Identifying regularities of high temperature on constant and variable fatigue life of AA7075-Al2O3 nanocomposite fabricated by stir casting method
DOI:
https://doi.org/10.15587/1729-4061.2023.276835Keywords:
AA7075, ceramic particles Al2O3, mechanical properties, fatigue characterizations, high temperatureAbstract
This study aims to determine the effect of high temperature on the fatigue life of AA7075-Al2O3 nanocomposites (6 wt % Al2O3) fabricated by stir casting. The research problem is to determine the durability, fatigue resistance, and mechanical properties of the nanocomposite under constant and variable loading conditions at elevated temperatures, as well as to identify changes in its behavior due to exposure to high temperatures. The results show that higher temperatures have a big effect on the nanocomposite's fatigue performance under both loading conditions. When the material was tested at a high temperature (150 °C) with an extra 6 wt % Al2O3, the ultimate tensile strength and yield stress both went up by 16 % and 15.7 %, respectively. Its fatigue life was also successfully tested under both variable and constant amplitude load conditions. The interpretation of the results suggests that the changes in the microstructure of the nanocomposite material at elevated temperatures lead to an increase in dislocation density and grain size, resulting in an improvement in its mechanical properties. The findings can be utilized to optimize the nanocomposite fabrication process and enhance its fatigue resistance at high temperatures. In addition, the results can be used to enhance the design of aerospace components and high-temperature engines that require materials with excellent fatigue resistance at elevated temperatures. In summary, the investigation of the effect of high temperature on the constant and variable fatigue lives of AA7075-Al2O3 nanocomposite provides valuable insight into the material's mechanical properties. The findings contribute to the development of materials that can withstand high-temperature conditions, which has implications for a variety of industries.
Supporting Agency
- The authors would like to express their gratitude to the Iraqi Ministry of Higher Education and Scientific Research for their support during this project.
References
- Aynalem, G. F. (2020). Processing Methods and Mechanical Properties of Aluminium Matrix Composites. Advances in Materials Science and Engineering, 2020, 1–19. doi: https://doi.org/10.1155/2020/3765791
- Hussain, F., Abdullah, S., Nuawi, M. Z. (2016). Effect of temperature on fatigue life behaviour of aluminium alloy AA6061 using analytical approach. Journal of Mechanical Engineering and Sciences, 10 (3), 2324–2335. doi:https://doi.org/10.15282/jmes.10.3.2016.10.0216
- RaviKumar, M., Reddappa, H. N., Suresh, R. (2018). Mechanical and Wear behavior of Al7075/Al2O3/SiC Hybrid Composite. Materials Today: Proceedings, 5 (2), 5573–5579. doi:https://doi.org/10.1016/j.matpr.2017.12.148
- Abed, R. M., Khenyab, A. Y., Alalkawi, H. J. M. (2021). Development in mechanical and fatigue properties of AA6061/AL2O3 nanocomposites under stirring temperature (ST). Eastern-European Journal of Enterprise Technologies, 4 (12 (112)), 47–52. doi:https://doi.org/10.15587/1729-4061.2021.238588
- Winter, L., Hockauf, K., Lampke, T. (2018). Temperature and Particle Size Influence on the High Cycle Fatigue Behavior of the SiC Reinforced 2124 Aluminum Alloy. Metals, 8 (1), 43. doi: https://doi.org/10.3390/met8010043
- Al-Mushehdany, A. M., Yahya, M. M., Hmood, B. K., Alalkawi, H. J. M. (2022). Using modern concepts in the design of extrusion dies to improve the mechanical extrusion and fatigue properties for AA1100. Eastern-European Journal of Enterprise Technologies, 5 (12 (119)), 31–37. doi: https://doi.org/10.15587/1729-4061.2022.265712
- Bharath, V., Ashita, D. H., Auradi, V., Nagaral, M. (2020). Influence of variable particle size reinforcement on mechanical and wear properties of alumina reinforced 2014Al alloy particulate composite. FME Transactions, 48 (4), 968–978. doi: https://doi.org/10.5937/fme2004968b
- Mahdi, H. S., Alalkawi, H. J., Mohamed, M. T., Faris, S. T. (2022). Evaluation of creep-fatigue life and strength for AA7001-T6 under constant amplitude loading. Eastern-European Journal of Enterprise Technologies, 4 (12 (118)), 22–28. doi: https://doi.org/10.15587/1729-4061.2022.263344
- Radha Krishnan, B., Theerkka Tharisanan, R., Arumuga Prabu, V., Immanuel, P., Ramakrishnan, A. (2022). Experimental investigation of mechanical properties of Al7075-Al2O3-B4C composite via stir route. Materials Today: Proceedings, 64, 1721–1724. doi: https://doi.org/10.1016/j.matpr.2022.05.498
- Zahra, H. S. (2017). The effect of Al2O3 nano materials on fatigue behavior of Al2O3 nano materials on fatigue behavior of 7075Al-alloy. Al. Mustansiriahah University.
