Effect of anodizing on aluminum alloy 2024 with boric sulfate acid in medium 3.5 % NaCl
DOI:
https://doi.org/10.15587/1729-4061.2023.286351Keywords:
Langmuir adsorption, aluminum alloy, acetic acid, inhibition efficiency, surface coverageAbstract
The utilization of metal materials finds widespread applications in various industries, including the aircraft industry, where aluminum alloys are commonly employed. However, metal materials are prone to corrosion under specific conditions, necessitating the implementation of corrosion prevention methods to decelerate the material's corrosion rate. Corrosion is a process in which the quality of metal deteriorates due to environmental influences. An effective approach to inhibit corrosion is through anodizing, which involves applying a protective coating to the metal surface, preventing direct contact with the surrounding environment. In this research, the focus was on studying the corrosion rate of aluminum alloy 2024 using Boric Sulfate Acid Anodizing (BSAA) at 10 volts and immersion times of 10, 15, and 20 minutes, followed by sealing with acetic acid in a corrosive environment containing 3.5 % NaCl. The main goals were to evaluate the effectiveness of anodizing with and without sealing in lowering the rate of aluminum corrosion, to compare the effectiveness of anodizing with and without sealing, and to create adsorption models using Langmuir adsorption. Through the examination of the potentiodynamic approach, it was shown that anodizing had an inhibitory impact that was strengthened by sealing. The maximum efficiency of 76 % was attained after 20 minutes of anodizing and sealing at 10 volts. A correlation value of 0.7487 from the Langmuir adsorption modeling was also obtained, pointing to an advantageous adsorption behavior. This research demonstrates how effectively anodizing for aluminum alloy 2024 works with and without sealing, especially in a 3.5 % NaCl-corrosive environment
Supporting Agency
- This research has been made possible with the valuable support and assistance from the Mechanical Engineering Laboratory at Hasanuddin University. The dedicated contributions and resources provided by the laboratory have contributed significantly to the successful execution and completion of this study.
References
- Merisalu, M., Aarik, L., Kozlova, J., Mändar, H., Tarre, A., Sammelselg, V. (2021). Effective corrosion protection of aluminum alloy AA2024-T3 with novel thin nanostructured oxide coating. Surface and Coatings Technology, 411, 126993. doi: https://doi.org/10.1016/j.surfcoat.2021.126993
- Zhang, J., Zhao, X., Zuo, Y., Xiong, J. (2008). The bonding strength and corrosion resistance of aluminum alloy by anodizing treatment in a phosphoric acid modified boric acid/sulfuric acid bath. Surface and Coatings Technology, 202 (14), 3149–3156. doi: https://doi.org/10.1016/j.surfcoat.2007.10.041
- Saeedikhani, M., Javidi, M., Yazdani, A. (2013). Anodizing of 2024-T3 aluminum alloy in sulfuric-boric-phosphoric acids and its corrosion behavior. Transactions of Nonferrous Metals Society of China, 23 (9), 2551–2559. doi: https://doi.org/10.1016/s1003-6326(13)62767-3
- Elabar, D., La Monica, G. R., Santamaria, M., Di Quarto, F., Skeldon, P., Thompson, G. E. (2017). Anodizing of aluminium and AA 2024-T3 alloy in chromic acid: Effects of sulphate on film growth. Surface and Coatings Technology, 309, 480–489. doi: https://doi.org/10.1016/j.surfcoat.2016.11.108
- Covelo, A., Rodil, S., Nóvoa, X. R., Hernández, M. (2022). Development and characterization of sealed anodizing as a corrosion protection for AA2024-T3 in saline media. Materials Today Communications, 31, 103468. doi: https://doi.org/10.1016/j.mtcomm.2022.103468
