Designing a helical knife for a shredding drum using a sweep surface
DOI:
https://doi.org/10.15587/1729-4061.2024.308195Keywords:
unfolding helicoid, flat workpiece, return edge, helical knife, shredding drumAbstract
The object of this paper is a helical blade in a shredding drum from a sweep surface. Such drums are used in harvesters for crushing plant mass. If the flat blades are installed on the drum, cutting of the plant mass occurs simultaneously along the entire length of the blade. This could cause a pulsating dynamic load. If a flat knife with a straight blade is installed at an angle to the axis of the drum, then the distances from it to the points of the blade will be different, as well as the cutting conditions along the blade. The elliptical shape enables the same distance from the axis of rotation to the points of the blade, but this does not solve the problem. Many short flat knives with a straight blade can be mounted on the drum, placing them in such a way that the time between the individual knives is minimized. However, all these disadvantages can be eliminated by a helical knife with a blade in the form of a helical line.
The design of a helical knife from an unfolding helicoid has been considered. In differential geometry, the bending of unfolded surfaces of zero thickness is considered. Bending of the workpiece into a finished product occurs with minimal plastic deformations, the magnitude of which depends on the thickness of the workpiece sheet. The methods of differential geometry of unfolding surfaces were applied to the analytical description of the surface of the helical knife.
The parametric equations of the unfolding helicoid were derived according to the given structural parameters of the knife in space and on the plane. That has made it possible to mathematically describe the contour lines that cut the knife from the surface and on its sweep. Formulae for calculating a flat workpiece through the structural parameters of the knife have been derived. Thus, with the specified structural parameters of the knife R=0.25 m, τ=20°, φ=65°, according to the resulting formula, we find the radius of the knife blade on a flat workpiece: R0=4.8 m.
References
- Tian, F., Xia, K., Wang, J., Song, Z., Yan, Y., Li, F., Wang, F. (2021). Design and experiment of self-propelled straw forage crop harvester. Advances in Mechanical Engineering, 13 (7), 168781402110244. https://doi.org/10.1177/16878140211024455
- Derevyanko, D. A., Polishchuk, V. M., Chichilyuk, S. B., Derevyanko, А. D. (2020). Substantiation of effect of ladle conveyors on injury and quality of seeds of cereals. Machinery & Energetics, 11 (1), 163–169. Available at: https://technicalscience.com.ua/web/uploads/pdf/Machinery%20&%20Energetics_Vol.%2011,%20No.%201_163_169.pdf
- Buslаiev, D. O., Vаsylenko, M. O. (2020). Traction resistance of cultivator paws with surface hardening during operation of tillage machines. Machinery & Energetics, 11 (1), 177–182. Available at: https://technicalscience.com.ua/uk/journals/t-11-1-2020/tyagoviy-opir-kultivatornikh-lap-z-povyerkhnyevim-zmitsnyennyam-pri-yekspluatatsiyi-gruntoobrobnikh-mashin
- Mudarisov, S. G., Gabitov, I. I., Lobachevsky, Y. P., Mazitov, N. K., Rakhimov, R. S., Khamaletdinov, R. R. et al. (2019). Modeling the technological process of tillage. Soil and Tillage Research, 190, 70–77. https://doi.org/10.1016/j.still.2018.12.004
- Morris, N. L., Miller, P. C. H., Orson, J. H., Froud-Williams, R. J. (2010). The adoption of non-inversion tillage systems in the United Kingdom and the agronomic impact on soil, crops and the environment – A review. Soil and Tillage Research, 108 (1-2), 1–15. https://doi.org/10.1016/j.still.2010.03.004
- Tesliuk, H., Volik, B., Sokol, S., Ponomarenko, N. (2019). Design of working bodies for tillage tools using the methods of bionics. Eastern-European Journal of Enterprise Technologies, 3 (1 (99)), 49–54. https://doi.org/10.15587/1729-4061.2019.169156
- Kobets, A., Aliiev, E., Tesliuk, H., Aliieva, O. (2023). Simulation of the process of interaction of the working bodies of tillage machines with the soil in Simcenter STAR-CCM+. Machinery & Energetics, 14 (1). https://doi.org/10.31548/machinery/1.2023.09
- Kobets, A. S., Pugach, A. M., Kharytonov, M. M. (2018). Justification of the cultivator sweep and strengthening elements on the working surface. INMATEH – Agricultural Engineering, 54 (1), 161–170. Available at: https://dspace.dsau.dp.ua/bitstream/123456789/726/1/1.pdf
