Development of a compact forage harvester equipped with a stem length orienter and rectangular deflector for small farms
DOI:
https://doi.org/10.15587/1729-4061.2024.312154Keywords:
forage harvester, rectangular deflector, mass ejection range, orienter, alfalfaAbstract
The object of the study is the technological processes of high-quality crushing of stem feeds, due to the oriented feeding of stems into the grinding chamber and transportation of the crushed mass through a rectangular deflector.
A review of the literature sources has shown that at present, the design and technological scheme of a small-sized forage harvester has not yet been developed, which in turn ensures high-quality crushing of stem feeds and reduces operating costs in small farms.
As a result of theoretical studies, analytical expressions were obtained to determine the mass velocity at the deflector outlet and the range of mass ejection in the horizontal section.
The combine productivity when mowing alfalfa was equal to 6.22 t/h, the range of mass ejection in the horizontal direction was within 7.5...8.0 m (theoretical value – 7.8 m), the average size of crushed particles was 32.89 mm (estimated length – 33.5 mm), the difference between theoretical and actual values is 1.5 %.
The results of laboratory and field tests showed the efficiency of the forage harvester, the reliability of the analytical expressions obtained and the efficiency of the stem length orienter was determined. A distinctive feature of the research results is that a design and technological scheme of a small-sized forage harvester equipped with an orienter and a theoretical description of the feed transportation process through a rectangular deflector were developed.
According to the presented design and technological scheme, the deflector and orienter have a simplified design and good quality of crushing stem feeds. All this proves the practical significance and applicability of the developed forage harvester
References
- Pilyugin, K. A., Ishutko, A. S., Demchuk, E. V. (2017). Feeding and grinding apparatuses of forage harvesters. New Science: experience, traditions, innovations, 1-2 (123), 245–248.
- Kandel, M. V., Kandel, N. M., Zemlyak, V. L., Bumbar, I. V. (2019). Combine for harvesting corn for silage. Dalnevostochny agrarny vestnik, 2 (50), 93–98.
- Faritov, T. A. (2010). Resource-saving technologies of production, storage and use of fodder. Agrarny vestnik Urala, 3 (69), 43–45.
- Koprivica, R., Veljkovic, B., Radivojevic, D., Stanimirovic, N., Topisirovic, G., Djokic, D. (2012). Production of grass silage by direct mowing using Corner Machinery-1300 forage harvester. African Journal of Agricultural Research, 7 (40), 54–59.
- Amiama, C., Bueno, J., Álvarez, C. J. (2008). Influence of the physical parameters of fields and of crop yield on the effective field capacity of a self-propelled forage harvester. Biosystems Engineering, 100 (2), 198–205. https://doi.org/10.1016/j.biosystemseng.2008.03.004
- Zhang, M., Sword, M. L., Buckmaster, D. R., Cauffman, G. R. (2003). Design and evaluation of a corn silage harvester using shredding and flail cutting. Transactions of the ASAE, 46 (6), 1503–1511. https://doi.org/10.13031/2013.15633
- Savoie, P., Lemire, P., Thériault, R. (2002). Evaluation of five sensors to estimate mass-flow rate and moisture of grass in a forage harvester. Applied Engineering in Agriculture, 18 (4). https://doi.org/10.13031/2013.8751
- Kuzmenko, V., Maksimenko, V., Yampolsky, S. (2017). Experimental substantiation of the parameters of the mass accelerator of the forage harvester. Collection of scientific works of the Scientific and Practical Center of the National Academy of Sciences of Belarus for Agricultural Mechanization. Mechanization and electrification of agriculture, 51, 194–199.
- Maryina, A. M. (2007). Increasing the efficiency of the process of loading vehicles by a forage harvester by optimizing the design and mode parameters of the deflector. Saratov, 21.
