eliminate the cytotoxicity of vanadium (V) in Ti-6Al-4V alloy for orthopedic implants. The production of titanium alloys by centrifugal casting shows significant potential to reduce costs. Heat treatment and aging can tailor the microstructure and improve the corrosion resistance of titanium alloys. This study examines the effects of various ageing times on the microstructure and corrosion resistance of a centrifugal cast Ti-6Al-7Nb alloy that has previously been heated and treated at a temperature of 1050 °C, and subsequently cooled to room temperature in argon atmosphere gas. Ageing was carried out at a temperature of 550 °C with variable times of 0, 4, 6, and 8 hours. The surface morphology, metal phase changes, and electrochemical characterization were tested using an optical microscope (OM), X-ray diffraction (XRD), potentiodynamic polarization (PDP), and electrochemical impedance spectroscopy (EIS). The basket-weave microstructure is formed where globularization occurs in some phases as ageing time increases. Increasing the FWHM α value is correlated with increasing the amount of α' martensite phase. As an ageing time enhances, the temperature might offer a greater driving constrain for the nucleation and expansion of the lamellar phase (α). Ageing of 8 hours has the lowest corrosion rate, 0.0023 mpy and highest corrosion resistance, 90457 Ω∙cm2, due to the partially bimodal structure and grain refinement with a smallest grain size of 327.87 µm. Tafel polarization results show that all passivated samples are stable in the Solution Body Fluid (SBF). This work can be used as a starting point for developing microstructural evolution in titanium alloys
References
- Davis, J. R. (1998). Metals Handbook Desk Edition. It was prepared under the direction of the ASM International Handbook Committee.
- Leyens, C., Peters, M. (Eds.) (2003). Titanium and Titanium Alloys. Wiley. https://doi.org/10.1002/3527602119
- Whittaker, M. (2018). Titanium Alloys 2017. Metals, 8 (5), 319. https://doi.org/10.3390/met8050319
- Froes, F. H. (2015). TITANIUM Physical Metallurgy Processing and Applications. ASM. Available at: https://www.asminternational.org/wp-content/uploads/files/39989767/39989767-toc.pdf
- Choubey, A., Balasubramaniam, R., Basu, B. (2004). Effect of replacement of V by Nb and Fe on the electrochemical and corrosion behavior of Ti–6Al–4V in simulated physiological environment. Journal of Alloys and Compounds, 381 (1-2), 288–294. https://doi.org/10.1016/j.jallcom.2004.03.096
- Tamilselvi, S., Raman, V., Rajendran, N. (2006). Corrosion behaviour of Ti–6Al–7Nb and Ti–6Al–4V ELI alloys in the simulated body fluid solution by electrochemical impedance spectroscopy. Electrochimica Acta, 52 (3), 839–846. https://doi.org/10.1016/j.electacta.2006.06.018
- Ndukwe, A. I. (2022). Review of Recent Findings on Investment Casting of Titanium Alloys. Academic Journal of Manufacturing Engineering, 20 (2), 99–108. Available at: https://www.ajme.ro/PDF_AJME_2022_2/L12.pdf
- Su, B., Luo, L., Wang, B., Su, Y., Wang, L., Ritchie, R. O. et al. (2021). Annealed microstructure dependent corrosion behavior of Ti-6Al-3Nb-2Zr-1Mo alloy. Journal of Materials Science & Technology, 62, 234–248. https://doi.org/10.1016/j.jmst.2020.05.058
