Development of plant integrity inspection on the API 5L X65 material under humid conditions: emerging fitness for service assessment approach
DOI:
https://doi.org/10.15587/1729-4061.2024.297618Keywords:
corrosion mitigation, external corrosion, flowline-trunkline corrosion mitigations, plant integrity, ultrasonic inspectionAbstract
This work reports the development and corresponding monitoring of pipeline integrity inspection in the arid zone, which typically experiences external corrosion. The recent method poses the challenge which indaquate to synchronize the internal and external corrosion monitoring of API 5L X65 material trunklines and flowlines owing to imperfect types of inspection on the external progressive damage only. Red-clay soil, soil porosity, oxygen content, and moisture become critical parameters for controlling the corrosion of the above conditions. The combination of ultrasonic guided wave test, visual inspection, and design life calculation is implemented to address the above challenges. Based on the results, trunkline B (12-inch) is more severe than A (18-inch), with the shorter measured remaining thickness and remaining life of 4.35 mm and 1.9 years. External corrosion and visual inspection results show that sand threatens corrosion. The external corrosion product is evident at the 3 and 6 o’clock positions, corresponding to the exposure of the buried pipelines to moisture. The maximum metal loss in the trunk is 14.5 %, which confirms the environment of trunkline B. The internal corrosion has little effect on the integrity of the plant.
Despite the three fluid phases inside the flowlines and trunklines, the measured corrosion rate on the coupon is relatively lower. The highest recorded corrosion rate is 0.443 mmpy, while the contribution to internal corrosion from the rest of the monitor well is insufficient. This research is designed to model the strategy to utilize instrumentation of Ultrasonic tests and human intervention in corrosion mitigation
References
- Vanaei, H. R., Eslami, A., Egbewande, A. (2017). A review on pipeline corrosion, in-line inspection (ILI), and corrosion growth rate models. International Journal of Pressure Vessels and Piping, 149, 43–54. https://doi.org/10.1016/j.ijpvp.2016.11.007
- Zangeneh, Sh., Lashgari, H. R., Sharifi, H. R. (2020). Fitness-for-service assessment and failure analysis of AISI 304 demineralized-water (DM) pipeline weld crack. Engineering Failure Analysis, 107, 104210. https://doi.org/10.1016/j.engfailanal.2019.104210
- Tan, B., He, J., Zhang, S., Xu, C., Chen, S., Liu, H., Li, W. (2021). Insight into anti-corrosion nature of Betel leaves water extracts as the novel and eco-friendly inhibitors. Journal of Colloid and Interface Science, 585, 287–301. https://doi.org/10.1016/j.jcis.2020.11.059
- Verma, C., Ebenso, E. E., Quraishi, M. A. (2017). Corrosion inhibitors for ferrous and non-ferrous metals and alloys in ionic sodium chloride solutions: A review. Journal of Molecular Liquids, 248, 927–942. https://doi.org/10.1016/j.molliq.2017.10.094
- Aditiyawarman, T., Soedarsono, J. W., Kaban, A. P. S., Riastuti, R., Rahmadani, H. (2022). The Study of Artificial Intelligent in Risk-Based Inspection Assessment and Screening: A Study Case of Inline Inspection. ASCE-ASME Journal of Risk and Uncertainty in Engineering Systems, Part B: Mechanical Engineering, 9 (1). https://doi.org/10.1115/1.4054969
- Ma, Q., Tian, G., Zeng, Y., Li, R., Song, H., Wang, Z. et al. (2021). Pipeline In-Line Inspection Method, Instrumentation and Data Management. Sensors, 21 (11), 3862. https://doi.org/10.3390/s21113862
- Pan, E., Rogers, J., Datta, S. K., Shah, A. H. (1999). Mode selection of guided waves for ultrasonic inspection of gas pipelines with thick coating. Mechanics of Materials, 31 (3), 165–174. https://doi.org/10.1016/s0167-6636(98)00057-x
- Zang, X., Xu, Z.-D., Lu, H., Zhu, C., Zhang, Z. (2023). Ultrasonic guided wave techniques and applications in pipeline defect detection: A review. International Journal of Pressure Vessels and Piping, 206, 105033. https://doi.org/10.1016/j.ijpvp.2023.105033
