Розробка оптимальної геометрії радіусної матриці для протяжки гільз
DOI:
https://doi.org/10.15587/1729-4061.2024.317060Ключові слова:
гільза, протяжка, матриця, радіус заокруглення, зношування, оправка, стійкість, сила протяжки, пустотіла заготовка, МСЕАнотація
Об’єкт дослідження – технологічний процес протягування на оправці гільз через радіусну матрицю. Робота спрямована на вирішення актуального наукового та технічного завдання удосконалення технологічного процесу протягування на оправці через матрицю при виготовленні поковок типу гільз, який забезпечує підвищення стійкості протяжних матриць. Методом скінчених елементів (МСЕ) виконано моделювання процесів протягування гільз через матрицю. В результаті було встановлено раціональну геометрію радіусної матриці. Розроблено рекомендації для проектування нових конструкцій матриць, які полягають у визначенні раціонального радіусу заокруглення робочої частини матриці. Встановлені рекомендації перевірено експериментальними дослідженнями. Протяжку гільз через матрицю з робочою радіусною поверхнею слід проводити при відносному радіусі R/d=3.0. У цьому випадку: інтенсивність напружень знизилася на 7…17 %, середні стискаючі напруги знизилися на 8…15 %, а нормальний тиск знизився на 10…15 % порівняно з меншими радіусами округлення. Результуюча сила на робочу поверхню матриці знизилася на 40…55 %, а радіальна компонента цієї сили до 50 %. Встановлено, що робоча поверхня матриці розігрівається до температури 750…850 °C, проте радіус заокруглення R/d=3.0 забезпечує зниження об’єму цієї зони в 1.5…1.9 разів. Перевірка отриманого відносного радіусу заокруглення матриці проводилася в промислових умовах, яка підтвердила, що сила протяжки для цього радіусу нижча на 15...20 %, а стійкість такої матриці підвищилася на 20 %. Рекомендується використовувати радіусні матриці для протягування високих гільз. Встановлені результати можуть застосовуватись і на підприємствах під час виготовлення деталей подвійного призначення
Посилання
- Wang, P., Zhu, S., Wang, L., Wu, L., Guan, S. (2015). A two-step superplastic forging forming of semi-continuously cast AZ70 magnesium alloy. Journal of Magnesium and Alloys, 3 (1), 70–75. https://doi.org/10.1016/j.jma.2014.12.004
- Karnaukh, S., Markov, O., Lysenko, A. (2024). Research on the new process of separating hollow work-piece by eccentric torsion cutting for stamping. FME Transactions, 52 (1), 29–36. https://doi.org/10.5937/fme2401029k
- Guan, S. K., Wu, L. H., Wang, P. (2009). Hot forgeability and die-forging forming of semi-continuously cast AZ70 magnesium alloy. Materials Science and Engineering: A, 499 (1-2), 187–191. https://doi.org/10.1016/j.msea.2007.11.136
- Chander, S., Chawla, V. (2017). Failure of Hot Forging Dies –An Updated Perspective. Materials Today: Proceedings, 4 (2), 1147–1157. https://doi.org/10.1016/j.matpr.2017.01.131
- Aliiev, I. S., Levchenko, V. N., Markov, O. E., Kalujniy, A. V., Aliieva, L. I., Sivak, R. I. (2024). Development of devices for measuring contact friction forces in the processes of volumetric plastic deformation. The International Journal of Advanced Manufacturing Technology, 132 (5-6), 2839–2851. https://doi.org/10.1007/s00170-024-13537-4
- Podgrajšek, M., Glodež, S., Ren, Z. (2015). Failure analysis of forging die insert protected with diffusion layer and PVD coating. Surface and Coatings Technology, 276, 521–528. https://doi.org/10.1016/j.surfcoat.2015.06.021
