Експериментальне дослідження і моделювання залишкових напружень при торцевому фрезеруванні Al-6061-T3 з використанням нейронної мережі
DOI:
https://doi.org/10.15587/1729-4061.2022.267032Ключові слова:
торцеве фрезерування, рентгенівська дифракція (XRD), залишкові напруження (RS), алюмінієвий сплав (AA 6061-T3), штучна нейронна мережа (ШНМ)Анотація
Процес фрезерування є поширеною операцією механічної обробки, яка використовується при виготовленні складних поверхонь. Залишкові напруження (RS), спричинені механічною обробкою, мають великий вплив на характеристики оброблюваних компонентів та якість поверхні при торцевому фрезеруванні з параметричним різанням. Залишкові напруження можуть істотно впливати на властивості конструкційних матеріалів, а також конструктивних компонентів, зокрема втомну довговічність, деформацію, удароміцність, корозійну стійкість і крихке руйнування. Відповідно, для захисту виробу та запобігання руйнуванню важливий контроль розподілу залишкових напружень. У більшості попередніх робіт вивчалися властивості матеріалу, параметри інструменту або параметри різання, але лише деякі з них забезпечували розподіл RS прямим і єдиним способом. Дана робота присвячена вивченню та оптимізації впливу швидкості, подачі та глибини різання для алюмінієвого сплаву 6061-T3 на RS поверхні. Звикористанням ортогональної решітки L27 знайдені оптимальні значення геометричних параметрів. За допомогою штучної нейронної мережі (ШНМ) проведено аналіз та моделювання RS для прогнозування поведінки RS при зміні параметрів процесу механічної обробки. Використання ШНМ для прогнозування поведінки RS при зміні параметрів процесу обробки представлено у якості перспективного методу. Згідно з результатами, в процесі фрезерування RS підвищуються при високій швидкості різання, приблизно проміжної швидкості подачі і більш глибокому різанні. Найвищі залишкові напруження, отримані за допомогою ШНМ, становлять ‒135,204 Н/мм2 при глибині різання 5 мм, подачі 0,25 мм/об і швидкості різання 1000 об/хв. ШНМ можна вважати потужним інструментом для оцінки залишкових напружень
Спонсор дослідження
- We sincerely thank the Al-Khwarizmi College of Engineering and the mechanical applied Laboratory of the Department of Automated Manufacturing Engineering for their assistance in carrying out this work.
Посилання
- Treuting, R. G., Read, W. T. (1951). A Mechanical Determination of Biaxial Residual Stress in Sheet Materials. Journal of Applied Physics, 22 (2), 130–134. doi: https://doi.org/10.1063/1.1699913
- Lucca, D. A., Brinksmeier, E., Goch, G. (1998). Progress in Assessing Surface and Subsurface Integrity. CIRP Annals, 47 (2), 669–693. doi: https://doi.org/10.1016/s0007-8506(07)63248-x
- Tang, Z. T., Liu, Z. Q., Pan, Y. Z., Wan, Y., Ai, X. (2009). The influence of tool flank wear on residual stresses induced by milling aluminum alloy. Journal of Materials Processing Technology, 209 (9), 4502–4508. doi: https://doi.org/10.1016/j.jmatprotec.2008.10.034
- Masmiati, N., Sarhan, A. A. D., Hassan, M. A. N., Hamdi, M. (2016). Optimization of cutting conditions for minimum residual stress, cutting force and surface roughness in end milling of S50C medium carbon steel. Measurement, 86, 253–265. doi: https://doi.org/10.1016/j.measurement.2016.02.049
- Wu, Q., Li, D.-P., Zhang, Y.-D. (2016). Detecting Milling Deformation in 7075 Aluminum Alloy Aeronautical Monolithic Components Using the Quasi-Symmetric Machining Method. Metals, 6 (4), 80. doi: https://doi.org/10.3390/met6040080
- Hlembotska, L., Melnychuk, P., Balytska, N., Melnyk, O. (2018). Modelling the loading of the nose-free cutting edges of face mill with a spiral-stepped arrangement of inserts. Eastern-European Journal of Enterprise Technologies, 1 (1 (91)), 46–54. doi: https://doi.org/10.15587/1729-4061.2018.121712
- Huang, X., Sun, J., Li, J. (2015). Experimental investigation of the effect of tool geometry on residual stresses in high speed milling 7050-T7451 aluminium alloy. International Journal of Surface Science and Engineering, 9 (4), 359. doi: https://doi.org/10.1504/ijsurfse.2015.070813
