Determining technological parameters for obtaining ta15 titanium alloy blanks with improved mechanical characteristics using the electron-beam 3D printing method
DOI:
https://doi.org/10.15587/1729-4061.2024.306613Keywords:
electron beam 3D printing, titanium alloy, TA15, technological parameters, metallographic studiesAbstract
The object of this study is the process of electron beam 3D printing of articles made of TA15 titanium alloy powder. Peculiarities of the structure and properties formation of alloy blanks, obtained by this method have been described. Influence of process parameters (electron beam power and geometric scanning parameters) on the characteristics of the material were considered.
Step of displacement of the beam trajectory changed from 0.1 to 0.25 mm with an interval of 0.05 mm. Specific energy of the electron beam varied from 20 to 70 J/mm3 for every trajectory displacement step.
The macrostructure was examined visually while the microstructure was studied by optical microscopy. Mechanical properties were determined by uniaxial tension and impact bending tests. It was established that depending on the 3D printing parameters the macrostructure of most samples is dense but with unfavorable parameters non-fusions or shrinkage porosity defects may form. The microstructure of the dendritic type has an α´+β lamellar-acicular morphology, its dispersity and shape of α´–phase areas vary depending on the process parameters.
A scanning step of 0.2 mm and a beam energy of 40 J/mm3 allows obtaining a dispersed microstructure in which there are no non-fusions and shrinkage micropores. The value of the Rm is 27 %, and the R0.2 is 24 % higher than that of the alloy obtained by the conventional technology of electron beam melting. The A5 is 3.2 times higher. However, impact toughness of the sample with dendrite unfavorable orientation to the direction of load applying may be lower compared to conventional technology. The results could be used for devising commercial technology of high strength titanium alloys parts produced by 3D printing
References
- Murr, L. E., Gaytan, S. M., Ramirez, D. A., Martinez, E., Hernandez, J., Amato, K. N. et al. (2012). Metal Fabrication by Additive Manufacturing Using Laser and Electron Beam Melting Technologies. Journal of Materials Science & Technology, 28 (1), 1–14. https://doi.org/10.1016/s1005-0302(12)60016-4
- Lai, X., Yang, G., Wang, Y., Wei, Z. (2023). Heat and mass transfer in electron beam additive manufacturing. International Journal of Mechanical Sciences, 259, 108613. https://doi.org/10.1016/j.ijmecsci.2023.108613
- Shi, Y., Gong, S., Xu, H., Yang, G., Qiao, J., Wang, Z. et al. (2023). Electron beam metal additive manufacturing: Defects formation and in-process control. Journal of Manufacturing Processes, 101, 386–431. https://doi.org/10.1016/j.jmapro.2023.06.013
- Wang, X., Gong, X., Chou, K. (2015). Scanning Speed Effect on Mechanical Properties of Ti-6Al-4V Alloy Processed by Electron Beam Additive Manufacturing. Procedia Manufacturing, 1, 287–295. https://doi.org/10.1016/j.promfg.2015.09.026
- Wang, X., Chou, K. (2018). EBSD study of beam speed effects on Ti-6Al-4V alloy by powder bed electron beam additive manufacturing. Journal of Alloys and Compounds, 748, 236–244. https://doi.org/10.1016/j.jallcom.2018.03.173
- Batalha, G. F., Silva, L. C., Coelho, R. S., Teixeira, M. C. C., Castro, T. L., Pereira, M. V. S. et al. (2024). Mechanical properties characterization of Ti-6Al-4 V grade 5 (recycled) additively manufactured by selective electron beam melting (EB-PBF). Engineering Failure Analysis, 157, 107892. https://doi.org/10.1016/j.engfailanal.2023.107892
- Hrabe, N., Quinn, T. (2013). Effects of processing on microstructure and mechanical properties of a titanium alloy (Ti–6Al–4V) fabricated using electron beam melting (EBM), part 1: Distance from build plate and part size. Materials Science and Engineering: A, 573, 264–270. https://doi.org/10.1016/j.msea.2013.02.064
- Hrabe, N., Quinn, T. (2013). Effects of processing on microstructure and mechanical properties of a titanium alloy (Ti–6Al–4V) fabricated using electron beam melting (EBM), Part 2: Energy input, orientation, and location. Materials Science and Engineering: A, 573, 271–277. https://doi.org/10.1016/j.msea.2013.02.065