- Ghalehbandi, S. M., Biglari, F. (2020). Predicting damage and failure under thermomechanical fatigue in hot forging tools. Engineering Failure Analysis, 113, 104545. https://doi.org/10.1016/j.engfailanal.2020.104545
- Chen, Q., Geng, H., Zhang, H., Li, X., Chen, G. (2022). Microstructure and mechanical properties of in situ TiB2•TiAl3/2024Al composite subjected to multidirectional forging. Journal of Materials Research and Technology, 21, 2827–2840. https://doi.org/10.1016/j.jmrt.2022.10.098
- Jeong, H. Y., Park, J., Kim, Y., Shin, S. Y., Kim, N. (2023). Processing parameters optimization in hot forging of AISI 4340 steel using instability map and reinforcement learning. Journal of Materials Research and Technology, 23, 1995–2009. https://doi.org/10.1016/j.jmrt.2023.01.106
- Hawryluk, M. (2016). Review of selected methods of increasing the life of forging tools in hot die forging processes. Archives of Civil and Mechanical Engineering, 16 (4), 845–866. https://doi.org/10.1016/j.acme.2016.06.001
- Markov, O., Shevtsov, S., Hrudkina, N., Molodetskyi, V., Musorin, A., Zinskyi, V. (2023). Testing a new technique for producing artillery cartridge cases from pipe workpiece by roughing with a friction tool. Eastern-European Journal of Enterprise Technologies, 6 (1 (126)), 91–97. https://doi.org/10.15587/1729-4061.2023.291881
- Hawryluk, M., Ziemba, J. (2017). Possibilities of application measurement techniques in hot die forging processes. Measurement, 110, 284–295. https://doi.org/10.1016/j.measurement.2017.07.003
- Shen, L., Zhou, J., Xiong, Y.-B., Zhang, J.-S., Meng, Y. (2018). Analysis of service condition of large hot forging die and refabrication of die by bimetal-layer weld surfacing technology with a cobalt-based superalloy and a ferrous alloy. Journal of Manufacturing Processes, 31, 731–743. https://doi.org/10.1016/j.jmapro.2018.01.005
- Soranansri, P., Yanil, S., Sirivedin, K. (2019). Finite Element Modeling of Shrink-Fit Design for Improvement of Die-Service Life in Hot Forging Process of a Bevel Gear. Materials Today: Proceedings, 17, 1711–1719. https://doi.org/10.1016/j.matpr.2019.06.202
- Tanrıkulu, B., Karakuzu, R. (2020). Fatigue life prediction model of WC-Co cold forging dies based on experimental and numerical studies. Engineering Failure Analysis, 118, 104910. https://doi.org/10.1016/j.engfailanal.2020.104910
- Dalbosco, M., da Silva Lopes, G., Schmitt, P. D., Pinotti, L., Boing, D. (2021). Improving fatigue life of cold forging dies by finite element analysis: A case study. Journal of Manufacturing Processes, 64, 349–355. https://doi.org/10.1016/j.jmapro.2021.01.039
- Karnaukh, S. G., Markov, O. E., Shapoval, A. A., Hrudkina, N. S. (2023). Selecting a cutting method for workpieces before stamping using synergetic fracture criteria and a deformability limit determination technique for separating processes. The International Journal of Advanced Manufacturing Technology, 129 (11-12), 5447–5455. https://doi.org/10.1007/s00170-023-12627-z
- Emamverdian, A. A., Sun, Y., Cao, C., Pruncu, C., Wang, Y. (2021). Current failure mechanisms and treatment methods of hot forging tools (dies) - a review. Engineering Failure Analysis, 129, 105678. https://doi.org/10.1016/j.engfailanal.2021.105678
- Madhankumar, S., Hari Narayanan, K. R., Harini, V., Gokulraj, K. V., Selvakumar, S., Dharshini, R. et al. (2021). Study and selection of hot forging die materials and hardness. Materials Today: Proceedings, 45, 6563–6566. https://doi.org/10.1016/j.matpr.2020.11.472
