Development of a technology to produce titanium powder with a low carbon footprint
DOI:
https://doi.org/10.15587/1729-4061.2023.276746Keywords:
titanium powders, titanium dioxide, dendrite, titanium deoxidation, carbon footprint, reductionAbstract
This paper reports the analysis of modern technologies for the production of titanium from oxide raw materials. It has been established that current industrial methods for producing titanium require the use of carbon as a reducing agent and, accordingly, cannot decrease carbon emissions without changing the technology. That is why devising a technology for producing titanium with a reduction in emissions of carbon components is a relevant task. So, the object of research is the technology of obtaining titanium from its oxide without the use of carbon components. It was found that an integrated approach to the preparation of raw materials and the separation of reduction processes with the successive use of two types of reducing agents – magnesium and calcium, made it possible to create an effective process for producing titanium without the use of carbon reducing agents. The influence of calcium and magnesium chlorides as promoters of the reduction process was revealed. Experimental studies have established that the shape and density of raw materials significantly affect the efficiency of the reduction process by streamlining the reducing agent flows and reaction products in the furnace charge. The established regularities made it possible to improve the process of reduction of titanium oxide to obtain samples of titanium powders with an oxygen content of 0.17 %, which corresponds to international standards for titanium alloys and powders. Additional plasma treatment made it possible to obtain materials that were suitable for additive processes in all respects. A systematic approach to the utilization of reaction products made it possible to devise a technological scheme in which all possible waste is either returned to the technological process after treatment or processed into marketable products. Based on the results of the study, a technological scheme for obtaining powders of titanium alloys from titanium oxide by complex reduction in two stages – magnesium and calcium – was developed. The proposed scheme involves standard metallurgical processes and is brought to standard processes and equipment of metallurgical enterprises and chemical industry.
In terms of practical significance, the results of this work could be used in the development of industrial technology to produce titanium from titanium dioxide without the use of carbon components.
References
- Williams, J. C., Boyer, R. R. (2020). Opportunities and Issues in the Application of Titanium Alloys for Aerospace Components. Metals, 10 (6), 705. doi: https://doi.org/10.3390/met10060705
- Liu, S., Song, X., Xue, T., Ma, N., Wang, Y., Wang, L. (2020). Application and development of titanium alloy and titanium matrix composites in aerospace field. Journal of Aeronautical Materials, 2020, 40 (3), 77–94. doi: https://doi.org/10.11868/j.issn.1005-5053.2020.000061
- Haider, A. J., Jameel, Z. N., Al-Hussaini, I. H. M. (2019). Review on: Titanium Dioxide Applications. Energy Procedia, 157, 17–29. doi: https://doi.org/10.1016/j.egypro.2018.11.159
- Chen, M. C., Koh, P. W., Ponnusamy, V. K., Lee, S. L. (2022). Titanium dioxide and other nanomaterials based antimicrobial additives in functional paints and coatings: Review. Progress in Organic Coatings, 163, 106660. doi: https://doi.org/10.1016/j.porgcoat.2021.106660
- Adams, R. (2022). Thirtieth anniversary conference: TiO2 & colour pigments in amsterdam. Focus on Pigments, 2022 (11), 1–4. doi: https://doi.org/10.1016/j.fop.2022.10.001
- Kapustyan, A. Y., Ovchinnikov, A. V., Yanko, T. B. (2018). Syntered titanium alloys for nuclear industry. Questions of atomic science and technology, 1 (113), 134–141. Available at: https://vant.kipt.kharkov.ua/ARTICLE/VANT_2018_1/article_2018_1_134.pdf
- Baltatu, M. S., Tugui, C. A., Perju, M. C., Benchea, M., Spataru, M. C., Sandu, A. V., Vizureanu, P. (2019). Biocompatible titanium alloys used in medical applications. Revista de Chimie, 70 (4), 1302–1306. doi: https://doi.org/10.37358/RC.19.4.7114
- Taşdemir, A., Nohut, S. (2021). An overview of wire arc additive manufacturing (WAAM) in shipbuilding industry. Ships and Offshore Structures, 16 (7), 797–814. doi: https://doi.org/10.1080/17445302.2020.1786232
- Li, M., Pan, Y., Zou, Y. (2021). Application and optimization design of Titanium alloy in sports equipment. Journal of Physics: Conference Series, 1820. doi: https://doi.org/10.1088/1742-6596/1820/1/012011
- Zhang, L.-C., Chen, L.-Y. (2019). A review on biomedical titanium alloys: recent progress and prospect. Advanced Engineering Materials, 21 (4), 1801215. doi: https://doi.org/10.1002/adem.201801215
- Froes, F. H., Qian, M., Niinomi, M. (Eds.) (2019). Titanium for Consumer Applications: Real-World Use of Titanium. Elsevier.
