The important factors for structure and mechanical properties in the repair of iron base metal component by thermal spray and welding processes
DOI:
https://doi.org/10.15587/1729-4061.2024.310239Keywords:
cast iron, repair, thermal spray, welding, spraying distance, microstructure, hardnessAbstract
Cast iron is widely used in the manufacturing industry due to its high strength and wear resistance properties. However, cast iron's brittle nature results in frequent failure of cracks during formation or use. Among the repair methods that can be used are thermal spray and the welding process. Even though both welding and thermal spray have been implemented for various metal repairs processes, however very limited technical reports as well as scientific papers are found for this topic. Therefore, the optimum condition of metal repair by both processes is still needed to be explored. The present works focus on the comparison between thermal spray and welding method for cast iron repairs purposes. In the experiment of thermal spray process focus has been given in optimizing spraying distance on microstructure and hardness properties. On the other hand, in the welding experimental works focus has been given on the influence of groove design on microstructure and hardness. Each research variable is carried out to obtain optimal crack repair results. It was observed that thermal spray process produces less Heat Affected Zone (HAZ) area compared to the welding process therefore having less critical area. The highest hardness value of thermal spray method is 101.33 shown by 30 cm spraying distance. Meanwhile, the highest hardness value of HAZ area of welding method is 600 HV shown by specimen A. It was obtained that from the present experimental works, thermal spray process produces better results than welding process. However, the value of the specimen hardness produced by the welding and thermal spray method depends on the type of coating material used
References
- Reed, G. J. (2014). Understanding cast iron and repairing damaged castings permanently. LOCK-N-STITCH. Available at: https://asremavad.com/wp-content/uploads/2019/03/31-Understanding-cast-iron-and-repairing-damaged-castings-permanently.pdf
- Properties and Selection: Irons, Steels, and High-Performance Alloys (1990). ASM Handbook Committee. https://doi.org/10.31399/asm.hb.v01.9781627081610
- Wube Dametew, A. (2015). Experimental Investigation on Weld Ability of Cast Iron. Science Discovery, 3 (6), 71. https://doi.org/10.11648/j.sd.20150306.15
- Arc Welding of Specific Steels and Cast Irons (2015). KOBELCO. Available at: https://www.kobelco.co.jp/english/welding/events/files/2015_KOBELCO_Specific.pdf
- Askari-Paykani, M., Shayan, M., Shamanian, M. (2014). Weldability of Ferritic Ductile Cast Iron Using Full Factorial Design of Experiment. Journal of Iron and Steel Research International, 21 (2), 252–263. https://doi.org/10.1016/s1006-706x(14)60039-x
- Permana, M. S., Suratman, R. (2012). How to Repair Surface Defect of Gray Cast Iron Components. Proc. XI Annu. Natl. Semin. Mech. Eng. (SNTTM XI) Thermofluid IV Univ. Gadjah Mada. Available at: https://pdfcoffee.com/08-how-to-repair-surface-defect-of-gray-cast-iron-components-pdf-free.html
- Wiryosumarto, H., Okumura, T. (2000). Metal Welding Technology. Jakarta: Pradnya Paramita.
- Butola, R. (2013). Study of Microstructure, Impact Strength on Manual Metal Arc Welding Of Gray Cast Iron Using Enife–Ci Filler Metal. IOSR Journal of Engineering, 3 (7), 37–42. https://doi.org/10.9790/3021-03733742
- Callister, W. D. (1999). Materials Science and Engineering - An Introduction (5th edition). Aircraft Engineering and Aerospace Technology, 71 (6). https://doi.org/10.1108/aeat.1999.12771fae.004