- Mia, M., Bashir, M. A., Khan, M. A., Dhar, N. R. (2016). Optimization of MQL flow rate for minimum cutting force and surface roughness in end milling of hardened steel (HRC 40). The International Journal of Advanced Manufacturing Technology, 89 (1-4), 675–690. doi: https://doi.org/10.1007/s00170-016-9080-8
- Mumali, F. (2022). Artificial neural network-based decision support systems in manufacturing processes: A systematic literature review. Computers & Industrial Engineering, 165, 107964. doi: https://doi.org/10.1016/j.cie.2022.107964
- Faizin, A., I Made Londen, B., Pramono, A. S., Wahjudi, A. (2021). Determination of the effect of thickness reduction ratio, die angle, and coefficient of friction on residual stresses in ironing process: an analysis using computer simulation. Eastern-European Journal of Enterprise Technologies, 5 (1 (113)), 70–78. doi: https://doi.org/10.15587/1729-4061.2021.243245
- Yao, C., Dou, X., Wu, D., Zhou, Z., Zhang, J. (2016). Surface integrity and fatigue analysis of shot-peening for 7055 aluminum alloy under different high-speed milling conditions. Advances in Mechanical Engineering, 8 (10), 168781401667462. doi: https://doi.org/10.1177/1687814016674628
- Jiang, X., Zhang, Z., Ding, Z., Fergani, O., Liang, S. Y. (2017). Tool overlap effect on redistributed residual stress and shape distortion produced by the machining of thin-walled aluminum parts. The International Journal of Advanced Manufacturing Technology, 93 (5-8), 2227–2242. doi: https://doi.org/10.1007/s00170-017-0693-3
- Ji, C., Sun, S., Lin, B., Fei, J. (2018). Effect of cutting parameters on the residual stress distribution generated by pocket milling of 2219 aluminum alloy. Advances in Mechanical Engineering, 10 (12), 168781401881305. doi: https://doi.org/10.1177/1687814018813055
- Perez, I., Madariaga, A., Cuesta, M., Garay, A., Arrazola, P. J., Ruiz, J. J. et al. (2018). Effect of cutting speed on the surface integrity of face milled 7050-T7451 aluminium workpieces. Procedia CIRP, 71, 460–465. doi: https://doi.org/10.1016/j.procir.2018.05.034
- Mohammadpour, M., Razfar, M. R., Jalili Saffar, R. (2010). Numerical investigating the effect of machining parameters on residual stresses in orthogonal cutting. Simulation Modelling Practice and Theory, 18 (3), 378–389. doi: https://doi.org/10.1016/j.simpat.2009.12.004
- Schajer, G. S. (1981). Application of Finite Element Calculations to Residual Stress Measurements. Journal of Engineering Materials and Technology, 103 (2), 157–163. doi: https://doi.org/10.1115/1.3224988
- Afazov, S. M., Becker, A. A., Hyde, T. H. (2012). Mathematical Modeling and Implementation of Residual Stress Mapping From Microscale to Macroscale Finite Element Models. Journal of Manufacturing Science and Engineering, 134 (2). doi: https://doi.org/10.1115/1.4006090
- Fuh, K.-H., Wu, C.-F. (1995). A residual-stress model for the milling of aluminum alloy (2014-T6). Journal of Materials Processing Technology, 51 (1-4), 87–105. doi: https://doi.org/10.1016/0924-0136(94)01355-5
- Zhou, R., Yang, W. (2019). Analytical modeling of machining-induced residual stresses in milling of complex surface. The International Journal of Advanced Manufacturing Technology, 105 (1-4), 565–577. doi: https://doi.org/10.1007/s00170-019-04219-7
- Huang, X., Sun, J., Li, J., Han, X., Xiong, Q. (2013). An Experimental Investigation of Residual Stresses in High-Speed End Milling 7050-T7451 Aluminum Alloy. Advances in Mechanical Engineering, 5, 592659. doi: https://doi.org/10.1155/2013/592659
- El-Axir, M. H. (2002). A method of modeling residual stress distribution in turning for different materials. International Journal of Machine Tools and Manufacture, 42 (9), 1055–1063. doi: https://doi.org/10.1016/s0890-6955(02)00031-7
- Cheng, M., Jiao, L., Yan, P., Feng, L., Qiu, T., Wang, X., Zhang, B. (2021). Prediction of surface residual stress in end milling with Gaussian process regression. Measurement, 178, 109333. doi: https://doi.org/10.1016/j.measurement.2021.109333
- Davis, J. R. (2001). Aluminum and Aluminum Alloys. ASM Internationa. Available at: https://materialsdata.nist.gov/bitstream/handle/11115/173/Aluminum%20and%20Aluminum%20Alloys%20Davis.pdf
- Standard test methods for tension testing wrought and cast aluminum- and magnesium-alloy products (Metric) (2015). ASTM International.
