Preparation of wells using an electrohydraulic drill and modeling of heat transfer processes in heat transfer elements of a heat pump
DOI:
https://doi.org/10.15587/1729-4061.2023.285179Keywords:
electrohydraulic drilling, borehole, heat exchanger, discharge voltage, fracture energy, modelingAbstract
The article discusses the use of innovative electrohydraulic technology in the preparation of vertical ground heat exchangers to create heat supply using heat pumps. The discharge energy in the operating range varied E=900÷2600 J. The most economical mode of operation of the electrohydraulic installation is carried out with the following parameters: discharge voltage 30÷51 kV, capacitor bank capacity 2 µF and interelectrode distance 8÷15 mm. It is determined that the optimal energy of destruction of natural materials depends on their thickness. Based on the research, the limits of the electrophysical parameters of the approach were established, at which the concentrated destruction of hard rocks – the main stones ‒ begins. The effective amount of energy for the destruction of stones with a thickness of 53 mm is 900 J. For stones with a thickness of 78 mm, there should be 2600 J. If to increase the energy of the discharges to 1837 J, the process of complete destruction of the stones is underway. Using an electro hydraulic drill, we have prepared vertical wells up to 25 m deep.
In the future, we have installed special temperature sensors along the length of the pipes, inside the well. Using a software product (Temp Keeper), data from temperature sensors are received in real time. This program allows to visually monitor temperature changes occurring at a local point. Temperature and time dependences are also obtained at coolant velocities of 0.2÷0.4 m/s. A significant decrease in the temperature in the well and at the outlet was observed at a coolant velocity of 0.35 m/s for one hour. The study conducted on the basis of the data obtained enables to achieve higher optimal drilling performance compared to conventional installations
Supporting Agency
- This research is funded by the Science Committee of the Ministry of Science and Higher Education of the Republic of Kazakhstan (Grant no. AP14870433).
References
- Song, H. Y., Chen, J. T., Sun, W. L., Li, Y. Y. (2013). Design of Monitor System for JD15 Electro-Hydraulic Controlling Drill Rig. Applied Mechanics and Materials, 385-386, 683–686. doi: https://doi.org/10.4028/www.scientific.net/amm.385-386.683
- Isakov, V. (2016). Justification of adaptable parameters of the cutting drilling tool. University News. North-Caucasian Region. Technical Sciences Series, 1, 76–79. doi: https://doi.org/10.17213/0321-2653-2016-1-76-79
- Proshin, I. A., Proshin, D. I., Proshina, N. N. (2012). Matematicheskaya model' obrazovatel'nogo protsessa v prostranstve vektora znaniy. XXI vek: Itogi proshlogo i problemy nastoyaschego plyus, 3 (07), 153–160.
- Permyakov, P. S., Repin, O. I (2018). Mathematical modeling of physical processes. Mezhdunarodnyy studencheskiy nauchnyy vestnik, 6. Available at: https://s.eduherald.ru/pdf/2018/6/19442.pdf
- Menin, B. (2017). Information measure approach for calculating model uncertainty of physical phenomena. American Journal of Computational and Applied Mathematics, 7 (1), 11–24. Available at: https://www.researchgate.net/publication/315491393_Information_Measure_Approach_for_Calculating_Model_Uncertainty_of_Physical_Phenomena
- Grigoriev, B. S., Eliseev, A. A., Pogarskaya, T. A., Toropov, E. E. (2019). Mathematical modeling of rock crushing and multiphase flow of drilling fluid in well drilling. Journal of Mining Institute, 235 (1), 16–23. doi: https://doi.org/10.31897/pmi.2019.1.16
- Lubega, W. N., Stillwell, A. S. (2019). Analyzing the economic value of thermal power plant cooling water consumption. Water Resources and Economics, 27, 100137. doi: https://doi.org/10.1016/j.wre.2019.01.003
- Su, O. (2015). Performance Evaluation of Button Bits in Coal Measure Rocks by Using Multiple Regression Analyses. Rock Mechanics and Rock Engineering, 49 (2), 541–553. doi: https://doi.org/10.1007/s00603-015-0749-3
- Bazhenov, V. G., Kotov, V. L. (2011). Matematicheskoe modelirovanie nestatsionarnykh protsessov udara i pronikaniya osesimmetrichnykh tel i identifikatsiya svoystv gruntovykh sred. Moscow: Fizmatlit, 208.