- Gouveia, R., Silva, F., Paiva, O., Andrade, M., Silva, L., Moselli, P., Papis, K. (2017). Study of the Heat-Treatments Effect on High Strength Ductile Cast Iron Welded Joints. Metals, 7 (9), 382. https://doi.org/10.3390/met7090382
- Sonawan, H., Suratman, R. (2006). Introduction to Understanding Metal Welding. Alfabeta. Available at: https://www.scribd.com/document/374354885/Pengantar-Untuk-Memahami-Proses-Pengelasan-Logam
- Maranho, O., Rodrigues, D., Boccalini, M., Sinatora, A. (2008). Influence of parameters of the HVOF thermal spray process on the properties of multicomponent white cast iron coatings. Surface and Coatings Technology, 202 (15), 3494–3500. https://doi.org/10.1016/j.surfcoat.2007.12.026
- Almeida, E. (2000). Surface Treatments and Coatings for Metals. A General Overview. 1. Surface Treatments, Surface Preparation, and the Nature of Coatings. Industrial & Engineering Chemistry Research, 40 (1), 3–14. https://doi.org/10.1021/ie000209l
- Jalali Azizpour, M., Tolouei-Rad, M. (2019). The effect of spraying temperature on the corrosion and wear behavior of HVOF thermal sprayed WC-Co coatings. Ceramics International, 45 (11), 13934–13941. https://doi.org/10.1016/j.ceramint.2019.04.091
- Vardavoulias, M., Economou, S., Papapanos, G. (2023). Industrial Component Restoration Using Thermal Spray Technologies. Surface Modification Technologies XVIII: Proceedings of the Eighteenth International Conference on Surface Modification Technologies Held in Dijon, France November 15-17, 2004: V. 18, 195–200. https://doi.org/10.1201/9781003423874-48
- Sahraoui, T., Guessasma, S., Ali Jeridane, M., Hadji, M. (2010). HVOF sprayed WC–Co coatings: Microstructure, mechanical properties and friction moment prediction. Materials & Design, 31 (3), 1431–1437. https://doi.org/10.1016/j.matdes.2009.08.037
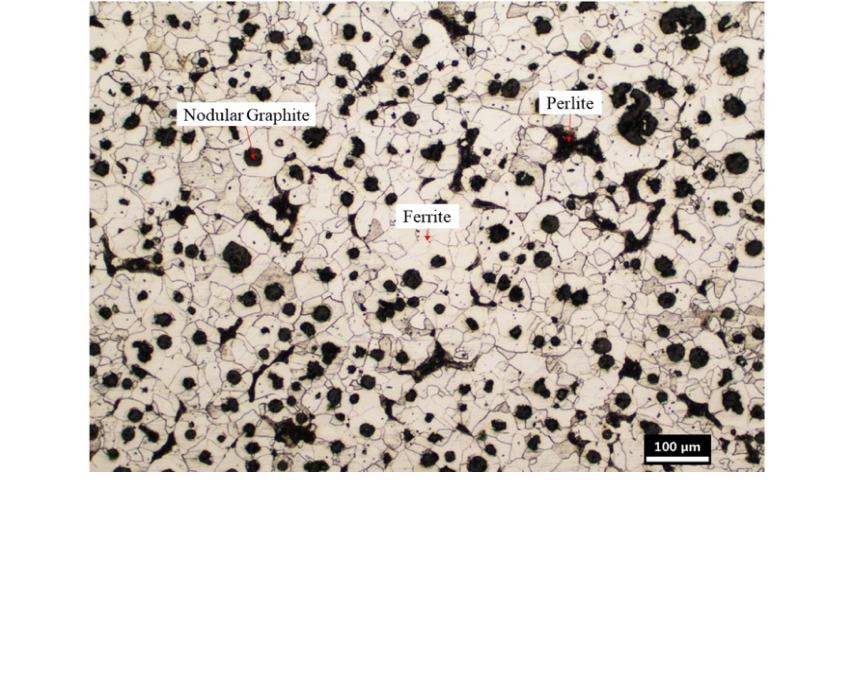
Downloads
Published
How to Cite
Issue
Section
License
Copyright (c) 2024 Raden Dadan Ramdan, Yasya Nur Muhammad, Sihol Christian Lumbantoruan, Irma Pratiwi, Bambang Widyanto, Aditianto Ramelan

This work is licensed under a Creative Commons Attribution 4.0 International License.
The consolidation and conditions for the transfer of copyright (identification of authorship) is carried out in the License Agreement. In particular, the authors reserve the right to the authorship of their manuscript and transfer the first publication of this work to the journal under the terms of the Creative Commons CC BY license. At the same time, they have the right to conclude on their own additional agreements concerning the non-exclusive distribution of the work in the form in which it was published by this journal, but provided that the link to the first publication of the article in this journal is preserved.
A license agreement is a document in which the author warrants that he/she owns all copyright for the work (manuscript, article, etc.).
The authors, signing the License Agreement with TECHNOLOGY CENTER PC, have all rights to the further use of their work, provided that they link to our edition in which the work was published.
According to the terms of the License Agreement, the Publisher TECHNOLOGY CENTER PC does not take away your copyrights and receives permission from the authors to use and dissemination of the publication through the world's scientific resources (own electronic resources, scientometric databases, repositories, libraries, etc.).
In the absence of a signed License Agreement or in the absence of this agreement of identifiers allowing to identify the identity of the author, the editors have no right to work with the manuscript.
It is important to remember that there is another type of agreement between authors and publishers – when copyright is transferred from the authors to the publisher. In this case, the authors lose ownership of their work and may not use it in any way.