Identification of the electric motor mathematical model based on a data sample with feature engineering
DOI:
https://doi.org/10.15587/1729-4061.2024.312610Keywords:
mathematical model of a synchronous electric motor, mathematical model identification, mutual information, correlation analysis of electric motor operating parameters, artificial feature engineeringAbstract
The object of this study is a mathematical model of a synchronous electric motor, obtained on the basis of experimental data, which takes into account the temperature mode and uses artificial features to increase the accuracy of its operation. A characteristic feature of this work is that the model takes into account the temperature mode as a component of the technical-operational state of the object. The resulting mathematical model could make it possible to synthesize an optimal automatic control system in terms of the operational state of the object.
The problem addressed was to increase the accuracy of the identified mathematical models by applying the approach of feature engineering.
The results showed that the identification of mathematical models by the initial data leads to a low level of accuracy of the obtained models, namely 65–70 % for the first output channel, 80–85 % for the second, and 75–80 % for the third, fourth, and fifth output channels.
Accordingly, building models with a higher threshold of accuracy requires the use of other, more significant data for identification. This paper reports a method for reformatting the original data into artificial features and provides results of their effectiveness in relation to the original channels.
The resulting artificial features and the original features were used for further identification; the resulting mathematical model has on average higher accuracy thresholds, namely 82 %, 93 %, 88 %, 85 % for the corresponding output channels. The results prove the effectiveness of applying the principle of feature engineering since the accuracy of the resulting model is 5–10 % higher compared to the baseline.
The scope of practical application of the results includes the synthesis of automatic control systems based on mathematical models of control objects obtained as a result of identification.
References
- Drif, M., Cardoso, A. J. M. (2014). Stator Fault Diagnostics in Squirrel Cage Three-Phase Induction Motor Drives Using the Instantaneous Active and Reactive Power Signature Analyses. IEEE Transactions on Industrial Informatics, 10 (2), 1348–1360. https://doi.org/10.1109/tii.2014.2307013
- Trzynadlowski, A. M. (2001). Construction and steady-state operation of induction motors. Control of Induction Motors, 15–41. https://doi.org/10.1016/b978-012701510-1/50002-7
- Lindegger, M. (2009). Economic viability, applications and limits of efficient permanent magnet motors. Switzerland: Swiss Federal Office of Energy.
- Zhang, M., Tang, J., Zhang, X., Zhang, J. (2016). Intelligent diagnosis of short hydraulic signal based on improved EEMD and SVM with few low-dimensional training samples. Chinese Journal of Mechanical Engineering, 29 (2), 396–405. https://doi.org/10.3901/cjme.2015.1214.147
- Matić, D., Kulić, F., Pineda-Sánchez, M., Kamenko, I. (2012). Support vector machine classifier for diagnosis in electrical machines: Application to broken bar. Expert Systems with Applications, 39 (10), 8681–8689. https://doi.org/10.1016/j.eswa.2012.01.214
- Lei, Y., Jia, F., Lin, J., Xing, S., Ding, S. X. (2016). An Intelligent Fault Diagnosis Method Using Unsupervised Feature Learning Towards Mechanical Big Data. IEEE Transactions on Industrial Electronics, 63 (5), 3137–3147. https://doi.org/10.1109/tie.2016.2519325
- Boukra, T., Lebaroud, A., Clerc, G. (2013). Statistical and Neural-Network Approaches for the Classification of Induction Machine Faults Using the Ambiguity Plane Representation. IEEE Transactions on Industrial Electronics, 60 (9), 4034–4042. https://doi.org/10.1109/tie.2012.2216242
- Wang, J., Gao, R. X., Yan, R. (2014). Multi-scale enveloping order spectrogram for rotating machine health diagnosis. Mechanical Systems and Signal Processing, 46 (1), 28–44. https://doi.org/10.1016/j.ymssp.2013.06.001
- Boashash, B. (2015). Time-frequency signal analysis and processing: A comprehensive reference. Academic Press.