- Mohr, W. (2010). Assessment of Structural Integrity of Titanium Weldments for U.S. Navy Applications. Singapore. doi: https://doi.org/10.3850/978-981-08-5118-7_070
- Yimeng, F., Wenhua, W., Xun, G., Yadong, L., Xiaozhou, Z., Qingyan, M. et al. (2021). Characteristics, Connotation and Military Application of Additive Remanufacturing Technology. Journal of Physics: Conference Series, 1948 (1), 012118. doi: https://doi.org/10.1088/1742-6596/1948/1/012118
- Fang, Z. Z., Paramore, J. D., Sun, P., Chandran, K. R., Zhang, Y., Xia, Y. et al. (2018). Powder metallurgy of titanium – past, present, and future. International Materials Reviews, 63 (7), 407–459. doi: https://doi.org/10.1080/09506608.2017.1366003
- Behera, M. P., Dougherty, T., Singamneni, S. (2019). Conventional and Additive Manufacturing with Metal Matrix Composites: A Perspective. Procedia Manufacturing, 30, 159–166. doi: https://doi.org/10.1016/j.promfg.2019.02.023
- Zhang, T., Liu, C.-T. (2021). Design of titanium alloys by additive manufacturing: A critical review. Advanced Powder Materials, 1 (1), 100014. doi: https://doi.org/10.1016/j.apmate.2021.11.001
- Denkena, B., Jacob, S. (2015). Approach for increasing the resource efficiency for the production process of titanium structural components. Procedia CIRP, 35, 45–49. doi: https://doi.org/10.1016/j.procir.2015.08.054
- Xin, S., Zhang, J., Mao, X., Zhao, Y., Hong, Q. (2019). Research and Development of Low-cost Titanium Alloys. Journal of Physics: Conference Series, 1347 (1), 012022. doi: https://doi.org/10.1088/1742-6596/1347/1/012022
- Reddy, R. G., Shinde, P. S., Liu, A. (2021). Review – The Emerging Technologies for Producing Low-Cost Titanium. Journal of The Electrochemical Society, 168 (4), 042502. doi: https://doi.org/10.1149/1945-7111/abe50d
- Titanium Manufacturing Process. Available at: https://www.osaka-ti.co.jp/e/e_product/titan/
- Doblin, C., Chryss, A., Monch, A. (2012). Titanium powder from the TiRO™ process. Key Engineering Materials, 520, 95–100. doi: https://doi.org/10.4028/www.scientific.net/KEM.520.95
- van Vuuren, D. S. (2015). Direct titanium powder production by metallothermic processes. Titanium Powder Metallurgy, 69–93. doi: https://doi.org/10.1016/B978-0-12-800054-0.00005-8
- Hansen, D. A., Gerdemann, S. J. (1998). Producing titanium powder by continuous vapor-phase reduction. JOM, 50 (11), 56–58. doi: https://doi.org/10.1007/s11837-998-0289-3
- Chen, W., Yamamoto, Y., Peter, W. H. (2010). Investigation of pressing and sintering processes of CP-Ti powder made by Armstrong Process. Key Engineering Materials, 436, 123–130. doi: https://doi.org/10.4028/www.scientific.net/KEM.436.123
- El Khalloufi, M., Drevelle, O., Soucy, G. (2021). Titanium: An Overview of Resources and Production Methods. Minerals, 11, 1425. doi: https://doi.org/10.3390/min11121425
