Identifying the features of structural and phase transformations during the processing of oxide waste from the production of high-speed steel
DOI:
https://doi.org/10.15587/1729-4061.2023.288506Keywords:
carbon thermal recovery, slag of high-speed steels, oxide man-made waste, structural-phase transformationsAbstract
Peculiarities of phase and structural transformations during the carbon-thermal recovery of high-speed steel slag with the production of an alloying additive were investigated. This is necessary to determine the technological indicators that allow reducing the loss of high-value elements during the production and use of the alloying additive. A gradual change in the degree of scale reduction from 32 % to 69 % and 77 % led to an increase in the appearance of the solid solution of alloying elements and carbon in the α-Fe lattice with respect to FeWO4 and Fe3O4. Along with this, Fe3C, FeW3C, WC, VC, V2C, and Cr3C2 were manifested. At the same time, the formation of polyhedral and rounded particles of different chemical composition and the formation of a spongy microstructure was observed. It was determined that the most acceptable degree of recovery is 77 %. At the same time, the degree of reduction of 69 % is also sufficient since due to the residual carbon in the form of carbides, an increased reduction capacity is ensured with additional reduction of the oxide component in the liquid metal during alloying. The spongy microstructure provides relatively fast dissolution compared to standard ferroalloys, which causes a reduction in the total melting time while reducing the resources spent. No phases and compounds characterized by an increased tendency to sublimation were detected in the obtained alloying additive. That is, there is no need to provide additional conditions that prevent the loss of high-value elements during evaporation with the gas phase, which causes an increase in the degree of extraction of alloying elements. The indicators of the obtained alloying additive make it possible to melt alloyed steel in an electric arc furnace with respect to brands whose composition does not have strict restrictions on carbon, while replacing a part of standard ferroalloys.
References
- Petryshchev, A., Milko, D., Borysov, V., Tsymbal, B., Hevko, I., Borysova, S., Semenchuk, A. (2019). Studying the physicalchemical transformations at resourcesaving reduction melting of chrome–nickelcontaining metallurgical waste. Eastern-European Journal of Enterprise Technologies, 2 (12 (98)), 59–64. doi: https://doi.org/10.15587/1729-4061.2019.160755
- Henckens, M. L. C. M., van Ierland, E. C., Driessen, P. P. J., Worrell, E. (2016). Mineral resources: Geological scarcity, market price trends, and future generations. Resources Policy, 49, 102–111. doi: https://doi.org/10.1016/j.resourpol.2016.04.012
- Sekiguchi, N. (2017). Trade specialisation patterns in major steelmaking economies: the role of advanced economies and the implications for rapid growth in emerging market and developing economies in the global steel market. Mineral Economics, 30 (3), 207–227. doi: https://doi.org/10.1007/s13563-017-0110-2
- Mechachti, S, Benchiheub, O., Serrai, S., Shalabi, M. (2013). Preparation of iron Powders by Reduction of Rolling Mill Scale. International Journal of Scientific & Engineering Research, 4 (5), 1467–1472. Available at: https://www.researchgate.net/publication/269463295_Preparation_of_iron_Powders_by_Reduction_of_Rolling_Mill_Scale_International_Journal_of_Scientific_Engineering_Research_Volume_4_Issue_5_May-20131457-1472
- Grigor’ev, S. M., Petrishchev, A. S. (2012). Assessing the phase and structural features of the scale on P6M5Φ3 and P12M3K5Φ2 steel. Steel in Translation, 42 (3), 272–275. doi: https://doi.org/10.3103/s0967091212030059
- Hryhoriev, S., Petryshchev, A., Shyshkanova, G., Zaytseva, T., Frydman, O., Krupey, K. et al. (2018). A study of environmentally friendly recycling of technogenic chromium and nickel containing waste by the method of solid phase extraction. Eastern-European Journal of Enterprise Technologies, 1 (10 (91)), 44–49. doi: https://doi.org/10.15587/1729-4061.2018.121615