- Gu, B., Chekhonin, P., Xin, S. W., Liu, G. Q., Ma, C. L., Zhou, L., Skrotzki, W. (2021). Microstructure and texture development during hot-compression of Ti5321. Materials Characterization, 179, 111297. https://doi.org/10.1016/j.matchar.2021.111297
- Hulka, I., Florido-Suarez, N. R., Mirza-Rosca, J. C., Saceleanu, A. (2022). Mechanical Properties and Corrosion Behavior of Thermally Treated Ti-6Al-7Nb Dental Alloy. Materials, 15 (11), 3813. https://doi.org/10.3390/ma15113813
- Lei, L., Zhao, Y., Zhao, Q., Wu, C., Huang, S., Jia, W., Zeng, W. (2021). Impact toughness and deformation modes of Ti–6Al–4V alloy with different microstructures. Materials Science and Engineering: A, 801, 140411. https://doi.org/10.1016/j.msea.2020.140411
- Yao, L., He, Y., Wang, Z., Peng, B., Li, G., Liu, Y. (2021). Effect of Heat Treatment on the Wear Properties of Selective Laser Melted Ti–6Al–4V Alloy Under Different Loads. Acta Metallurgica Sinica (English Letters), 35 (3), 517–525. https://doi.org/10.1007/s40195-021-01280-8
- Tian, Y., Li, S., Hao, Y., Yang, R. (2013). High temperature deformation behavior and microstructure evolution mechanism transformation in Ti2448 alloy. Acta Metallurgica Sinica, 48 (7), 837–844. https://doi.org/10.3724/sp.j.1037.2012.00007
- Wang, G., Zhao, Z., Yu, B., Chen, Z., Wang, Q., Yang, R. (2017). Effect of Heat Treatment Process on Microstructure and Mechanical Properties of Titanium Alloy Ti6246. Chinese Journal of Materials Research, 31 (5), 352–358. https://doi.org/10.11901/1005.3093.2016.621
- Lee, C. S., Kim, M. G., Kim, G.-H., Kim, K.-T., Hwang, D., Kim, H. S. (2019). Corrosion Properties of Ultra-Fine-Grained Cu-3 wt%Ti Alloy Fabricated by Combination of Hot Rolling and Aging Treatment. Journal of Nanoscience and Nanotechnology, 19 (10), 6487–6492. https://doi.org/10.1166/jnn.2019.17071
- Avinash, D., Leo Kumar, S. P. (2021). Investigations on surface-integrity and mechanical properties of biocompatible grade Ti-6Al-7Nb alloy. Materials Technology, 37 (9), 897–905. https://doi.org/10.1080/10667857.2021.1903671
- Gao, K., Zhang, Y., Yi, J., Dong, F., Chen, P. (2024). Overview of Surface Modification Techniques for Titanium Alloys in Modern Material Science: A Comprehensive Analysis. Coatings, 14 (1), 148. https://doi.org/10.3390/coatings14010148
- Yang, X., Dong, X., Li, W., Feng, W., Xu, Y. (2020). Effect of solution and aging treatments on corrosion performance of laser solid formed Ti-6Al-4V alloy in a 3.5 wt. % NaCl solution. Journal of Materials Research and Technology, 9 (2), 1559–1568. https://doi.org/10.1016/j.jmrt.2019.11.082
- Senopati, G., Rahman Rashid, R. A., Kartika, I., Palanisamy, S. (2023). Recent Development of Low-Cost β-Ti Alloys for Biomedical Applications: A Review. Metals, 13 (2), 194. https://doi.org/10.3390/met13020194
- Li, X. X., Zhou, Y., Ji, X. L., Li, Y. X., Wang, S. Q. (2015). Effects of sliding velocity on tribo-oxides and wear behavior of Ti–6Al–4V alloy. Tribology International, 91, 228–234. https://doi.org/10.1016/j.triboint.2015.02.009
