Застосування методологій QFD та FMEA для розробки та вдосконалення конструкції робота зі знешкодження боєприпасів
DOI:
https://doi.org/10.15587/1729-4061.2024.306986Ключові слова:
розгортання функції якості, аналіз режимів та наслідків відмов, вибухова речовина, роботАнотація
У цій роботі вивчається методологія розгортання функції якості (QFD) і аналізу режиму та наслідків відмови (FMEA), заснована на концепції «Проектування для X», щоб визначити критерії проектування механічних характеристик робота зі знешкодження боєприпасів (РЗБ) і перевіряється за допомогою віртуального прототип РЗБ. Метою є застосування цієї методології для отримання продукту, який відповідає специфікаціям якості та надійності, враховуючи потреби користувача як вихідні дані. Щоб підтвердити цю методологію, техніки UDEX (підрозділу знешкодження вибухонебезпечних предметів), механічні характеристики попередньої версії JVC 0.2, розробленої дослідницькою групою Національного університету Сан-Агустіна (UNSA), мінімальні характеристики роботів, які беруть участь у Лізі роботів-рятувальників і застосування для роботи в реальному середовищі були взяті як приклад. Результати свідчать про те, що застосування запропонованої методики значно підвищило якість і надійність конструкції. Щоб підтвердити ефективність цієї методології, за допомогою програмного забезпечення для моделювання SolidWorks було створено віртуальний прототип під назвою JVC 0.3 та було досягнуто значного зменшення ваги на 27,13 %, а робочу швидкість було збільшено до 1 км/год за оптимальних умов. Технічний аналіз JVC 0.3 показав значні покращення в кількох ключових областях, таких як збільшення модульності для полегшення складання та обслуговування, зменшення загальної ваги, збільшення крутного моменту та швидкості, а також підвищення стабільності під час роботи. Ці фактори є важливими для практичного застосування РЗБ у реальних польових операціях, які виконуються спеціалізованими підрозділами, такими як UDEX
Спонсор дослідження
- With the support of the Universidad Nacional de San Agustín de Arequipa with the following contract N◦. IBA-IB-27-2020-UNSA and UDEX-AQP
Посилання
- Guevara Mamani, J., Pinto, P. P., Vilcapaza Goyzueta, D., Supo Colquehuanca, E., Sulla Espinoza, E., Silva Vidal, Y. (2021). Compilation and Analysis of Requirements for the Design of an Explosive Ordnance Disposal Robot Prototype Applied in UDEX-Arequipa. HCI International 2021 - Posters, 131–138. https://doi.org/10.1007/978-3-030-78642-7_18
- Czop, A., Hacker, K., Murphy, J., Zimmerman, T. (2005). Low-cost explosive ordnance disposal robot using off-the-shelf parts. Unmanned Ground Vehicle Technology VII, 5804, 130. https://doi.org/10.1117/12.602526
- Czop, A., Hacker, K., Murphy, J., Zimmerman, T. (2006). Low-cost EOD robot using off-the-shelf parts: revisions and performance testing results. Unmanned Systems Technology VIII, 6230, 62301Z. https://doi.org/10.1117/12.666531
- Szynkarczyk, P. (2005). Neutralising and assisting robot smr-100 expert – design problematics. Bulletin of the Polish Academy of Sciences: Technical Sciences, 53 (1), 87–92. Available at: https://journals.pan.pl/Content/111756/PDF/(53-1)87.pdf
- Grigore, L. Ștefăniță, Oncioiu, I., Priescu, I., Joița, D. (2021). Development and Evaluation of the Traction Characteristics of a Crawler EOD Robot. Applied Sciences, 11 (9), 3757. https://doi.org/10.3390/app11093757
- de Cubber, G., Balta, H., Lietart, C. (2014). Teodor: A Semi-Autonomous Search and Rescue and Demining Robot. Applied Mechanics and Materials, 658, 599–605. https://doi.org/10.4028/www.scientific.net/amm.658.599
