Devising a calculation method for modern structures of current-conducting elements in large electric machines in a three-dimensional statement
DOI:
https://doi.org/10.15587/1729-4061.2024.310049Keywords:
hydraulic generator, rotor, pole-to-pole connection, pole-to-pole jumper, ventilation system of hydraulic generator, cooling conditions, stressed-strained state, three-dimensional calculation, strength of rotating partsAbstract
The jumpers of rotor pole-to-pole connections are highly stressed elements in a hydraulic generator structure. These assemblies often fail due to deformation that exceeds the size of an air gap. Existing methods do not take into account the thermal component and attempts to improve the design are not based on mathematical models that make it possible to perform calculations with an accuracy of more than 50 %. The method devised in this work makes it possible to obtain boundary conditions of the third kind on the basis of three-dimensional mathematical modeling of the ventilation system of the hydraulic unit without simplifications. The method accuracy is explained by taking into account the spatial thermal component. The heat transfer coefficient determined by this method in the pole-to-pole connections area was ~250 W/(m2·K). Using FEM, mathematical modeling of the thermal stress state of pole-to-pole connections was carried out, taking into account mechanical and thermal factors. This made it possible to design the improved connection structure with additional fastening elements, which make it possible to reduce the displacement to 0.03 mm, and the stress to 53 MPa at the rotor rotation frequency of 880 rpm. This design makes it possible to enable reliable operation of the hydraulic unit under the condition of increasing the rotor rotation frequency to overspeed with disconnected combinatorial dependence, provided that the actual stresses are 0.95 % of the material yield strength. The convergence of the values obtained by the proposed method and by the HSS method exceeded 99 %. The practical result is the proposals for the hydraulic generator design modernization
References
- Liu, X., Luo, Y., Wang, Z. (2016). A review on fatigue damage mechanism in hydro turbines. Renewable and Sustainable Energy Reviews, 54, 1–14. https://doi.org/10.1016/j.rser.2015.09.025
- Selak, L., Butala, P., Sluga, A. (2014). Condition monitoring and fault diagnostics for hydropower plants. Computers in Industry, 65 (6), 924–936. https://doi.org/10.1016/j.compind.2014.02.006
- Kobzar, K. O., Gakal, P. G., Ovsyannykova, O. O. (2015). The Review of the Methods Used for the Analysis of the Thermal State of the Turbo-Generator Rotor with the Intermediate Hydrogen Cooling. NTU “KhPI” Bulletin: Power and Heat Engineering Processes and Equipment, 15, 112–117. https://doi.org/10.20998/2078-774x.2015.15.14
- DeCamillo, S. M., Dadouche, A., Fillon, M. (2013). Thrust Bearings in Power Generation. Encyclopedia of Tribology, 3682–3690. https://doi.org/10.1007/978-0-387-92897-5_57
- Zhou, C., Bian, X., Liang, Y., Zong, R. (2018). Numerical calculation and analysis of temperature field for stator transposition bar in hydro-generator. International Journal of Thermal Sciences, 125, 350–357. https://doi.org/10.1016/j.ijthermalsci.2017.12.004
- El-Zohri, E. H., Shafey, H. M., Kahoul, A. (2019). Performance evaluation of generator air coolers for the hydro-power plant of Aswan High Dam at Egypt. Energy, 179, 960–974. https://doi.org/10.1016/j.energy.2019.05.006