- Heinrichs, J., Mikado, H., Wiklund, U., Kawamura, S., Jacobson, S. (2022). Wear of cemented carbide forging dies used in zipper production. Wear, 492–493, 204216. https://doi.org/10.1016/j.wear.2021.204216
- Alessio, A., Antonelli, D., Doglione, R., Genta, G. (2022). Die wear reduction by multifactorial Design of Experiments applied to forging simulations. Procedia CIRP, 112, 424–429. https://doi.org/10.1016/j.procir.2022.09.031
- Aliiev, I. S., Sivak, R. I., Markov, O. E., Levchenko, V. N. (2023). The evaluation of workpiece deformability for the process of two-stage extrusion of hollow hull. The International Journal of Advanced Manufacturing Technology, 129 (3-4), 1345–1353. https://doi.org/10.1007/s00170-023-12353-6
- Kalyuzhnyi, V. L., Markov, O. E., Aliieva, L. I., Levchenko, V. N., Kaliuzhnyi, O. V., Hrudkina, N. S. (2024). Investigation of hot combined extrusion of steel hollow conical parts. Journal of the Brazilian Society of Mechanical Sciences and Engineering, 46 (8). https://doi.org/10.1007/s40430-024-05032-4
- Davoudi, M., Nejad, A. F., Rahimian Koloor, S. S., Petrů, M. (2021). Investigation of effective geometrical parameters on wear of hot forging die. Journal of Materials Research and Technology, 15, 5221–5231. https://doi.org/10.1016/j.jmrt.2021.10.093
- Hawryluk, M., Lachowicz, M., Janik, M., Ziemba, J., Gronostajski, Z. (2023). Preliminary studies of increasing the durability of forging tools subjected to various variants of surface treatment used in the hot die forging process of producing valve forgings. Engineering Failure Analysis, 143, 106886. https://doi.org/10.1016/j.engfailanal.2022.106886
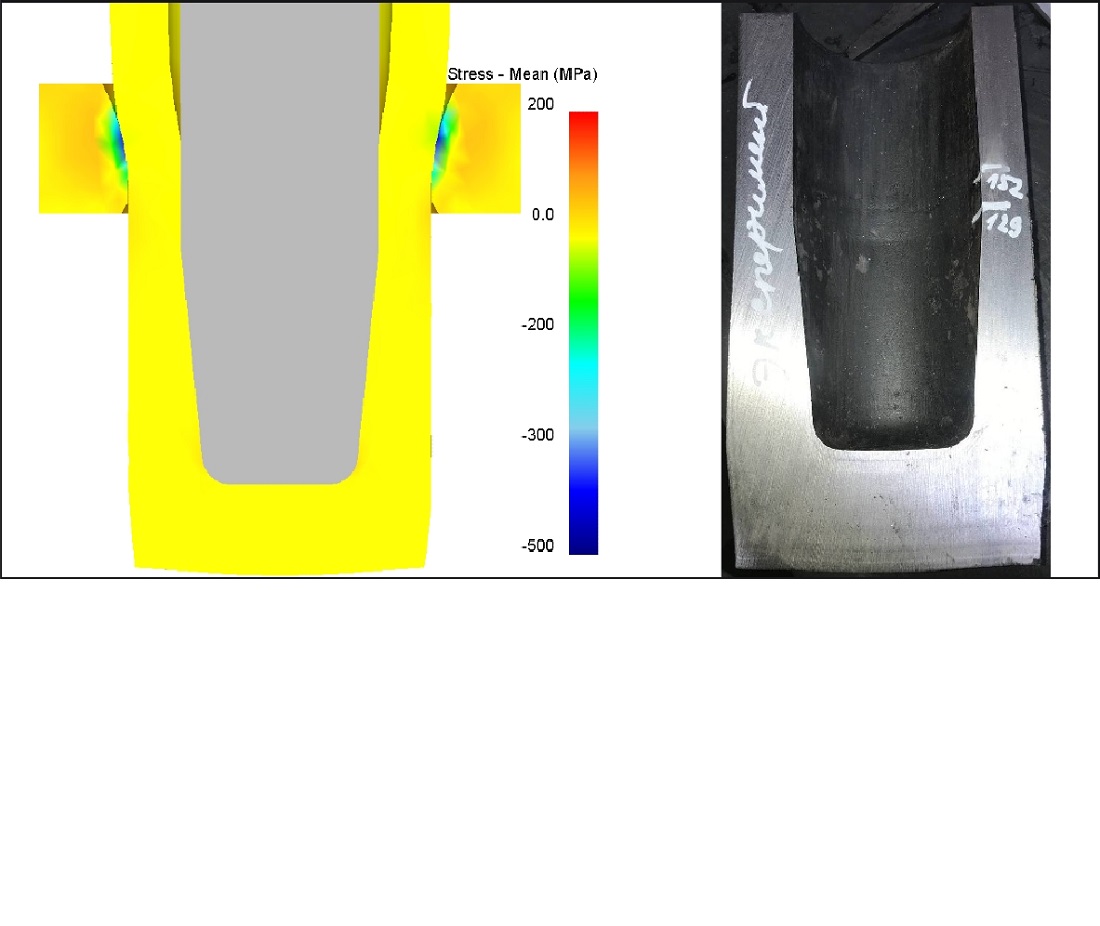
##submission.downloads##
Опубліковано
Як цитувати
Номер
Розділ
Ліцензія
Авторське право (c) 2024 Oleg Markov, Volodymyr Zinskyi, Serhii Shevtsov, Natalia Hrudkina

Ця робота ліцензується відповідно до Creative Commons Attribution 4.0 International License.
Закріплення та умови передачі авторських прав (ідентифікація авторства) здійснюється у Ліцензійному договорі. Зокрема, автори залишають за собою право на авторство свого рукопису та передають журналу право першої публікації цієї роботи на умовах ліцензії Creative Commons CC BY. При цьому вони мають право укладати самостійно додаткові угоди, що стосуються неексклюзивного поширення роботи у тому вигляді, в якому вона була опублікована цим журналом, але за умови збереження посилання на першу публікацію статті в цьому журналі.
Ліцензійний договір – це документ, в якому автор гарантує, що володіє усіма авторськими правами на твір (рукопис, статтю, тощо).
Автори, підписуючи Ліцензійний договір з ПП «ТЕХНОЛОГІЧНИЙ ЦЕНТР», мають усі права на подальше використання свого твору за умови посилання на наше видання, в якому твір опублікований. Відповідно до умов Ліцензійного договору, Видавець ПП «ТЕХНОЛОГІЧНИЙ ЦЕНТР» не забирає ваші авторські права та отримує від авторів дозвіл на використання та розповсюдження публікації через світові наукові ресурси (власні електронні ресурси, наукометричні бази даних, репозитарії, бібліотеки тощо).
За відсутності підписаного Ліцензійного договору або за відсутністю вказаних в цьому договорі ідентифікаторів, що дають змогу ідентифікувати особу автора, редакція не має права працювати з рукописом.
Важливо пам’ятати, що існує і інший тип угоди між авторами та видавцями – коли авторські права передаються від авторів до видавця. В такому разі автори втрачають права власності на свій твір та не можуть його використовувати в будь-який спосіб.