Determining the influence of technological parameters of the laser processing of plastic cards edges on improving their wear resistance
DOI:
https://doi.org/10.15587/1729-4061.2024.317448Keywords:
plastic card, wear of plastic card, multilayer structure, modes of laser processing, polyvinyl chlorideAbstract
The object of this study is plastic cards for various purposes, which are a multilayer structure. The main factors affecting the wear of cards are environmental influences, storage and use conditions, and equipment for reading our personalized information. During the operation of plastic cards, the most common defects are peeling of the top protective layer and violation of the integrity of the card structure. An increase in the frequency of such operational defects may be caused at the production stage by the peculiarities of a die-cutting process.
The subject of the study is to determine the optimal technological parameters for laser processing of plastic cards in order to improve their quality characteristics, in particular, wear resistance. The process of card wear was simulated by exposure to chemical and mechanical factors. The study was conducted using a standard procedure. The new methodology includes a combination of classical tests: a combination of chemical and dynamic effects and the introduction of a washing test.
To solve the existing problem, it was proposed to improve the technological process by introducing laser edge processing of plastic cards after die-cutting. A set of experimental studies on resistance to transverse, longitudinal bending and twisting revealed that the wear resistance of cards after laser edge treatment increased by 12 % compared to untreated cards. It was established that for cards made of polyvinylidene chloride, processing with a CO2 laser with a power of 25.5 W and a diameter of the laser beam of 1.5 mm is the most rational. It has been confirmed that this laser processing technique makes it possible to strengthen the chemical bonds between the layers of the body of a plastic card
References
- Mahajan, A., Verma, A., Pahuja, D. (2014). Smart card: Turning point of technology. International Journal of Computer Science and Mobile Computing, 3 (10), 982–987. Available at: https://ijcsmc.com/docs/papers/October2014/V3I10201499a40.pdf
- Kyrychok, T., Nazarenko, O., Barauskiene, O. (2020). Formation of Wear of Plastic Cards. Technology and Technique of Typography (Tekhnolohiia I Tekhnika Drukarstva), 4 (70), 34–41. https://doi.org/10.20535/2077-7264.4(70).2020.238598
- Khamula, O., Koniukhov, A. (2016). Development of a Model of Factors Influencing the Performance of Plastic Cards. Technology and Technique of Typography (Tekhnolohiia I Tekhnika Drukarstva), 4 (54), 21–28. https://doi.org/10.20535/2077-7264.4(54).2016.84589
- Corradini, F., Paganelli, E., Polzonetti, A. (2006). Smart card distribution for E-government digital identity promotion: problems and solutions. 28th International Conference on Information Technology Interfaces, 2006., 315–320. https://doi.org/10.1109/iti.2006.1708499
- Mentens, N., Genoe, J., Vandenabeele, T., Verschueren, L., Smets, D., Dehaene, W., Myny, K. (2019). Security on Plastics: Fake or Real? IACR Transactions on Cryptographic Hardware and Embedded Systems, 1–16. https://doi.org/10.46586/tches.v2019.i4.1-16
- Billiaert, E. (2014). Polycarbonate for ID documents. White Paper. Available at: https://www.academia.edu/7966334/Polycarbonate_for_ID_documents
- Naumenko, S. (2016). Some aspects of manufacturing and personalizing documents on the polymeric basis. Kryminalistyka i sudova ekspertyza, 61, 265–271. Available at: http://nbuv.gov.ua/UJRN/krise_2016_61_33
- Cai, X., An, B., Lai, X., Wu, Y., Wu, F. (2007). Reliability Evaluation on Flexible RFID Tag Inlay Packaged by Anisotropic Conductive Adhesive. 2007 8th International Conference on Electronic Packaging Technology, 1–4. https://doi.org/10.1109/icept.2007.4441524
- Using QSDC to optimize the laser engraving of ID documents. Entrust Datacard | White Paper. Available at: https://cards.mk/assets/cms/uploads/files/GS13-2100-002_QSDC_LaserEngraving_WP.pdf
- Bouffard, G., Thampi, B. N., Lanet, J.-L. (2013). Detecting Laser Fault Injection for Smart Cards Using Security Automata. Security in Computing and Communications, 18–29. https://doi.org/10.1007/978-3-642-40576-1_3
- Pardos, F. (2004). Plastic films: situation and outlook: a Rapra market report. iSmithers Rapra Publishing, 182.
