Construction of a mathematical model of turbulent heat and mass transfer processes for the case of electron beam melting of titanium alloy casts
DOI:
https://doi.org/10.15587/1729-4061.2024.312561Keywords:
electron beam melting, titanium alloys, mathematical model, heat transfer, mass transfer, technological modesAbstract
This paper describes a mathematical model built for turbulent heat and mass transfer processes in the case of electron beam melting of titanium alloy ingots. The object of research is the conditions that ensure the quality of ingots. The model makes it possible to calculate the distribution of hydrodynamic flows in the liquid metal and temperature fields in the ingot, to determine the profile of the metal crystallization front, taking into account the interphase transition zones. The model solves the problem of finding the necessary melting regimes of ingots by calculation, in contrast to high-cost natural experiments. The thermal and hydrodynamic processes during the melting of a cylindrical ingot with a diameter of 110 mm of the newest titanium alloy Ti-6Al-7Nb for medical use were calculated and its melting parameters were determined. The small diameter of the ingot significantly facilitates its further machining. The geometry of the two-phase zone of the liquidus-solidus transition, which determines the crystallization front of the metal, was calculated. The position and geometry of this front greatly affects the quality of ingot formation and the concentration of the distribution of alloying elements and the homogeneity of the metal across its volume. A sufficiently flat crystallization front has been obtained, under which the given conditions are ensured. It was found that heat transfer in the liquid phase of the metal is mainly caused by heat and mass transfer due to its movement, and heat and mass transfer significantly depends on the power of the electron beam and its distribution on the surface of the bath. According to the calculated regimes, at the Institute of Electric Welding named after E. O. Paton, the National Academy of Sciences of Ukraine, high-quality ingots for the needs of the medical industry were smelted. The castings are used for the manufacture of light and ultra-strong endoprostheses and implants, which are chemically neutral and biologically and biomechanically compatible with the human body and do not cause rejection.
Supporting Agency
References
- Tamayo, J. A., Riascos, M., Vargas, C. A., Baena, L. M. (2021). Additive manufacturing of Ti6Al4V alloy via electron beam melting for the development of implants for the biomedical industry. Heliyon, 7 (5), e06892. https://doi.org/10.1016/j.heliyon.2021.e06892
- Mahlobo, M. G. R., Chikosha, L., Olubambi, P. A. (2022). Study of the corrosion properties of powder rolled Ti–6Al–4V alloy applied in the biomedical implants. Journal of Materials Research and Technology, 18, 3631–3639. https://doi.org/10.1016/j.jmrt.2022.04.004
- Fellah, M., Labaïz, M., Assala, O., Dekhil, L., Taleb, A., Rezag, H., Iost, A. (2014). Tribological behavior of Ti-6Al-4V and Ti-6Al-7Nb Alloys for Total Hip Prosthesis. Advances in Tribology, 2014, 1–13. https://doi.org/10.1155/2014/451387
- Bartha, K., Zháňal, P., Stráský, J., Čížek, J., Dopita, M., Lukáč, F., Harcuba, P. et al. (2019). Lattice defects in severely deformed biomedical Ti-6Al-7Nb alloy and thermal stability of its ultra-fine grained microstructure. Journal of Alloys and Compounds, 788, 881–890. https://doi.org/10.1016/j.jallcom.2019.02.173
- Bolzoni, L., Ruiz-Navas, E. M., Gordo, E. (2017). Evaluation of the mechanical properties of powder metallurgy Ti-6Al-7Nb alloy. Journal of the Mechanical Behavior of Biomedical Materials, 67, 110–116. https://doi.org/10.1016/j.jmbbm.2016.12.005
