Determination of processing conditions for a heat-resistant superalloy used in turbine elements
DOI:
https://doi.org/10.15587/1729-4061.2024.313452Keywords:
turbine elements, electrochemical dissolution, methanesulfonic acid, hydrochloric acid, sodium chloride, sulfuric acidAbstract
A heat-resistant superalloy from destroyed special equipment was used for further processing to extract valuable metals such as rhenium, nickel, cobalt, tungsten, molybdenum, niobium, tantalum, and others. The need to develop an effective method for the electrochemical dissolution of this superalloy is due to the shortage and high cost of the component metals, especially rhenium. The electrochemical dissolution method is effective for the rapid and complete dissolution of such hard alloys, optimizing the extraction process of valuable components.
In the course of the work, the composition of the unknown superalloy was determined, and the possible grade of the alloy was identified as JS32-VI. For the first time, a comparison of the anodic behavior of the heat-resistant superalloy containing rhenium in various electrolyte solutions, including methanesulfonic acid, was carried out. This comparison helped determine which electrolyte is best suited for dissolving the superalloy and extracting valuable metals from it.
The results showed that solutions containing chloride ions (NaCl and HCl) are the most effective for the electrochemical dissolution of the superalloy. These results are explained by the fact that chloride ions help remove the passive oxide film from the metal surface. Thus, chloride solutions provide more effective dissolution of the superalloy compared to methanesulfonic acid and sulfuric acid.
The key finding of the study is the identification of chloride solutions as the most effective for dissolving the superalloy, which optimizes the process of extracting valuable metals. The application of these methods will contribute to resource conservation and the reduction of production costs, which is important for industries using such materials
References
- Zhang, Y., Zuo, T. T., Tang, Z., Gao, M. C., Dahmen, K. A., Liaw, P. K., Lu, Z. P. (2014). Microstructures and properties of high-entropy alloys. Progress in Materials Science, 61, 1–93. https://doi.org/10.1016/j.pmatsci.2013.10.001
- Jiao, Z., Yang, T. (Eds.) (2022). Advanced Multicomponent Alloys: From Fundamentals to Applications. Springer Singapore. https://doi.org/10.1007/978-981-19-4743-8
- Zhang, W., Huang, L., Mi, X., Xie, H., Feng, X., Ahn, J. H. (2024). Researches for higher electrical conductivity copper‐based materials. CMat, 1 (1). https://doi.org/10.1002/cmt2.13
- Binder Jetting and beyond: Optimising the use of metal powders for additive manufacturing. METAL AM. Available at: https://www.metal-am.com/articles/binder-jetting-and-beyond-optimising-the-use-of-metal-powders-for-additive-manufacturing/
- Economics of Metal Additive Manufacturing. Digital Alloys. Available at: https://www.digitalalloys.com/blog/economics-metal-additive-manufacturing/
- Kovalenko, V., Kotok, V., Vlasov, S. (2018). Development of the electrochemical synthesis method of ultrafine cobalt powder for a superalloy production. Eastern-European Journal of Enterprise Technologies, 2 (6 (92)), 41–47. https://doi.org/10.15587/1729-4061.2018.126928