- Khun, N. W., Tan, A. W. Y., Bi, K. J. W., Liu, E. (2016). Effects of working gas on wear and corrosion resistances of cold sprayed Ti-6Al-4V coatings. Surface and Coatings Technology, 302, 1–12. https://doi.org/10.1016/j.surfcoat.2016.05.052
- Weng, F., Yu, H., Chen, C., Liu, J., Zhao, L., Dai, J., Zhao, Z. (2017). Effect of process parameters on the microstructure evolution and wear property of the laser cladding coatings on Ti-6Al-4V alloy. Journal of Alloys and Compounds, 692, 989–996. https://doi.org/10.1016/j.jallcom.2016.09.071
- Marenych, O. O., Ding, D., Pan, Z., Kostryzhev, A. G., Li, H., van Duin, S. (2018). Effect of chemical composition on microstructure, strength and wear resistance of wire deposited Ni-Cu alloys. Additive Manufacturing, 24, 30–36. https://doi.org/10.1016/j.addma.2018.08.003
- Sieniawski, J., Ziaja, W., Kubiak, K., Motyk, M. (2013). Microstructure and Mechanical Properties of High Strength Two-Phase Titanium Alloys. Titanium Alloys - Advances in Properties Control. https://doi.org/10.5772/56197
- Guan, S., Solberg, K., Wan, D., Berto, F., Welo, T., Yue, T. M., Chan, K. C. (2019). Formation of fully equiaxed grain microstructure in additively manufactured AlCoCrFeNiTi0.5 high entropy alloy. Materials & Design, 184, 108202. https://doi.org/10.1016/j.matdes.2019.108202
- Yan, C., Hao, L., Hussein, A., Young, P. (2015). Ti–6Al–4V triply periodic minimal surface structures for bone implants fabricated via selective laser melting. Journal of the Mechanical Behavior of Biomedical Materials, 51, 61–73. https://doi.org/10.1016/j.jmbbm.2015.06.024
- Matthew, J., Donachie, M. (2001). Heat treating titanium and its alloys. HEAT TREATIN G PRO G RESS. Available at: https://www.academia.edu/32143147/Titanium_A_Technical_Guide
- Bălţatu, M. S., Vizureanu, P., Bălan, T., Lohan, M., Ţugui, C. A. (2018). Preliminary Tests for Ti-Mo-Zr-Ta Alloys as Potential Biomaterials. IOP Conference Series: Materials Science and Engineering, 374, 012023. https://doi.org/10.1088/1757-899x/374/1/012023
- Semiatin, S. L. (2020). An Overview of the Thermomechanical Processing of α/β Titanium Alloys: Current Status and Future Research Opportunities. Metallurgical and Materials Transactions A, 51 (6), 2593–2625. https://doi.org/10.1007/s11661-020-05625-3
- Zuo, H., Deng, H., Zhou, L., Qiu, W., Xu, P., Wei, Y. et al. (2022). The effect of heat treatment on corrosion behavior of selective laser melted Ti-5Al-5Mo-5V-3Cr-1Zr alloy. Surface and Coatings Technology, 445, 128743. https://doi.org/10.1016/j.surfcoat.2022.128743
- Seo, S., Park, J. (2023). Annealing Heat Treatment for Homogenizing the Microstructure and Mechanical Properties of Electron-Beam-Welded Thick Plate of Ti-6Al-4V Alloy. Materials, 16 (23), 7423. https://doi.org/10.3390/ma16237423
- Winda Sari, M. (2019). Studi pengaruh temperatur solution treatment dan waktu aging terhadap sifat mekanik serta ketahanan korosi pada paduan implan biomedis Ti-6Al-7Nb hasil centrifugal casting. S1 thesis, Universitas Sultan Ageng Tirtayasa. Available at: https://eprints.untirta.ac.id/6046/
