Determination of the fatigue behavior of the composite Single-Stringer structure based on the quasi-static method
DOI:
https://doi.org/10.15587/1729-4061.2023.277911Keywords:
directional deformation, shear analysis, general deformation, equivalent stresses, composite structureAbstract
In this investigation, the Mechanical Behavior of the composite Single-Stringer structure was subjected to numerical analysis in order to better understand its properties. As the primary material for the modeling process, the carbon-epoxy IM7/8552 with quasi-isotropic Layups has been utilized. The outcomes of the numerical analysis that were carried out on the structure while it was in its static state have been put into the structural tool that was developed by the ANSYS programme. The fundamental boundary conditions have been defined on the basis of the information that was received from the testing. Static forces with a combined magnitude of 13.7 kN are being applied to the composite Single-Stringer structure. Shear stresses, direction deformation, von mises stresses, and total deformation have all been shown to have an effect on a material's mechanical behaviour, and this effect has been demonstrated. The calculations indicate that there is a maximum amount of bending that can take place as a direct result of the load that is being applied, and that amount is equal to 0.0147. The maximum amount of bending that can take place as a direct result of the load that is being applied is equal to 0.0147. As a consequence of the application of 13.7 kN of pressure, the von Mises stress, which is also frequently referred to as comparable stresses, has reached 51.9 MPa. Shear stresses have been estimated in three distinct plans, and it was discovered that the shear stress that was applied to the XY plane achieved a maximum of 15 MPa, but the shear stress that was applied to the XZ plane reached a maximum of 9.8 MPa. This was found. Both aeroplanes were put through precisely the same amount of tension at the exact same time. At this time, the shear stress on the plane YZ has reached a level of 1.5 MPa.
References
- Raimondo, A., Doesburg, S. A., Bisagni, C. (2020). Numerical study of quasi-static and fatigue delamination growth in a post-buckled composite stiffened panel. Composites Part B: Engineering, 182, 107589. doi: https://doi.org/10.1016/j.compositesb.2019.107589
- Zalameda, J., Winfree, W. (2018). Detection and Characterization of Damage in Quasi-Static Loaded Composite Structures using Passive Thermography. Sensors, 18 (10), 3562. doi: https://doi.org/10.3390/s18103562
- Zalameda, J. N., Winfree, W. P., Horne, M. R. (2018). Detection of Damage During Quasi-Static Loading of a Single Stringer Panel Using Passive Thermography and Acoustic Emission. Conference Proceedings of the Society for Experimental Mechanics Series, 77–86. doi: https://doi.org/10.1007/978-3-319-95074-7_15
- Raimondo, A., Mendez, J. P., Bisagni, C. (2021). Experimental study on post-buckled composite single-stringer specimens with initial delamination under fatigue loads. American Society for Composites 2021. doi: https://doi.org/10.12783/asc36/35772
- Winfree, W. P., Zalameda, J. N., Horne, M. R. (2019). Simulations of thermal signatures of damage measured during quasi-static loading of a single stringer panel. AIP Conference Proceedings. doi: https://doi.org/10.1063/1.5099849
- Milanoski, D., Galanopoulos, G., Broer, A., Zarouchas, D., Loutas, T. (2021). A Strain-Based Health Indicator for the SHM of Skin-to-Stringer Disbond Growth of Composite Stiffened Panels in Fatigue. European Workshop on Structural Health Monitoring, 626–635. doi: https://doi.org/10.1007/978-3-030-64594-6_61