- Iskakov, R., Sugirbay, A. (2023). Technologies for the Rational Use of Animal Waste: A Review. Sustainability, 15 (3), 2278. https://doi.org/10.3390/su15032278
- Abilzhanuly, T., Iskakov, R., Abilzhanov, D., Darkhan, O. (2023). Determination of the average size of preliminary grinded wet feed particles in hammer grinders. Eastern-European Journal of Enterprise Technologies, 1 (1 (121)), 34–43. https://doi.org/10.15587/1729-4061.2023.268519
- Abilzhanuly, T., Abilzhanov, D., Khamitov, N., Iskakov, R., Orazakhyn, D., Naidenko, E. (2023). Justification for the speed of a knife and blade depending on the range of the ejectable mass through the deflector of a forage harvester. Izdenister Natigeler, 3 (99), 345–355. https://doi.org/10.37884/3-2023/35
- Abilzhanuly, T., Iskakov, R., Issenov, S., Kubentaeva, G., Mamyrbayeva, I., Abilzhanov, D. et al. (2023). Development of a layer leveling technology that reduces the energy intensity of the processes of mixing and drying the fodder mass. Eastern-European Journal of Enterprise Technologies, 4 (7 (124)), 106–115. https://doi.org/10.15587/1729-4061.2023.286325
- Abilzhanuly, T., Iskakov, R., Abilzhanov, D., Gulyarenko, A., Khan, V. (2024). Justification of parameters of impact-spreading finger shaft for grinder-mixer-dryer using the example of eggshells. Eastern-European Journal of Enterprise Technologies, 3 (1 (129)), 33–44. https://doi.org/10.15587/1729-4061.2024.304127
- Self-propelled forage harvester KSK-600 “Palesse FS60”. Available at: https://souzbelagro.ru/kombajn-kormouborochnyj-samohodnyj-ksk-600-palesse-fs60
- Independent tests of forage harvester. Available at: http://vfermer.ru/rubrics/tehnika/tehnika_1451.html
- Belov, M. I. (2019). The Method of Calculating Cut Length for Flail and Double Chop Forage Harvesters. Engineering Technologies and Systems, 29 (2), 279–294. https://doi.org/10.15507/2658-4123.029.201902.279-294
- Wang, J., Wang, X., Li, H., Lu, C., He, J., Wang, Q. et al. (2022). Improvement of Straw Throwing Performance of Harvester Based on Matching Header Width. Agriculture, 12 (9), 1291. https://doi.org/10.3390/agriculture12091291
- Deglaf, A. A., Yavorsky, B. M. (2002). Course of physics. Moscow: “Vysshaya Shkola”, 718.
- Abilzhanuly, T., Iskakov, R., Abilzhanov, D., Gulyarenko, A., Khan, V. (2024). Identifying the influence of the pitch of hammers with cutting edges on the average length of feed crushed in hammer grinders. Engineering Technological Systems, 4 (1 (130)), 69–78. https://doi.org/10.15587/1729-4061.2024.310045
- Bertin, D., Cotabarren, I., Piña, J., Bucalá, V. (2016). Population balance discretization for growth, attrition, aggregation, breakage and nucleation. Computers & Chemical Engineering, 84, 132–150. https://doi.org/10.1016/j.compchemeng.2015.08.011
- Kosilov, N. I., Stoyan, S. V., Kosilov, D. N. (2006). Fodder harvester trailed combine harvester KPK-2,1 “Bulat”. Prospectus of science and technology, 6, 43–44.