- Li, D., Li, W., Li, J., Liu, X. (2020). Analyzing regularity of interpolar air motion and heat dissipation coefficient distribution of a salient pole synchronous generator considering rotary airflow. International Communications in Heat and Mass Transfer, 119, 104828. https://doi.org/10.1016/j.icheatmasstransfer.2020.104828
- Verma, S., Chelliah, T. R. (2024). Restoration of extra-high voltage power grids through synchronous and asynchronous hydro units during blackout – A comprehensive review and case study. Electric Power Systems Research, 228, 110054. https://doi.org/10.1016/j.epsr.2023.110054
- Dang, D.-D., Pham, X.-T., Labbe, P., Torriano, F., Morissette, J.-F., Hudon, C. (2018). CFD analysis of turbulent convective heat transfer in a hydro-generator rotor-stator system. Applied Thermal Engineering, 130, 17–28. https://doi.org/10.1016/j.applthermaleng.2017.11.034
- Bucur, D. M., Cosoiu, C. I., Iovanel, R. G., Nicolae, A. A., Georgescu, S.-C. (2017). Assessing the Operation of the Cooling Water System of a Hydro-Power Plant Using EPANET. Energy Procedia, 112, 51–57. https://doi.org/10.1016/j.egypro.2017.03.1058
- Goričanec, D., Pozeb, V., Tomšič, L., Trop, P. (2014). Exploitation of the waste-heat from hydro power plants. Energy, 77, 220–225. https://doi.org/10.1016/j.energy.2014.06.106
- Olkkonen, V., Haaskjold, K., Klyve, Ø. S., Skartlien, R. (2023). Techno-economic feasibility of hybrid hydro-FPV systems in Sub-Saharan Africa under different market conditions. Renewable Energy, 215, 118981. https://doi.org/10.1016/j.renene.2023.118981
- Stancel, E., Cadis, M., Schiau, C., Ghiran, O., Stoian, I. (2007). Temperature Monitoring – Improved Diagnosis Support for Hydro Power Generators. IFAC Proceedings Volumes, 40 (8), 177–181. https://doi.org/10.3182/20070709-3-ro-4910.00029
- Bomben, S. G., LeBlanc, J.-B. (2009). Experience with field coil interconnection failures on large hydro generators Part I. 2009 IEEE Electrical Insulation Conference. https://doi.org/10.1109/eic.2009.5166391
- Chaulagain, R. K., Poudel, L., Maharjan, S. (2024). Design and experimental analysis of a new vertical ultra-low-head hydro turbine with the variation of outlet flow level on the head drop section of an open canal. Results in Engineering, 22, 102240. https://doi.org/10.1016/j.rineng.2024.102240
- Zito, R., Ardebili, H. (2019). Energy Storage: A New Approach. John Wiley & Sons. https://doi.org/10.1002/9781119083979
- Keyhani, A. (2019). Design of Smart Power Grid Renewable Energy Systems. John Wiley & Sons. https://doi.org/10.1002/9781119573265
- Rotor Inspection (2020). Handbook of Large Hydro Generators, 417–463. https://doi.org/10.1002/9781119524205.ch9
- Rausand, M., Barros, A., Hoyland, A. (2020). System Reliability Theory. Wiley Series in Probability and Statistics. John Wiley & Sons, Inc. https://doi.org/10.1002/9781119373940
- EN IEC 60034-33:2022. Rotating electrical machines - Part 33: Synchronous hydrogenerators including motor-generators - Specific requirements. Available at: https://standards.iteh.ai/catalog/standards/clc/f12936e0-2cf5-4b1d-990f-b3ee4f12ca57/en-iec-60034-33-2022
- Wang, H. (2023). Similarity and Dimensional Analysis. A Guide to Fluid Mechanics. Cambridge: Cambridge University Press, 230–245. https://doi.org/10.1017/9781108671149.009