- Kovalenko, V., Kotok, V., Vlasov, S. (2018). Definition of synthesis parameters of ultrafine nickel powder by direct electrolysis for application in superalloy production. Eastern-European Journal of Enterprise Technologies, 1 (6 (91)), 27–33. https://doi.org/10.15587/1729-4061.2018.121595
- Murakumo, T., Kobayashi, T., Koizumi, Y., Harada, H. (2004). Creep behaviour of Ni-base single-crystal superalloys with various γ′ volume fraction. Acta Materialia, 52 (12), 3737–3744. https://doi.org/10.1016/j.actamat.2004.04.028
- Shen, L., Tesfaye, F., Li, X., Lindberg, D., Taskinen, P. (2021). Review of rhenium extraction and recycling technologies from primary and secondary resources. Minerals Engineering, 161, 106719. https://doi.org/10.1016/j.mineng.2020.106719
- Ganji, D. K., Rajyalakshmi, G. (2020). Influence of Alloying Compositions on the Properties of Nickel-Based Superalloys: A Review. Recent Advances in Mechanical Engineering, 537–555. https://doi.org/10.1007/978-981-15-1071-7_44
- Brainard, J. L. (2023). The availability of primary rhenium as a by-product of copper and molybdenum mining. Mineral Economics, 37 (3), 445–461. https://doi.org/10.1007/s13563-023-00392-0
- Rhenium Prices. Strategic Metals Invest. Available at: https://strategicmetalsinvest.com/rhenium-prices/
- Leszczyńska-Sejda, K., Palmowski, A., Ochmański, M., Benke, G., Grzybek, A., Orda, S. et al. (2024). Recycling of Rhenium from Superalloys and Manganese from Spent Batteries to Produce Manganese(II) Perrhenate Dihydrate. Recycling, 9 (3), 36. https://doi.org/10.3390/recycling9030036
- Srivastava, R. R., Kim, M., Lee, J. (2016). Novel Aqueous Processing of the Reverted Turbine-Blade Superalloy for Rhenium Recovery. Industrial & Engineering Chemistry Research, 55 (29), 8191–8199. https://doi.org/10.1021/acs.iecr.6b00778
- Kovalenko, V., Kotok, V. (2020). Investigation of the anodic behavior of w-based superalloy for electrochemical selective treatment. Eastern-European Journal of Enterprise Technologies, 6 (12 (108)), 55–60. https://doi.org/10.15587/1729-4061.2020.218355
- Xu, D., Zheng, S., Chen, P., Wei, B., Zhang, J., Cheng, J. (2022). Recycling of Rhenium from W–Re-Alloyed Scraps by a Pyrometallurgical Method. Journal of Sustainable Metallurgy, 8 (1), 148–155. https://doi.org/10.1007/s40831-021-00487-4
- Olbrich, A., Meese-Marktscheffel, J., Jahn, M., Zertani, R., Stoller, V., Erb, M., Kutzler, U. (2006). Pat. No. US20090255372A1. Recycling of superalloys with the aid of an alkali metal salt bath. Available at: https://patents.google.com/patent/US20090255372A1/en?oq=12306853
- Ferron, C. G., Seeley, L. E. (2010). Pat. No. US8956582B2. Rhenium recovery. Available at: https://patents.google.com/patent/US8956582B2/en?oq=8956582
- Guo, Z., Gong, Y., Lu, W. (2007). Electrochemical studies of nickel deposition from aqueous solution in super-gravity field. Science in China Series E: Technological Sciences, 50 (1), 39–50. https://doi.org/10.1007/s11431-007-0001-9
- Sunaba, T., Ito, T., Miyata, Y., Asakura, S., Shinohara, T., Yakou, T. et al. (2014). Influence of Chloride Ions on Corrosion of Modified Martensitic Stainless Steels at High Temperatures Under a CO2Environment. CORROSION, 70 (10), 988–999. https://doi.org/10.5006/1141
