Оптимізація топології для ізотропних пружних матеріалів за допомогою стільникової мозаїки
DOI:
https://doi.org/10.15587/1729-4061.2023.277909Ключові слова:
оптимізація топології, граничні умови, ізотропний матеріал, чутливість фільтра, стільникова мозаїкаАнотація
Оптимізація топології набуває популярності як основний інструмент для інженерів на початкових етапах проектування. По суті, область дизайну розбивається на окремі пікселі, причому щільність матеріалу кожного елемента або точки сітки є змінною дизайну. Потім проблема оптимізації вирішується за допомогою математичного програмування та методів оптимізації, які спираються на аналітичний розрахунок градієнта. У цьому дослідженні досліджується оптимізація топології за допомогою стільникових елементів мозаїки. Шестикутні елементи мають можливість гнучко з'єднувати два сусідніх елемента. Використання гексагонального елемента обмежує появу шахового порядку скінченними елементами чотирикутного стандартного типу Лагранжа. Розробляється математична модель з цільовою функцією, яка є мінімальним значенням відповідності області проектування. Матриця жорсткості елемента будується з використанням матриці деформації-переміщення та конститутивної матриці, припускаючи одиничний модуль Юнга. Крім того, оптимальні умови встановлюються за допомогою множників Лагранжа. Для підвищення ефективності оптимізації, запобігання досягненню алгоритмом локального оптимального стану та прискорення конвергенції використовуються два фільтри фільтрації чутливості та щільності. Якщо використовується запропонований фільтр, цільова функція досягає значення c=173,0293 і збіжність досягається після 200 ітерацій. Навпаки, без використання фільтра цільова функція має більше значення (c=186,7922) і збіжність відбувається на 27-й ітерації. Результати мають важливе значення для оптимізації топології для задоволення конкретних вимог граничних умов. У цьому документі пропонується новий підхід із використанням комбінації фільтрів для покращення оптимізації топології за допомогою шестикутних елементів у майбутніх програмах.
Посилання
- Sigmund, O. (2007). Morphology-based black and white filters for topology optimization. Structural and Multidisciplinary Optimization, 33 (4-5), 401–424. doi: https://doi.org/10.1007/s00158-006-0087-x
- Banh, T. T., Luu, N. G., Lee, D. (2021). A non-homogeneous multi-material topology optimization approach for functionally graded structures with cracks. Composite Structures, 273, 114230. doi: https://doi.org/10.1016/j.compstruct.2021.114230
- Huang, X., Li, W. (2022). Three-field floating projection topology optimization of continuum structures. Computer Methods in Applied Mechanics and Engineering, 399, 115444. doi: https://doi.org/10.1016/j.cma.2022.115444
- Zhou, P., Du, J., Lü, Z. (2018). A generalized DCT compression based density method for topology optimization of 2D and 3D continua. Computer Methods in Applied Mechanics and Engineering, 334, 1–21. doi: https://doi.org/10.1016/j.cma.2018.01.051
- Shen, W., Ohsaki, M. (2020). Geometry and topology optimization of plane frames for compliance minimization using force density method for geometry model. Engineering with Computers. doi: https://doi.org/10.1007/s00366-019-00923-w
