Підвищення стійкості бокової матриці до термічного удару в автомобільному литті: порівняльне дослідження матеріалів FCD550 та SKD6
DOI:
https://doi.org/10.15587/1729-4061.2024.306615Ключові слова:
термічний удар, дискове колесо, виробництво, автомобільні деталі, продуктивність литтяАнотація
Підвищення стійкості бокових матриць до термічного удару в машинах із прес-формами було досягнуто шляхом заміни матеріалу FCD550 матеріалом SKD6. Основною проблемою, яку розглядають, є розтріскування бічних матриць через термічний удар, спричинений прискореним виробничим процесом, що призводить до зупинки виробництва та невиконання великих замовлень клієнтів. Дослідження спрямоване на визначення матеріалу, який може краще протистояти термічному удару, ніж FCD550, тим самим підвищуючи довговічність бічних матриць і загальну продуктивність виробничого процесу. Дослідження включало прямі виробничі експерименти, аналіз матеріалів FCD550 і SKD6, оцінку характеристик матриці та оцінку характеристик готового продукту до та після зміни матеріалу. Були проведені лабораторні випробування та випробування налагодження машин, варіювання виробничих процесів та оцінка результатів. Отримані дані свідчать про те, що SKD6 є значно стійкішим до термічного удару, ніж FCD550 у машинах із прес-формами. Дослідження порівнювало міцність матеріалів бічних матриць за допомогою таблиць даних і скоригованих параметрів налаштування в існуючих умовах охолодження. Експеримент передбачав зміну стандартної температури з 520–545 °C до 532–538 °C і скорочення часу замочування з мінімум 270–540 секунд до 332 секунд. Це скоротило час замочування з 69 секунд до 46 секунд і час витримки зі 190 секунд до 180 секунд, підвищивши продуктивність лиття з 194870 штук/28 днів до 213311 штук/28 днів на семи машинах, таким чином задовольняючи вимоги замовника щодо 200000 штук/28 днів без бічних тріщин. Випробування на довговічність п'яти зразків продукції відповідно до стандартів TSD5605G підтвердили, що якість відповідає вимогам замовника
Спонсор дослідження
- The author would like to acknowledge the funding support to this research from the Center of research and community service Politeknik Negeri Jakarta. The author would like to acknowledgments to Mr. Juhery the funding support to this research from Engineering department PT. PAKO 4-wheel Jakarta.
Посилання
- Wankhede, V. A., Vinodh, S. (2022). State of the art review on Industry 4.0 in manufacturing with the focus on automotive sector. International Journal of Lean Six Sigma, 13 (3), 692–732. Available at: https://www.x-mol.net/paper/article/1451642237902290944
- Zhao, X., Gao, P., Zhang, Z., Wang, Q., Yan, F. (2020). Fatigue characteristics of the extruded AZ80 automotive wheel. International Journal of Fatigue, 132, 105393. https://doi.org/10.1016/j.ijfatigue.2019.105393
- Klobčar, D., Kosec, L., Kosec, B., Tušek, J. (2012). Thermo fatigue cracking of die casting dies. Engineering Failure Analysis, 20, 43–53. https://doi.org/10.1016/j.engfailanal.2011.10.005
- Schwam, D., Wallace, J., Birceanu, S. (2002). Die Materials for Critical Applications and Increased Production Rates. Office of Scientific and Technical Information (OSTI). https://doi.org/10.2172/806823