- Fadhel, E. Z. (2018). Effect of the Elevated Temperature on Fatigue Behavior of Aluminum Alloy AA 7075. Journal of University of Babylon for Engineering Sciences, 26 (8), 256–264. Available at: https://www.journalofbabylon.com/index.php/JUBES/article/view/1630
- Allawi, H. Al., Hatem, K., Driss, Z., Alalkawi, H. J. M. (2023). Safe fatigue life model for AA2024-T4 and AA2024-T361 under combined high temperature and shot peening. Cyrved and Layered Structures.
- Adil, A. N., Alasadi, A. A., Alalkawi, H. J. M. (2023). Effect of nano particle size on mechanical and fatigue behaviour of TiO_2 particular. Reinforced aluminum alloy composites. IJNE, 16 (3).
- ASTM B221-14. Standard Specification For Aluminum And Aluminum-Alloy Extruded Bars, Rods, Wire, Profiles, And Tubes. Available at: https://webstore.ansi.org/standards/astm/astmb22114
- Ghdhban, T. Y. (2020). Design and Modification of a computerized tensile test machine at high temperature. University of Technology.
- Designation: E8/E8M – 09 Standard Test Methods for Tension Testing of Metallic Materials. Available at: https://www.academia.edu/14298711/Designation_E8_E8M_09_Standard_Test_Methods_for_Tension_Testing_of_Metallic_Materials
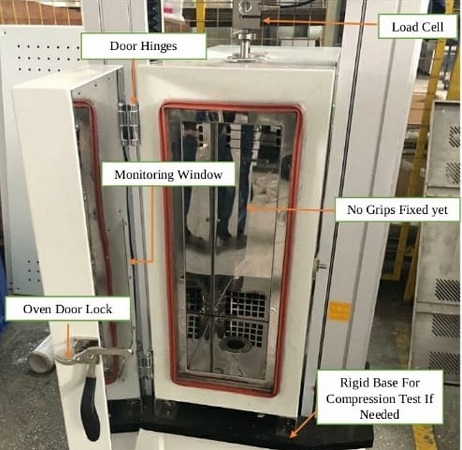
Downloads
Published
How to Cite
Issue
Section
License
Copyright (c) 2023 Muzher Taha Mohamed, Rawa A. Helal, Sami A. Nawi, Hussain Jasim Alalkawi, Ahmed AAG Al-rubaiy

This work is licensed under a Creative Commons Attribution 4.0 International License.
The consolidation and conditions for the transfer of copyright (identification of authorship) is carried out in the License Agreement. In particular, the authors reserve the right to the authorship of their manuscript and transfer the first publication of this work to the journal under the terms of the Creative Commons CC BY license. At the same time, they have the right to conclude on their own additional agreements concerning the non-exclusive distribution of the work in the form in which it was published by this journal, but provided that the link to the first publication of the article in this journal is preserved.
A license agreement is a document in which the author warrants that he/she owns all copyright for the work (manuscript, article, etc.).
The authors, signing the License Agreement with TECHNOLOGY CENTER PC, have all rights to the further use of their work, provided that they link to our edition in which the work was published.
According to the terms of the License Agreement, the Publisher TECHNOLOGY CENTER PC does not take away your copyrights and receives permission from the authors to use and dissemination of the publication through the world's scientific resources (own electronic resources, scientometric databases, repositories, libraries, etc.).
In the absence of a signed License Agreement or in the absence of this agreement of identifiers allowing to identify the identity of the author, the editors have no right to work with the manuscript.
It is important to remember that there is another type of agreement between authors and publishers – when copyright is transferred from the authors to the publisher. In this case, the authors lose ownership of their work and may not use it in any way.