Improving the technological process of balancing electric machine rotors on a balancing machine
DOI:
https://doi.org/10.15587/1729-4061.2024.309867Keywords:
railroad transport, vibrations of electric machines, imbalance, mechanical balancing of rotors, balancing machineAbstract
The object of research is the process of dynamic balancing of rotors on a balancing machine in the process of restoring electric machines.
The work is aimed at improving the quality of balancing rotors in the process of major repairs of traction electric motors for electric trains. The problem addressed was the quality of balancing the rotors of electric machines on stationary balancing machines. According to the conventional balancing technology, the rotor to be balanced is mounted on the supports of the balancing machine with support surfaces that usually have mechanical defects. These defects cannot be eliminated by machining due to the peculiarities of rotor repair technology. Theoretical and experimental studies of the effect of damage to the rotor support surfaces on the balancing parameters have been carried out. It has been proven that the properties of the bearing surfaces of the rotor during its balancing on a balancing machine significantly affect the results of determining the imbalance. At the same time, the difference in the mass values of balancing loads can reach 25 %. This is because damage to the bearing surfaces of the rotor generates false signals unrelated to the imbalance.
In order to increase the accuracy of determining the mass of balancing loads during rotor balancing, it is proposed to improve the technological process of balancing. The improvement involves the inclusion of a frequency filter in the signal conversion chain of acceleration sensors. The filter is designed to separate signals with a frequency greater than the rotational frequency of the rotor.
A condition for the practical application of the research results is the expediency of introducing a frequency filter of signals of acceleration sensors with a threshold frequency of filtering signals that exceeds the rotational frequency of the rotor into the schematic diagram of the balancing machine.
References
- Tiwari, R. (2017). Rotor systems: analysis and identification. CRC Press. https://doi.org/10.1201/9781315230962
- Rangel-Magdaleno, J., Peregrina-Barreto, H., Ramirez-Cortes, J., Morales-Caporal, R., Cruz-Vega, I. (2016). Vibration Analysis of Partially Damaged Rotor Bar in Induction Motor under Different Load Condition Using DWT. Shock and Vibration, 2016, 1–11. https://doi.org/10.1155/2016/3530464
- Ágoston, K. (2015). Fault Detection of the Electrical Motors Based on Vibration Analysis. Procedia Technology, 19, 547–553. https://doi.org/10.1016/j.protcy.2015.02.078
- Hraniak, V., Solona, O. (2022). Prospects for detecting defects in rotating electric machines on the basis of the analysis of their vibration signals. Vibrations in Engineering and Technology, 1 (104), 20–29. https://doi.org/10.37128/2306-8744-2022-1-3
- Ibraheem, A. A., Ghazaly, N. M., Abd el-Jaber, G. (2019). Review of rotor balancing techniques. American Journal of Industrial Engineering, 6 (1), 19–25.
- Gangsar, P., Tiwari, R. (2017). Comparative investigation of vibration and current monitoring for prediction of mechanical and electrical faults in induction motor based on multiclass-support vector machine algorithms. Mechanical Systems and Signal Processing, 94, 464–481. https://doi.org/10.1016/j.ymssp.2017.03.016
- Ágoston, K. (2016). Vibration Detection of the Electrical Motors using Strain Gauges. Procedia Technology, 22, 767–772. https://doi.org/10.1016/j.protcy.2016.01.037
- Zubenko, D. Yu. (2012). Justification of diagnostic characteristics of rotors disbalance of traction engine of rolling stock. Eastern-European Journal of Enterprise Technologies, 3 (8 (51)), 16–18. Available at: https://journals.uran.ua/eejet/article/view/1651
- Znaidiuk, V. H., Ostrovskyi, O. S. (2013). Diahnostyka tekhnichnoho stanu shvydkokhidnykh barabaniv. Mashynobuduvannia, 11, 8–13.
- Li, L., Cao, S., Li, J., Nie, R., Hou, L. (2021). Review of Rotor Balancing Methods. Machines, 9 (5), 89. https://doi.org/10.3390/machines9050089
- MacCamhaoil, M. (2016). Static and dynamic balancing of rigid rotors. Bruel & Kjaer application notes.
