Testing a new technique for producing artillery cartridge cases from pipe workpiece by roughing with a friction tool
DOI:
https://doi.org/10.15587/1729-4061.2023.291881Keywords:
workpiece deformation, cartridge case, hollow workpiece, pipe roughing, internal defects, FEMAbstract
The object of this study is the technological process of manufacturing parts such as artillery shells using pressure treatment methods. The work is aimed at solving the current scientific and technical task to improve the technological processes for manufacturing parts such as cartridge cases based on the use of a tangential rolling operation with a friction tool, which ensures the production of hollow products with a bottom. Using the finite element method, modeling of the bottom rolling processes was carried out, which made it possible to establish the effective geometry of the processed workpieces and their heating temperature. Recommendations have been devised for the design of new technological processes for roughing bottoms, which consist of determining the wall thickness of the workpiece before deformation, the heating temperature of the workpieces, and the amount of supply of the workpiece to the friction tool. The resulting recommendations were verified by experimental studies. Roughing of spherical bottoms should be carried out for pipes with a relative wall thickness (D/s) in the range of 15...20, the homologous heating temperature should be 0.8, and the relative feed of the workpiece into the friction tool should be 0.9. Testing the established relationships under laboratory conditions confirmed the recommendations for changing the shape of spherical bottoms during the roughing process. The results of metallographic studies on full-scale products confirm the results of the theoretical study. It is recommended to use this technique for products that have an axial hole (artillery shells, hydraulic cylinders, etc.), which will allow removing axial defects in the bottom after drilling the axial hole. The results could be used at machine-building enterprises in the manufacture of dual-use parts
References
- Markov, O., Gerasimenko, O., Aliieva, L., Shapoval, A., Kosilov, M. (2019). Development of a new process for expanding stepped tapered rings. Eastern-European Journal of Enterprise Technologies, 2 (1 (98)), 39–46. doi: https://doi.org/10.15587/1729-4061.2019.160395
- Markov, O., Gerasimenko, O., Khvashchynskyi, A., Zhytnikov, R., Puzyr, R. (2019). Modeling the techological process of pipe forging without a mandrel. Eastern-European Journal of Enterprise Technologies, 3 (1 (99)), 42–48. doi: https://doi.org/10.15587/1729-4061.2019.167077
- Hrudkina, N., Aliieva, L., Abhari, P., Markov, O., Sukhovirska, L. (2019). Investigating the process of shrinkage depression formation at the combined radial-backward extrusion of parts with a flange. Eastern-European Journal of Enterprise Technologies, 5 (1 (101)), 49–57. doi: https://doi.org/10.15587/1729-4061.2019.179232
- Markov, O., Panov, V., Karnaukh, S., Khvashchynskyi, A., Zhytnikov, R., Kukhar, V. et al. (2020). Determining the deformed state in the process of rolling conical shells with a flange. Eastern-European Journal of Enterprise Technologies, 6 (1 (108)), 34–41. doi: https://doi.org/10.15587/1729-4061.2020.216523
- Hrudkina, N., Aliiev, I., Markov, O., Savchenko, I., Sukhovirska, L., Tahan, L. (2021). Designing a kinematic module with rounding to model the processes of combined radial-longitudinal extrusion involving a tool whose configuration is complex. Eastern-European Journal of Enterprise Technologies, 2 (1 (110)), 81–89. doi: https://doi.org/10.15587/1729-4061.2021.227120
- Wu, Y., Dong, X., Yu, Q. (2015). Upper bound analysis of axial metal flow inhomogeneity in radial forging process. International Journal of Mechanical Sciences, 93, 102–110. doi: https://doi.org/10.1016/j.ijmecsci.2015.01.012
- Sizek, H. W. (2005). Radial Forging. Metalworking: Bulk Forming, 172–178. doi: https://doi.org/10.31399/asm.hb.v14a.a0003984
- Markov, O., Kosilov, M., Panov, V., Kukhar, V., Karnaukh, S., Ragulina, N. et al. (2019). Modeling and improvement of saddling a stepped hollow workpiece with a profiled tool. Eastern-European Journal of Enterprise Technologies, 6 (1), 19–25. doi: https://doi.org/10.15587/1729-4061.2019.183663
- Ghaei, A., Movahhedy, M. R., Karimi Taheri, A. (2008). Finite element modelling simulation of radial forging of tubes without mandrel. Materials & Design, 29 (4), 867–872. doi: https://doi.org/10.1016/j.matdes.2007.03.013
- Fan, L., Wang, Z., Wang, H. (2014). 3D finite element modeling and analysis of radial forging processes. Journal of Manufacturing Processes, 16 (2), 329–334. doi: https://doi.org/10.1016/j.jmapro.2014.01.005
- Aliieva, L., Hrudkina, N., Aliiev, I., Zhbankov, I., Markov, O. (2020). Effect of the tool geometry on the force mode of the combined radial-direct extrusion with compression. Eastern-European Journal of Enterprise Technologies, 2 (1 (104)), 15–22. doi: https://doi.org/10.15587/1729-4061.2020.198433
- Burkin, S. P., Korshunov, E. A., Kolmogorov, V. L., Babailov, N. A., Nalesnik, V. M. (1996). A vertical automated forging center for the plastic deformation of continuously-cast ingots. Journal of Materials Processing Technology, 58 (2-3), 170–173. doi: https://doi.org/10.1016/0924-0136(95)02146-9
- Sanjari, M., Saidi, P., Karimi Taheri, A., Hossein-Zadeh, M. (2012). Determination of strain field and heterogeneity in radial forging of tube using finite element method and microhardness test. Materials & Design, 38, 147–153. doi: https://doi.org/10.1016/j.matdes.2012.01.048
- Knauf, F., Nieschwitz, P.-J., Holl, A., Pelster, H., Vest, R. (2011). Latest Development in Railway Axle and Thick-Walled Tube forging on a Hydraulic Radial Forging Machine Type SMX. 18th International Forgemasters Meeting. Market and Technical Proceedings. Pittsburgh, 215–220.