- Sun, Y., Huang, B., Puleo, D. A., Schoop, J., Jawahir, I. S. (2016). Improved Surface Integrity from Cryogenic Machining of Ti-6Al-7Nb Alloy for Biomedical Applications. Procedia CIRP, 45, 63–66. https://doi.org/10.1016/j.procir.2016.02.362
- Wei, G., Tan, M., Attarilar, S., Li, J., Uglov, V. V., Wang, B. et al. (2023). An overview of surface modification, A way toward fabrication of nascent biomedical Ti–6Al–4V alloys. Journal of Materials Research and Technology, 24, 5896–5921. https://doi.org/10.1016/j.jmrt.2023.04.046
- Oktikawati, A., Riastuti, R., Damisih, D., Nyoman Jujur, I., Paul Setiawan Kaban, A. (2024). Electrochemical characteristic and microstructure of Ti-6Al-7Nb alloy by centrifugal casting for orthopedic implant based on ageing time variations. Eastern-European Journal of Enterprise Technologies, 2 (12 (128)), 6–15. https://doi.org/10.15587/1729-4061.2024.302614
- Hussain, S. A., Panchal, M., Allamraju, K. V., Rajak, U., Verma, T. N., Brindhadevi, K. (2023). Optimization of wear behavior of heat-treated Ti-6Al-7Nb biomedical alloy by response surface methodology. Environmental Research, 231, 116193. https://doi.org/10.1016/j.envres.2023.116193
- Biswal, S., Tripathy, S., Tripathy, D. K. (2024). Optimisation of PMEDM process parameters for Ti-6Al-7Nb biomedical material. Materials Today: Proceedings. https://doi.org/10.1016/j.matpr.2024.02.044
- Cabrini, M., Carrozza, A., Lorenzi, S., Pastore, T., Testa, C., Manfredi, D. et al. (2022). Influence of surface finishing and heat treatments on the corrosion resistance of LPBF-produced Ti-6Al-4V alloy for biomedical applications. Journal of Materials Processing Technology, 308, 117730. https://doi.org/10.1016/j.jmatprotec.2022.117730
- Xu, X., Li, J., Dong, Z., Zeng, L., Xu, Z., Li, J. (2022). Multiphase modelling of the continuous metallurgical purification process for impurity removing of recycled aluminum. Journal of Materials Research and Technology, 18, 830–840. https://doi.org/10.1016/j.jmrt.2022.03.003
- Hatič, V., Mavrič, B., Šarler, B. (2020). Simulation of macrosegregation in direct-chill casting – A model based on meshless diffuse approximate method. Engineering Analysis with Boundary Elements, 113, 191–203. https://doi.org/10.1016/j.enganabound.2019.12.006
- Luo, Y., Zhang, Z. (2019). Numerical modeling of annular electromagnetic stirring with intercooling in direct chill casting of 7005 aluminum alloy billet. Progress in Natural Science: Materials International, 29 (1), 81–87. https://doi.org/10.1016/j.pnsc.2019.01.007
- Begum, L. (2013). 3-D Transport Phenomena in Vertical Direct. Chill Casting Processes. Montreal, 279.
- Ufodike, C. O., Nzebuka, G. C., Egole, C. P. (2023). Prediction of Limiting Casting Speed in a Horizontal Direct-Chill Casting through Numerical Modeling and Simulation. Metals, 13 (6), 1071. https://doi.org/10.3390/met13061071
- Pardeshi, R. (2016). Computational model for multi alloy casting of aluminum rolling ingots. Journal of Manufacturing Processes, 21, 23–29. https://doi.org/10.1016/j.jmapro.2015.10.006
- Ludwig, A., Rodrigues, C. M. G., Zhang, Z., Zhang, H., Karimi-Sibaki, E., Barati, H. et al. (2021). Important Key Process Simulations in the Field of Steel Metallurgy. BHM Berg- Und Hüttenmännische Monatshefte, 167 (1), 2–9. https://doi.org/10.1007/s00501-021-01184-1
- Haag, J., Martens, J., Dussoubs, B., Jardy, A., Bellot, J.-P. (2020). Analysis of the Thermal Transfers in a VASM Crucible: Electron Beam Melting Experiment and Numerical Simulation. Metals, 10 (9), 1152. https://doi.org/10.3390/met10091152
- El Idi, M. M., Karkri, M. (2020). Melting and solidification behavior of PCM embedded in metal foam. COMSOL Conference 2020 Europe. Available at: https://hal.science/hal-02966782
