Перевірка нового способу отримання артелерійських гільз з трубної заготовки обкатуванням інструментом тертя
DOI:
https://doi.org/10.15587/1729-4061.2023.291881Ключові слова:
деформація заготовки, гільза, порожниста заготовка, обкатка труб, внутрішні дефекти, МСЕАнотація
Об’єкт дослідження – технологічний процес виготовлення деталей типу артилерійських гільз методами обробки тиском. Робота спрямована на розв'язання актуальної науково-технічної проблеми вдосконалення технологічних процесів виготовлення деталей типу гільз на основі використання операції тангенціального обкатування інструментом тертя, що забезпечує отримання порожнистих виробів із дном. Методом скінченних елементів проведено моделювання процесів обкатки днищ, що дало змогу встановити ефективну геометрію оброблюваних заготовок і температуру їх нагрівання. Встановлено рекомендації щодо проектування нових технологічних процесів обкатки днищ, які полягають у визначенні товщини стінки заготовки перед деформацією, температури нагріву заготовок, а також величини подачі заготовки в інструмент тертя. Отримані рекомендації перевірені експериментальними дослідженнями. Обкатку сферичних днищ слід проводити для труб із відносною товщиною стінки (D/s) у діапазоні 15...20, гомологічна температура нагріву повинна становити 0,8, а відносна подача заготовки до інструменту тертя повинна бути 0,9. Апробація встановлених співвідношень у лабораторних умовах підтвердила отримані рекомендації щодо формозміни сферичних днищ у процесі обкатки. Результати металографічних досліджень на натурних виробах підтверджують результати теоретичного дослідження. Рекомендується використовувати цей спосіб для виробів, що мають осьовий отвір (артилерійські гільзи, гідроциліндри та ін), що дозволить видалити осьові дефекти в днищі після висвердлювання осьового отвору. Отримані результати можна використовувати на машинобудівних підприємствах під час виготовлення деталей подвійного призначення
Посилання
- Markov, O., Gerasimenko, O., Aliieva, L., Shapoval, A., Kosilov, M. (2019). Development of a new process for expanding stepped tapered rings. Eastern-European Journal of Enterprise Technologies, 2 (1 (98)), 39–46. doi: https://doi.org/10.15587/1729-4061.2019.160395
- Markov, O., Gerasimenko, O., Khvashchynskyi, A., Zhytnikov, R., Puzyr, R. (2019). Modeling the techological process of pipe forging without a mandrel. Eastern-European Journal of Enterprise Technologies, 3 (1 (99)), 42–48. doi: https://doi.org/10.15587/1729-4061.2019.167077
- Hrudkina, N., Aliieva, L., Abhari, P., Markov, O., Sukhovirska, L. (2019). Investigating the process of shrinkage depression formation at the combined radial-backward extrusion of parts with a flange. Eastern-European Journal of Enterprise Technologies, 5 (1 (101)), 49–57. doi: https://doi.org/10.15587/1729-4061.2019.179232
- Markov, O., Panov, V., Karnaukh, S., Khvashchynskyi, A., Zhytnikov, R., Kukhar, V. et al. (2020). Determining the deformed state in the process of rolling conical shells with a flange. Eastern-European Journal of Enterprise Technologies, 6 (1 (108)), 34–41. doi: https://doi.org/10.15587/1729-4061.2020.216523
- Hrudkina, N., Aliiev, I., Markov, O., Savchenko, I., Sukhovirska, L., Tahan, L. (2021). Designing a kinematic module with rounding to model the processes of combined radial-longitudinal extrusion involving a tool whose configuration is complex. Eastern-European Journal of Enterprise Technologies, 2 (1 (110)), 81–89. doi: https://doi.org/10.15587/1729-4061.2021.227120
- Wu, Y., Dong, X., Yu, Q. (2015). Upper bound analysis of axial metal flow inhomogeneity in radial forging process. International Journal of Mechanical Sciences, 93, 102–110. doi: https://doi.org/10.1016/j.ijmecsci.2015.01.012
- Sizek, H. W. (2005). Radial Forging. Metalworking: Bulk Forming, 172–178. doi: https://doi.org/10.31399/asm.hb.v14a.a0003984
- Markov, O., Kosilov, M., Panov, V., Kukhar, V., Karnaukh, S., Ragulina, N. et al. (2019). Modeling and improvement of saddling a stepped hollow workpiece with a profiled tool. Eastern-European Journal of Enterprise Technologies, 6 (1), 19–25. doi: https://doi.org/10.15587/1729-4061.2019.183663
- Ghaei, A., Movahhedy, M. R., Karimi Taheri, A. (2008). Finite element modelling simulation of radial forging of tubes without mandrel. Materials & Design, 29 (4), 867–872. doi: https://doi.org/10.1016/j.matdes.2007.03.013
- Fan, L., Wang, Z., Wang, H. (2014). 3D finite element modeling and analysis of radial forging processes. Journal of Manufacturing Processes, 16 (2), 329–334. doi: https://doi.org/10.1016/j.jmapro.2014.01.005
- Aliieva, L., Hrudkina, N., Aliiev, I., Zhbankov, I., Markov, O. (2020). Effect of the tool geometry on the force mode of the combined radial-direct extrusion with compression. Eastern-European Journal of Enterprise Technologies, 2 (1 (104)), 15–22. doi: https://doi.org/10.15587/1729-4061.2020.198433
- Burkin, S. P., Korshunov, E. A., Kolmogorov, V. L., Babailov, N. A., Nalesnik, V. M. (1996). A vertical automated forging center for the plastic deformation of continuously-cast ingots. Journal of Materials Processing Technology, 58 (2-3), 170–173. doi: https://doi.org/10.1016/0924-0136(95)02146-9
- Sanjari, M., Saidi, P., Karimi Taheri, A., Hossein-Zadeh, M. (2012). Determination of strain field and heterogeneity in radial forging of tube using finite element method and microhardness test. Materials & Design, 38, 147–153. doi: https://doi.org/10.1016/j.matdes.2012.01.048
- Knauf, F., Nieschwitz, P.-J., Holl, A., Pelster, H., Vest, R. (2011). Latest Development in Railway Axle and Thick-Walled Tube forging on a Hydraulic Radial Forging Machine Type SMX. 18th International Forgemasters Meeting. Market and Technical Proceedings. Pittsburgh, 215–220.
