Fatigue determination of the kenaf/PLA composite structure using fatigue specimen (ASTM D7791): a computational analysis
DOI:
https://doi.org/10.15587/1729-4061.2023.273974Keywords:
Static structural, FEM, Fatigue analysis, kenaf/PLA composite, ASTM D7791Abstract
In this investigation, a kenaf/PLA composite specimen was subjected to the fatigue load, and the results were analyzed numerically. Some of the most significant fatigue tool aspects that were looked into were life expectancy, damage, alternative stress, and biaxiality indication. The static structural tool was utilized in order to predict the numerical analysis, and the calculations were performed with the GoodMan theory of fatigue. The loading was completely reversed so that it was equal to 30 kN. When it was discovered that the system could continue to function even after 1e6 cycles had been completed. After applying the alternative load of 30 kN, the biaxiality indication was found to be 0.425, with a minimum value of 0.9. It has been determined how much damage has occurred. The minimum amount of cycles necessary to reach the maximum damage potential is 1000, while the maximum amount of cycles necessary to reach the maximum damage potential is 1.7662·106. It has been established that there is another stress that is comparable to this one. Based on the findings of the investigation, it was determined that the fillet regions of the specimen were subjected to a maximum alternative stress of 716.4 MPa. The alternative stress cannot drop below 31.276 MPa under any circumstances. It has been determined that 106cycles have been spent living in total by the calculation. It has been found out that there is not going to be any damage regardless of the number of cycles that pass due to the fact that that number is 1. It was found that the alternative stress could reach a maximum value of 716.4 MPa, so that was the value that was used for the alternative stress
References
- Shahar, F. S., Hameed Sultan, M. T., Safri, S. N. A., Jawaid, M., Abu Talib, Abd. R., Basri, A. A., Md Shah, A. U. (2022). Fatigue and impact properties of 3D printed PLA reinforced with kenaf particles. Journal of Materials Research and Technology, 16, 461–470. doi: https://doi.org/10.1016/j.jmrt.2021.12.023
- Travieso-Rodriguez, J. A., Zandi, M. D., Jerez-Mesa, R., Lluma-Fuentes, J. (2020). Fatigue behavior of PLA-wood composite manufactured by fused filament fabrication. Journal of Materials Research and Technology, 9 (4), 8507–8516. doi: https://doi.org/10.1016/j.jmrt.2020.06.003
- Shahar, F. S., Hameed Sultan, M. T., Safri, S. N. A., Jawaid, M., Abu Talib, Abd. R., Basri, A. A., Md Shah, A. U. (2022). Physical, thermal and tensile behaviour of 3D printed kenaf/PLA to suggest its usability for ankle–foot orthosis – a preliminary study. Rapid Prototyping Journal, 28 (8), 1573–1588. doi: https://doi.org/10.1108/rpj-08-2021-0207