- Tarek, M., Ray, T. (2020). Adaptive continuation solid isotropic material with penalization for volume constrained compliance minimization. Computer Methods in Applied Mechanics and Engineering, 363, 112880. doi: https://doi.org/10.1016/j.cma.2020.112880
- Mathai, B., Dhara, S., Gupta, S. (2022). Bone remodelling in implanted proximal femur using topology optimization and parameterized cellular model. Journal of the Mechanical Behavior of Biomedical Materials, 125, 104903. doi: https://doi.org/10.1016/j.jmbbm.2021.104903
- Li, H., Li, H., Gao, L., Li, J., Li, P., Yang, Y. (2021). Topology optimization of arbitrary-shape multi-phase structure with structured meshes based on a virtual phase method. Computer Methods in Applied Mechanics and Engineering, 387, 114138. doi: https://doi.org/10.1016/j.cma.2021.114138
- Liu, J., Zheng, Y., Ma, Y., Qureshi, A., Ahmad, R. (2019). A Topology Optimization Method for Hybrid Subtractive–Additive Remanufacturing. International Journal of Precision Engineering and Manufacturing-Green Technology, 7 (5), 939–953. doi: https://doi.org/10.1007/s40684-019-00075-8
- Sha, L., Lin, A., Zhao, X., Kuang, S. (2020). A topology optimization method of robot lightweight design based on the finite element model of assembly and its applications. Science Progress, 103 (3), 003685042093648. doi: https://doi.org/10.1177/0036850420936482
- Sato, A., Yamada, T., Izui, K., Nishiwaki, S., Takata, S. (2019). A topology optimization method in rarefied gas flow problems using the Boltzmann equation. Journal of Computational Physics, 395, 60–84. doi: https://doi.org/10.1016/j.jcp.2019.06.022
- Liu, S., Li, Q., Liu, J., Chen, W., Zhang, Y. (2018). A Realization Method for Transforming a Topology Optimization Design into Additive Manufacturing Structures. Engineering, 4 (2), 277–285. doi: https://doi.org/10.1016/j.eng.2017.09.002
- Xia, L., Zhang, L., Xia, Q., Shi, T. (2018). Stress-based topology optimization using bi-directional evolutionary structural optimization method. Computer Methods in Applied Mechanics and Engineering, 333, 356–370. doi: https://doi.org/10.1016/j.cma.2018.01.035
- Abdi, M., Ashcroft, I., Wildman, R. (2018). Topology optimization of geometrically nonlinear structures using an evolutionary optimization method. Engineering Optimization, 50 (11), 1850–1870. doi: https://doi.org/10.1080/0305215x.2017.1418864
- Hu, J., Yao, S., Gan, N., Xiong, Y., Chen, X. (2019). Fracture strength topology optimization of structural specific position using a bi-directional evolutionary structural optimization method. Engineering Optimization, 52 (4), 583–602. doi: https://doi.org/10.1080/0305215x.2019.1609466
- Rahmatalla, S. F., Swan, C. C. (2004). A Q4/Q4 continuum structural topology optimization implementation. Structural and Multidisciplinary Optimization, 27 (1-2), 130–135. doi: https://doi.org/10.1007/s00158-003-0365-9
- Talischi, C., Paulino, G. H., Pereira, A., Menezes, I. F. M. (2009). Polygonal finite elements for topology optimization: A unifying paradigm. International Journal for Numerical Methods in Engineering, 82 (6), 671–698. doi: https://doi.org/10.1002/nme.2763
- Kunakote, T., Bureerat, S. (2011). Multi-objective topology optimization using evolutionary algorithms. Engineering Optimization, 43 (5), 541–557. doi: https://doi.org/10.1080/0305215x.2010.502935