- Moench, S., Dittrich, R. (2022). Influence of Natural Convection and Volume Change on Numerical Simulation of Phase Change Materials for Latent Heat Storage. Energies, 15 (8), 2746. https://doi.org/10.3390/en15082746
- Akhonin, S. V., Gorislavets, Yu. M., Glukhenkiy, A. I., Berezos, V. A., Bondar, A. I., Pikulin, A. N. (2019). Modeling Hydrodynamic And Thermal Processes In The Mould In Cold-hearth Electron Beam Melting. Sovremennaâ Èlektrometallurgiâ, 2019 (4), 9–17. https://doi.org/10.15407/sem2019.04.02
- Akhonin, S. V., Berezos, V. O., Bondar, O. I., Glukhenkii, O. I., Goryslavets, Yu. M., Severin, A. Yu. (2021). Mathematical modeling of hydrodynamic and thermal processes at crystallization of titanium ingots produced by EBM. Sovremennaâ Èlektrometallurgiâ, 2021 (1), 27–34. https://doi.org/10.37434/sem2021.01.03
- Rubinetti, D., Weiss, D. A., Chaudhuri, A., Kraniotis, D. (2018). Modeling Approach to Facilitate Thermal Energy Management with Phase Change Materials (PCM). COMSOL Conference. Available at: https://www.comsol.com/paper/modeling-approach-to-facilitate-thermal-energy-management-with-phase-change-mate-63481
- Heat Transfer Module User’s Guide. Available at: https://doc.comsol.com/5.4/doc/com.comsol.help.heat/HeatTransferModuleUsersGuide.pdf
- Panton, R. L. (2013). Incompressible Flow. John Wiley & Sons. https://doi.org/10.1002/9781118713075
- Civan, F., Sliepcevich, C. M. (1987). Limitation in the Apparent Heat Capacity Formulation for Heat Transfer With Phase Change. Available at: https://citeseerx.ist.psu.edu/document?repid=rep1&type=pdf&doi=a164ded6feb6d03531c1b0b43b8ab8f45b0cf747
- Zhu, Z., Zhou, R., Li, X., Xiong, W., Li, Z. (2022). Flow Field and Inclusions Movement in the Cold Hearth for the Ti-0.3Mo-0.8Ni Alloy. Crystals, 12 (10), 1471. https://doi.org/10.3390/cryst12101471
- Lacasse, D., Turgeon, É., Pelletier, D. (2004). On the judicious use of the k–ε model, wall functions and adaptivity. International Journal of Thermal Sciences, 43(10), 925–938. https://doi.org/10.1016/j.ijthermalsci.2004.03.004
- Weigand, B., Ferguson, J. R., Crawford, M. E. (1997). An extended Kays and Crawford turbulent Prandtl number model. International Journal of Heat and Mass Transfer, 40 (17), 4191–4196. https://doi.org/10.1016/s0017-9310(97)00084-7
- Kays W. M., Crawford M. E. (1993). Convective Heat and Mass Transfer. McGraw-Hill Science/Engineering/Math, 480.
- Kays, W., Crawford, M., Weigand, B. (2005). Convective Heat and Mass Transfer. McGraw-Hill.
- Jischa, M., Rieke, H. B. (1979). About the prediction of turbulent prandtl and schmidt numbers from modeled transport equations. International Journal of Heat and Mass Transfer, 22 (11), 1547–1555. https://doi.org/10.1016/0017-9310(79)90134-0
- Fuchs, H. (1973). Wärmeübergang an strömendes Natrium. Würenlingen, 257.
- Launder, B. E., Spalding, D. B. (1974). The numerical computation of turbulent flows. Computer Methods in Applied Mechanics and Engineering, 3 (2), 269–289. https://doi.org/10.1016/0045-7825(74)90029-2
- Versteeg, H. K., Malalasekera, W. (2007). An Introduction to Computational Fluid Dynamics: The Finite Volume Method. Pearson Education.
- Arpaci, V., Larsen, P. (1984). Convection Heat Transfer. Prentice Hall, 512.
- Bushok, H .F., Venher, Ye. F. (2002). Fizychni osnovy mekhaniky. Molekuliarna fizyka i termodynamika. Knyha 1. Kyiv: Vyshcha shkola, 375.
- Truong, V.-D., Hyun, Y.-T., Won, J. W., Lee, W., Yoon, J. (2022). Numerical Simulation of the Effects of Scanning Strategies on the Aluminum Evaporation of Titanium Alloy in the Electron Beam Cold Hearth Melting Process. Materials, 15 (3), 820. https://doi.org/10.3390/ma15030820
- Nogovicyn, A. V., Podol'cev, A. D., Kucheryavaya, I. N. (2015). CHislennoe modelirovanie gidrodinamicheskih i teplovyh processov pri nepreryvnoj dvuhvalkovoj razlivke stali. Metall i lit'e Ukrainy, 3 (262), 15–20.