- Lisowski, A., Świątek, K., Klonowski, J., Sypuła, M., Chlebowski, J., Nowakowski, T. et al. (2012). Movement of chopped material in the discharge spout of forage harvester with a flywheel chopping unit: Measurements using maize and numerical simulation. Biosystems Engineering, 111 (4), 381–391. https://doi.org/10.1016/j.biosystemseng.2012.01.003
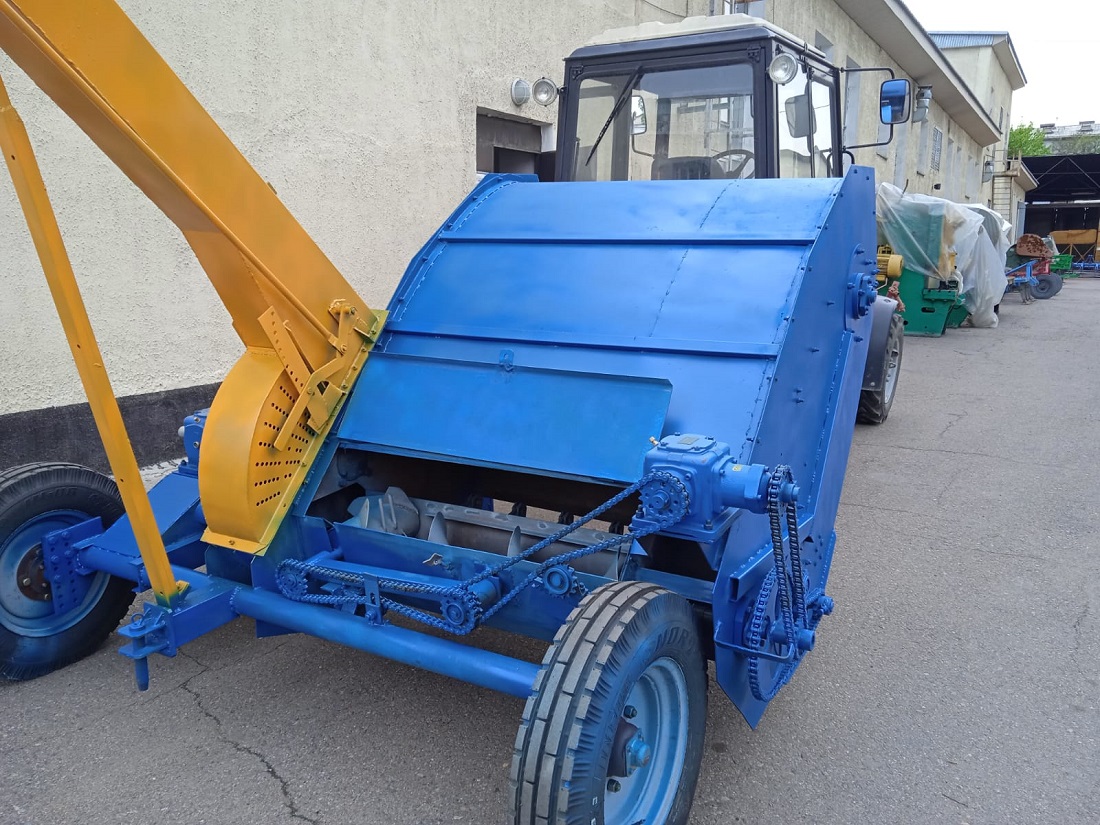
Downloads
Published
How to Cite
Issue
Section
License
Copyright (c) 2024 Tokhtar Abilzhanuly, Serik Nurgozhayev, Daniyar Abilzhanov, Olzhas Seipataliyev, Darkhan Karmanov, Dauren Kosherbay, Ruslan Iskakov, Nurakhet Khamitov

This work is licensed under a Creative Commons Attribution 4.0 International License.
The consolidation and conditions for the transfer of copyright (identification of authorship) is carried out in the License Agreement. In particular, the authors reserve the right to the authorship of their manuscript and transfer the first publication of this work to the journal under the terms of the Creative Commons CC BY license. At the same time, they have the right to conclude on their own additional agreements concerning the non-exclusive distribution of the work in the form in which it was published by this journal, but provided that the link to the first publication of the article in this journal is preserved.
A license agreement is a document in which the author warrants that he/she owns all copyright for the work (manuscript, article, etc.).
The authors, signing the License Agreement with TECHNOLOGY CENTER PC, have all rights to the further use of their work, provided that they link to our edition in which the work was published.
According to the terms of the License Agreement, the Publisher TECHNOLOGY CENTER PC does not take away your copyrights and receives permission from the authors to use and dissemination of the publication through the world's scientific resources (own electronic resources, scientometric databases, repositories, libraries, etc.).
In the absence of a signed License Agreement or in the absence of this agreement of identifiers allowing to identify the identity of the author, the editors have no right to work with the manuscript.
It is important to remember that there is another type of agreement between authors and publishers – when copyright is transferred from the authors to the publisher. In this case, the authors lose ownership of their work and may not use it in any way.