- Horvath, R., Flowers, G. T., Fausz, J. (2008). Passive Balancing of Rotor Systems Using Pendulum Balancers. Journal of Vibration and Acoustics, 130 (4). https://doi.org/10.1115/1.2731401
- Svyrydov, V. I. (2015). Analiz osnovnykh defektiv pry roboti nasosnykh ahrehativ. Vodnyi transport, 2, 86–91. Available at: http://nbuv.gov.ua/UJRN/Vodt_2015_2_13
- Puerto-Santana, C., Ocampo-Martinez, C., Diaz-Rozo, J. (2022). Mechanical rotor unbalance monitoring based on system identification and signal processing approaches. Journal of Sound and Vibration, 541, 117313. https://doi.org/10.1016/j.jsv.2022.117313
- Lee, C.-W. (1993). Vibration Analysis of Rotors. In Solid Mechanics and Its Applications. Springer Netherlands. https://doi.org/10.1007/978-94-015-8173-8
- Curtis, G. C., McInturff, J. A., Rubel, H. J., Wall, W. F. (1980). Pat. No. US4238960A. Means for balancing rotors of a machine. Available at: https://patents.google.com/patent/US4238960A/en
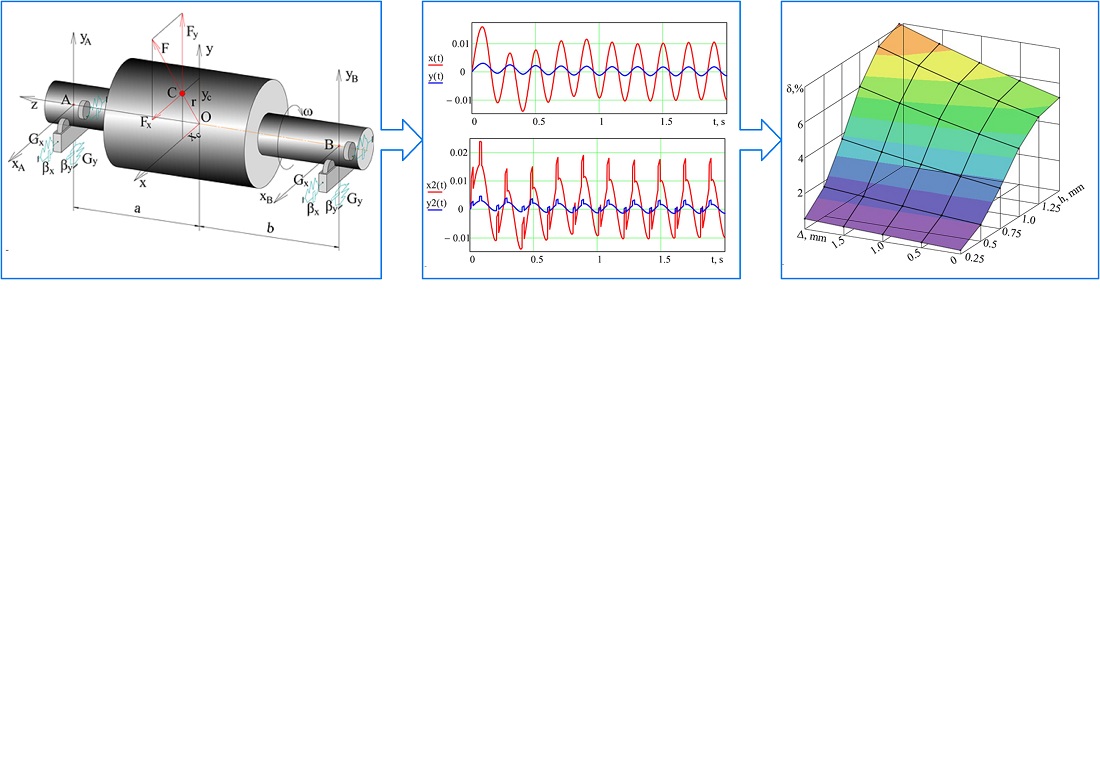
Downloads
Published
How to Cite
Issue
Section
License
Copyright (c) 2024 Yaroslav Shostak, Oleh Holovashchenko, Yuriy Reshetnikov, Viktor Tkachenko

This work is licensed under a Creative Commons Attribution 4.0 International License.
The consolidation and conditions for the transfer of copyright (identification of authorship) is carried out in the License Agreement. In particular, the authors reserve the right to the authorship of their manuscript and transfer the first publication of this work to the journal under the terms of the Creative Commons CC BY license. At the same time, they have the right to conclude on their own additional agreements concerning the non-exclusive distribution of the work in the form in which it was published by this journal, but provided that the link to the first publication of the article in this journal is preserved.
A license agreement is a document in which the author warrants that he/she owns all copyright for the work (manuscript, article, etc.).
The authors, signing the License Agreement with TECHNOLOGY CENTER PC, have all rights to the further use of their work, provided that they link to our edition in which the work was published.
According to the terms of the License Agreement, the Publisher TECHNOLOGY CENTER PC does not take away your copyrights and receives permission from the authors to use and dissemination of the publication through the world's scientific resources (own electronic resources, scientometric databases, repositories, libraries, etc.).
In the absence of a signed License Agreement or in the absence of this agreement of identifiers allowing to identify the identity of the author, the editors have no right to work with the manuscript.
It is important to remember that there is another type of agreement between authors and publishers – when copyright is transferred from the authors to the publisher. In this case, the authors lose ownership of their work and may not use it in any way.