- Tretiak, O., Kritskiy, D., Kobzar, I., Arefieva, M., Nazarenko, V. (2022). The Methods of Three-Dimensional Modeling of the Hydrogenerator Thrust Bearing. Computation, 10 (9), 152. https://doi.org/10.3390/computation10090152
- Tretiak, O., Kritskiy, D., Kobzar, I., Sokolova, V., Arefieva, M., Tretiak, I. et al. (2022). Modeling of the Stress–Strain of the Suspensions of the Stators of High-Power Turbogenerators. Computation, 10 (11), 191. https://doi.org/10.3390/computation10110191
- Tretiak, O., Kritskiy, D., Kobzar, I., Arefieva, M., Selevko, V., Brega, D. et al. (2023). Stress-Strained State of the Thrust Bearing Disc of Hydrogenerator-Motor. Computation, 11 (3), 60. https://doi.org/10.3390/computation11030060
- Anderson, D. A., Tannehill, J. C., Pletcher, R. H., Ramakanth, M., Shankar, V. (2020). Computational Fluid Mechanics and Heat Transfer. CRC Press. https://doi.org/10.1201/9781351124027
- Putignano, C., Afferrante, L., Carbone, G., Demelio, G. (2012). A new efficient numerical method for contact mechanics of rough surfaces. International Journal of Solids and Structures, 49 (2), 338–343. https://doi.org/10.1016/j.ijsolstr.2011.10.009
- Gerling, D. (2014). DC-Machines. Electrical Machines. Springer, 37–88. https://doi.org/10.1007/978-3-642-17584-8_2
- Li, W., Liu, Y.-P., Peng, X.-F. (2012). The generalized HSS method for solving singular linear systems. Journal of Computational and Applied Mathematics, 236 (9), 2338–2353. https://doi.org/10.1016/j.cam.2011.11.020
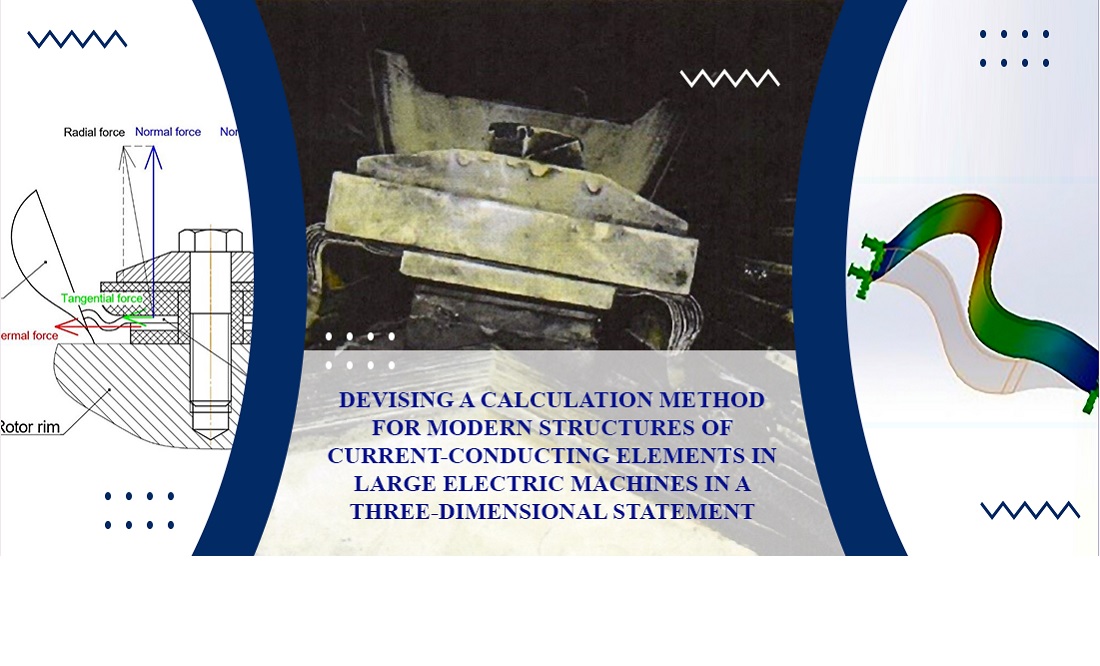
Downloads
Published
How to Cite
Issue
Section
License
Copyright (c) 2024 Oleksii Tretiak, Serhii Smyk, Stanislav Kravchenko, Serhii Smakhtin, Dmytro Brega, Anton Zhukov, Serhii Serhiienko, Yevhen Don

This work is licensed under a Creative Commons Attribution 4.0 International License.
The consolidation and conditions for the transfer of copyright (identification of authorship) is carried out in the License Agreement. In particular, the authors reserve the right to the authorship of their manuscript and transfer the first publication of this work to the journal under the terms of the Creative Commons CC BY license. At the same time, they have the right to conclude on their own additional agreements concerning the non-exclusive distribution of the work in the form in which it was published by this journal, but provided that the link to the first publication of the article in this journal is preserved.
A license agreement is a document in which the author warrants that he/she owns all copyright for the work (manuscript, article, etc.).
The authors, signing the License Agreement with TECHNOLOGY CENTER PC, have all rights to the further use of their work, provided that they link to our edition in which the work was published.
According to the terms of the License Agreement, the Publisher TECHNOLOGY CENTER PC does not take away your copyrights and receives permission from the authors to use and dissemination of the publication through the world's scientific resources (own electronic resources, scientometric databases, repositories, libraries, etc.).
In the absence of a signed License Agreement or in the absence of this agreement of identifiers allowing to identify the identity of the author, the editors have no right to work with the manuscript.
It is important to remember that there is another type of agreement between authors and publishers – when copyright is transferred from the authors to the publisher. In this case, the authors lose ownership of their work and may not use it in any way.