- Baden, A. S. (2017). Prediction the effect of milling parameters upon the residual stresses through using taghuchi method. Iraqi journal of mechanical and material engineering, 17 (2), 211–222. Available at: https://www.iasj.net/iasj/download/bdfade35166a8370
- Muñoz-Escalona, P., Maropoulos, P. G. (2015). A geometrical model for surface roughness prediction when face milling Al 7075-T7351 with square insert tools. Journal of Manufacturing Systems, 36, 216–223. doi: https://doi.org/10.1016/j.jmsy.2014.06.011
- Sova, O., Shyshatskyi, A., Zhuravskyi, Y., Salnikova, O., Zubov, O., Zhyvotovskyi, R. et al. (2020). Development of a methodology for training artificial neural networks for intelligent decision support systems. Eastern-European Journal of Enterprise Technologies, 2 (4 (104)), 6–14. doi: https://doi.org/10.15587/1729-4061.2020.199469
- Silva, D. P., Bastos, I. N., Fonseca, M. C. (2020). Influence of surface quality on residual stress of API 5L X80 steel submitted to static load and its prediction by artificial neural networks. The International Journal of Advanced Manufacturing Technology, 108 (11-12), 3753–3764. doi: https://doi.org/10.1007/s00170-020-05621-2
- Nouioua, M., Laouissi, A., Yallese, M. A., Khettabi, R., Belhadi, S. (2021). Multi-response optimization using artificial neural network-based GWO algorithm for high machining performance with minimum quantity lubrication. The International Journal of Advanced Manufacturing Technology, 116 (11-12), 3765–3778. doi: https://doi.org/10.1007/s00170-021-07745-5
- Jebaraj, M., Pradeep Kumar, M., Yuvaraj, N., Mujibar Rahman, G. (2019). Experimental study of the influence of the process parameters in the milling of Al6082-T6 alloy. Materials and Manufacturing Processes, 34 (12), 1411–1427. doi: https://doi.org/10.1080/10426914.2019.1594271
- Reimer, A., Luo, X. (2018). Prediction of residual stress in precision milling of AISI H13 steel. Procedia CIRP, 71, 329–334. doi: https://doi.org/10.1016/j.procir.2018.05.036