- Koppensteiner, R., Tang, Z. (2011). Optimizing Tooling And Pass Design For Effectiveness On Forged Product. 18th International Forgemasters Meeting. Market and Technical Proceedings. Pittsburgh, 225–229.
- Sheu, J.-J., Lin, S.-Y., Yu, C.-H. (2014). Optimum Die Design for Single Pass Steel Tube Drawing with Large Strain Deformation. Procedia Engineering, 81, 688–693. doi: https://doi.org/10.1016/j.proeng.2014.10.061
- Hrudkina, N., Aliieva, L., Markov, O., Malii, K., Sukhovirska, L., Kuznetsov, M. (2020). Predicting the shape formation of parts with a flange and an axial protrusion in the process of combined aligned radial-direct extrusion. Eastern-European Journal of Enterprise Technologies, 5 (1 (107)), 110–117. doi: https://doi.org/10.15587/1729-4061.2020.212018
- Li, Y., He, T., Zeng, Z. (2013). Numerical simulation and experimental study on the tube sinking of a thin-walled copper tube with axially inner micro grooves by radial forging. Journal of Materials Processing Technology, 213 (6), 987–996. doi: https://doi.org/10.1016/j.jmatprotec.2012.12.002
- Li, Y., Huang, J., Huang, G., Wang, W., Chen, J., Zeng, Z. (2014). Comparison of radial forging between the two- and three-split dies of a thin-walled copper tube during tube sinking. Materials & Design (1980-2015), 56, 822–832. doi: https://doi.org/10.1016/j.matdes.2013.11.079
- Hrudkina, N., Aliieva, L., Markov, O., Kartamyshev, D., Shevtsov, S., Kuznetsov, M. (2020). Modeling the process of radial-direct extrusion with expansion using a triangular kinematic module. Eastern-European Journal of Enterprise Technologies, 3 (1 (105)), 17–22. doi: https://doi.org/10.15587/1729-4061.2020.203989
- Pantalé, O., Gueye, B. (2013). Influence of the Constitutive Flow Law in FEM Simulation of the Radial Forging Process. Journal of Engineering, 2013, 1–8. doi: https://doi.org/10.1155/2013/231847
- Kowalski, J., Hoderny, B., Malinowski, Z. (1987). Experimental investigation of the strain state in the ring-forging process. Journal of Mechanical Working Technology, 14 (3), 309–324. doi: https://doi.org/10.1016/0378-3804(87)90016-7
- Zhang, Q., Jin, K., mu, D., Ma, P., Tian, J. (2014). Rotary Swaging Forming Process of Tube Workpieces. Procedia Engineering, 81, 2336–2341. doi: https://doi.org/10.1016/j.proeng.2014.10.330
- Wang, Z. G. (2011). The theory analysis and numerical simulation for the radial forging process of gun barrel. Nanjing University of Science and Technology, 28–30.