- Nogovicyn, A. V., Podol'cev, A. D., Kucheryavaya, I. N. (2016). Turbulentnyj gidrodinamicheskij i teplovoj processy pri dvuhvalkovoj razlivke stali (trekhmernoe komp'yuternoe modelirovanie). Processy lit'ya, 2 (116), 23–34.
- Yao, L., Maijer, D. M., Cockcroft, S. L., Fiore, D., Tripp, D. W. (2018). Quantification of heat transfer phenomena within the melt pool during the plasma arc re-melting of titanium alloys. International Journal of Heat and Mass Transfer, 126, 1123–1133. https://doi.org/10.1016/j.ijheatmasstransfer.2018.06.051
- Belyaev, N. M. (1989). Osnovy teploperedachi. Kyiv, 343.
- Wilcox, D.C. (2006). Turbulence modeling for CFD. California: DCW Industries Inc., 515.
- Pope, S. B. (2000). Turbulent Flow. Cambridge University Press, 771.
- Launder, B. E., Sharma, B. I. (1974). Application of the energy-dissipation model of turbulence to the calculation of flow near a spinning disc. Letters in Heat and Mass Transfer, 1(2), 131–137. https://doi.org/10.1016/0094-4548(74)90150-7
- Jones, W. P., Launder, B. E. (1972). The prediction of laminarization with a two-equation model of turbulence. International Journal of Heat and Mass Transfer, 15(2), 301–314. https://doi.org/10.1016/0017-9310(72)90076-2
- Launder, B .E., Spalding, D. B. (1972). Mathematical Models of Turbulence. New York: Academic Press, 169.
- Baraniuk, O. V., Vorobiov, M. V., Rachynskyi, A. Yu. (2023). CFD-modeliuvannia protsesiv teploobminu i hidrodynamiky zasobamy prohramnoho kompleksu. Kyiv: Politekhnika, 164.
- Larsson, J. (1998). Numerical Simulation of Turbulent Flows for Turbine Blade Heat Transfer Applications. Gothenburg: Chalmers University of Technology, 57.
- Avnaim, M. H., Levy, A., Mikhailovich, B., Ben-David, O., Azulay, A. (2016). Comparison of Three-Dimensional Multidomain and Single-Domain Models for the Horizontal Solidification Problem. Journal of Heat Transfer, 138 (11). https://doi.org/10.1115/1.4033700
- Ben-David, O., Levy, A., Mikhailovich, B., Azulay, A. (2013). 3D numerical and experimental study of gallium melting in a rectangular container. International Journal of Heat and Mass Transfer, 67, 260–271. https://doi.org/10.1016/j.ijheatmasstransfer.2013.07.058
- Mizukami, H., Funagane, H., Kitaura, T., Takeda, Y., Wada, M., Shirai, Y., Umeda, S. (2022). Removal Technology of Inclusion from Titanium Alloy Melt in Hearth. Nippon Steel Technical Report.
- Boettinger, W. J., Warren, J. A., Beckermann, C., Karma, A. (2002). Phase-Field Simulation of Solidification. Annual Review of Materials Research, 32 (1), 163–194. https://doi.org/10.1146/annurev.matsci.32.101901.155803