- Yang, Z., Li, J., Zhang, B., Li, J. (2022). Microstructures and mechanical properties of a titanium alloy thick plate joint after electron beam welding plus solution-aging. Journal of Materials Research and Technology, 19, 913–922. https://doi.org/10.1016/j.jmrt.2022.05.091
- Muniz, F. T. L., Miranda, M. A. R., Morilla dos Santos, C., Sasaki, J. M. (2016). The Scherrer equation and the dynamical theory of X-ray diffraction. Acta Crystallographica Section A Foundations and Advances, 72 (3), 385–390. https://doi.org/10.1107/s205327331600365x
- Su, B., Wang, B., Luo, L., Wang, L., Liu, C., Su, Y. et al. (2022). Tuning microstructure and improving the corrosion resistance of a Ti-6Al-3Nb-2Zr-1Mo alloy via solution and aging treatments. Corrosion Science, 208, 110694. https://doi.org/10.1016/j.corsci.2022.110694
- Liang, Z., Sun, Z., Zhang, W., Wu, S., Chang, H. (2019). The effect of heat treatment on microstructure evolution and tensile properties of selective laser melted Ti6Al4V alloy. Journal of Alloys and Compounds, 782, 1041–1048. https://doi.org/10.1016/j.jallcom.2018.12.051
- Xu, W., Brandt, M., Sun, S., Elambasseril, J., Liu, Q., Latham, K. et al. (2015). Additive manufacturing of strong and ductile Ti–6Al–4V by selective laser melting via in situ martensite decomposition. Acta Materialia, 85, 74–84. https://doi.org/10.1016/j.actamat.2014.11.028
- Chanfreau, N., Poquillon, D., Stark, A., Maawad, E., Mareau, C., Dehmas, M. (2022). Phase transformation of the Ti-5553 titanium alloy subjected to rapid heating. Journal of Materials Science, 57 (9), 5620–5633. https://doi.org/10.1007/s10853-022-06959-6
- Xu, C., Sikan, F., Atabay, S. E., Muñiz-Lerma, J. A., Sanchez-Mata, O., Wang, X., Brochu, M. (2020). Microstructure and mechanical behavior of as-built and heat-treated Ti–6Al–7Nb produced by laser powder bed fusion. Materials Science and Engineering: A, 793, 139978. https://doi.org/10.1016/j.msea.2020.139978
- Yu, J., Yin, Z., Huang, Z., Zhao, S., Huang, H., Yu, K. et al. (2022). Effect of Aging Treatment on Microstructural Evolution and Mechanical Properties of the Electron Beam Cold Hearth Melting Ti-6Al-4V Alloy. Materials, 15 (20), 7122. https://doi.org/10.3390/ma15207122
- Lei, Z., Chen, Y., Ma, S., Zhou, H., Liu, J., Wang, X. (2020). Influence of aging heat treatment on microstructure and tensile properties of laser oscillating welded TB8 titanium alloy joints. Materials Science and Engineering: A, 797, 140083. https://doi.org/10.1016/j.msea.2020.140083
- Li, C.-L., Hong, J.-K., Narayana, P. L., Choi, S.-W., Lee, S. W., Park, C. H. et al. (2021). Realizing superior ductility of selective laser melted Ti-6Al-4V through a multi-step heat treatment. Materials Science and Engineering: A, 799, 140367. https://doi.org/10.1016/j.msea.2020.140367
- Mahadule, D., Khatirkar, R. K., Gupta, S. K., Gupta, A., Dandekar, T. R. (2022). Microstructure evolution and corrosion behaviour of a high Mo containing α + β titanium alloy for biomedical applications. Journal of Alloys and Compounds, 912, 165240. https://doi.org/10.1016/j.jallcom.2022.165240
- Scully, J., Silverman, D., Kendig, M. (Eds.) (1993). Electrochemical Impedance: Analysis and Interpretation. ASTM International. https://doi.org/10.1520/stp1188-eb
