Identifying the mechanism of the fatigue behavior of the composite shaft subjected to variable load
DOI:
https://doi.org/10.15587/1729-4061.2023.283078Keywords:
composite shaft, variable loading, fatigue life, biaxiality indication, damage indicatorAbstract
This paper presents a finite element analysis of a composite shaft under dynamic variable fatigue loading. The object of this study is the behavior of the fatigue life of a composite shaft under dynamic variable fatigue loading. The fatigue life of the shaft is then determined by analyzing the stress distribution and its effect on the material's fatigue strength. The investigation of fatigue behavior involves evaluating factors such as stress concentrations, fatigue crack initiation and propagation, and the cumulative damage caused by cyclic loading. The study explores the impact of biaxial loading on the shaft's fatigue performance and provides insights into its significance in predicting fatigue life and it is 10e7 cycles. Furthermore, a damage indicator is predicted to assess the accumulated damage and monitor the progression of fatigue-related degradation. This indicator serves as a valuable tool for predicting the remaining useful life of the composite shaft. The equivalent alternative stress is calculated to characterize the combined effect of different loading conditions on the fatigue life of the composite shaft. By quantifying the stress level and variations experienced by the structure, this parameter allows for a comprehensive assessment of the fatigue performance under variable loading scenarios 250 N. The findings of this research contribute to the understanding of fatigue behavior in composite shafts under dynamic variable fatigue loading. The insights gained from the fatigue life investigation, biaxiality indication, damage prediction, and equivalent alternative stress calculation can aid in optimizing design considerations, maintenance planning, and enhancing the reliability and durability of composite shafts in various engineering applications
References
- Nadeem, S. K. S., Giridhara, G., Rangavittal, H. K. (2018). A Review on the design and analysis of composite drive shaft. Materials Today: Proceedings, 5 (1), 2738–2741. doi: https://doi.org/10.1016/j.matpr.2018.01.058
- Stedile Filho, P., Almeida, J. H. S., Amico, S. C. (2017). Carbon/epoxy filament wound composite drive shafts under torsion and compression. Journal of Composite Materials, 52 (8), 1103–1111. doi: https://doi.org/10.1177/0021998317722043
- Hao, W., Yuan, Z., Tang, C., Zhang, L., Zhao, G., Luo, Y. (2019). Acoustic emission monitoring of damage progression in 3D braiding composite shafts during torsional tests. Composite Structures, 208, 141–149. doi: https://doi.org/10.1016/j.compstruct.2018.10.011
- Zhao, G., Zhang, L., Tang, C., Zhou, Y., Hao, W., Luo, Y. (2018). Experimental study on the torsion behavior of a 3D 4-directionally braided composite shaft using DIC and AE. Polymer Testing, 72, 122–131. doi: https://doi.org/10.1016/j.polymertesting.2018.10.016
- Zhao, G., Zhang, L., Tang, C., Hao, W., Luo, Y. (2019). Clustering of AE signals collected during torsional tests of 3D braiding composite shafts using PCA and FCM. Composites Part B: Engineering, 161, 547–554. doi: https://doi.org/10.1016/j.compositesb.2018.12.145
- Aghajani Derazkola, H., Kordani, N., Aghajani Derazkola, H. (2021). Effects of friction stir welding tool tilt angle on properties of Al-Mg-Si alloy T-joint. CIRP Journal of Manufacturing Science and Technology, 33, 264–276. doi: https://doi.org/10.1016/j.cirpj.2021.03.015
- Zhao, G., Wang, J., Hao, W., Liu, Y., Luo, Y. (2017). Numerical Study on the Tensile Behavior of 3D Four Directional Cylindrical Braided Composite Shafts. Applied Composite Materials, 25 (5), 1103–1114. doi: https://doi.org/10.1007/s10443-017-9655-z
- Hao, W., Liu, Y., Huang, X., Liu, Y., Zhu, J. (2017). A Unit-Cell Model for Predicting the Elastic Constants of 3D Four Directional Cylindrical Braided Composite Shafts. Applied Composite Materials, 25 (3), 619–633. doi: https://doi.org/10.1007/s10443-017-9639-z