- Electrolysis. Refining of Copper. Available at: https://science.jrank.org/pages/2353/Electrolysis-Refining-copper.html
- Sknar, Yu. E., Amirulloeva, N. V., Sknar, I. V., Danylov, F. I. (2016). Influence of Methylsulfonate Anions on the Structure of Electrolytic Cobalt Coatings. Materials Science, 52 (3), 396–401. https://doi.org/10.1007/s11003-016-9970-9
- Sknar, I. V., Sknar, Yu. E., Savchuk, О. О., Baskevich, A. S., Kozhura, О., Hrydnieva, T. V. (2020). Electrodeposition of copper from a methanesulphonate electrolyte. Journal of chemistry and technologies, 28 (1), 1–9. https://doi.org/10.15421/082001
- Mikhailov, I. F. (2016). Perspectives of development of X-ray analysis for material composition. Functional Materials, 23 (1), 5–14. https://doi.org/10.15407/fm23.01.005
- ZHS32-VI. Aloro. Available at: https://aloro.org/grades/su/gr-gs32-vi
- Zhang, B., Wang, J., Wu, B., Guo, X. W., Wang, Y. J., Chen, D. et al. (2018). Unmasking chloride attack on the passive film of metals. Nature Communications, 9 (1). https://doi.org/10.1038/s41467-018-04942-x
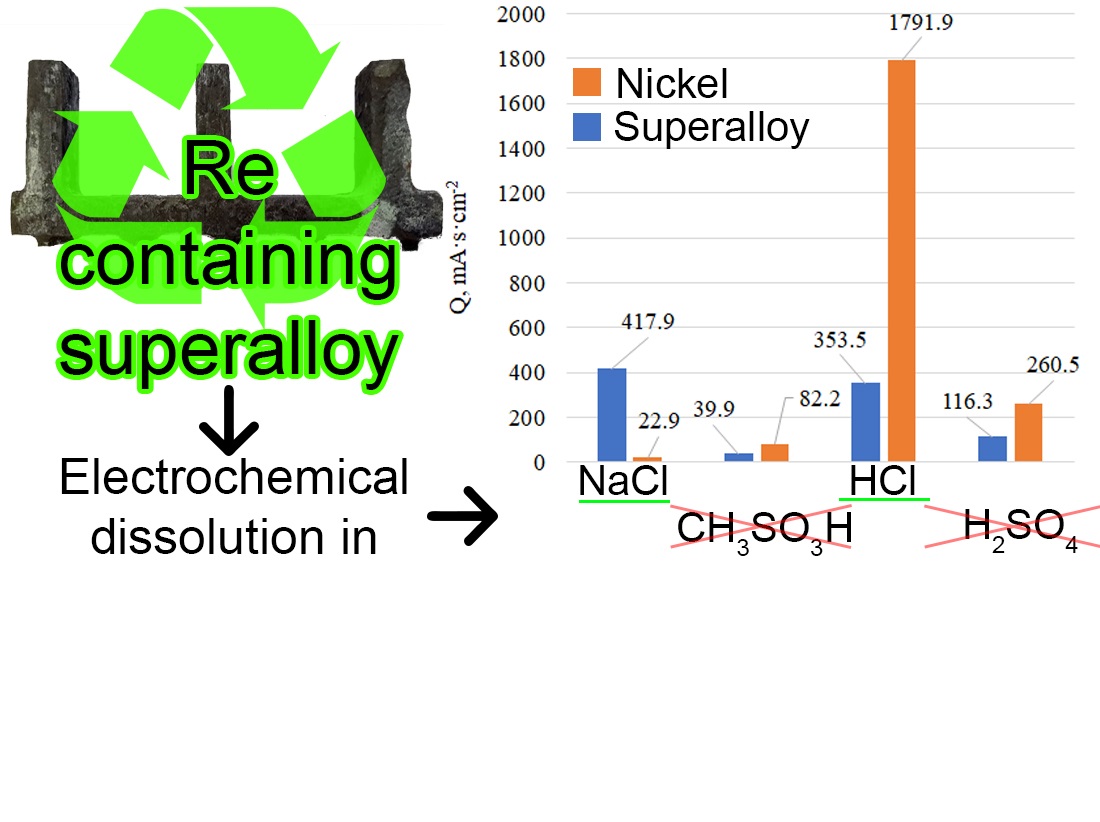
Downloads
Published
How to Cite
Issue
Section
License
Copyright (c) 2024 Valerii Kotok, Tatyana Butyrina, Yuri Sknar, Oksana Demchyshyna, Anna Liashenko, Irina Sukha

This work is licensed under a Creative Commons Attribution 4.0 International License.
The consolidation and conditions for the transfer of copyright (identification of authorship) is carried out in the License Agreement. In particular, the authors reserve the right to the authorship of their manuscript and transfer the first publication of this work to the journal under the terms of the Creative Commons CC BY license. At the same time, they have the right to conclude on their own additional agreements concerning the non-exclusive distribution of the work in the form in which it was published by this journal, but provided that the link to the first publication of the article in this journal is preserved.
A license agreement is a document in which the author warrants that he/she owns all copyright for the work (manuscript, article, etc.).
The authors, signing the License Agreement with TECHNOLOGY CENTER PC, have all rights to the further use of their work, provided that they link to our edition in which the work was published.
According to the terms of the License Agreement, the Publisher TECHNOLOGY CENTER PC does not take away your copyrights and receives permission from the authors to use and dissemination of the publication through the world's scientific resources (own electronic resources, scientometric databases, repositories, libraries, etc.).
In the absence of a signed License Agreement or in the absence of this agreement of identifiers allowing to identify the identity of the author, the editors have no right to work with the manuscript.
It is important to remember that there is another type of agreement between authors and publishers – when copyright is transferred from the authors to the publisher. In this case, the authors lose ownership of their work and may not use it in any way.