- Black, M., Heinks, C., Cramer, R. (2022). Real-Time Well Performance Measurement Using Non-Intrusive Clamp-On Measurement Technique. SPE Annual Technical Conference and Exhibition. https://doi.org/10.2118/210126-ms
- Shahriar, A., Sadiq, R., Tesfamariam, S. (2012). Risk analysis for oil & gas pipelines: A sustainability assessment approach using fuzzy based bow-tie analysis. Journal of Loss Prevention in the Process Industries, 25 (3), 505–523. https://doi.org/10.1016/j.jlp.2011.12.007
- Chen, J., Ji, L., Song, J. (2022). Study of Crevice Corrosion Behavior and Cathodic Protection of Carbon Steel Reinforcement in Concrete. International Journal of Electrochemical Science, 17 (1), 220140. https://doi.org/10.20964/2022.01.01
- Rodríguez-Mariscal, J. D., Canivell, J., Solís, M. (2021). Evaluating the performance of sonic and ultrasonic tests for the inspection of rammed earth constructions. Construction and Building Materials, 299, 123854. https://doi.org/10.1016/j.conbuildmat.2021.123854
- Kaban, A., Mayangsari, W., Anwar, M., Maksum, A., Aditiyawarman, T., Soedarsono, J. et al. (2022). Unraveling the study of liquid smoke from rice husks as a green corrosion inhibitor in mild steel under 1 M HCl. Eastern-European Journal of Enterprise Technologies, 5 (6 (119)), 41–53. https://doi.org/10.15587/1729-4061.2022.265086
- Kaban, A. P. S., Soedarsono, J. W., Mayangsari, W., Anwar, M. S., Maksum, A., Ridhova, A., Riastuti, R. (2023). Insight on Corrosion Prevention of C1018 in 1.0 M Hydrochloric Acid Using Liquid Smoke of Rice Husk Ash: Electrochemical, Surface Analysis, and Deep Learning Studies. Coatings, 13 (1), 136. https://doi.org/10.3390/coatings13010136
- Kaban, A. P. S., Ridhova, A., Priyotomo, G., Elya, B., Maksum, A., Sadeli, Y. et al. (2021). Development of white tea extract as green corrosion inhibitor in mild steel under 1 M hydrochloric acid solution. Eastern-European Journal of Enterprise Technologies, 2 (6 (110)), 6–20. https://doi.org/10.15587/1729-4061.2021.224435
- NACE SP0169. Standard Recomended Practice: Control of External Corrosion on Underground or Submerged Metallic Piping Systems (2002). NACE.
- Standard Practice 0502-2010. Pipeline External Corrosion Direct Assessment Methodology.
- Ben Seghier, M. E. A., Keshtegar, B., Mahmoud, H. (2021). Time-Dependent Reliability Analysis of Reinforced Concrete Beams Subjected to Uniform and Pitting Corrosion and Brittle Fracture. Materials, 14 (8), 1820. https://doi.org/10.3390/ma14081820
- Joosten, M. W., Kolts, J., Humble, P. G., Keilty, D. M., Blakset, T. J., Sirnes, G. (1999). Internal Corrosion Monitoring of Subsea Production Flowlines - Probe Design, Testing, and Operational Results. All Days. https://doi.org/10.4043/11058-ms
- Vahdati, N., Wang, X., Shiryayev, O., Rostron, P., Yap, F. F. (2020). External Corrosion Detection of Oil Pipelines Using Fiber Optics. Sensors, 20 (3), 684. https://doi.org/10.3390/s20030684
- Niu, P. Y., Zhang, C. S., Zhao, J. C., Li, P. (2021). Propagation characteristics of low-frequency ultrasonic guided waves in grouting rock bolts. Rock and Soil Mechanics, 10, 2885–2894. https://doi.org/10.16285/j.rsm.2021.0293
- Cawley, P. (2002). Practical long range guided wave inspection-applications to pipes and rail. NDE2002 predict. assure. improve. National Se minar of ISNT. Available at: http://qnetworld.de/nde2002/papers/045P.pdf
- Wang, X., Gao, S., Liu, H., Li, J. (2020). Low frequency ultrasonic guided waves excitated by Galfenol Rod Ultrasonic Transducer in plate inspection. Sensors and Actuators A: Physical, 313, 112196. https://doi.org/10.1016/j.sna.2020.112196
- ASME B31.4: Pipeline Transportation Systems for Liquids and Slurries.
- Ma, J., Cawley, P. (2010). Low-frequency pulse echo reflection of the fundamental shear horizontal mode from part-thickness elliptical defects in plates. The Journal of the Acoustical Society of America, 127 (6), 3485–3493. https://doi.org/10.1121/1.3409446
- Fatima Saifee, K., Filmwala Zoeb, A., Hussain Kaneez, F. (2019). Corrosion inhibition of thiourea with synergistic effect of potassium iodide on mild steel in brackish water and effluent water. Research Journal of Chemistry and Environment, 23 (6).
