Development of excavator arm movement with wireless control using Bluetooth and the Internet of Things (IoT)
DOI:
https://doi.org/10.15587/1729-4061.2024.312074Keywords:
heavy equipment, wireless control, excavator model, pneumatic valve, microcontrollerAbstract
This research is to develop a wired control system into a wireless control system on a laboratory scale mini excavator. First step is to review the development of the drive system and control system on previous excavator models, change the pneumatic drive system to electro-pneumatic, changing the control system from wired control to wireless control using Bluetooth and Internet of Things (IoT) system. The excavator with scale 1:14 is driven by a pneumatic system. The movement of the actuator is controlled using a wired remote, so that the working area is still limited to a certain area. The pneumatic control system on previous excavators was developed into an electro-pneumatic control system. Electro-pneumatic control system by replacing the 5/2-way directional valve with a 5/3-way double solenoid directional valve. With this valve, the movement of the excavator arms can be adjusted according to the operator’s wishes. The wired control system was developed into a wires control system including the Bluetooth system and the Internet of Things (IoT). Important components in these two control systems are Arduino Mega 2560, WEMOS D1 R32, 16 channel relay, and HC05 module. The excavator model with the development of a new control system has unchanged dimensions from the previous model. The excavator arms still use the previous excavator arms as well as the traveler with the same undercarriage. Only the body housing the control system is adapted to the new component layout area. Testing the wireless remote system is at a distance of around 30 meters, while the IoT remote system at a distance of around 1.5 km. The movement of each step is easier to regulate because it uses a 5/3-way directional valve. The time used for each step is also less than previous excavator models
Supporting Agency
- The authors would like to thank LPPM Universitas Riau for funding this research
References
- Nazaruddin, Gunawan, K., (2015). Undercarriage Design of Excavator Model in Application of Various Track Drive. Journal of Subsea and Offshore, 26. Available at: https://isomase.org/JOMAse/Vol.26%20Dec%202015/26-1.pdf
- Nazaruddin, Suhandi, A. (2015). Modification and Testing System Control and Swing Model Excavator System. Journal of Subsea and Offshore, 25. Available at: https://isomase.org/JOMAse/Vol.25%20Nov%202015/25-1.pdf
- Kolhe, P., Kalbande, K., Deshmukh, A. (2022). Internet of Thing and Machine Learning Approach for Agricultural Application: A Review. 2022 10th International Conference on Emerging Trends in Engineering and Technology - Signal and Information Processing (ICETET-SIP-22), 1–6. https://doi.org/10.1109/icetet-sip-2254415.2022.9791751
- Mishra, M., Lourenço, P. B., Ramana, G. V. (2022). Structural health monitoring of civil engineering structures by using the internet of things: A review. Journal of Building Engineering, 48, 103954. https://doi.org/10.1016/j.jobe.2021.103954
- Yusof, E. M. M., Yusof, M. I., Ali, R., Harjimi, I. H., Bahrin, Q. K. (2020). Welding station monitoring system using internet of thing (IOT). Indonesian Journal of Electrical Engineering and Computer Science, 18 (3), 1319. https://doi.org/10.11591/ijeecs.v18.i3.pp1319-1330
- Kurnia, R., Mulyanti, B., Widiaty, I. (2020). Internet of things application in mechanical learning in automotive engineering. IOP Conference Series: Materials Science and Engineering, 830 (4), 042098. https://doi.org/10.1088/1757-899x/830/4/042098
- Raufelder, J. (2021). Modeling Analysis of Attitude Perception of Engineering Manipulator Supporting Wireless Communication and Internet of Things. Kinetic Mechanical Engineering, 2 (2). https://doi.org/10.38007/kme.2021.020203