- Akhonin, S., Pikulin, O., Berezos, V., Severyn, A., Erokhin, O., Kryzhanovskyi, V. (2022). Determining the structure and properties of heat-resistant titanium alloys VT3-1 and VT9 obtained by electron-beam melting. Eastern-European Journal of Enterprise Technologies, 5 (12 (119)), 6–12. https://doi.org/10.15587/1729-4061.2022.265014
- Akhonin, S. V., Pikulin, O. M. (2019). Investigation of Effect of Electron Beam Surface Treatment of Titanium Alloy Ingots on Structure and Properties of Melted Metal. IOP Conference Series: Materials Science and Engineering, 582 (1), 012047. https://doi.org/10.1088/1757-899x/582/1/012047
- Berezos, V. O., Akhonin, D. S. (2023). Electron beam melting of titanium alloys for medical purposes. The Paton Welding Journal, 2023 (6), 41–48. https://doi.org/10.37434/tpwj2023.06.06
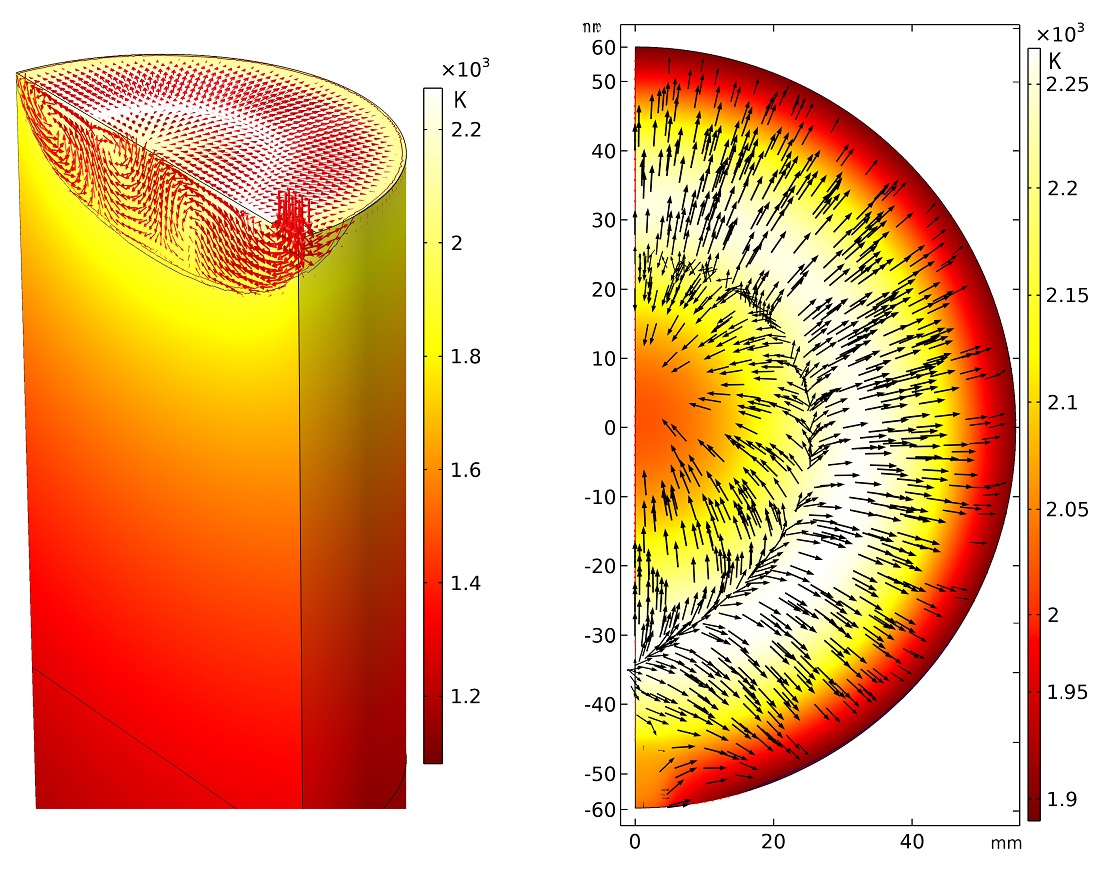
Downloads
Published
How to Cite
Issue
Section
License
Copyright (c) 2024 Serhii Rymar, Igor Krivtsun, Ruslan Hubatiuk, Volodymyr Berezos, Dmytro Akhonin

This work is licensed under a Creative Commons Attribution 4.0 International License.
The consolidation and conditions for the transfer of copyright (identification of authorship) is carried out in the License Agreement. In particular, the authors reserve the right to the authorship of their manuscript and transfer the first publication of this work to the journal under the terms of the Creative Commons CC BY license. At the same time, they have the right to conclude on their own additional agreements concerning the non-exclusive distribution of the work in the form in which it was published by this journal, but provided that the link to the first publication of the article in this journal is preserved.
A license agreement is a document in which the author warrants that he/she owns all copyright for the work (manuscript, article, etc.).
The authors, signing the License Agreement with TECHNOLOGY CENTER PC, have all rights to the further use of their work, provided that they link to our edition in which the work was published.
According to the terms of the License Agreement, the Publisher TECHNOLOGY CENTER PC does not take away your copyrights and receives permission from the authors to use and dissemination of the publication through the world's scientific resources (own electronic resources, scientometric databases, repositories, libraries, etc.).
In the absence of a signed License Agreement or in the absence of this agreement of identifiers allowing to identify the identity of the author, the editors have no right to work with the manuscript.
It is important to remember that there is another type of agreement between authors and publishers – when copyright is transferred from the authors to the publisher. In this case, the authors lose ownership of their work and may not use it in any way.