- Ștefan, A., Grigore, L. Ștefăniță, Oncioiu, I., Constantin, D., Mustață et al. (2022). Influence of the Stiffness of the Robotic Arm on the Position of the Effector of an EOD Robot. Electronics, 11 (15), 2355. https://doi.org/10.3390/electronics11152355
- Silva Vidal, Y., Elvis Supo, C., Milton Ccallata, C., Jesus Mamani, G., Betancur P., M., Brunno Pino, C. et al. (2022). Analysis and Evaluation of a EOD Robot Prototype. 2022 IEEE International IOT, Electronics and Mechatronics Conference (IEMTRONICS), 1–6. https://doi.org/10.1109/iemtronics55184.2022.9795740
- Fargnoli, M., Sakao, T. (2016). Uncovering differences and similarities among quality function deployment-based methods in Design for X: Benchmarking in different domains. Quality Engineering, 29 (4), 690–712. https://doi.org/10.1080/08982112.2016.1253849
- Atilano, L., Martinho, A., Silva, M. A., Baptista, A. J. (2019). Lean Design-for-X: Case study of a new design framework applied to an adaptive robot gripper development process. Procedia CIRP, 84, 667–672. https://doi.org/10.1016/j.procir.2019.04.190
- Furtado, L. F. F., Villani, E., Trabasso, L. G., Silva, C. E. O. (2013). DTW: a design method for designing robot end-effectors. Journal of the Brazilian Society of Mechanical Sciences and Engineering, 36 (4), 871–885. https://doi.org/10.1007/s40430-013-0109-8
- Gonçalves-Coelho, A. M., Mourão, A. J. F. (2007). Axiomatic design as support for decision-making in a design for manufacturing context: A case study. International Journal of Production Economics, 109 (1-2), 81–89. https://doi.org/10.1016/j.ijpe.2006.11.002
- Würtenberger, J., Kloberdanz, H., Lotz, J., von Ahsen, A. (2014). Application of the FMEA during the product development process – Dependencies between level of information and quality of result. Design Methods, 417–426.
- Yang, Z., Kou, M. (2021). Innovation fusion design of mechanical system robust design. The International Journal of Advanced Manufacturing Technology, 124 (11-12), 3795–3811. https://doi.org/10.1007/s00170-021-07843-4
- Munoz, V. F., Garcia-Morales, L., Fernandez-Lozano, J., Gomez-De-Gabriel, J. M., Garcia-Cerezo, A., Vara, C. (2004). Risk analysis for fail-safe motion control implementation in surgical robotics. Proceedings World Automation Congress, 235–240.
- Backar, S. (2019). Integrative Framework of Kansei Engineering (KE) and Kano Model (KM) applied to Light Bulb Changer. The Academic Research Community Publication, 2 (4), 430–439. https://doi.org/10.21625/archive.v2i4.392
- Korayem, M. H., Iravani, A. (2008). Improvement of 3P and 6R mechanical robots reliability and quality applying FMEA and QFD approaches. Robotics and Computer-Integrated Manufacturing, 24 (3), 472–487. https://doi.org/10.1016/j.rcim.2007.05.003
- Shvetsova, O. A., Park, S. C., Lee, J. H. (2021). Application of Quality Function Deployment for Product Design Concept Selection. Applied Sciences, 11 (6), 2681. https://doi.org/10.3390/app11062681
- Büyüközkan, G., Ilıcak, Ö., Feyzioğlu, O. (2021). An Integrated QFD Approach for Industrial Robot Selection. Advances in Production Management Systems. Artificial Intelligence for Sustainable and Resilient Production Systems, 561–570. https://doi.org/10.1007/978-3-030-85906-0_61
- Sørensen, C. G., Jørgensen, R. N., Maagaard, J., Bertelsen, K. K., Dalgaard, L., Nørremark, M. (2010). Conceptual and user-centric design guidelines for a plant nursing robot. Biosystems Engineering, 105 (1), 119–129. https://doi.org/10.1016/j.biosystemseng.2009.10.002
- Li, M., Zhang, A. (2022). Innovative design of intelligent medical delivery robot based on FAHP and QFD. ICETIS 2022; 7th International Conference on Electronic Technology and Information Science.