- Wallin, M., Ivarsson, N., Amir, O., Tortorelli, D. (2020). Consistent boundary conditions for PDE filter regularization in topology optimization. Structural and Multidisciplinary Optimization, 62 (3), 1299–1311. doi: https://doi.org/10.1007/s00158-020-02556-w
- Kumar, P., Saxena, A., Sauer, R. A. (2016). Implementation of Self Contact in Path Generating Compliant Mechanisms. Microactuators and Micromechanisms, 251–261. doi: https://doi.org/10.1007/978-3-319-45387-3_22
- Saxena, A. (2011). Topology design with negative masks using gradient search. Structural and Multidisciplinary Optimization, 44 (5), 629–649. doi: https://doi.org/10.1007/s00158-011-0649-4
- Sukumar, N., Tabarraei, A. (2004). Conforming polygonal finite elements. International Journal for Numerical Methods in Engineering, 61 (12), 2045–2066. doi: https://doi.org/10.1002/nme.1141
- Yoon, G. H., Ha, S. I. (2020). A New Development of a Shadow Density Filter for Manufacturing Constraint and Its Applications to Multiphysics Topology Optimization. Journal of Mechanical Design, 143 (6). doi: https://doi.org/10.1115/1.4048818
- Yi, B., Yoon, G. H., Peng, X. (2020). A simple density filter for the topology optimization of coated structures. Engineering Optimization, 53 (12), 2088–2107. doi: https://doi.org/10.1080/0305215x.2020.1845326
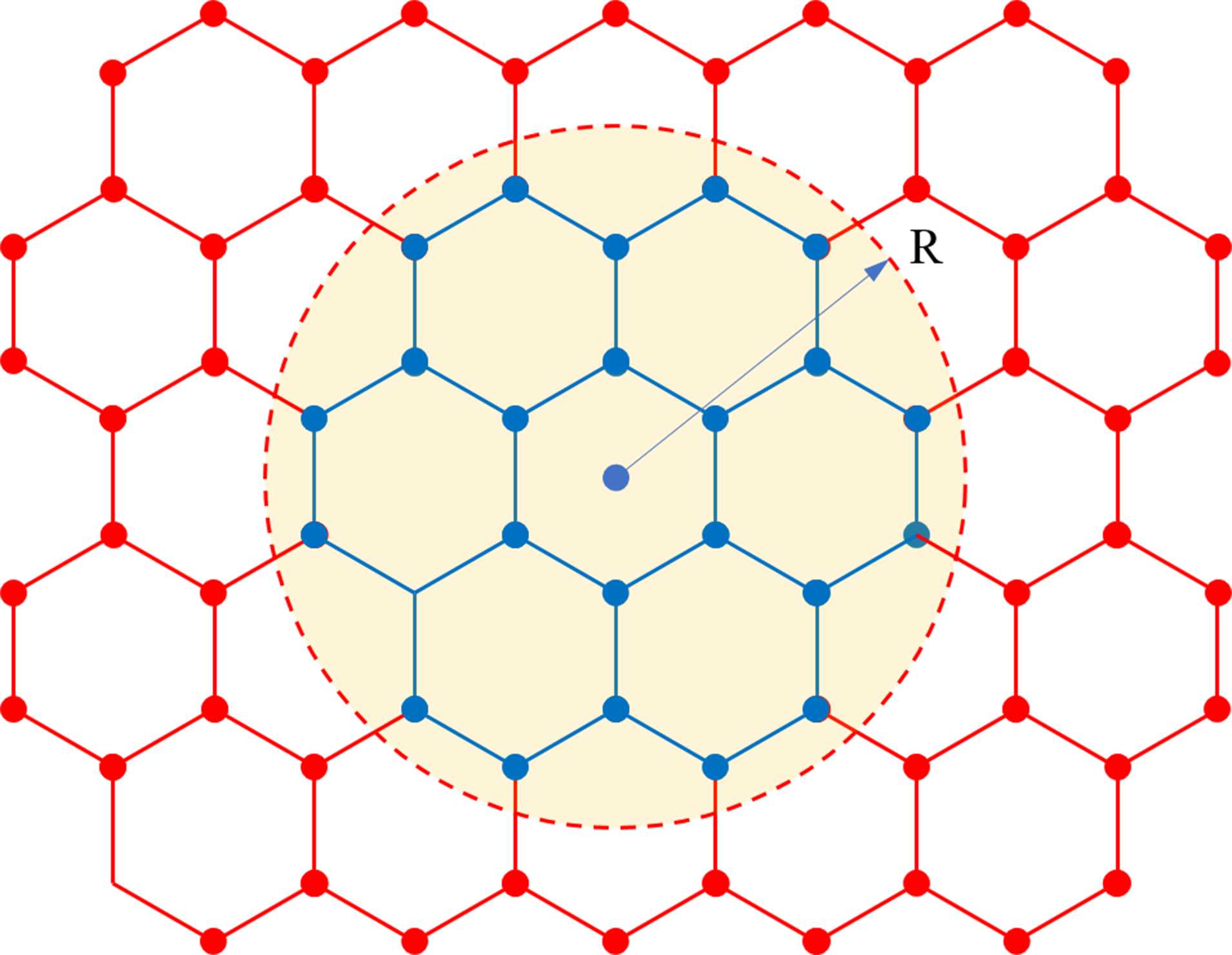
##submission.downloads##
Опубліковано
Як цитувати
Номер
Розділ
Ліцензія
Авторське право (c) 2023 Ngoc-Tien Tran

Ця робота ліцензується відповідно до Creative Commons Attribution 4.0 International License.
Закріплення та умови передачі авторських прав (ідентифікація авторства) здійснюється у Ліцензійному договорі. Зокрема, автори залишають за собою право на авторство свого рукопису та передають журналу право першої публікації цієї роботи на умовах ліцензії Creative Commons CC BY. При цьому вони мають право укладати самостійно додаткові угоди, що стосуються неексклюзивного поширення роботи у тому вигляді, в якому вона була опублікована цим журналом, але за умови збереження посилання на першу публікацію статті в цьому журналі.
Ліцензійний договір – це документ, в якому автор гарантує, що володіє усіма авторськими правами на твір (рукопис, статтю, тощо).
Автори, підписуючи Ліцензійний договір з ПП «ТЕХНОЛОГІЧНИЙ ЦЕНТР», мають усі права на подальше використання свого твору за умови посилання на наше видання, в якому твір опублікований. Відповідно до умов Ліцензійного договору, Видавець ПП «ТЕХНОЛОГІЧНИЙ ЦЕНТР» не забирає ваші авторські права та отримує від авторів дозвіл на використання та розповсюдження публікації через світові наукові ресурси (власні електронні ресурси, наукометричні бази даних, репозитарії, бібліотеки тощо).
За відсутності підписаного Ліцензійного договору або за відсутністю вказаних в цьому договорі ідентифікаторів, що дають змогу ідентифікувати особу автора, редакція не має права працювати з рукописом.
Важливо пам’ятати, що існує і інший тип угоди між авторами та видавцями – коли авторські права передаються від авторів до видавця. В такому разі автори втрачають права власності на свій твір та не можуть його використовувати в будь-який спосіб.