- Akhmadiev, B. A., Tatybekov, A., Shuyushbayeva, N. N., Tanasheva, N. K. (2019). Propagation of Pulsed Pressure during Electrohydraulic Drilling. Technical Physics, 64 (4), 455–457. doi: https://doi.org/10.1134/s1063784219040029
- Kusaiynov, K., Nusupbekov, B. R., Sakipova, S. E., Shuyushbayeva, N. N., Khasenov, А. K. (2016). Investigation of the Wear of the Metallic Part of Electrode System of Electrohydraulic Drill. Metallofizika i noveishie tekhnologii, 37 (3), 397–407. doi: https://doi.org/10.15407/mfint.37.03.0397
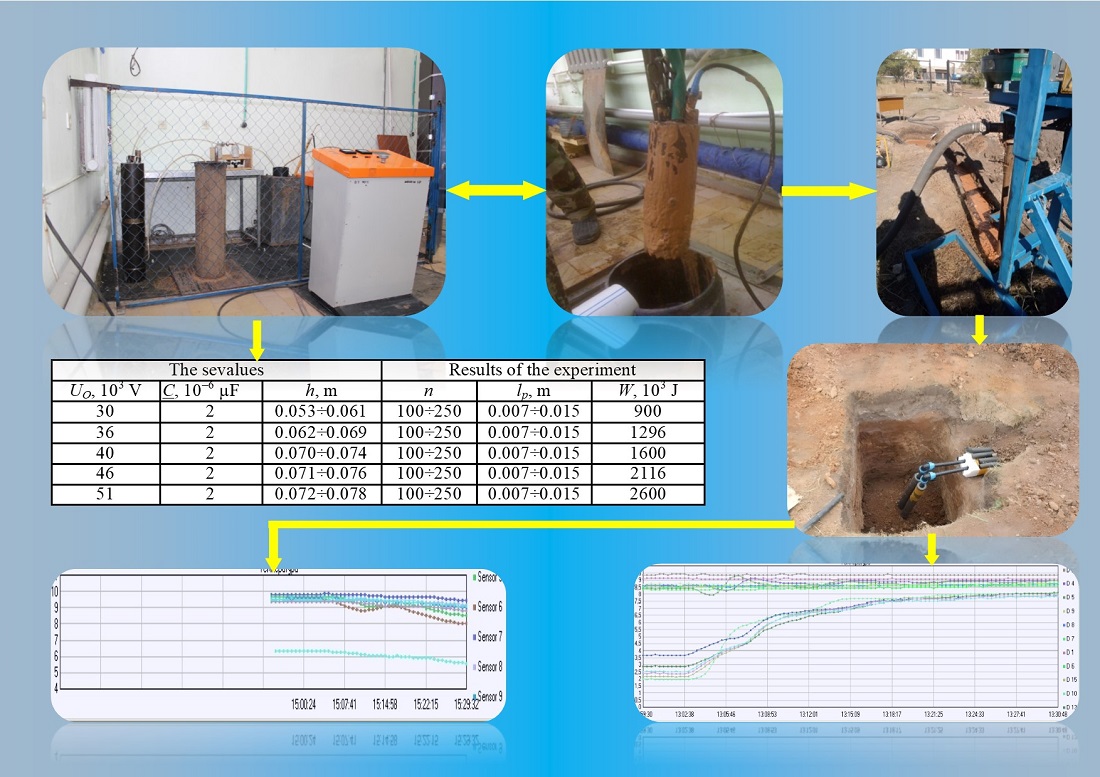
Downloads
Published
How to Cite
Issue
Section
License
Copyright (c) 2023 Bektursin Akhmadiyev, Gaukhar Zhetimekova, Мoldir Duisenbayeva, Adilzada Sharzadin, Bekbolat Nussupbekov

This work is licensed under a Creative Commons Attribution 4.0 International License.
The consolidation and conditions for the transfer of copyright (identification of authorship) is carried out in the License Agreement. In particular, the authors reserve the right to the authorship of their manuscript and transfer the first publication of this work to the journal under the terms of the Creative Commons CC BY license. At the same time, they have the right to conclude on their own additional agreements concerning the non-exclusive distribution of the work in the form in which it was published by this journal, but provided that the link to the first publication of the article in this journal is preserved.
A license agreement is a document in which the author warrants that he/she owns all copyright for the work (manuscript, article, etc.).
The authors, signing the License Agreement with TECHNOLOGY CENTER PC, have all rights to the further use of their work, provided that they link to our edition in which the work was published.
According to the terms of the License Agreement, the Publisher TECHNOLOGY CENTER PC does not take away your copyrights and receives permission from the authors to use and dissemination of the publication through the world's scientific resources (own electronic resources, scientometric databases, repositories, libraries, etc.).
In the absence of a signed License Agreement or in the absence of this agreement of identifiers allowing to identify the identity of the author, the editors have no right to work with the manuscript.
It is important to remember that there is another type of agreement between authors and publishers – when copyright is transferred from the authors to the publisher. In this case, the authors lose ownership of their work and may not use it in any way.