- Pasawang, T., Chatchanayuenyong, T., Sa-Ngiamvibool, W. (2015). QFD-based conceptual design of an autonomous underwater robot. Songklanakarin Journal of Science and Technology, 37 (6), 659–668. Available at: https://www.thaiscience.info/journals/Article/SONG/10977690.pdf
- Jiménez, G. E. C., Cárdenas, D. J. M., Aponte, J. A., Sánchez, O. F. A., Monroy, M. F. M. (2017). QFD design methology and construction of a type rover mobile robotic platform. ARPN Journal of Engineering and Applied Sciences, 12 (4), 1098–1104. Available at: http://www.arpnjournals.org/jeas/research_papers/rp_2017/jeas_0217_5731.pdf
- Kobayashi, H., Shimizu, R., Takeuchi, K., Sugai, R., Hasegawa, H. (2022). RoboCup Rescue 2022 Team Description Paper Nexis-R. RoboCup Rescue 2022. Available at: https://tdp.robocup.org/wp-content/uploads/tdp/robocup/2022/robocuprescue-robot/nexis-r-355/robocup-2022-robocuprescue-robot-nexis-riU2awoV6f5.pdf
- Morimoto, Y., Tomiyama, T., Michikawa, R. (2022). RoboCup Rescue 2022 Team Description Paper SHINOBI. ROBOCUP RESCUE 2022. Available at: https://tdp.robocup.org/wp-content/uploads/tdp/robocup/2022/robocuprescue-robot/shinobi-356/robocup-2022-robocuprescue-robot-shinobiAw37ofmjWF.pdf
- Karmaker, C. L., Halder, P., Ahmed, S. M. T. (2019). Customer driven quality improvement of a specific product through AHP and entropy based QFD: a case study. International Journal of the Analytic Hierarchy Process, 11 (3), 389–414. https://doi.org/10.13033/ijahp.v11i3.606
- Mamani G., J., Ccallata C., M., Flores, E. V., Meneses, D., Betancur, M. A., Silva, Y. L., Apaza, J. L. (2024). Development of an EOD Robot for the Arequipa Explosive Disposal Unit. International Journal of Mechanical Engineering and Robotics Research, 13 (4), 414–427. https://doi.org/10.18178/ijmerr.13.4.414-427
- Vilcapaza Goyzueta, D., Guevara Mamani, J., Sulla Espinoza, E., Supo Colquehuanca, E., Silva Vidal, Y., Pinto, P. P. (2021). Evaluation of a NUI Interface for an Explosives Deactivator Robotic Arm to Improve the User Experience. HCI International 2021 - Late Breaking Posters, 288–293. https://doi.org/10.1007/978-3-030-90176-9_37
- Montoya Angulo, A., Pari Pinto, L., Sulla Espinoza, E., Silva Vidal, Y., Supo Colquehuanca, E. (2022). Assisted Operation of a Robotic Arm Based on Stereo Vision for Positioning near an Explosive Device. Robotics, 11 (5), 100. https://doi.org/10.3390/robotics11050100