- Su, Y., Fu, G., Liu, C., Liu, C., Long, X. (2021). Fatigue crack evolution and effect analysis of Ag sintering die-attachment in SiC power devices under power cycling based on phase-field simulation. Microelectronics Reliability, 126, 114244. https://doi.org/10.1016/j.microrel.2021.114244
- Cai, H., Wang, Z., Liu, L., Li, Y., Xing, F., Guo, F. (2022). Crack source and propagation of AZ91-0.9Gd alloy. Journal of Materials Research and Technology, 16, 1571–1577. https://doi.org/10.1016/j.jmrt.2021.12.065
- Schumacher, O., Marvel, C. J., Kelly, M. N., Cantwell, P. R., Vinci, R. P., Rickman, J. M. et al. (2016). Complexion time-temperature-transformation (TTT) diagrams: Opportunities and challenges. Current Opinion in Solid State and Materials Science, 20 (5), 316–323. https://doi.org/10.1016/j.cossms.2016.05.004
- Lordan, E., Zhang, Y., Dou, K., Jacot, A., Tzileroglou, C., Wang, S. et al. (2022). High-Pressure Die Casting: A Review of Progress from the EPSRC Future LiME Hub. Metals, 12 (10), 1575. https://doi.org/10.3390/met12101575
- Luthfiyah, S., Faridh, A., Soegijono, B. (2019). The Effect of Vacuum Quenching on Corrosion and Hardness of the Surface of SKD61 Steel. IOP Conference Series: Materials Science and Engineering, 694 (1), 012033. https://doi.org/10.1088/1757-899x/694/1/012033
- Sudjadi, U., Sinaga, R. V. (2020). Study of the hardness and microstructure profiles of SKD61 steel plunger tip (local material) after plasma nitriding. IOP Conference Series: Materials Science and Engineering, 839 (1), 012019. https://doi.org/10.1088/1757-899x/839/1/012019
- Yi, W., Liu, G., Gao, J., Zhang, L. (2021). Boosting for concept design of casting aluminum alloys driven by combining computational thermodynamics and machine learning techniques. Journal of Materials Informatics. https://doi.org/10.20517/jmi.2021.10
- Walsh, E., Maclean, N., Turner, A., Alsuleman, M., Prasad, E., Halbert, G. et al. (2022). Manufacture of tablets with structurally-controlled drug release using rapid tooling injection moulding. International Journal of Pharmaceutics, 624, 121956. https://doi.org/10.1016/j.ijpharm.2022.121956
- Yang, Q., Wu, X., Qiu, X. (2023). Microstructural Characteristics of High-Pressure Die Casting with High Strength–Ductility Synergy Properties: A Review. Materials, 16 (5), 1954. https://doi.org/10.3390/ma16051954
- Zhou, Y., Tian, N., Liu, W., Zeng, Y., Wang, G., Han, S. et al. (2022). Mechanism of heterogeneous distribution of Cr-containing dispersoids in DC casting 7475 aluminum alloy. Transactions of Nonferrous Metals Society of China, 32 (5), 1416–1427. https://doi.org/10.1016/s1003-6326(22)65883-7
- Wei, C., Ou, J., Farhang Mehr, F., Maijer, D., Cockcroft, S., Wang, X. et al. (2021). A thermal-stress modelling methodology in ABAQUS for fundamentally describing the die/casting interface behaviour in a cyclic permanent die casting process. Journal of Materials Research and Technology, 15, 5252–5264. https://doi.org/10.1016/j.jmrt.2021.10.120