- Koppensteiner, R., Tang, Z. (2011). Optimizing Tooling And Pass Design For Effectiveness On Forged Product. 18th International Forgemasters Meeting. Market and Technical Proceedings. Pittsburgh, 225–229.
- Sheu, J.-J., Lin, S.-Y., Yu, C.-H. (2014). Optimum Die Design for Single Pass Steel Tube Drawing with Large Strain Deformation. Procedia Engineering, 81, 688–693. doi: https://doi.org/10.1016/j.proeng.2014.10.061
- Hrudkina, N., Aliieva, L., Markov, O., Malii, K., Sukhovirska, L., Kuznetsov, M. (2020). Predicting the shape formation of parts with a flange and an axial protrusion in the process of combined aligned radial-direct extrusion. Eastern-European Journal of Enterprise Technologies, 5 (1 (107)), 110–117. doi: https://doi.org/10.15587/1729-4061.2020.212018
- Li, Y., He, T., Zeng, Z. (2013). Numerical simulation and experimental study on the tube sinking of a thin-walled copper tube with axially inner micro grooves by radial forging. Journal of Materials Processing Technology, 213 (6), 987–996. doi: https://doi.org/10.1016/j.jmatprotec.2012.12.002
- Li, Y., Huang, J., Huang, G., Wang, W., Chen, J., Zeng, Z. (2014). Comparison of radial forging between the two- and three-split dies of a thin-walled copper tube during tube sinking. Materials & Design (1980-2015), 56, 822–832. doi: https://doi.org/10.1016/j.matdes.2013.11.079
- Hrudkina, N., Aliieva, L., Markov, O., Kartamyshev, D., Shevtsov, S., Kuznetsov, M. (2020). Modeling the process of radial-direct extrusion with expansion using a triangular kinematic module. Eastern-European Journal of Enterprise Technologies, 3 (1 (105)), 17–22. doi: https://doi.org/10.15587/1729-4061.2020.203989
- Pantalé, O., Gueye, B. (2013). Influence of the Constitutive Flow Law in FEM Simulation of the Radial Forging Process. Journal of Engineering, 2013, 1–8. doi: https://doi.org/10.1155/2013/231847
- Kowalski, J., Hoderny, B., Malinowski, Z. (1987). Experimental investigation of the strain state in the ring-forging process. Journal of Mechanical Working Technology, 14 (3), 309–324. doi: https://doi.org/10.1016/0378-3804(87)90016-7
- Zhang, Q., Jin, K., mu, D., Ma, P., Tian, J. (2014). Rotary Swaging Forming Process of Tube Workpieces. Procedia Engineering, 81, 2336–2341. doi: https://doi.org/10.1016/j.proeng.2014.10.330
- Wang, Z. G. (2011). The theory analysis and numerical simulation for the radial forging process of gun barrel. Nanjing University of Science and Technology, 28–30.