- Andres, M. A., Pari, L., Elvis, S. C. (2021). Design of a User Interface to Estimate Distance of Moving Explosive Devices with Stereo Cameras. 2021 6th International Conference on Image, Vision and Computing (ICIVC), 362–366. https://doi.org/10.1109/icivc52351.2021.9526934
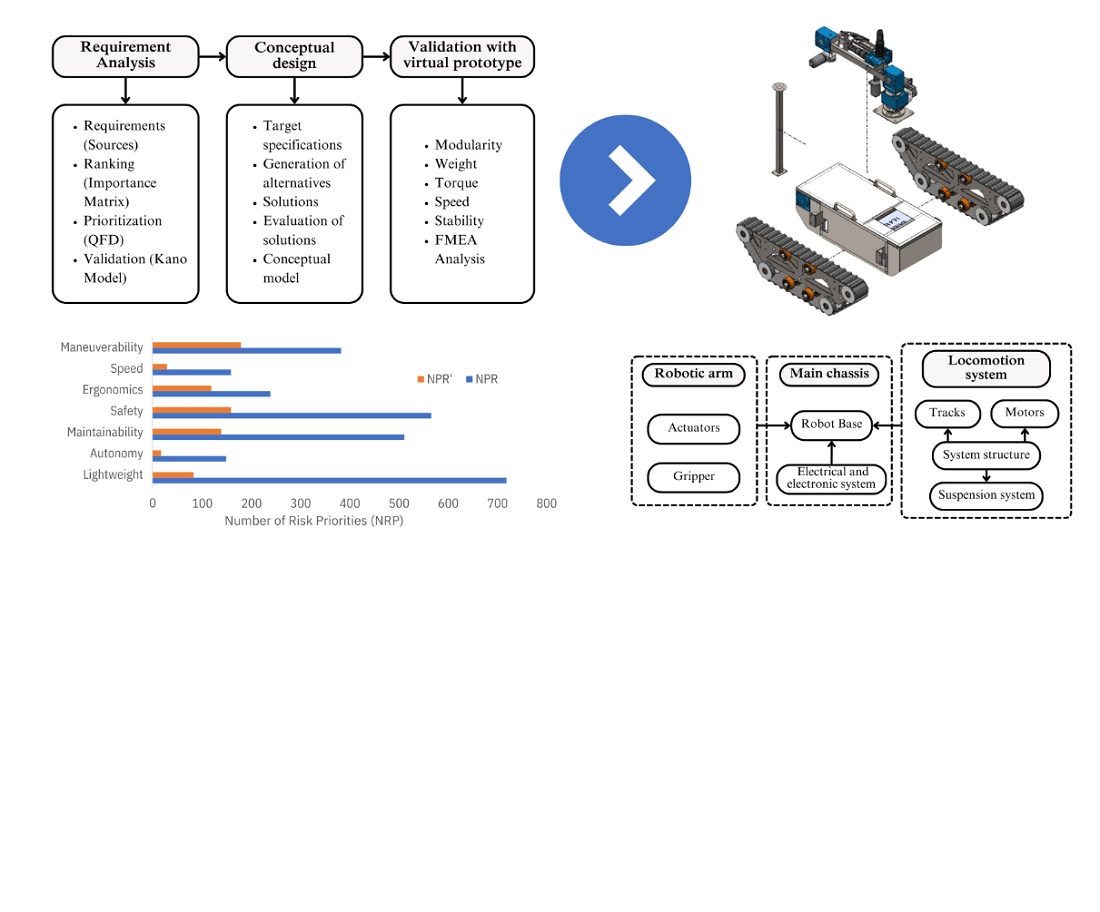
##submission.downloads##
Опубліковано
Як цитувати
Номер
Розділ
Ліцензія
Авторське право (c) 2024 Brayan Alex Apfata Limachi, Frank Alexander Cari Mora, Yuri Saúl Sivincha Quispe, Erick Valdeiglesias Flores, Yuri Lester Silva Vidal, Erasmo Sulla Espinoza, Lizardo Pari

Ця робота ліцензується відповідно до Creative Commons Attribution 4.0 International License.
Закріплення та умови передачі авторських прав (ідентифікація авторства) здійснюється у Ліцензійному договорі. Зокрема, автори залишають за собою право на авторство свого рукопису та передають журналу право першої публікації цієї роботи на умовах ліцензії Creative Commons CC BY. При цьому вони мають право укладати самостійно додаткові угоди, що стосуються неексклюзивного поширення роботи у тому вигляді, в якому вона була опублікована цим журналом, але за умови збереження посилання на першу публікацію статті в цьому журналі.
Ліцензійний договір – це документ, в якому автор гарантує, що володіє усіма авторськими правами на твір (рукопис, статтю, тощо).
Автори, підписуючи Ліцензійний договір з ПП «ТЕХНОЛОГІЧНИЙ ЦЕНТР», мають усі права на подальше використання свого твору за умови посилання на наше видання, в якому твір опублікований. Відповідно до умов Ліцензійного договору, Видавець ПП «ТЕХНОЛОГІЧНИЙ ЦЕНТР» не забирає ваші авторські права та отримує від авторів дозвіл на використання та розповсюдження публікації через світові наукові ресурси (власні електронні ресурси, наукометричні бази даних, репозитарії, бібліотеки тощо).
За відсутності підписаного Ліцензійного договору або за відсутністю вказаних в цьому договорі ідентифікаторів, що дають змогу ідентифікувати особу автора, редакція не має права працювати з рукописом.
Важливо пам’ятати, що існує і інший тип угоди між авторами та видавцями – коли авторські права передаються від авторів до видавця. В такому разі автори втрачають права власності на свій твір та не можуть його використовувати в будь-який спосіб.