- Campos Neto, N. D., Korenyi-Both, A. L., Vian, C., Midson, S. P., Kaufman, M. J. (2023). The development of coating selection criteria to minimize die failure by soldering and erosion during aluminum high pressure die casting. Journal of Materials Processing Technology, 316, 117954. https://doi.org/10.1016/j.jmatprotec.2023.117954
- Ahmadein, M., Elsheikh, A. H., Alsaleh, N. A. (2022). Modeling of cooling and heat conduction in permanent mold casting process. Alexandria Engineering Journal, 61 (2), 1757–1768. https://doi.org/10.1016/j.aej.2021.06.048
- Niu, Z., Liu, G., Li, T., Ji, S. (2022). Effect of high pressure die casting on the castability, defects and mechanical properties of aluminium alloys in extra-large thin-wall castings. Journal of Materials Processing Technology, 303, 117525. https://doi.org/10.1016/j.jmatprotec.2022.117525
- Li, Z., Li, D., Zhou, W., Hu, B., Zhao, X., Wang, J. et al. (2022). Characterization on the formation of porosity and tensile properties prediction in die casting Mg alloys. Journal of Magnesium and Alloys, 10 (7), 1857–1867. https://doi.org/10.1016/j.jma.2020.12.006
- Dudek, P., Białoń, J., Piwowońska, J., Walczak, W., Wrzała, K. (2023). The impact on the cost of making high pressure die castings with multi-cavity die and vacuum assistance. Vacuum, 210, 111859. https://doi.org/10.1016/j.vacuum.2023.111859
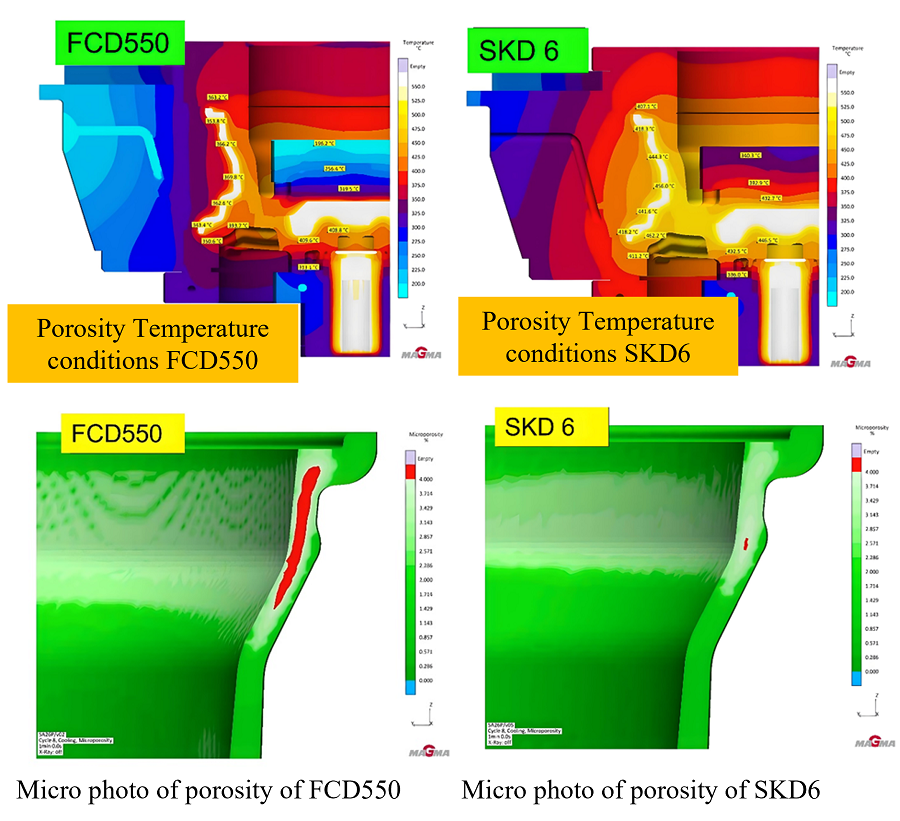
##submission.downloads##
Опубліковано
Як цитувати
Номер
Розділ
Ліцензія
Авторське право (c) 2024 Herry Patria, Iwan Susanto, Belyamin Belyamin, Dianta Mustofa Kamal

Ця робота ліцензується відповідно до Creative Commons Attribution 4.0 International License.
Закріплення та умови передачі авторських прав (ідентифікація авторства) здійснюється у Ліцензійному договорі. Зокрема, автори залишають за собою право на авторство свого рукопису та передають журналу право першої публікації цієї роботи на умовах ліцензії Creative Commons CC BY. При цьому вони мають право укладати самостійно додаткові угоди, що стосуються неексклюзивного поширення роботи у тому вигляді, в якому вона була опублікована цим журналом, але за умови збереження посилання на першу публікацію статті в цьому журналі.
Ліцензійний договір – це документ, в якому автор гарантує, що володіє усіма авторськими правами на твір (рукопис, статтю, тощо).
Автори, підписуючи Ліцензійний договір з ПП «ТЕХНОЛОГІЧНИЙ ЦЕНТР», мають усі права на подальше використання свого твору за умови посилання на наше видання, в якому твір опублікований. Відповідно до умов Ліцензійного договору, Видавець ПП «ТЕХНОЛОГІЧНИЙ ЦЕНТР» не забирає ваші авторські права та отримує від авторів дозвіл на використання та розповсюдження публікації через світові наукові ресурси (власні електронні ресурси, наукометричні бази даних, репозитарії, бібліотеки тощо).
За відсутності підписаного Ліцензійного договору або за відсутністю вказаних в цьому договорі ідентифікаторів, що дають змогу ідентифікувати особу автора, редакція не має права працювати з рукописом.
Важливо пам’ятати, що існує і інший тип угоди між авторами та видавцями – коли авторські права передаються від авторів до видавця. В такому разі автори втрачають права власності на свій твір та не можуть його використовувати в будь-який спосіб.