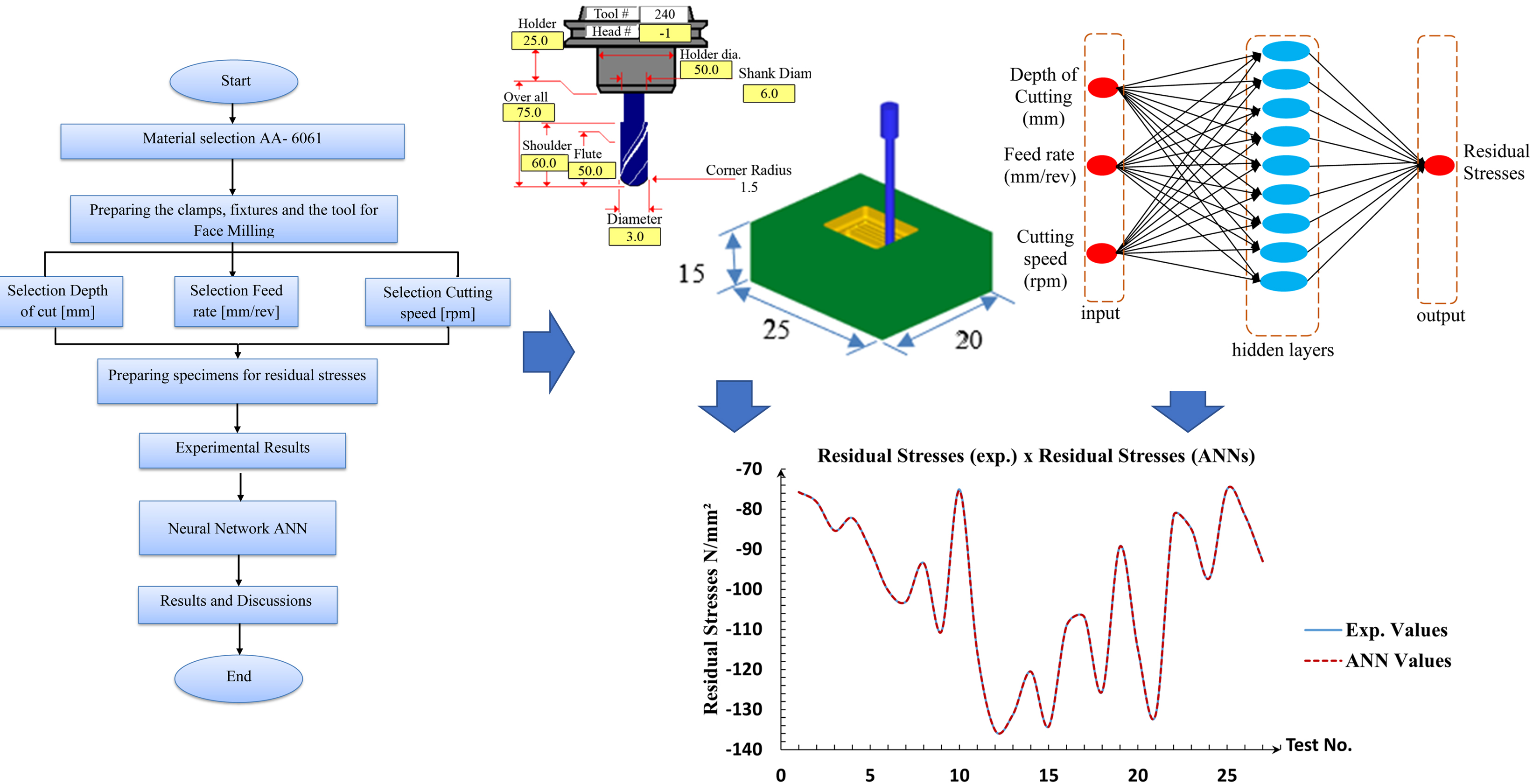
##submission.downloads##
Опубліковано
Як цитувати
Номер
Розділ
Ліцензія
Авторське право (c) 2022 Basma L. Mahdi, Huda H. Dalef, Hiba K. Hussein

Ця робота ліцензується відповідно до Creative Commons Attribution 4.0 International License.
Закріплення та умови передачі авторських прав (ідентифікація авторства) здійснюється у Ліцензійному договорі. Зокрема, автори залишають за собою право на авторство свого рукопису та передають журналу право першої публікації цієї роботи на умовах ліцензії Creative Commons CC BY. При цьому вони мають право укладати самостійно додаткові угоди, що стосуються неексклюзивного поширення роботи у тому вигляді, в якому вона була опублікована цим журналом, але за умови збереження посилання на першу публікацію статті в цьому журналі.
Ліцензійний договір – це документ, в якому автор гарантує, що володіє усіма авторськими правами на твір (рукопис, статтю, тощо).
Автори, підписуючи Ліцензійний договір з ПП «ТЕХНОЛОГІЧНИЙ ЦЕНТР», мають усі права на подальше використання свого твору за умови посилання на наше видання, в якому твір опублікований. Відповідно до умов Ліцензійного договору, Видавець ПП «ТЕХНОЛОГІЧНИЙ ЦЕНТР» не забирає ваші авторські права та отримує від авторів дозвіл на використання та розповсюдження публікації через світові наукові ресурси (власні електронні ресурси, наукометричні бази даних, репозитарії, бібліотеки тощо).
За відсутності підписаного Ліцензійного договору або за відсутністю вказаних в цьому договорі ідентифікаторів, що дають змогу ідентифікувати особу автора, редакція не має права працювати з рукописом.
Важливо пам’ятати, що існує і інший тип угоди між авторами та видавцями – коли авторські права передаються від авторів до видавця. В такому разі автори втрачають права власності на свій твір та не можуть його використовувати в будь-який спосіб.