Creation of automatic clamping mechanisms for spindle assemblies of machine tools using a formalized description of structural elements
DOI:
https://doi.org/10.15587/1729-4061.2022.265191Keywords:
clamping mechanism drive, clamping chuck, spindle, clamping forces, mechanism structureAbstract
The characteristics of the functioning of automatic mechanisms for clamping workpieces and cylindrical tools in the spindle assemblies of metalworking machines determine the potential for improving the productivity and quality of processing. The conducted research is aimed at developing new approaches to the creation of automatic clamping mechanisms with qualitatively new and necessary characteristics of their functioning. The formation of new characteristics is achieved by implementing appropriate changes at the structural level of an object. The results obtained provide better opportunities for the development of structures of automatic clamping mechanisms by improving the systematization of a review of an increased number of alternative options for their structural elements. This was achieved by solving the problem of formal description and representation of structural elements operating on the basis of various physical effects within one subject area of the systematization matrix. The results allow strengthening the heuristic potential in the design and involving an extended range of physical effects suitable for effective energy transfer and conversion in the operating conditions of automatic clamping mechanisms. The possibility of describing structural elements as digital codes helps to increase the efficiency of analysis and processing of information of the initial design stages. Using the codes of the selected structural elements, three sequences corresponding to the structures of automatic clamping mechanisms according to the brief descriptions [1.7–2.4]–(1.1–2.3); [1.7–2.6]–(1.1–2.3); [1.7–2.6+1.6/1.7–2.1]–(1.1–2.3) were compiled. On their basis, designs of automatic clamping mechanisms with predictably better characteristics and extended technological capabilities are developed
References
- Thorenz, B., Westermann, H., Kafara, M., Nuetzel, M., Steinhilper, R. (2018). Evaluation of the influence of different clamping chuck types on energy consumption, tool wear and surface qualities in milling operations. Procedia Manufacturing, 21, 575-582. doi: https://doi.org/10.1016/j.promfg.2018.02.158
- Hsieh, L.-C., Chen, T.-H., Lai, P.-C. (2014). The kinematic design of mold clamping mechanism with minimal maximum acceleration. Advances in Mechanical Engineering, 12 (6). doi: https://doi.org/10.1177/1687814020926280
- Wan, S., Hong, J., Du, F., Fang, B., Li, X. (2019). Modelling and characteristic investigation of spindle-holder assembly under clamping and centrifugal forces. Journal of Mechanical Science and Technology, 33 (5), 2397–2405. doi: https://doi.org/10.1007/s12206-019-0438-3
- Xu, C., Zhang, J., Feng, P., Yu, D., Wu, Z. (2014). Characteristics of stiffness and contact stress distribution of a spindle–holder taper joint under clamping and centrifugal forces. International Journal of Machine Tools and Manufacture, 82-83, 21–28. doi: https://doi.org/10.1016/j.ijmachtools.2014.03.006
- Alquraan, T., Kuznetsov, Yu., Tsvyd, T. (2016). High-speed Clamping Mechanism of the CNC Lathe with Compensation of Centrifugal Forces. Procedia Engineering, 150, 689–695. doi: https://doi.org/10.1016/j.proeng.2016.07.081
- Soriano, E., Rubio, H., García-Prada, J. C. (2012). Analysis of the Clamping Mechanisms of Collet-Chucks Holders for Turning. Mechanisms and Machine Science, 391–398. doi: https://doi.org/10.1007/978-94-007-4902-3_42
- Prydalnyi, B. (2021). Mathematical Model of a Backlash Elimination in the New Clamping Mechanism. Lecture Notes in Mechanical Engineering, 109–118. doi: https://doi.org/10.1007/978-3-030-91327-4_11
- Estrems, M., Carrero-Blanco, J., Cumbicus, W. E., de Francisco, O., Sánchez, H. T. (2017). Contact mechanics applied to the machining of thin rings. Procedia Manufacturing, 13, 655–662. doi: https://doi.org/10.1016/j.promfg.2017.09.138
- Spur, G., Stelzer, C. (1994). Closed-loop Control in Power Operated Three-jaw Chucks. Advancement of Intelligent Production, 271–276. doi: https://doi.org/10.1016/b978-0-444-81901-7.50059-1
- Wang, G., Cao, Y., Zhang, Y. (2022). Digital twin-driven clamping force control for thin-walled parts. Advanced Engineering Informatics, 51, 101468. doi: https://doi.org/10.1016/j.aei.2021.101468
- Sondar, P. R., Gurudath, B., Ahirwar, V., Hegde, S. R. (2022). Failure of hydraulic lathe chuck assembly. Engineering Failure Analysis, 133, 106001. doi: https://doi.org/10.1016/j.engfailanal.2021.106001
- Estrems, M., Arizmendi, M., Cumbicus, W. E., López, A. (2015). Measurement of Clamping Forces in a 3 Jaw Chuck through an Instrumented Aluminium Ring. Procedia Engineering, 132, 456–463. doi: https://doi.org/10.1016/j.proeng.2015.12.519
- Neugebauer, R., Denkena, B., Wegener, K. (2007). Mechatronic Systems for Machine Tools. CIRP Annals, 56 (2), 657–686. doi: https://doi.org/10.1016/j.cirp.2007.10.007
- Prydalnyi, B., Sulym, H. (2021). Identification of Analytical Dependencies of the Operational Characteristics of the Workpiece Clamping Mechanisms with the Rotary Movement of the Input Link. Acta Mechanica et Automatica, 15 (1), 47–52. doi: https://doi.org/10.2478/ama-2021-0007
- Yoshitomi, K., Une, A., Tada, K. (2020). Study of a clamping process with no deformation for a thin substrate using a freezing pin chuck system. Precision Engineering, 64, 45–52. doi: https://doi.org/10.1016/j.precisioneng.2020.03.008
- Walter, M. F., Ståhl, J. E. (1994). The connection between cutting and clamping forces in turning. International Journal of Machine Tools and Manufacture, 34 (7), 991–1003. doi: https://doi.org/10.1016/0890-6955(94)90030-2
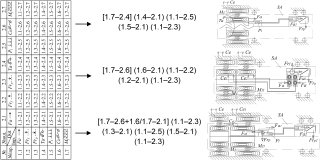
Downloads
Published
How to Cite
Issue
Section
License
Copyright (c) 2022 Borys Prydalnyi

This work is licensed under a Creative Commons Attribution 4.0 International License.
The consolidation and conditions for the transfer of copyright (identification of authorship) is carried out in the License Agreement. In particular, the authors reserve the right to the authorship of their manuscript and transfer the first publication of this work to the journal under the terms of the Creative Commons CC BY license. At the same time, they have the right to conclude on their own additional agreements concerning the non-exclusive distribution of the work in the form in which it was published by this journal, but provided that the link to the first publication of the article in this journal is preserved.
A license agreement is a document in which the author warrants that he/she owns all copyright for the work (manuscript, article, etc.).
The authors, signing the License Agreement with TECHNOLOGY CENTER PC, have all rights to the further use of their work, provided that they link to our edition in which the work was published.
According to the terms of the License Agreement, the Publisher TECHNOLOGY CENTER PC does not take away your copyrights and receives permission from the authors to use and dissemination of the publication through the world's scientific resources (own electronic resources, scientometric databases, repositories, libraries, etc.).
In the absence of a signed License Agreement or in the absence of this agreement of identifiers allowing to identify the identity of the author, the editors have no right to work with the manuscript.
It is important to remember that there is another type of agreement between authors and publishers – when copyright is transferred from the authors to the publisher. In this case, the authors lose ownership of their work and may not use it in any way.