- Sanni, S. E., Adefila, S. S., Anozie, A. N. (2019). Prediction of sand kinematic pressure and fluid-particle interaction coefficient as means of preventing sand-induced corrosion in crude oil pipelines. Ain Shams Engineering Journal, 10 (1), 55–62. https://doi.org/10.1016/j.asej.2018.02.007
- Mao, Y., Zhu, Y., Deng, C.-M., Sun, S., Xia, D.-H. (2022). Analysis of localized corrosion mechanism of 2024 aluminum alloy at a simulated marine splash zone. Engineering Failure Analysis, 142, 106759. https://doi.org/10.1016/j.engfailanal.2022.106759
- Laleh, M., Hughes, A. E., Xu, W., Gibson, I., Tan, M. Y. (2019). Unexpected erosion-corrosion behaviour of 316L stainless steel produced by selective laser melting. Corrosion Science, 155, 67–74. https://doi.org/10.1016/j.corsci.2019.04.028
- Ossai, C. I., Boswell, B., Davies, I. J. (2015). Pipeline failures in corrosive environments – A conceptual analysis of trends and effects. Engineering Failure Analysis, 53, 36–58. https://doi.org/10.1016/j.engfailanal.2015.03.004
- Glazov, N. N., Ukhlovtsev, S. M., Reformatskaya, I. I., Podobaev, A. N., Ashcheulova, I. I. (2006). Corrosion of carbon steel in soils of varying moisture content. Protection of Metals, 42 (6), 601–608. https://doi.org/10.1134/s0033173206060130
- Salgado, I. C., Font, P. G., Ibáñez, J. C., Reyes, C. A. (2015). Failure analysis of localized corrosion in sour environments in discharge lines of hydrocarbon wells. NACE - International Corrosion Conference Series 2015. Available at: https://www.researchgate.net/publication/282924249_Failure_analysis_of_localized_corrosion_in_sour_environments_in_discharge_lines_of_hydrocarbon_wells
- Li, J.-Y., Xu, R.-K., Zhang, H. (2012). Iron oxides serve as natural anti-acidification agents in highly weathered soils. Journal of Soils and Sediments, 12 (6), 876–887. https://doi.org/10.1007/s11368-012-0514-0
- Aditiyawarman, T., Kaban, A. P. S., Soedarsono, J. W. (2022). A Recent Review of Risk-Based Inspection Development to Support Service Excellence in the Oil and Gas Industry: An Artificial Intelligence Perspective. ASCE-ASME Journal of Risk and Uncertainty in Engineering Systems, Part B: Mechanical Engineering, 9 (1). https://doi.org/10.1115/1.4054558
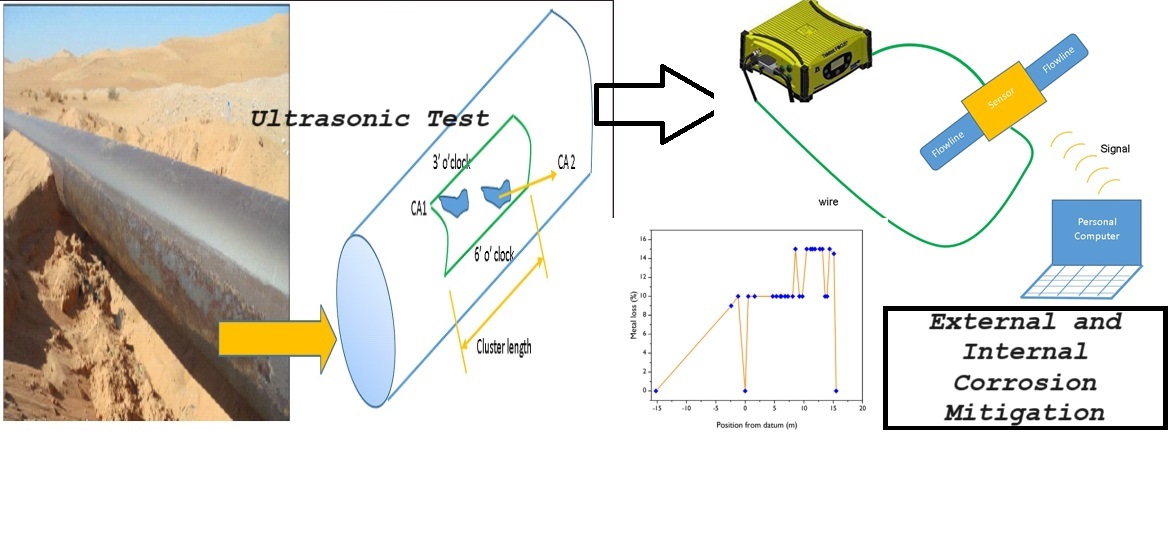
Downloads
Published
How to Cite
Issue
Section
License
Copyright (c) 2024 Sidhi Aribowo, Johny Soedarsono, Christy Sicilia, Rini Riastuti, Agus Kaban

This work is licensed under a Creative Commons Attribution 4.0 International License.
The consolidation and conditions for the transfer of copyright (identification of authorship) is carried out in the License Agreement. In particular, the authors reserve the right to the authorship of their manuscript and transfer the first publication of this work to the journal under the terms of the Creative Commons CC BY license. At the same time, they have the right to conclude on their own additional agreements concerning the non-exclusive distribution of the work in the form in which it was published by this journal, but provided that the link to the first publication of the article in this journal is preserved.
A license agreement is a document in which the author warrants that he/she owns all copyright for the work (manuscript, article, etc.).
The authors, signing the License Agreement with TECHNOLOGY CENTER PC, have all rights to the further use of their work, provided that they link to our edition in which the work was published.
According to the terms of the License Agreement, the Publisher TECHNOLOGY CENTER PC does not take away your copyrights and receives permission from the authors to use and dissemination of the publication through the world's scientific resources (own electronic resources, scientometric databases, repositories, libraries, etc.).
In the absence of a signed License Agreement or in the absence of this agreement of identifiers allowing to identify the identity of the author, the editors have no right to work with the manuscript.
It is important to remember that there is another type of agreement between authors and publishers – when copyright is transferred from the authors to the publisher. In this case, the authors lose ownership of their work and may not use it in any way.