- Stępień, M., Handzlik, P., Fitzner, K. (2016). Electrochemical synthesis of oxide nanotubes on Ti6Al7Nb alloy and their interaction with the simulated body fluid. Journal of Solid State Electrochemistry, 20 (10), 2651–2661. https://doi.org/10.1007/s10008-016-3258-8
- Li, B. Q., Xie, R. Z., Lu, X. (2020). Microstructure, mechanical property and corrosion behavior of porous Ti–Ta–Nb–Zr. Bioactive Materials, 5 (3), 564–568. https://doi.org/10.1016/j.bioactmat.2020.04.014
- Mansfeld, F. (1990). Electrochemical impedance spectroscopy (EIS) as a new tool for investigating methods of corrosion protection. Electrochimica Acta, 35 (10), 1533–1544. https://doi.org/10.1016/0013-4686(90)80007-b
- Boukamp, B. (1986). A Nonlinear Least Squares Fit procedure for analysis of immittance data of electrochemical systems. Solid State Ionics, 20 (1), 31–44. https://doi.org/10.1016/0167-2738(86)90031-7
- Ibriş, N., Mirza Rosca, J. C. (2002). EIS study of Ti and its alloys in biological media. Journal of Electroanalytical Chemistry, 526 (1-2), 53–62. https://doi.org/10.1016/s0022-0728(02)00814-8
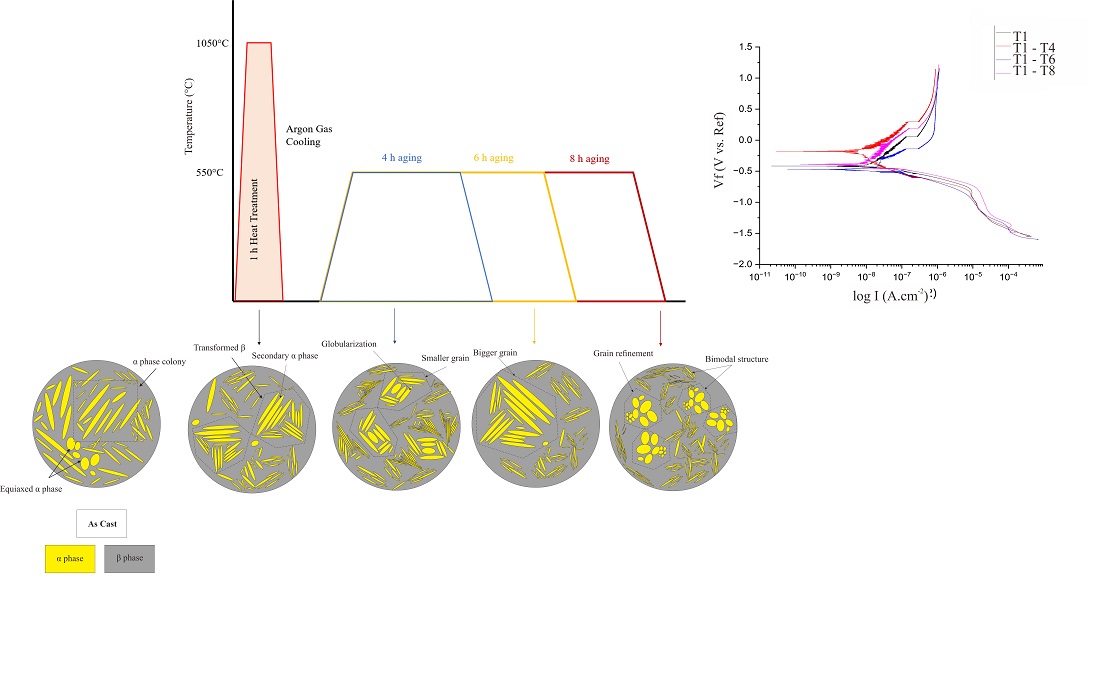
Downloads
Published
How to Cite
Issue
Section
License
Copyright (c) 2024 Anjar Oktikawati, Rini Riastuti, Damisih Damisih, I Nyoman Jujur, Agus Paul Setiawan Kaban

This work is licensed under a Creative Commons Attribution 4.0 International License.
The consolidation and conditions for the transfer of copyright (identification of authorship) is carried out in the License Agreement. In particular, the authors reserve the right to the authorship of their manuscript and transfer the first publication of this work to the journal under the terms of the Creative Commons CC BY license. At the same time, they have the right to conclude on their own additional agreements concerning the non-exclusive distribution of the work in the form in which it was published by this journal, but provided that the link to the first publication of the article in this journal is preserved.
A license agreement is a document in which the author warrants that he/she owns all copyright for the work (manuscript, article, etc.).
The authors, signing the License Agreement with TECHNOLOGY CENTER PC, have all rights to the further use of their work, provided that they link to our edition in which the work was published.
According to the terms of the License Agreement, the Publisher TECHNOLOGY CENTER PC does not take away your copyrights and receives permission from the authors to use and dissemination of the publication through the world's scientific resources (own electronic resources, scientometric databases, repositories, libraries, etc.).
In the absence of a signed License Agreement or in the absence of this agreement of identifiers allowing to identify the identity of the author, the editors have no right to work with the manuscript.
It is important to remember that there is another type of agreement between authors and publishers – when copyright is transferred from the authors to the publisher. In this case, the authors lose ownership of their work and may not use it in any way.