- Linardon, C., Favier, D., Chagnon, G., Gruez, B. (2014). A conical mandrel tube drawing test designed to assess failure criteria. Journal of Materials Processing Technology, 214 (2), 347–357. doi: https://doi.org/10.1016/j.jmatprotec.2013.09.021
- Khayatzadeh, S., Poursina, M., Golestanian, H. (2008). A Simulation of Hollow and Solid Products in Multi-Pass Hot Radial Forging Using 3D-FEM Method. International Journal of Material Forming, 1 (S1), 371–374. doi: https://doi.org/10.1007/s12289-008-0072-6
- Özer, A., Sekiguchi, A., Arai, H. (2012). Experimental implementation and analysis of robotic metal spinning with enhanced trajectory tracking algorithms. Robotics and Computer-Integrated Manufacturing, 28 (4), 539–550. doi: https://doi.org/10.1016/j.rcim.2011.12.003
- Polyblank, J. A., Allwood, J. M. (2015). Parametric toolpath design in metal spinning. CIRP Annals, 64 (1), 301–304. doi: https://doi.org/10.1016/j.cirp.2015.04.077
- Music, O., Allwood, J. M., Kawai, K. (2010). A review of the mechanics of metal spinning. Journal of Materials Processing Technology, 210 (1), 3–23. doi: https://doi.org/10.1016/j.jmatprotec.2009.08.021
- Automatisсhe Schwenkformmaschine Modell AST (1989). Lizenz Autospin/Kieserling Kieserling & Albrecht GmbH & Со. KG.
- Palter, Н. (1982). Herstellung von Gasflasahen und Stobdampferrohren auf einer automatischen Rohrschliebmosehine. Blech-Rohre-Profile, 11, 529–530.
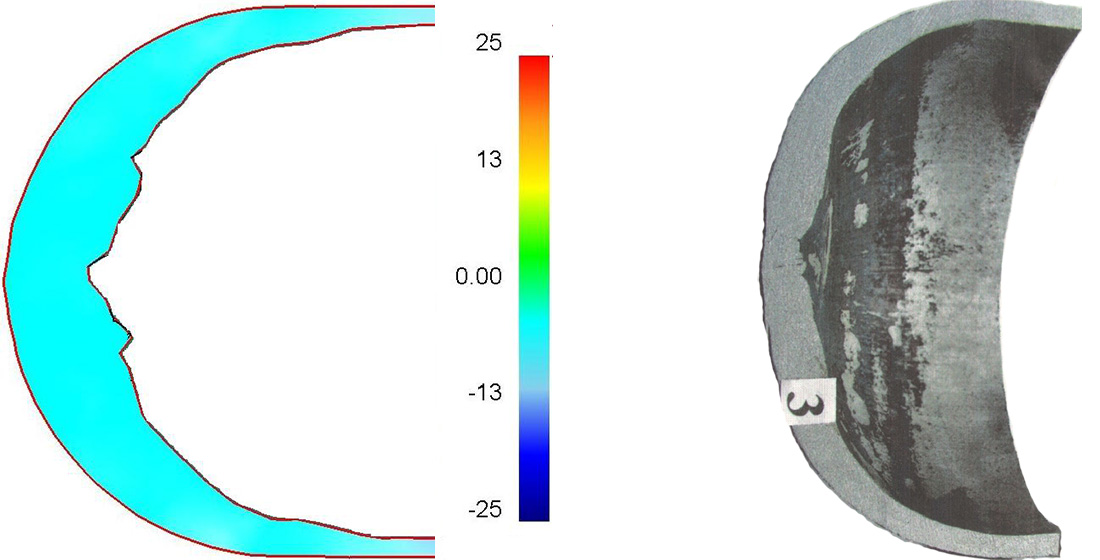
##submission.downloads##
Опубліковано
Як цитувати
Номер
Розділ
Ліцензія
Авторське право (c) 2023 Oleg Markov, Serhii Shevtsov, Natalia Hrudkina, Vitalii Molodetskyi, Anton Musorin, Volodymyr Zinskyi

Ця робота ліцензується відповідно до Creative Commons Attribution 4.0 International License.
Закріплення та умови передачі авторських прав (ідентифікація авторства) здійснюється у Ліцензійному договорі. Зокрема, автори залишають за собою право на авторство свого рукопису та передають журналу право першої публікації цієї роботи на умовах ліцензії Creative Commons CC BY. При цьому вони мають право укладати самостійно додаткові угоди, що стосуються неексклюзивного поширення роботи у тому вигляді, в якому вона була опублікована цим журналом, але за умови збереження посилання на першу публікацію статті в цьому журналі.
Ліцензійний договір – це документ, в якому автор гарантує, що володіє усіма авторськими правами на твір (рукопис, статтю, тощо).
Автори, підписуючи Ліцензійний договір з ПП «ТЕХНОЛОГІЧНИЙ ЦЕНТР», мають усі права на подальше використання свого твору за умови посилання на наше видання, в якому твір опублікований. Відповідно до умов Ліцензійного договору, Видавець ПП «ТЕХНОЛОГІЧНИЙ ЦЕНТР» не забирає ваші авторські права та отримує від авторів дозвіл на використання та розповсюдження публікації через світові наукові ресурси (власні електронні ресурси, наукометричні бази даних, репозитарії, бібліотеки тощо).
За відсутності підписаного Ліцензійного договору або за відсутністю вказаних в цьому договорі ідентифікаторів, що дають змогу ідентифікувати особу автора, редакція не має права працювати з рукописом.
Важливо пам’ятати, що існує і інший тип угоди між авторами та видавцями – коли авторські права передаються від авторів до видавця. В такому разі автори втрачають права власності на свій твір та не можуть його використовувати в будь-який спосіб.