- Beigpour, R., Shokrollahi, H., Khalili, S. M. R. (2021). Experimental and numerical analysis of a biodegradable hybrid composite under tensile and three-point bending tests. Composite Structures, 273, 114255. doi: https://doi.org/10.1016/j.compstruct.2021.114255
- Azlin, M. N. M., Sapuan, S. M., Zuhri, M. Y. M., Zainudin, E. S. (2022). Effect of stacking sequence and fiber content on mechanical and morphological properties of woven kenaf/polyester fiber reinforced polylactic acid (PLA) hybrid laminated composites. Journal of Materials Research and Technology, 16, 1190–1201. doi: https://doi.org/10.1016/j.jmrt.2021.12.046
- Nurazzi, N. M., Shazleen, S. S., Aisyah, H. A., Asyraf, M. R. M., Sabaruddin, F. A., Mohidem, N. A. et al. (2021). Effect of silane treatments on mechanical performance of kenaf fibre reinforced polymer composites: a review. Functional Composites and Structures, 3 (4), 045003. doi: https://doi.org/10.1088/2631-6331/ac351b
- Samat, N., Sulaiman, M. A., Ahmad, Z., Anuar, H. (2021). A comparative study on the desiccant effect of polypropylene and polylactic acid composites reinforced with different lignocellulosic fibres. Journal of Applied Science and Engineering, 24 (2), 223–231. doi: https://doi.org/10.6180/jase.202104_24(2).0011
- Lee, C. H., Padzil, F. N. B. M., Lee, S. H., Ainun, Z. M. A., Abdullah, L. C. (2021). Potential for Natural Fiber Reinforcement in PLA Polymer Filaments for Fused Deposition Modeling (FDM) Additive Manufacturing: A Review. Polymers, 13 (9), 1407. doi: https://doi.org/10.3390/polym13091407
- Radzuan, N. A. M., Tholibon, D., Sulong, A. B., Muhamad, N., Haron, C. H. C. (2020). New processing technique for biodegradable kenaf composites: A simple alternative to commercial automotive parts. Composites Part B: Engineering, 184, 107644. doi: https://doi.org/10.1016/j.compositesb.2019.107644
- Nor Arman, N. S., Chen, R. S., Ahmad, S. (2021). Review of state-of-the-art studies on the water absorption capacity of agricultural fiber-reinforced polymer composites for sustainable construction. Construction and Building Materials, 302, 124174. doi: https://doi.org/10.1016/j.conbuildmat.2021.124174
- Asim, M., Paridah, M. T., Chandrasekar, M., Shahroze, R. M., Jawaid, M., Nasir, M., Siakeng, R. (2020). Thermal stability of natural fibers and their polymer composites. Iranian Polymer Journal, 29 (7), 625–648. doi: https://doi.org/10.1007/s13726-020-00824-6
- Chandgude, S., Salunkhe, S. (2021). In state of art: Mechanical behavior of natural fiber‐based hybrid polymeric composites for application of automobile components. Polymer Composites, 42 (6), 2678–2703. doi: https://doi.org/10.1002/pc.26045
