Designing optimal geometry of the radius die for broaching cases
DOI:
https://doi.org/10.15587/1729-4061.2024.317060Keywords:
cartridge case, broaching, die, rounding radius, wear, mandrel, stability, broach force, hollow workpiece, FEMAbstract
The object of this study is the technological process of broaching cartridge cases through a radius die on a mandrel. The work is aimed at solving the actual scientific and technical task of improving the technological process of broaching on a mandrel through a die in the manufacture of cartridge-case type forgings, which provides an increase in the stability of broaching dies. The finite element method (FEM) was used to simulate the processes of broaching cartridge cases through the die. As a result, a rational geometry of the radius die has been established. Recommendations for designing new die structures have been devised, which involve determining the rational radius of rounding of the working part of the die. The established recommendations have been verified by experimental studies. The broaching of cartridge cases through a die with a working radius surface should be carried out at relative radius R/d=3.0. In this case, stress intensity decreased by 7...17 %, average compressive stresses decreased by 8...15 %, and normal pressure decreased by 10...15 % compared to smaller rounding radii. The resulting force on the working surface of the die decreased by 40...55 %, and the radial component of this force decreased by 50 %. It was found that the working surface of the die is heated to a temperature of 750...850 °C, but the rounding radius R/d=3.0 provides a reduction in the volume of this zone by 1.5...1.9 times. The resulting relative rounding radius of the die was tested under industrial conditions, which confirmed that the broaching force for this radius is lower by 15...20 %, and the stability of such a die increased by 20 %. It is recommended to use radius dies for broaching high cartridge cases. The results could also be applied at enterprises during the production of dual-purpose parts
References
- Wang, P., Zhu, S., Wang, L., Wu, L., Guan, S. (2015). A two-step superplastic forging forming of semi-continuously cast AZ70 magnesium alloy. Journal of Magnesium and Alloys, 3 (1), 70–75. https://doi.org/10.1016/j.jma.2014.12.004
- Karnaukh, S., Markov, O., Lysenko, A. (2024). Research on the new process of separating hollow work-piece by eccentric torsion cutting for stamping. FME Transactions, 52 (1), 29–36. https://doi.org/10.5937/fme2401029k
- Guan, S. K., Wu, L. H., Wang, P. (2009). Hot forgeability and die-forging forming of semi-continuously cast AZ70 magnesium alloy. Materials Science and Engineering: A, 499 (1-2), 187–191. https://doi.org/10.1016/j.msea.2007.11.136
- Chander, S., Chawla, V. (2017). Failure of Hot Forging Dies –An Updated Perspective. Materials Today: Proceedings, 4 (2), 1147–1157. https://doi.org/10.1016/j.matpr.2017.01.131
- Aliiev, I. S., Levchenko, V. N., Markov, O. E., Kalujniy, A. V., Aliieva, L. I., Sivak, R. I. (2024). Development of devices for measuring contact friction forces in the processes of volumetric plastic deformation. The International Journal of Advanced Manufacturing Technology, 132 (5-6), 2839–2851. https://doi.org/10.1007/s00170-024-13537-4
- Podgrajšek, M., Glodež, S., Ren, Z. (2015). Failure analysis of forging die insert protected with diffusion layer and PVD coating. Surface and Coatings Technology, 276, 521–528. https://doi.org/10.1016/j.surfcoat.2015.06.021