- Miramontes, J. C., Gaona Tiburcio, C., García Mata, E., Esneider Alcála, M. Á., Maldonado-Bandala, E., Lara-Banda, M. et al. (2022). Corrosion Resistance of Aluminum Alloy AA2024 with Hard Anodizing in Sulfuric Acid-Free Solution. Materials, 15 (18), 6401. doi: https://doi.org/10.3390/ma15186401
- Schindelholz, E. J., Melia, M. A., Rodelas, J. M. (2021). Corrosion of Additively Manufactured Stainless Steels—Process, Structure, Performance: A Review. Corrosion, 77 (5), 484–503. doi: https://doi.org/10.5006/3741
- Ofoegbu, S. U., Fernandes, F. A. O., Pereira, A. B. (2020). The Sealing Step in Aluminum Anodizing: A Focus on Sustainable Strategies for Enhancing Both Energy Efficiency and Corrosion Resistance. Coatings, 10 (3), 226. doi: https://doi.org/10.3390/coatings10030226
- Wilcox, G. D., Walker, D. E. (2013). Chemical Conversion Coatings. Encyclopedia of Tribology, 359–366. doi: https://doi.org/10.1007/978-0-387-92897-5_1004
- Zhang, L., Thompson, G. E., Curioni, M., Skeldon, P. (2013). Anodizing of Aluminum in Sulfuric Acid/Boric Acid Mixed Electrolyte. Journal of The Electrochemical Society, 160 (4), C179–C184. doi: https://doi.org/10.1149/2.032306jes
- Chamidy, H. N., Ngatin, A., Rosyadi, A. F., Julviana, A., Noviyani, N. (2023). Effect of voltage on the thickness of oxide layer at aluminum alloys for structural bonding using phosphoric sulfuric acid anodizing (PSA) process. International Journal of Mechanical Engineering Technologies and Applications, 4 (1), 69–76. doi: https://doi.org/10.21776/mechta.2023.004.01.8
- Raffin, F., Echouard, J., Volovitch, P. (2023). Influence of the Anodizing Time on the Microstructure and Immersion Stability of Tartaric-Sulfuric Acid Anodized Aluminum Alloys. Metals, 13 (5), 993. doi: https://doi.org/10.3390/met13050993
- Zuchry, M., Renreng, I., Arsyad, H., Arma, L. H., Widyianto, A. (2023). Sealing effect on corrosion resistance of boric sulfuric acid anodizing on AA2024. Eastern-European Journal of Enterprise Technologies, 2 (6 (122)), 43–52. doi: https://doi.org/10.15587/1729-4061.2023.277961
- Naief, T. M., Rashid, K. H. (2011). Comparative Study for Anodizing Aluminum Alloy 1060 by Different Types of Electrolytes Solutions. Engineering & Technology. Available at: https://www.researchgate.net/publication/295911313_Comparative_Study_for_Anodizing_Aluminum_Alloy_1060_by_Different_Types_of_Electrolytes_Solutions
- Zarras, P., Stenger-Smith, J. D. (2015). Smart Inorganic and Organic Pretreatment Coatings for the Inhibition of Corrosion on Metals/Alloys. Intelligent Coatings for Corrosion Control, 59–91. doi: https://doi.org/10.1016/b978-0-12-411467-8.00003-9
- Wan, Y., Wang, H., Zhang, Y., Wang, X., Li, Y. (2018). Study on Anodic Oxidation and Sealing of Aluminum Alloy. International Journal of Electrochemical Science, 13 (2), 2175–2185. doi: https://doi.org/10.20964/2018.02.78
- Hou, F., Hu, B., Tay, S. L., Wang, Y., Xiong, C., Gao, W. (2017). A new, bright and hard aluminum surface produced by anodization. International Journal of Modern Physics B, 31 (16-19), 1744029. doi: https://doi.org/10.1142/s0217979217440295
- Collazo, A., Ezpeleta, I., Figueroa, R., Nóvoa, X. R., Pérez, C. (2020). Corrosion protection properties of anodized AA2024T3 alloy sealing with organic-based species. Progress in Organic Coatings, 147, 105779. doi: https://doi.org/10.1016/j.porgcoat.2020.105779
- Paz Martínez-Viademonte, M., Abrahami, S. T., Hack, T., Burchardt, M., Terryn, H. (2020). A Review on Anodizing of Aerospace Aluminum Alloys for Corrosion Protection. Coatings, 10 (11), 1106. doi: https://doi.org/10.3390/coatings10111106