- Ilyas, R. A., Zuhri, M. Y. M., Aisyah, H. A., Asyraf, M. R. M., Hassan, S. A., Zainudin, E. S. et al. (2022). Natural Fiber-Reinforced Polylactic Acid, Polylactic Acid Blends and Their Composites for Advanced Applications. Polymers, 14 (1), 202. doi: https://doi.org/10.3390/polym14010202
- Senthil Muthu Kumar, T., Senthilkumar, K., Chandrasekar, M., Subramaniam, S., Mavinkere Rangappa, S., Siengchin, S., Rajini, N. (2020). Influence of Fillers on the Thermal and Mechanical Properties of Biocomposites: An Overview. Biofibers and Biopolymers for Biocomposites, 111–133. doi: https://doi.org/10.1007/978-3-030-40301-0_5
- Whitworth, A. H., Tsavdaridis, K. D. (2020). Genetic Algorithm for Embodied Energy Optimisation of Steel-Concrete Composite Beams. Sustainability, 12 (8), 3102. doi: https://doi.org/10.3390/su12083102
- Xiang, S., Wang, D., Yang, L., Tan, B. (2021). Study on the life cycle simulation method of the temperature field and temperature effect of a steel–concrete composite bridge deck system. Measurement and Control, 54 (5-6), 1068–1081. doi: https://doi.org/10.1177/00202940211020343
- Cheng, Z., Zhang, Q., Bao, Y., Deng, P., Wei, C., Li, M. (2021). Flexural behavior of corrugated steel-UHPC composite bridge decks. Engineering Structures, 246, 113066. doi: https://doi.org/10.1016/j.engstruct.2021.113066
- Ovuoba, B., Prinz, G. S. (2018). Investigation of residual fatigue life in shear studs of existing composite bridge girders following decades of traffic loading. Engineering Structures, 161, 134–145. doi: https://doi.org/10.1016/j.engstruct.2018.02.018
- Ferreira, F. P. V., Tsavdaridis, K. D., Martins, C. H., De Nardin, S. (2021). Steel-Concrete Composite Beams with Precast Hollow-Core Slabs: A Sustainable Solution. Sustainability, 13 (8), 4230. doi: https://doi.org/10.3390/su13084230
- Li, C., Lei, Z., Feng, Z., He, W., Tan, L. (2021). Research on static performance of lightweight STC-steel composite deck. J. Transp. Sci. Eng., 37, 26–33. doi: https://doi.org/10.16544/j.cnki.cn43-1494/u.2021.01.005
- Lee, P.-G., Shim, C.-S., Chang, S.-P. (2005). Static and fatigue behavior of large stud shear connectors for steel–concrete composite bridges. Journal of Constructional Steel Research, 61 (9), 1270–1285. doi: https://doi.org/10.1016/j.jcsr.2005.01.007
- Xu, X., Zhou, X., Liu, Y. (2020). Behavior of rubber-sleeved stud shear connectors under fatigue loading. Construction and Building Materials, 244, 118386. doi: https://doi.org/10.1016/j.conbuildmat.2020.118386
- Cao, J., Shao, X., Deng, L., Gan, Y. (2017). Static and Fatigue Behavior of Short-Headed Studs Embedded in a Thin Ultrahigh-Performance Concrete Layer. Journal of Bridge Engineering, 22 (5). doi: https://doi.org/10.1061/(asce)be.1943-5592.0001031