- Huang, X., Liu, Y., Hao, W., Liu, Y., Zhu, J. (2017). Computational Analysis of Torsional Bulking Behavior of 3D 4-Directional Braided Composites Shafts. Applied Composite Materials, 25 (1), 163–176. doi: https://doi.org/10.1007/s10443-017-9616-6
- Wang, Y. Q., Wang, A. S. D. (1997). Spatial distribution of yarns and mechanical properties in 3D braided tubular composites. Applied Composite Materials, 4 (2), 121–132. doi: https://doi.org/10.1007/bf02481384
- Wang, Y. Q., Wang, A. S. D. (1994). On the topological yarn structure of 3-D rectangular and tubular braided preforms. Composites Science and Technology, 51 (4), 575–586. doi: https://doi.org/10.1016/0266-3538(94)90090-6
- Kalidindi, S. R., Franco, E. (1997). Numerical evaluation of isostrain and weighted-average models for elastic moduli of three-dimensional composites. Composites Science and Technology, 57 (3), 293–305. doi: https://doi.org/10.1016/s0266-3538(96)00119-4
- Gideon, R. K., Zhou, H., Li, Y., Sun, B., Gu, B. (2015). Quasi-static compression and compression–compression fatigue characteristics of 3D braided carbon/epoxy tube. The Journal of The Textile Institute, 107 (7), 938–948. doi: https://doi.org/10.1080/00405000.2015.1071964
- Gideon, R. K., Zhou, H., Wu, X., Sun, B., Gu, B. (2015). Finite element analysis of 3D circular braided composites tube damage based on three unit cell models under axial compression loading. International Journal of Damage Mechanics, 25 (4), 574–607. doi: https://doi.org/10.1177/1056789515605568
- Sun, J., Wang, Y., Zhou, G., Wang, X. (2016). Finite Element Analysis of Mechanical Properties of 3D Surface-Core Braided Composites. Polymer Composites, 39 (4), 1076–1088. doi: https://doi.org/10.1002/pc.24035
- Ouyang, Y., Sun, B., Gu, B. (2017). Finite element analyses on bending fatigue of three-dimesional five-directional braided composite T-beam with mixed unit-cell model. Journal of Composite Materials, 52 (9), 1139–1154. doi: https://doi.org/10.1177/0021998317722203
- Berardi, V. P., Perrella, M., Feo, L., Cricrì, G. (2017). Creep behavior of GFRP laminates and their phases: Experimental investigation and analytical modeling. Composites Part B: Engineering, 122, 136–144. doi: https://doi.org/10.1016/j.compositesb.2017.04.015
- Shokrieh, M. M., Mazloomi, M. S. (2012). A new analytical model for calculation of stiffness of three-dimensional four-directional braided composites. Composite Structures, 94 (3), 1005–1015. doi: https://doi.org/10.1016/j.compstruct.2011.09.010
- El-Sayed, M. M., Shash, A. Y., Abd-Rabou, M., ElSherbiny, M. G. (2021). Welding and processing of metallic materials by using friction stir technique: A review. Journal of Advanced Joining Processes, 3, 100059. doi: https://doi.org/10.1016/j.jajp.2021.100059
- Vuherer, T., Milčić, M., Glodež, S., Milčić, D., Radović, L., Kramberger, J. (2021). Fatigue and fracture behaviour of Friction Stir Welded AA-2024-T351 joints. Theoretical and Applied Fracture Mechanics, 114, 103027. doi: https://doi.org/10.1016/j.tafmec.2021.103027
- Deng, L., Li, S., Ke, L., Liu, J., Kang, J. (2019). Microstructure and Fracture Behavior of Refill Friction Stir Spot Welded Joints of AA2024 Using a Novel Refill Technique. Metals, 9 (3), 286. doi: https://doi.org/10.3390/met9030286
- Salman, S., Sharaf, H. K., Hussein, A. F., Khalaf, N. J., Abbas, M. K., Aned, A. M. et al. (2022). Optimization of raw material properties of natural starch by food glue based on dry heat method. Food Science and Technology, 42. doi: https://doi.org/10.1590/fst.78121
- Almagsoosi, L., Abadi, M. T. E., Hasan, H. F., Sharaf, H. K. (2022). Effect of the Volatility of the Crypto Currency and Its Effect on the Market Returns. Industrial Engineering & Management Systems, 21 (2), 238–243. doi: https://doi.org/10.7232/iems.2022.21.2.238
- Ashham, M., Sharaf, H. K., Salman, K., Salman, S. (2017). Simulation of heat transfer in a heat exchanger tube with inclined vortex rings inserts. International Journal of Applied Engineering Research, 12 (20), 9605–9613. Available at: https://www.ripublication.com/ijaer17/ijaerv12n20_48.pdf