- Hryhoriev, S., Petryshchev, A., Belokon’, K., Krupey, K., Yamshinskij, M., Fedorov, G. et al. (2018). Determining the physical-chemical characteristics of the carbon-thermal reduction of scale of tungsten high-speed steels. Eastern-European Journal of Enterprise Technologies, 2 (6 (92)), 10–15. doi: https://doi.org/10.15587/1729-4061.2018.125988
- Zhu, H., Li, Z., Yang, H., Luo, L. (2013). Carbothermic Reduction of MoO3 for Direct Alloying Process. Journal of Iron and Steel Research International, 20 (10), 51–56. doi: https://doi.org/10.1016/s1006-706x(13)60176-4
- Grigor’ev, S. M., Petrishchev, A. S. (2015). Refining metallized molybdenum concentrate by means of a low-temperature plasma-forming mixture. Steel in Translation, 45 (12), 954–958. doi: https://doi.org/10.3103/s0967091215120049
- Baghdasaryan, A. M., Niazyan, O. M., Khachatryan, H. L., Kharatyan, S. L. (2014). DTA/TG study of tungsten oxide and ammonium tungstate reduction by (Mg+C) combined reducers at non-isothermal conditions. International Journal of Refractory Metals and Hard Materials, 43, 216–221. doi: https://doi.org/10.1016/j.ijrmhm.2013.12.003
- Islam, M., Martinez-Duarte, R. (2017). A sustainable approach for tungsten carbide synthesis using renewable biopolymers. Ceramics International, 43 (13), 10546–10553. doi: https://doi.org/10.1016/j.ceramint.2017.05.118
- Chen, S. Y., Chu, M. S. (2014). A new process for the recovery of iron, vanadium, and titanium from vanadium titanomagnetite. The Journal of the Southern African Institute of Mining and Metallurgy, 114, 481–487. Available at: https://www.saimm.co.za/Journal/v114n06p481.pdf
- Zhao, L., Wang, L., Chen, D., Zhao, H., Liu, Y., Qi, T. (2015). Behaviors of vanadium and chromium in coal-based direct reduction of high-chromium vanadium-bearing titanomagnetite concentrates followed by magnetic separation. Transactions of Nonferrous Metals Society of China, 25 (4), 1325–1333. doi: https://doi.org/10.1016/s1003-6326(15)63731-1
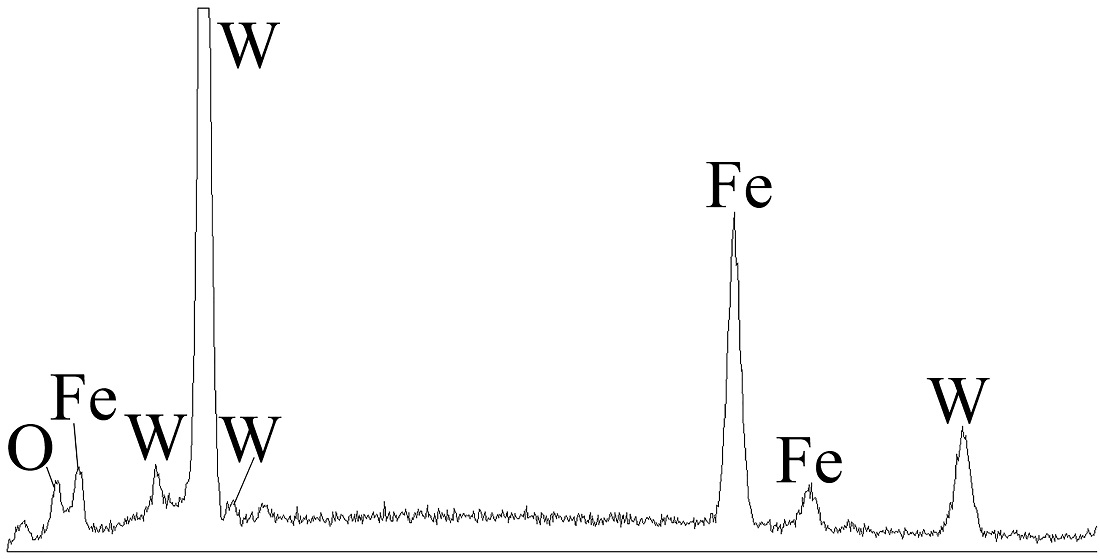
Downloads
Published
How to Cite
Issue
Section
License
Copyright (c) 2023 Vadym Volokh, Anatolii Poliakov, Victor Rebenko, Andrey Andreev, Mykhail Yamshinskij, Ivan Lukianenko, Viacheslav Kurlov, Yevhen Chaplyhin, Nataliya Vlasenko, Dmytro Ivanchenko

This work is licensed under a Creative Commons Attribution 4.0 International License.
The consolidation and conditions for the transfer of copyright (identification of authorship) is carried out in the License Agreement. In particular, the authors reserve the right to the authorship of their manuscript and transfer the first publication of this work to the journal under the terms of the Creative Commons CC BY license. At the same time, they have the right to conclude on their own additional agreements concerning the non-exclusive distribution of the work in the form in which it was published by this journal, but provided that the link to the first publication of the article in this journal is preserved.
A license agreement is a document in which the author warrants that he/she owns all copyright for the work (manuscript, article, etc.).
The authors, signing the License Agreement with TECHNOLOGY CENTER PC, have all rights to the further use of their work, provided that they link to our edition in which the work was published.
According to the terms of the License Agreement, the Publisher TECHNOLOGY CENTER PC does not take away your copyrights and receives permission from the authors to use and dissemination of the publication through the world's scientific resources (own electronic resources, scientometric databases, repositories, libraries, etc.).
In the absence of a signed License Agreement or in the absence of this agreement of identifiers allowing to identify the identity of the author, the editors have no right to work with the manuscript.
It is important to remember that there is another type of agreement between authors and publishers – when copyright is transferred from the authors to the publisher. In this case, the authors lose ownership of their work and may not use it in any way.