- Yang, D. (2021). Analysis of Fracture Mechanics Theory of the First Fracture Mechanism of Main Roof and Support Resistance with Large Mining Height in a Shallow Coal Seam. Sustainability, 13 (4), 1678. doi: https://doi.org/10.3390/su13041678
- Wang, Y., Nie, J. (2009). Fatigue behavior of studs in a composite beam based on fracture mechanics. Qinghua Daxue Xuebao/Journal of Tsinghua University, 49 (9), 1467–1470.
- Wu, X., Yu, H., Guo, L., Zhang, L., Sun, X., Chai, Z. (2019). Experimental and numerical investigation of static and fatigue behaviors of composites honeycomb sandwich structure. Composite Structures, 213, 165–172. doi: https://doi.org/10.1016/j.compstruct.2019.01.081
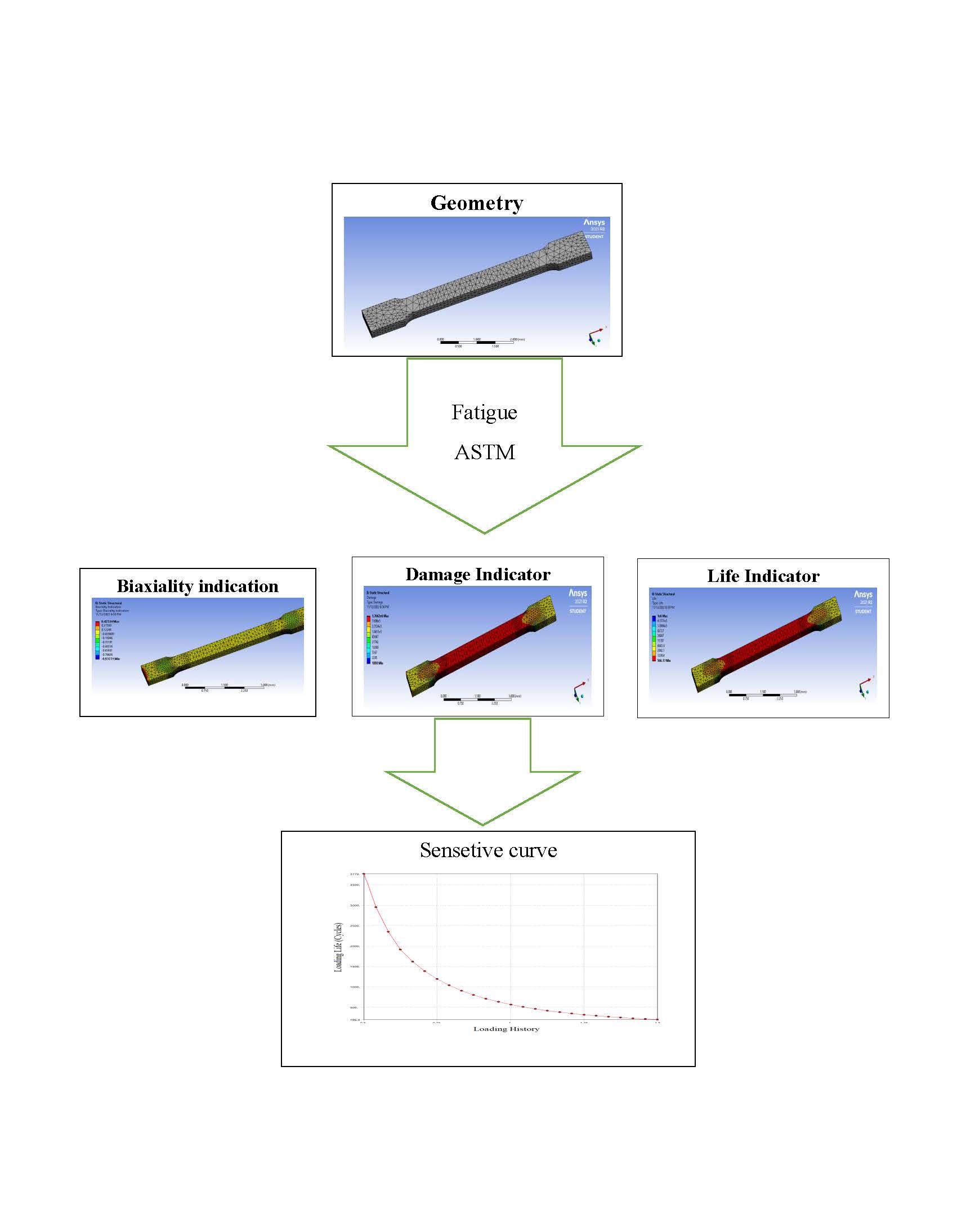
Downloads
Published
How to Cite
Issue
Section
License
Copyright (c) 2023 Muthana Adil Najim Abbu, Doaa Talib Hashim, Hasan Mohammed Ahmed Albegmprli, Mustafa Ridha Mezaal

This work is licensed under a Creative Commons Attribution 4.0 International License.
The consolidation and conditions for the transfer of copyright (identification of authorship) is carried out in the License Agreement. In particular, the authors reserve the right to the authorship of their manuscript and transfer the first publication of this work to the journal under the terms of the Creative Commons CC BY license. At the same time, they have the right to conclude on their own additional agreements concerning the non-exclusive distribution of the work in the form in which it was published by this journal, but provided that the link to the first publication of the article in this journal is preserved.
A license agreement is a document in which the author warrants that he/she owns all copyright for the work (manuscript, article, etc.).
The authors, signing the License Agreement with TECHNOLOGY CENTER PC, have all rights to the further use of their work, provided that they link to our edition in which the work was published.
According to the terms of the License Agreement, the Publisher TECHNOLOGY CENTER PC does not take away your copyrights and receives permission from the authors to use and dissemination of the publication through the world's scientific resources (own electronic resources, scientometric databases, repositories, libraries, etc.).
In the absence of a signed License Agreement or in the absence of this agreement of identifiers allowing to identify the identity of the author, the editors have no right to work with the manuscript.
It is important to remember that there is another type of agreement between authors and publishers – when copyright is transferred from the authors to the publisher. In this case, the authors lose ownership of their work and may not use it in any way.