- Ghalehbandi, S. M., Biglari, F. (2020). Predicting damage and failure under thermomechanical fatigue in hot forging tools. Engineering Failure Analysis, 113, 104545. https://doi.org/10.1016/j.engfailanal.2020.104545
- Chen, Q., Geng, H., Zhang, H., Li, X., Chen, G. (2022). Microstructure and mechanical properties of in situ TiB2•TiAl3/2024Al composite subjected to multidirectional forging. Journal of Materials Research and Technology, 21, 2827–2840. https://doi.org/10.1016/j.jmrt.2022.10.098
- Jeong, H. Y., Park, J., Kim, Y., Shin, S. Y., Kim, N. (2023). Processing parameters optimization in hot forging of AISI 4340 steel using instability map and reinforcement learning. Journal of Materials Research and Technology, 23, 1995–2009. https://doi.org/10.1016/j.jmrt.2023.01.106
- Hawryluk, M. (2016). Review of selected methods of increasing the life of forging tools in hot die forging processes. Archives of Civil and Mechanical Engineering, 16 (4), 845–866. https://doi.org/10.1016/j.acme.2016.06.001
- Markov, O., Shevtsov, S., Hrudkina, N., Molodetskyi, V., Musorin, A., Zinskyi, V. (2023). Testing a new technique for producing artillery cartridge cases from pipe workpiece by roughing with a friction tool. Eastern-European Journal of Enterprise Technologies, 6 (1 (126)), 91–97. https://doi.org/10.15587/1729-4061.2023.291881
- Hawryluk, M., Ziemba, J. (2017). Possibilities of application measurement techniques in hot die forging processes. Measurement, 110, 284–295. https://doi.org/10.1016/j.measurement.2017.07.003
- Shen, L., Zhou, J., Xiong, Y.-B., Zhang, J.-S., Meng, Y. (2018). Analysis of service condition of large hot forging die and refabrication of die by bimetal-layer weld surfacing technology with a cobalt-based superalloy and a ferrous alloy. Journal of Manufacturing Processes, 31, 731–743. https://doi.org/10.1016/j.jmapro.2018.01.005
- Soranansri, P., Yanil, S., Sirivedin, K. (2019). Finite Element Modeling of Shrink-Fit Design for Improvement of Die-Service Life in Hot Forging Process of a Bevel Gear. Materials Today: Proceedings, 17, 1711–1719. https://doi.org/10.1016/j.matpr.2019.06.202
- Tanrıkulu, B., Karakuzu, R. (2020). Fatigue life prediction model of WC-Co cold forging dies based on experimental and numerical studies. Engineering Failure Analysis, 118, 104910. https://doi.org/10.1016/j.engfailanal.2020.104910
- Dalbosco, M., da Silva Lopes, G., Schmitt, P. D., Pinotti, L., Boing, D. (2021). Improving fatigue life of cold forging dies by finite element analysis: A case study. Journal of Manufacturing Processes, 64, 349–355. https://doi.org/10.1016/j.jmapro.2021.01.039
- Karnaukh, S. G., Markov, O. E., Shapoval, A. A., Hrudkina, N. S. (2023). Selecting a cutting method for workpieces before stamping using synergetic fracture criteria and a deformability limit determination technique for separating processes. The International Journal of Advanced Manufacturing Technology, 129 (11-12), 5447–5455. https://doi.org/10.1007/s00170-023-12627-z
- Emamverdian, A. A., Sun, Y., Cao, C., Pruncu, C., Wang, Y. (2021). Current failure mechanisms and treatment methods of hot forging tools (dies) - a review. Engineering Failure Analysis, 129, 105678. https://doi.org/10.1016/j.engfailanal.2021.105678
- Madhankumar, S., Hari Narayanan, K. R., Harini, V., Gokulraj, K. V., Selvakumar, S., Dharshini, R. et al. (2021). Study and selection of hot forging die materials and hardness. Materials Today: Proceedings, 45, 6563–6566. https://doi.org/10.1016/j.matpr.2020.11.472