- Electric Motor Temperature. Available at: https://www.kaggle.com/wkirgsn/electric-motor-temperature
- Korotynskyi, A., Zhuchenko, O. (2020). A system of automated control for the baking process that minimizes the probability of defects. Eastern-European Journal of Enterprise Technologies, 1(2 (103)), 58–67. https://doi.org/10.15587/1729-4061.2020.195785
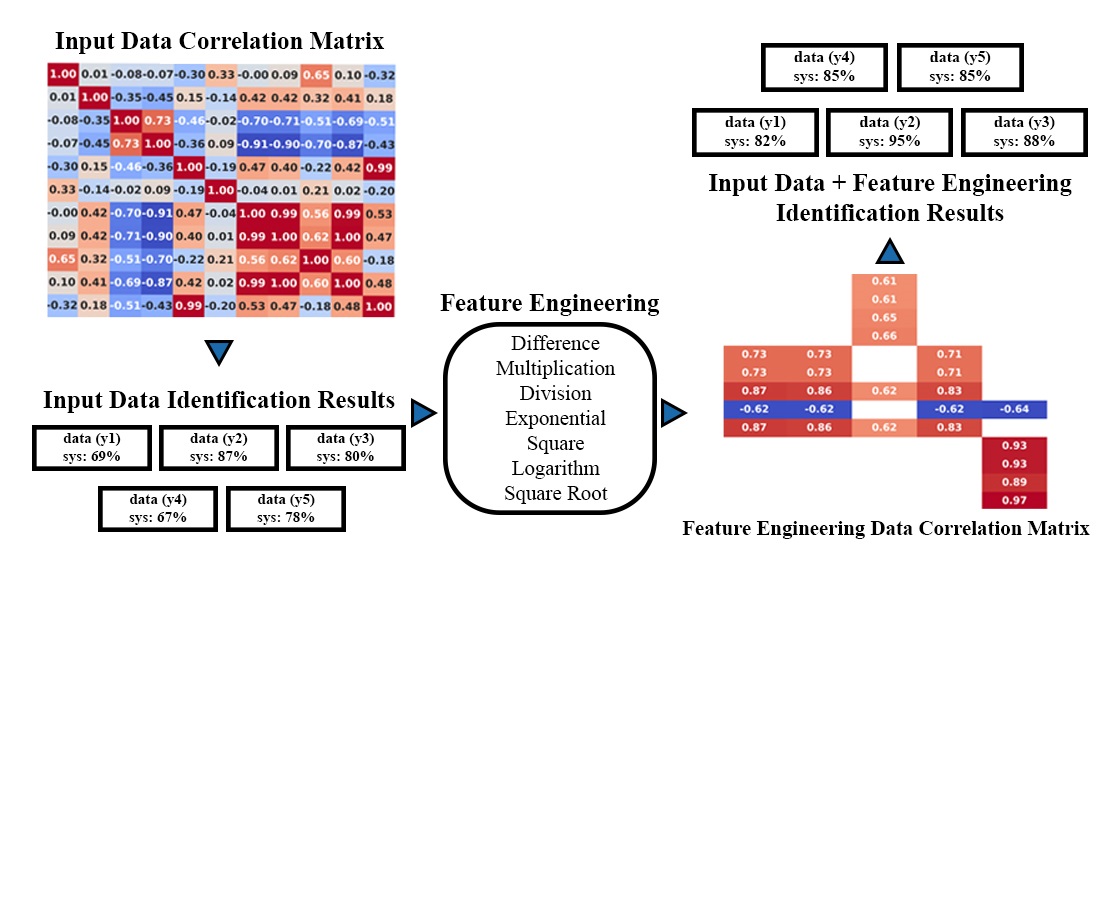
Downloads
Published
How to Cite
Issue
Section
License
Copyright (c) 2024 Anton Korotynskyi, Liudmyla Zhuchenko, Vitalii Tsapar, Andrii Savula

This work is licensed under a Creative Commons Attribution 4.0 International License.
The consolidation and conditions for the transfer of copyright (identification of authorship) is carried out in the License Agreement. In particular, the authors reserve the right to the authorship of their manuscript and transfer the first publication of this work to the journal under the terms of the Creative Commons CC BY license. At the same time, they have the right to conclude on their own additional agreements concerning the non-exclusive distribution of the work in the form in which it was published by this journal, but provided that the link to the first publication of the article in this journal is preserved.
A license agreement is a document in which the author warrants that he/she owns all copyright for the work (manuscript, article, etc.).
The authors, signing the License Agreement with TECHNOLOGY CENTER PC, have all rights to the further use of their work, provided that they link to our edition in which the work was published.
According to the terms of the License Agreement, the Publisher TECHNOLOGY CENTER PC does not take away your copyrights and receives permission from the authors to use and dissemination of the publication through the world's scientific resources (own electronic resources, scientometric databases, repositories, libraries, etc.).
In the absence of a signed License Agreement or in the absence of this agreement of identifiers allowing to identify the identity of the author, the editors have no right to work with the manuscript.
It is important to remember that there is another type of agreement between authors and publishers – when copyright is transferred from the authors to the publisher. In this case, the authors lose ownership of their work and may not use it in any way.