- Abikoye, O. C., Bajeh, A. O., Awotunde, J. B., Ameen, A. O., Mojeed, H. A., Abdulraheem, M. et al. (2021). Application of Internet of Thing and Cyber Physical System in Industry 4.0 Smart Manufacturing. Emergence of Cyber Physical System and IoT in Smart Automation and Robotics, 203–217. https://doi.org/10.1007/978-3-030-66222-6_14
- Zhidchenko, V., Handroos, H. (2022). A Method for the Camera-less Remote Surveillance on Hydraulically Actuated Heavy Equipment Using IoT Environment. International Journal of Fluid Power, 23 (03), 363–378. https://doi.org/10.13052/ijfp1439-9776.2335
- Zhou, C., Ding, L. Y. (2017). Safety barrier warning system for underground construction sites using Internet-of-Things technologies. Automation in Construction, 83, 372–389. https://doi.org/10.1016/j.autcon.2017.07.005
- Nanang Kardana, Y. A., Berchmans, H. J., Ali Nandar, C. S., Nasution, H., Hendriana, D. (2020). Fuel Level Monitoring and Security Warning Tools using IoT for Komatsu Excavator PC200-8M0. Proceedings of The Conference on Management and Engineering in Industry, 2 (1), 31–35. https://doi.org/10.33555/cmei.v2i1.41
- Nazaruddin, N., Adi Sucipto, S. (2018). Modifikasi Excavator Menggunakan Tabung Penyimpan Udara Bertekanan (Pressure Vessel) Sebagai Media Edukasi. J. Online Mhs. Univ. Riau., 5 (2). Available at: https://www.researchgate.net/publication/341852828_MODIFIKASI_EXCAVATOR_MENGGUNAKAN_TABUNG_PENYIMPAN_UDARA_BERTEKANAN_PRESSURE_VESSEL_SEBAGAI_MEDIA_EDUKASI
- Zhang, J., Jiao, S., Liao, X., Yin, P., Wang, Y., Si, K. et al. (2010). Design of Intelligent Hydraulic Excavator Control System Based on PID Method. Computer and Computing Technologies in Agriculture III, 207–215. https://doi.org/10.1007/978-3-642-12220-0_31
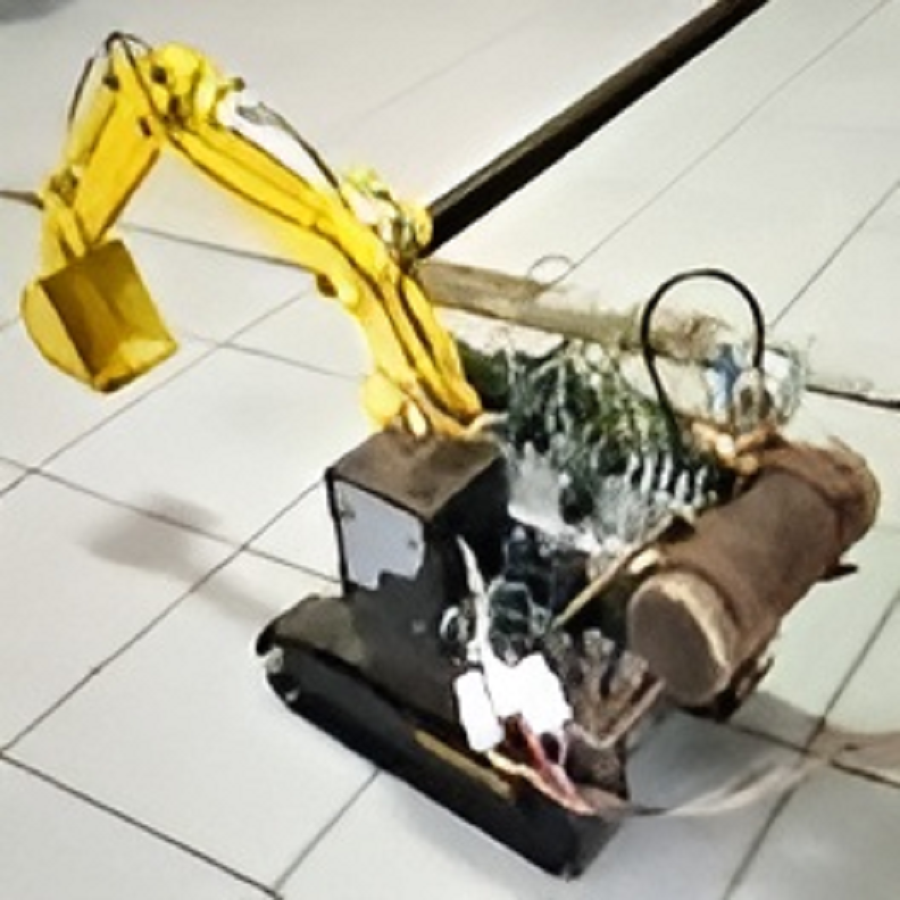
Downloads
Published
How to Cite
Issue
Section
License
Copyright (c) 2024 Nazaruddin Nazaruddin, Feblil Huda, Herisiswanto Herisiswanto, Efi Afrizal, Fajar Bayulesmana

This work is licensed under a Creative Commons Attribution 4.0 International License.
The consolidation and conditions for the transfer of copyright (identification of authorship) is carried out in the License Agreement. In particular, the authors reserve the right to the authorship of their manuscript and transfer the first publication of this work to the journal under the terms of the Creative Commons CC BY license. At the same time, they have the right to conclude on their own additional agreements concerning the non-exclusive distribution of the work in the form in which it was published by this journal, but provided that the link to the first publication of the article in this journal is preserved.
A license agreement is a document in which the author warrants that he/she owns all copyright for the work (manuscript, article, etc.).
The authors, signing the License Agreement with TECHNOLOGY CENTER PC, have all rights to the further use of their work, provided that they link to our edition in which the work was published.
According to the terms of the License Agreement, the Publisher TECHNOLOGY CENTER PC does not take away your copyrights and receives permission from the authors to use and dissemination of the publication through the world's scientific resources (own electronic resources, scientometric databases, repositories, libraries, etc.).
In the absence of a signed License Agreement or in the absence of this agreement of identifiers allowing to identify the identity of the author, the editors have no right to work with the manuscript.
It is important to remember that there is another type of agreement between authors and publishers – when copyright is transferred from the authors to the publisher. In this case, the authors lose ownership of their work and may not use it in any way.