- Tamayo, J. A., Riascos, M., Vargas, C. A., Baena, L. M. (2021). Additive manufacturing of Ti6Al4V alloy via electron beam melting for the development of implants for the biomedical industry. Heliyon, 7 (5), e06892. https://doi.org/10.1016/j.heliyon.2021.e06892
- Matviichuk, V. A., Nesterenkov, V. M., Berdnikova, O. M. (2022). Additive electron beam technology of manufacture of metal products from powder materials. Avtomaticheskaya Svarka (Automatic Welding), 2022 (2), 16–25. https://doi.org/10.37434/as2022.02.03
- Matviichuk, V. A., Nesterenkov, V. M. (2020). Additive electron beam equipment for layer-by-layer manufacture of metal products from powder materials. The Paton Welding Journal, 2020 (2), 41–46. https://doi.org/10.37434/tpwj2020.02.08
- Akhonin, S., Pikulin, O., Berezos, V., Severyn, A., Erokhin, O., Kryzhanovskyi, V. (2022). Determining the structure and properties of heat-resistant titanium alloys VT3-1 and VT9 obtained by electron-beam melting. Eastern-European Journal of Enterprise Technologies, 5 (12 (119)), 6–12. https://doi.org/10.15587/1729-4061.2022.265014
- Matviichuk, V., Nesterenkov, V., Berdnikova, O. (2022). Determining the influence of technological parameters of the electron-beam surfacing process on quality indicators. Eastern-European Journal of Enterprise Technologies, 1 (12 (115)), 21–30. https://doi.org/10.15587/1729-4061.2022.253473
- Akhonin, S. V., Pikulin, O. M. (2019). Investigation of Effect of Electron Beam Surface Treatment of Titanium Alloy Ingots on Structure and Properties of Melted Metal. IOP Conference Series: Materials Science and Engineering, 582 (1), 012047. https://doi.org/10.1088/1757-899x/582/1/012047
- Matviichuk, V., Nesterenkov, V., Berdnikova, O. (2024). Determining the influence of technological parameters of electron beam surfacing process on the microstructure and microhardness of Ti-6Al-4V alloy. Eastern-European Journal of Enterprise Technologies, 1 (12 (127)), 6–12. https://doi.org/10.15587/1729-4061.2024.297773
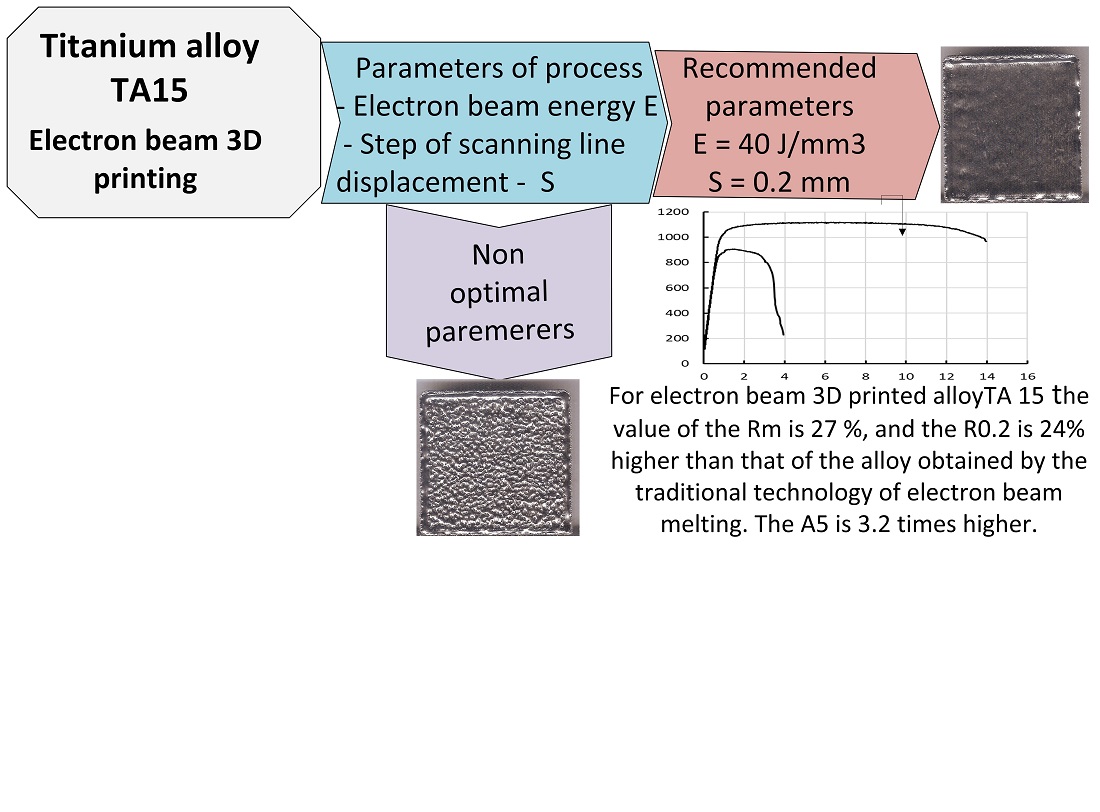
Downloads
Published
How to Cite
Issue
Section
License
Copyright (c) 2024 Serhii Akhonin, Vladimir Nesterenkov, Volodymyr Pashynskyi, Vladyslav Matviichuk, Sviatoslav Motrunich, Volodymyr Berezos, Illia Klochkov

This work is licensed under a Creative Commons Attribution 4.0 International License.
The consolidation and conditions for the transfer of copyright (identification of authorship) is carried out in the License Agreement. In particular, the authors reserve the right to the authorship of their manuscript and transfer the first publication of this work to the journal under the terms of the Creative Commons CC BY license. At the same time, they have the right to conclude on their own additional agreements concerning the non-exclusive distribution of the work in the form in which it was published by this journal, but provided that the link to the first publication of the article in this journal is preserved.
A license agreement is a document in which the author warrants that he/she owns all copyright for the work (manuscript, article, etc.).
The authors, signing the License Agreement with TECHNOLOGY CENTER PC, have all rights to the further use of their work, provided that they link to our edition in which the work was published.
According to the terms of the License Agreement, the Publisher TECHNOLOGY CENTER PC does not take away your copyrights and receives permission from the authors to use and dissemination of the publication through the world's scientific resources (own electronic resources, scientometric databases, repositories, libraries, etc.).
In the absence of a signed License Agreement or in the absence of this agreement of identifiers allowing to identify the identity of the author, the editors have no right to work with the manuscript.
It is important to remember that there is another type of agreement between authors and publishers – when copyright is transferred from the authors to the publisher. In this case, the authors lose ownership of their work and may not use it in any way.