- Heinrichs, J., Mikado, H., Wiklund, U., Kawamura, S., Jacobson, S. (2022). Wear of cemented carbide forging dies used in zipper production. Wear, 492–493, 204216. https://doi.org/10.1016/j.wear.2021.204216
- Alessio, A., Antonelli, D., Doglione, R., Genta, G. (2022). Die wear reduction by multifactorial Design of Experiments applied to forging simulations. Procedia CIRP, 112, 424–429. https://doi.org/10.1016/j.procir.2022.09.031
- Aliiev, I. S., Sivak, R. I., Markov, O. E., Levchenko, V. N. (2023). The evaluation of workpiece deformability for the process of two-stage extrusion of hollow hull. The International Journal of Advanced Manufacturing Technology, 129 (3-4), 1345–1353. https://doi.org/10.1007/s00170-023-12353-6
- Kalyuzhnyi, V. L., Markov, O. E., Aliieva, L. I., Levchenko, V. N., Kaliuzhnyi, O. V., Hrudkina, N. S. (2024). Investigation of hot combined extrusion of steel hollow conical parts. Journal of the Brazilian Society of Mechanical Sciences and Engineering, 46 (8). https://doi.org/10.1007/s40430-024-05032-4
- Davoudi, M., Nejad, A. F., Rahimian Koloor, S. S., Petrů, M. (2021). Investigation of effective geometrical parameters on wear of hot forging die. Journal of Materials Research and Technology, 15, 5221–5231. https://doi.org/10.1016/j.jmrt.2021.10.093
- Hawryluk, M., Lachowicz, M., Janik, M., Ziemba, J., Gronostajski, Z. (2023). Preliminary studies of increasing the durability of forging tools subjected to various variants of surface treatment used in the hot die forging process of producing valve forgings. Engineering Failure Analysis, 143, 106886. https://doi.org/10.1016/j.engfailanal.2022.106886
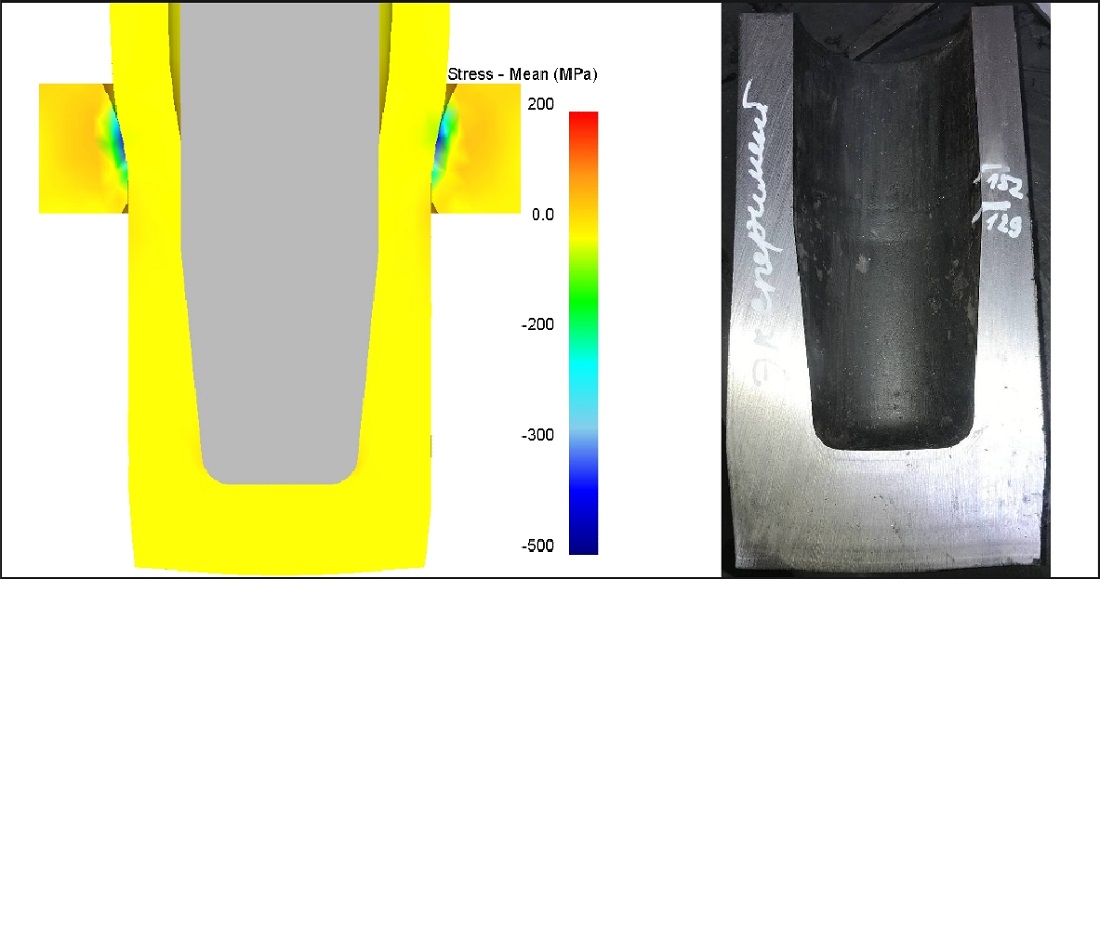
Downloads
Published
How to Cite
Issue
Section
License
Copyright (c) 2024 Oleg Markov, Volodymyr Zinskyi, Serhii Shevtsov, Natalia Hrudkina

This work is licensed under a Creative Commons Attribution 4.0 International License.
The consolidation and conditions for the transfer of copyright (identification of authorship) is carried out in the License Agreement. In particular, the authors reserve the right to the authorship of their manuscript and transfer the first publication of this work to the journal under the terms of the Creative Commons CC BY license. At the same time, they have the right to conclude on their own additional agreements concerning the non-exclusive distribution of the work in the form in which it was published by this journal, but provided that the link to the first publication of the article in this journal is preserved.
A license agreement is a document in which the author warrants that he/she owns all copyright for the work (manuscript, article, etc.).
The authors, signing the License Agreement with TECHNOLOGY CENTER PC, have all rights to the further use of their work, provided that they link to our edition in which the work was published.
According to the terms of the License Agreement, the Publisher TECHNOLOGY CENTER PC does not take away your copyrights and receives permission from the authors to use and dissemination of the publication through the world's scientific resources (own electronic resources, scientometric databases, repositories, libraries, etc.).
In the absence of a signed License Agreement or in the absence of this agreement of identifiers allowing to identify the identity of the author, the editors have no right to work with the manuscript.
It is important to remember that there is another type of agreement between authors and publishers – when copyright is transferred from the authors to the publisher. In this case, the authors lose ownership of their work and may not use it in any way.