- Card core films. Available at: https://www.kpfilms.com/en/cards-graphics/cards/card-core
- Speedmaster CD 74. Available at: https://print-machines.net/wp-content/uploads/Heidelberg_CD74_series_ENG.pdf
- NewV poly. UV offset inks for printing on films. Available at: https://www.hubergroup.com/cz/en/print-solutions-division/applications/sheet-fed-offset-uv/product/newv-poly
- Lauffer Card Lamination Systems. LAUFFER. Available at: https://lauffer.de/wp-content/uploads/2020/12/L003-Stand-09-2011-LC-LCL-Smartcards.pdf
- LOUDA SYSTEMS Card Punch DC 510. Available at: http://www.digitsmith.com/louda-systems-card-punch-dc-510-die-cutting-machine-sale-12880.html
- Peel testing identity cards. Available at: https://www.mecmesin.com/publications/peel-testing-identity-cards
- Microscop SIGETA BIOGENIC 40x-2000x LED Trino Infinity. Available at: https://sigeta.com.ua/products/mikroskop-sigeta-biogenic-40x-2000x-led-trino-infinity.html#technical
- Laser Engraving Cutting Machine. Available at: https://www.manualslib.com/manual/1831453/Bodor-Bcl-B-Series.html#manual
- Kyrychok, T. (2013). The methodology of visual assessment of stability of a layer of ink to simulate wear Intaglioprinting. Technology and Technique of Typography (Tekhnolohiia I Tekhnika Drukarstva), 4 (42), 4–12. https://doi.org/10.20535/2077-7264.4(42).2013.30810
- Card Making Machine (YMJ-ICTR). Available at: https://yuanmingjie.en.made-in-china.com/product/MKSQRYelhAVW/China-Card-Making-Machine-YMJ-ICTR-.html
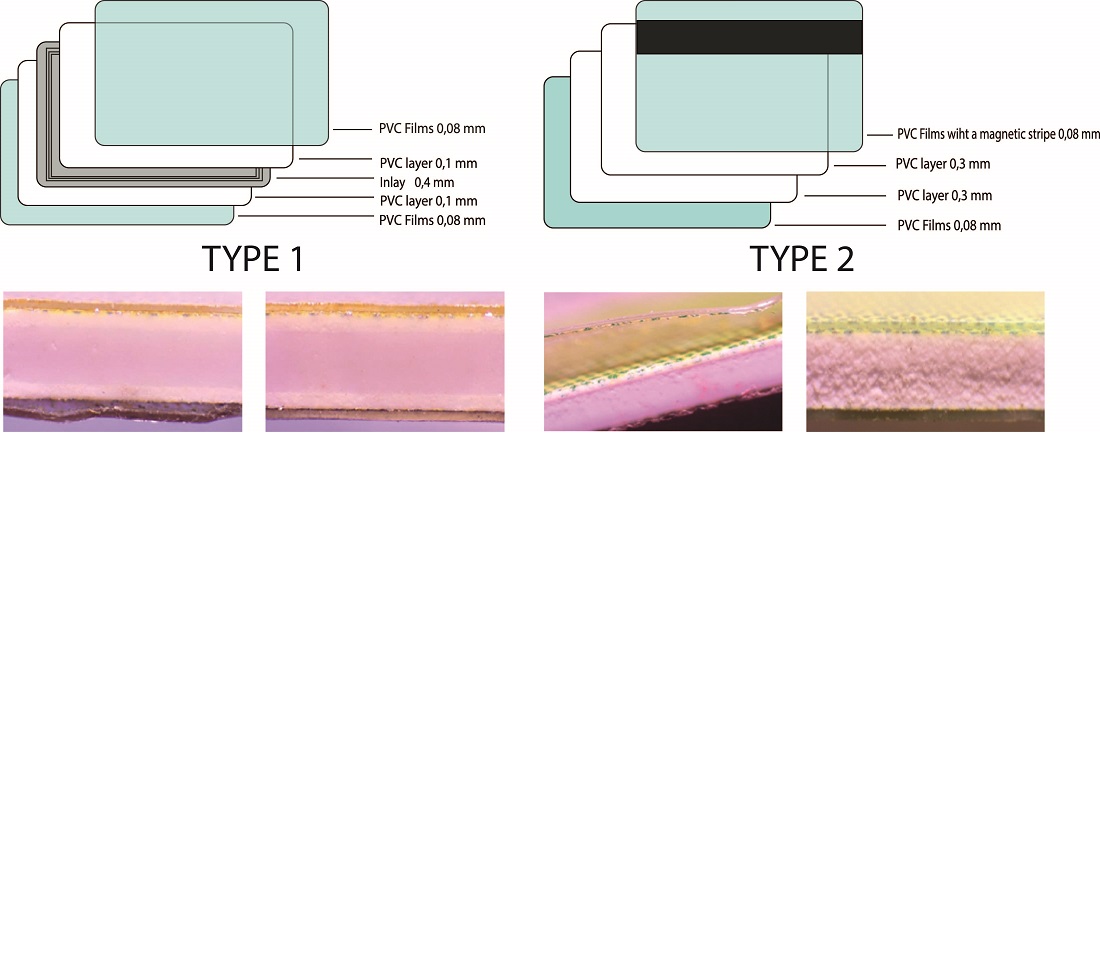
Downloads
Published
How to Cite
Issue
Section
License
Copyright (c) 2024 Tetiana Kyrychok, Olena Nazarenko, Olena Korotenko, Tetiana Klymenko, Nadiia Talimonova

This work is licensed under a Creative Commons Attribution 4.0 International License.
The consolidation and conditions for the transfer of copyright (identification of authorship) is carried out in the License Agreement. In particular, the authors reserve the right to the authorship of their manuscript and transfer the first publication of this work to the journal under the terms of the Creative Commons CC BY license. At the same time, they have the right to conclude on their own additional agreements concerning the non-exclusive distribution of the work in the form in which it was published by this journal, but provided that the link to the first publication of the article in this journal is preserved.
A license agreement is a document in which the author warrants that he/she owns all copyright for the work (manuscript, article, etc.).
The authors, signing the License Agreement with TECHNOLOGY CENTER PC, have all rights to the further use of their work, provided that they link to our edition in which the work was published.
According to the terms of the License Agreement, the Publisher TECHNOLOGY CENTER PC does not take away your copyrights and receives permission from the authors to use and dissemination of the publication through the world's scientific resources (own electronic resources, scientometric databases, repositories, libraries, etc.).
In the absence of a signed License Agreement or in the absence of this agreement of identifiers allowing to identify the identity of the author, the editors have no right to work with the manuscript.
It is important to remember that there is another type of agreement between authors and publishers – when copyright is transferred from the authors to the publisher. In this case, the authors lose ownership of their work and may not use it in any way.