- Merino, E., Durán, A., Ceré, S., Castro, Y. (2022). Hybrid Epoxy-Alkyl Sol–Gel Coatings Reinforced with SiO2 Nanoparticles for Corrosion Protection of Anodized AZ31B Mg Alloy. Gels, 8 (4), 242. doi: https://doi.org/10.3390/gels8040242
- Aghaei, M., Anbia, M., Salehi, S. (2022). Measurements and modeling of CO2 adsorption behaviors on granular zeolite 13X: Impact of temperature and time of calcination on granules properties in granulation process using organic binders. Environmental Progress & Sustainable Energy, 41 (5). doi: https://doi.org/10.1002/ep.13866
- Hafeznezami, S., Zimmer-Faust, A. G., Dunne, A., Tran, T., Yang, C., Lam, J. R. et al. (2016). Adsorption and desorption of arsenate on sandy sediments from contaminated and uncontaminated saturated zones: Kinetic and equilibrium modeling. Environmental Pollution, 215, 290–301. doi: https://doi.org/10.1016/j.envpol.2016.05.029
- Jedli, H., Jbara, A., Hedfi, H., Bouzgarrou, S., Slimi, K. (2017). Carbon dioxide adsorption isotherm study on various cap rocks in a batch reactor for CO2 sequestration processes. Applied Clay Science, 136, 199–207. doi: https://doi.org/10.1016/j.clay.2016.11.022
- Fedel, M., Franch, J., Rossi, S. (2021). Effect of thickness and sealing treatments on the corrosion protection properties of anodic oxide coatings on AA5005. Surface and Coatings Technology, 408, 126761. doi: https://doi.org/10.1016/j.surfcoat.2020.126761
- Wang, R., Wang, L., He, C., Lu, M., Sun, L. (2019). Studies on the sealing processes of corrosion resistant coatings formed on 2024 aluminium alloy with tartaric-sulfuric anodizing. Surface and Coatings Technology, 360, 369–375. doi: https://doi.org/10.1016/j.surfcoat.2018.12.092
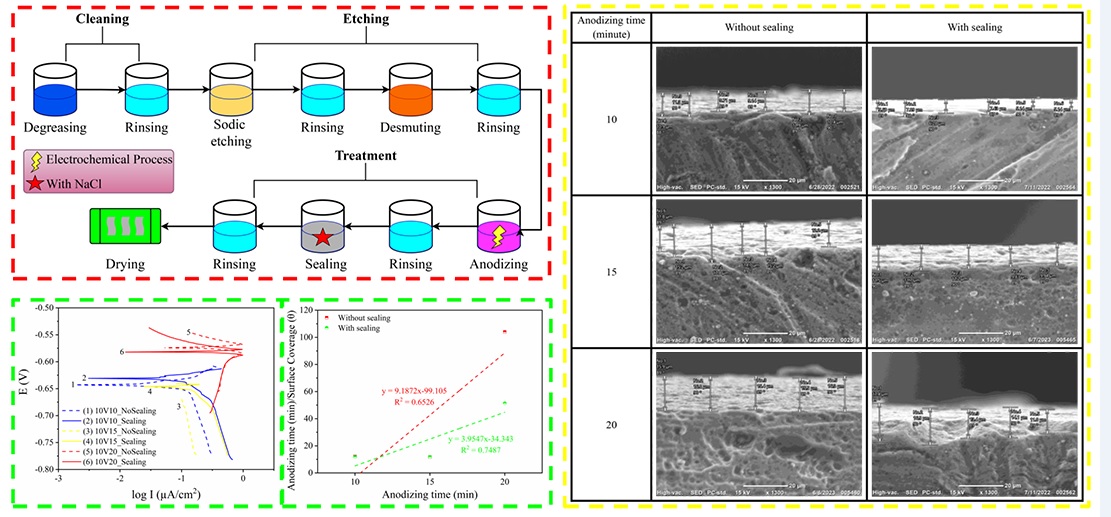
Downloads
Published
How to Cite
Issue
Section
License
Copyright (c) 2023 Muhammad Zuchry, Ilyas Renreng, Hairul Arsyad, Lukmanul Hakim Arma

This work is licensed under a Creative Commons Attribution 4.0 International License.
The consolidation and conditions for the transfer of copyright (identification of authorship) is carried out in the License Agreement. In particular, the authors reserve the right to the authorship of their manuscript and transfer the first publication of this work to the journal under the terms of the Creative Commons CC BY license. At the same time, they have the right to conclude on their own additional agreements concerning the non-exclusive distribution of the work in the form in which it was published by this journal, but provided that the link to the first publication of the article in this journal is preserved.
A license agreement is a document in which the author warrants that he/she owns all copyright for the work (manuscript, article, etc.).
The authors, signing the License Agreement with TECHNOLOGY CENTER PC, have all rights to the further use of their work, provided that they link to our edition in which the work was published.
According to the terms of the License Agreement, the Publisher TECHNOLOGY CENTER PC does not take away your copyrights and receives permission from the authors to use and dissemination of the publication through the world's scientific resources (own electronic resources, scientometric databases, repositories, libraries, etc.).
In the absence of a signed License Agreement or in the absence of this agreement of identifiers allowing to identify the identity of the author, the editors have no right to work with the manuscript.
It is important to remember that there is another type of agreement between authors and publishers – when copyright is transferred from the authors to the publisher. In this case, the authors lose ownership of their work and may not use it in any way.