- Horne, M. R., Zalameda, J. N. (2018). Real time detection of damage during quasi-static loading of a single stringer panel using passive thermography. Thermosense: Thermal Infrared Applications XL. doi: https://doi.org/10.1117/12.2305613
- Zalameda, J. N., Winfree, W. P., Horne, M. R. (2019). Characterization of damage formation in a composite single stringer hat stiffened panel using passive thermography. AIP Conference Proceedings. doi: https://doi.org/10.1063/1.5099753
- Seneviratne, W., Saseendran, V., Shafie, M., Tomblin, J. (2021). Skin/stringer interface damage characterization of stiffened composite structures. American Society for Composites 2021. doi: https://doi.org/10.12783/asc36/35929
- Milanoski, D., Galanopoulos, G., Zarouchas, D., Loutas, T. (2022). Damage Diagnostics on Post-buckled Stiffened Panels Utilizing the Digital-Twin Concept. European Workshop on Structural Health Monitoring, 213–222. doi: https://doi.org/10.1007/978-3-031-07254-3_21
- van Dooren, K. S., Tijs, B. H. A. H., Waleson, J. E. A., Bisagni, C. (2023). Skin-stringer separation in post-buckling of butt-joint stiffened thermoplastic composite panels. Composite Structures, 304, 116294. doi: https://doi.org/10.1016/j.compstruct.2022.116294
- Xiong, J., Zhu, Y., Luo, C., Li, Y. (2021). Fatigue-driven failure criterion for progressive damage modelling and fatigue life prediction of composite structures. International Journal of Fatigue, 145, 106110. doi: https://doi.org/10.1016/j.ijfatigue.2020.106110
- Dogan, A. (2022). Quasi-static and dynamic response of functionally graded viscoelastic plates. Composite Structures, 280, 114883. doi: https://doi.org/10.1016/j.compstruct.2021.114883
- Chen, J., Fang, H., Liu, W., Zhu, L., Zhuang, Y., Wang, J., Han, J. (2018). Energy absorption of foam-filled multi-cell composite panels under quasi-static compression. Composites Part B: Engineering, 153, 295–305. doi: https://doi.org/10.1016/j.compositesb.2018.08.122
- Zha, Y., Ma, Q., Gan, X., Cai, M., Zhou, T. (2020). Deformation and energy absorption characters of Al‐CFRP hybrid tubes under quasi‐static radial compression. Polymer Composites, 41 (11), 4602–4618. doi: https://doi.org/10.1002/pc.25737
- Shruti, M., Sri Hemanth, N., Badgayan, N. D., Sahu, S. K. (2021). Compressive behavior of auxetic structural metamaterial for lightweight construction using ANSYS static structural analysis. Materials Today: Proceedings, 38, 12–17. doi: https://doi.org/10.1016/j.matpr.2020.05.410
- Mirrudula, P., Priya, P. K., Malavika, M., Kumar, G. R., Vijayanandh, R., Kumar, M. S. (2020). Comparative structural analysis of the sandwich composite using advanced numerical simulation. AIP Conference Proceedings. doi: https://doi.org/10.1063/5.0019370
- Saravanakumar, S., Kumar Chandramohan, N., Tamil Prabakaran, S., Muniyappan, M., Shanmugam, M., Shaisundaram, V. S. (2021). The static structural analysis of torque converter material for better performance by changing the stator angle. Materials Today: Proceedings, 37, 1963–1972. doi: https://doi.org/10.1016/j.matpr.2020.07.487
- Vijayanandh, R., Venkatesan, K., Ramesh, M., Raj Kumar, G., Senthil Kumar, M. (2019). Optimization of orientation of carbon fiber reinforced polymer based on structural analysis. International Journal of Scientific & Technology Research, 8 (11), 3020–3029. Available at: http://www.ijstr.org/final-print/nov2019/Optimization-Of-Orientation-Of-Carbon-Fiber-Reinforced-Polymer-Based-On-Structural-Analysis-.pdf
- Htet, T. L. (2020). Structural analysis and topology design optimization of load bearing elements of aircraft fuselage structure. IOP Conference Series: Materials Science and Engineering, 709 (4), 044113. doi: https://doi.org/10.1088/1757-899x/709/4/044113
- Carneiro, P. M. C., Gamboa, P. (2019). Structural analysis of wing ribs obtained by additive manufacturing. Rapid Prototyping Journal, 25 (4), 708–720. doi: https://doi.org/10.1108/rpj-02-2018-0044