- Linardon, C., Favier, D., Chagnon, G., Gruez, B. (2014). A conical mandrel tube drawing test designed to assess failure criteria. Journal of Materials Processing Technology, 214 (2), 347–357. doi: https://doi.org/10.1016/j.jmatprotec.2013.09.021
- Khayatzadeh, S., Poursina, M., Golestanian, H. (2008). A Simulation of Hollow and Solid Products in Multi-Pass Hot Radial Forging Using 3D-FEM Method. International Journal of Material Forming, 1 (S1), 371–374. doi: https://doi.org/10.1007/s12289-008-0072-6
- Özer, A., Sekiguchi, A., Arai, H. (2012). Experimental implementation and analysis of robotic metal spinning with enhanced trajectory tracking algorithms. Robotics and Computer-Integrated Manufacturing, 28 (4), 539–550. doi: https://doi.org/10.1016/j.rcim.2011.12.003
- Polyblank, J. A., Allwood, J. M. (2015). Parametric toolpath design in metal spinning. CIRP Annals, 64 (1), 301–304. doi: https://doi.org/10.1016/j.cirp.2015.04.077
- Music, O., Allwood, J. M., Kawai, K. (2010). A review of the mechanics of metal spinning. Journal of Materials Processing Technology, 210 (1), 3–23. doi: https://doi.org/10.1016/j.jmatprotec.2009.08.021
- Automatisсhe Schwenkformmaschine Modell AST (1989). Lizenz Autospin/Kieserling Kieserling & Albrecht GmbH & Со. KG.
- Palter, Н. (1982). Herstellung von Gasflasahen und Stobdampferrohren auf einer automatischen Rohrschliebmosehine. Blech-Rohre-Profile, 11, 529–530.
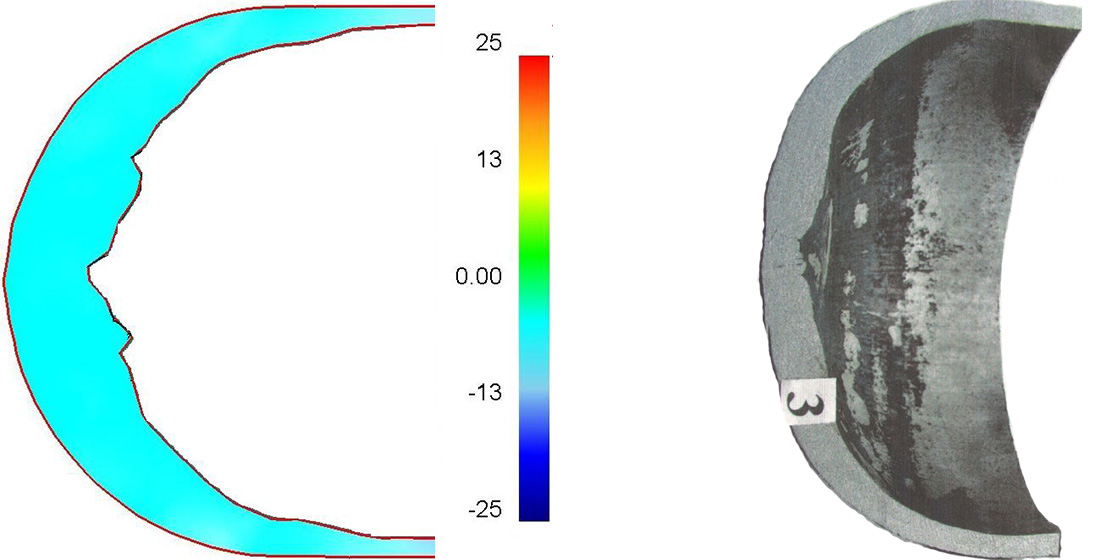
Downloads
Published
How to Cite
Issue
Section
License
Copyright (c) 2023 Oleg Markov, Serhii Shevtsov, Natalia Hrudkina, Vitalii Molodetskyi, Anton Musorin, Volodymyr Zinskyi

This work is licensed under a Creative Commons Attribution 4.0 International License.
The consolidation and conditions for the transfer of copyright (identification of authorship) is carried out in the License Agreement. In particular, the authors reserve the right to the authorship of their manuscript and transfer the first publication of this work to the journal under the terms of the Creative Commons CC BY license. At the same time, they have the right to conclude on their own additional agreements concerning the non-exclusive distribution of the work in the form in which it was published by this journal, but provided that the link to the first publication of the article in this journal is preserved.
A license agreement is a document in which the author warrants that he/she owns all copyright for the work (manuscript, article, etc.).
The authors, signing the License Agreement with TECHNOLOGY CENTER PC, have all rights to the further use of their work, provided that they link to our edition in which the work was published.
According to the terms of the License Agreement, the Publisher TECHNOLOGY CENTER PC does not take away your copyrights and receives permission from the authors to use and dissemination of the publication through the world's scientific resources (own electronic resources, scientometric databases, repositories, libraries, etc.).
In the absence of a signed License Agreement or in the absence of this agreement of identifiers allowing to identify the identity of the author, the editors have no right to work with the manuscript.
It is important to remember that there is another type of agreement between authors and publishers – when copyright is transferred from the authors to the publisher. In this case, the authors lose ownership of their work and may not use it in any way.