- Raheemah, S. H., Fadheel, K. I., Hassan, Q. H., Aned, A. M., Turki Al-Taie, A. A., Sharaf, H. K. (2021). Numerical Analysis of the Crack Inspections Using Hybrid Approach for the Application the Circular Cantilever Rods. Pertanika Journal of Science and Technology, 29 (2). doi: https://doi.org/10.47836/pjst.29.2.22
- Subhi, K. A., Hussein, E. K., Al-Hamadani, H. R. D., Sharaf, H. K. (2022). Investigation of the mechanical performance of the composite prosthetic keel based on the static load: a computational analysis. Eastern-European Journal of Enterprise Technologies, 3 (7 (117)), 22–30. doi: https://doi.org/10.15587/1729-4061.2022.256943
- Sharaf, H. K., Alyousif, S., Khalaf, N. J., Hussein, A. F., Abbas, M. K. (2022). Development of bracket for cross arm structure in transmission tower: Experimental and numerical analysis. New Materials, Compounds and Applications, 6 (3), 257–275. Available at: http://www.jomardpublishing.com/UploadFiles/Files/journals/NMCA/V6N3/SharafHS.pdf
- Ghosh, B., Das, H., Samanta, A., Majumdar, J. D., Ghosh, M. (2022). Influence of tool rotational speed on the evolution of microstructure and mechanical properties of precipitation-hardened Aluminium 6061 butt joint during friction stir welding. Engineering Research Express. doi: https://doi.org/10.1088/2631-8695/ac4a48
- Salimi, S., Bahemmat, P., Haghpanahi, M. (2018). Study on residual stresses caused by underwater friction stir welding: FE modeling and ultrasonic measurement. Proceedings of the Institution of Mechanical Engineers, Part E: Journal of Process Mechanical Engineering, 233 (1), 118–137. doi: https://doi.org/10.1177/0954408917751963
- Malopheyev, S., Vysotskiy, I., Zhemchuzhnikova, D., Mironov, S., Kaibyshev, R. (2020). On the Fatigue Performance of Friction-Stir Welded Aluminum Alloys. Materials, 13 (19), 4246. doi: https://doi.org/10.3390/ma13194246
- Shekhan, S. M. M. (2020). A model for the distribution of temperature on the aluminum alloy when using friction welding. Altınbaş Üniversitesi. Available at: http://openaccess.altinbas.edu.tr/xmlui/handle/20.500.12939/1889
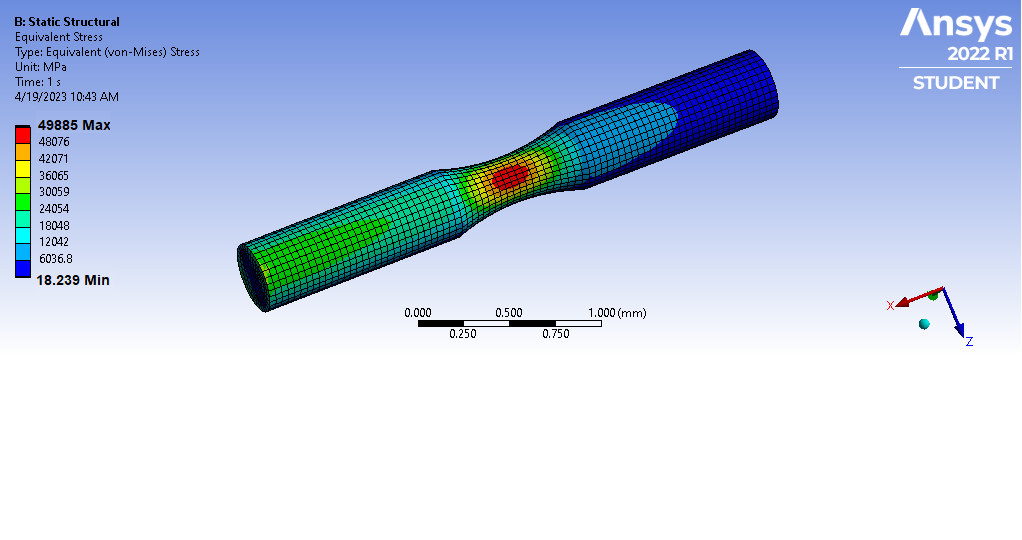
Downloads
Published
How to Cite
Issue
Section
License
Copyright (c) 2023 Imad Bachi Al-Fahad, Hussein kadhim Sharaf, Lina Nasseer Bachache, Nasseer Kassim Bachache

This work is licensed under a Creative Commons Attribution 4.0 International License.
The consolidation and conditions for the transfer of copyright (identification of authorship) is carried out in the License Agreement. In particular, the authors reserve the right to the authorship of their manuscript and transfer the first publication of this work to the journal under the terms of the Creative Commons CC BY license. At the same time, they have the right to conclude on their own additional agreements concerning the non-exclusive distribution of the work in the form in which it was published by this journal, but provided that the link to the first publication of the article in this journal is preserved.
A license agreement is a document in which the author warrants that he/she owns all copyright for the work (manuscript, article, etc.).
The authors, signing the License Agreement with TECHNOLOGY CENTER PC, have all rights to the further use of their work, provided that they link to our edition in which the work was published.
According to the terms of the License Agreement, the Publisher TECHNOLOGY CENTER PC does not take away your copyrights and receives permission from the authors to use and dissemination of the publication through the world's scientific resources (own electronic resources, scientometric databases, repositories, libraries, etc.).
In the absence of a signed License Agreement or in the absence of this agreement of identifiers allowing to identify the identity of the author, the editors have no right to work with the manuscript.
It is important to remember that there is another type of agreement between authors and publishers – when copyright is transferred from the authors to the publisher. In this case, the authors lose ownership of their work and may not use it in any way.