- Pennington, A., Goyal, V. (2023). Integration of Fatigue R-Curve Effects into VCCT for Durability Predictions, Part 1: Buckled Composite Single-Stringer Stiffened Panels. AIAA SCITECH 2023 Forum. doi: https://doi.org/10.2514/6.2023-0952
- Martulli, L. M., Bernasconi, A. (2023). An efficient and versatile use of the VCCT for composites delamination growth under fatigue loadings in 3D numerical analysis: the Sequential Static Fatigue algorithm. International Journal of Fatigue, 170, 107493. doi: https://doi.org/10.1016/j.ijfatigue.2022.107493
- Chiang, C.-H., Hidayat, M., Kumar, D. (2022). Simulated thermal image based on finite element models for a layered composite structures. Materials Today: Proceedings, 57, 871–877. doi: https://doi.org/10.1016/j.matpr.2022.02.539
- Tan, R., Xu, J., Guan, Z., Sun, W., Ouyang, T., Wang, S. (2020). Experimental study on effect of impact locations on damage formation and compression behavior of stiffened composite panels with L-shaped stiffener. Thin-Walled Structures, 150, 106707. doi: https://doi.org/10.1016/j.tws.2020.106707
- Saeedifar, M., Saleh, M. N., Nijhuis, P., de Freitas, S. T., Zarouchas, D. (2021). Damage assessment of a titanium skin adhesively bonded to carbon fiber–reinforced plastic omega stringers using acoustic emission. Structural Health Monitoring, 21 (2), 407–423. doi: https://doi.org/10.1177/14759217211001752
- Ciminello, M., Boffa, N. D., Concilio, A., Galasso, B., Romano, F., Monaco, E. (2020). Damage Detection of CFRP Stiffened Panels by Using Cross-Correlated Spatially Shifted Distributed Strain Sensors. Applied Sciences, 10 (8), 2662. doi: https://doi.org/10.3390/app10082662
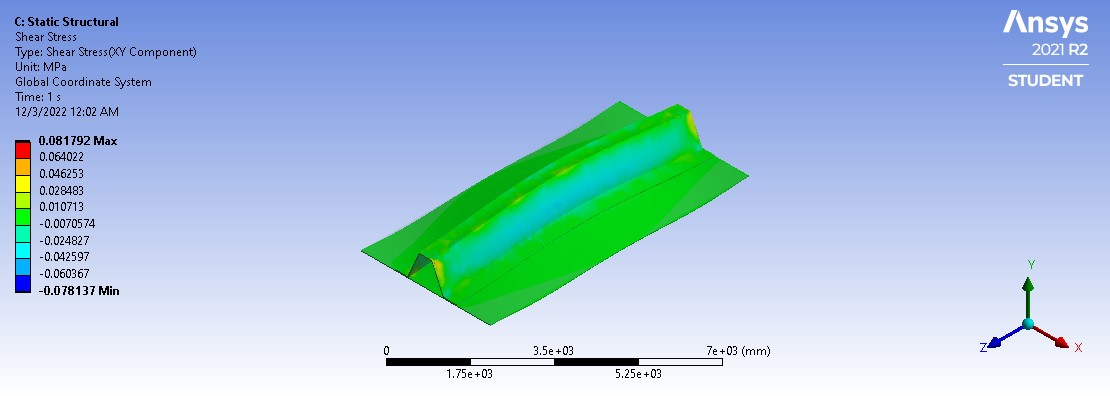
Downloads
Published
How to Cite
Issue
Section
License
Copyright (c) 2023 Ali Talib Shomran, Batool Mardan Faisal, Emad Kamil Hussein, Thiago Santos, Kies Fatima

This work is licensed under a Creative Commons Attribution 4.0 International License.
The consolidation and conditions for the transfer of copyright (identification of authorship) is carried out in the License Agreement. In particular, the authors reserve the right to the authorship of their manuscript and transfer the first publication of this work to the journal under the terms of the Creative Commons CC BY license. At the same time, they have the right to conclude on their own additional agreements concerning the non-exclusive distribution of the work in the form in which it was published by this journal, but provided that the link to the first publication of the article in this journal is preserved.
A license agreement is a document in which the author warrants that he/she owns all copyright for the work (manuscript, article, etc.).
The authors, signing the License Agreement with TECHNOLOGY CENTER PC, have all rights to the further use of their work, provided that they link to our edition in which the work was published.
According to the terms of the License Agreement, the Publisher TECHNOLOGY CENTER PC does not take away your copyrights and receives permission from the authors to use and dissemination of the publication through the world's scientific resources (own electronic resources, scientometric databases, repositories, libraries, etc.).
In the absence of a signed License Agreement or in the absence of this agreement of identifiers allowing to identify the identity of the author, the editors have no right to work with the manuscript.
It is important to remember that there is another type of agreement between authors and publishers – when copyright is transferred from the authors to the publisher. In this case, the authors lose ownership of their work and may not use it in any way.