- Klendii, M., Klendii, M. I., Shatrov, R. V. (2020). Research of influence of constructive and technological parameters of developed variants of screws with screw working bodies rabbit. Machinery & Energetics, 11 (4), 65–71. https://doi.org/10.31548/machenergy2020.04.065
- Chvartatskiy, I., Flonts, I., Grabar, A., Shatrov, R. (2021). Synthesis of energy-saving transport-technological systems with screw working bodies. Machinery & Energetics, 12 (4), 77–84. https://doi.org/10.31548/machenergy2021.04.077
- Kresan, T. A. (2020). Calculation of gravitation descent formed by surface of skew closed helicoid. Machinery & Energetics, 11 (2), 49–57. Available at: https://technicalscience.com.ua/web/uploads/pdf/Machinery%20&%20Energetics_Vol.%2011,%20No.%202_49-57.pdf
- Kresan, Т. (2021). Movement of soil particles on surface of developable helicoid with horizontal axis of rotation with given angle of attack. Machinery & Energetics, 12 (2), 67–75. https://doi.org/10.31548/machenergy2021.02.067
- Pylypaka, S., Klendii, M., Kresan, Т. (2022). Study of the movement of soil particles on the surface of a screw tillage working body. Machinery & Energetics, 13 (2), 62–72. https://doi.org/10.31548/machenergy.13(2).2022.62-72
- Paladiychuk, Yu. B., Melnik, Ju. M. (2021). Restoration resource of working bodies of soil treatment machines by applying wear-resistant coatings. Machinery & Energetics, 12 (4), 43–52. https://doi.org/10.31548/machenergy2021.04.043
- Borak, K. V. (2020). Influence of degree of abrasive particle clinging to wear mechanism of soil-cultivating machines operational mechanisms. Machinery & Energetics, 11 (2), 35–40. Available at: https://technicalscience.com.ua/uk/journals/t-11-2-2020/vpliv-stupyenya-zakriplyennya-abrazivnoyi-chastinki-na-myekhanizm-znoshuvannya-robochikh-organiv-gruntoobrobnikh-mashin
- Tan, C. M., Lin, G. Y. (2016). An Innovative Compression Mold Design for Manufacture of Reel Mower Helical Blades. Applied Mechanics and Materials, 851, 255–258. https://doi.org/10.4028/www.scientific.net/amm.851.255
- Li, Z. F., Jiang, L. Q. (2013). Design of Combined Helical Blade Manufacturing Device. Advanced Materials Research, 753-755, 1386–1390. https://doi.org/10.4028/www.scientific.net/amr.753-755.1386
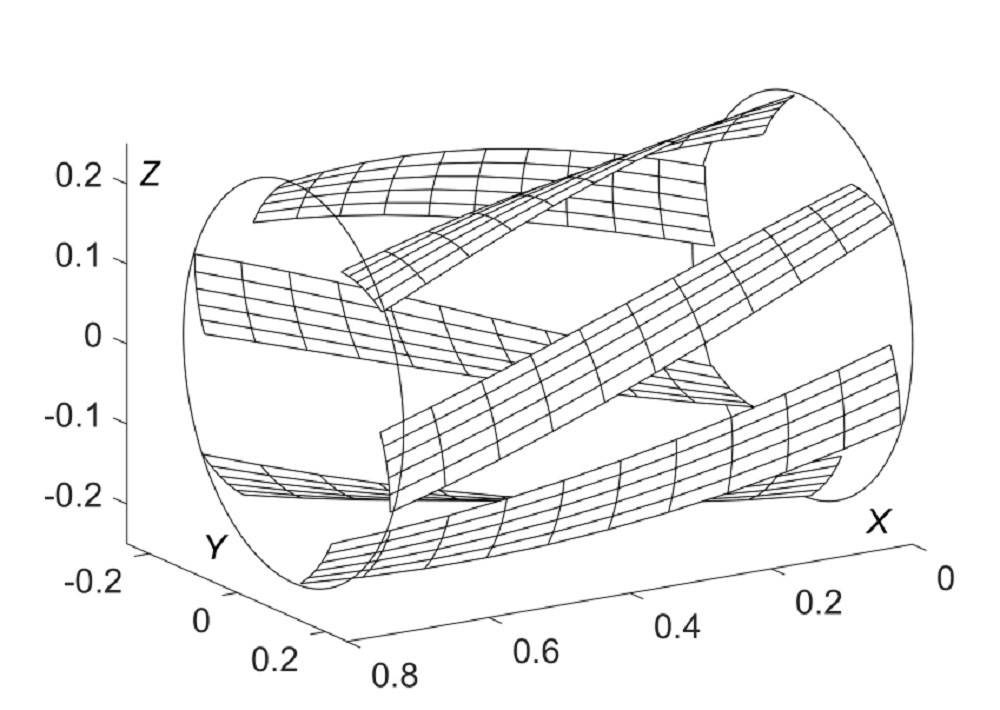
Downloads
Published
How to Cite
Issue
Section
License
Copyright (c) 2024 Serhii Pylypaka, Vyacheslav Hropost, Viktor Nesvidomin, Tetiana Volina, Mykhailo Kalenyk, Mykola Volokha, Olha Zalevska, Ivan Shuliak, Serhii Dieniezhnikov, Svetlana Motsak

This work is licensed under a Creative Commons Attribution 4.0 International License.
The consolidation and conditions for the transfer of copyright (identification of authorship) is carried out in the License Agreement. In particular, the authors reserve the right to the authorship of their manuscript and transfer the first publication of this work to the journal under the terms of the Creative Commons CC BY license. At the same time, they have the right to conclude on their own additional agreements concerning the non-exclusive distribution of the work in the form in which it was published by this journal, but provided that the link to the first publication of the article in this journal is preserved.
A license agreement is a document in which the author warrants that he/she owns all copyright for the work (manuscript, article, etc.).
The authors, signing the License Agreement with TECHNOLOGY CENTER PC, have all rights to the further use of their work, provided that they link to our edition in which the work was published.
According to the terms of the License Agreement, the Publisher TECHNOLOGY CENTER PC does not take away your copyrights and receives permission from the authors to use and dissemination of the publication through the world's scientific resources (own electronic resources, scientometric databases, repositories, libraries, etc.).
In the absence of a signed License Agreement or in the absence of this agreement of identifiers allowing to identify the identity of the author, the editors have no right to work with the manuscript.
It is important to remember that there is another type of agreement between authors and publishers – when copyright is transferred from the authors to the publisher. In this case, the authors lose ownership of their work and may not use it in any way.