- Zhang, Y., Fang, Z. Z., Xia, Y., Huang, Z., Lefler, H., Zhang, T. et al. (2016). A novel chemical pathway for energy efficient production of Ti metal from upgraded titanium slag. Chemical Engineering Journal, 286, 517–527. doi: https://doi.org/10.1016/j.cej.2015.10.090
- Zhang, Y., Fang, Z. Z., Sun, P., Zheng, S., Xia, Y., Free, M. (2017). A perspective on thermochemical and electrochemical processes for titanium metal production. JOM, 69, 1861–1868. doi: https://doi.org/10.1007/s11837-017-2481-9
- Noguchi, H., Natsui, S., Kikuchi, T., Suzuki, R. O. (2018). Reduction of CaTiO3 by electrolysis in the molten salt CaCl2-CaO. Electrochemistry, 86 (2), 82–87. doi: https://doi.org/10.5796/electrochemistry.17-00078
- Yanko, T. B., Ovchinnikov, A. V., Lyutyk, N. P., Korzhyk, V. N. (2018). Technology for obtaining of plasma spheroidised HDH titanium alloy powders used in 3D printing. Technological systems, 85/4. doi: https://doi.org/10.29010/085.7
- Karaca, A., Sermond, B., Wilfing, G. (2008). Pat. No. US UA102387C2. Method for manufacturing alloy powders based on titanium, zirconium and hafnium, alloyed with elements Ni, Cu, Ta, W, Re, Os, and Ir. Available at: https://patents.google.com/patent/UA102387C2/en
- Buttner, G., Domazer, H.-G., Eggert, H. (1980). Pat. No. US 4373947A. Process for the preparation of alloy powders which can be sintered and which are based on titanium. Available at: https://patents.google.com/patent/US4373947A/de
- Moxson, V. S., Duz, V. A., Klevtsov, A. G., Sukhoplyuyev, V. D., Sopka, M. D., Shuvalov, Y. V., Matviychuk, M. (2012). Pat. No. US9067264B2. Method of manufacturing pure titanium hydride powder and alloyed titanium hydride powders by combined hydrogen-magnesium reduction of metal halides.
- Abayaweera, G., Amaratunga, G., Fernando, N., Karunaratne, V., Kottegoda, N., Ekanayake, R. (2016). Pat. No. US 10316391B2. Method of producing titanium from titanium oxides through magnesium vapour reduction. Available at: https://patents.google.com/patent/US10316391B2/en
- Bolivar, R., Friedrich, B. (2019). Magnesiothermic Reduction from Titanium Dioxide to Produce Titanium Powder. Journal of Sustainable Metallurgy, 5 (2), 219–229. doi: https://doi.org/10.1007/s40831-019-00215-z
- Bolívar, R., Friedrich, B. (2009). Synthesis of titanium via magnesiothermic reduction of TiO2 (Pigment). Proceedings - European Metallurgical Conference. doi: https://doi.org/10.13140/RG.2.2.11374.61760
- Kharytonov, V. M., Kharytonov, V. N., Kharytonov, D. V. (2020). Osoblyvosti khimichnoho skladu ilmenitu.
- Brodskyy, A., Troshchylo, V., Gonchar, A., Chukhmanov, O., Romanov, R. (2022). US Pat. No. 11440096 B2.
- Brodskyy, A., Troshchylo, V., Gonchar, A., Chukhmanov, O., Romanov, R. (2022). WO 2022/046020/A1.
- Mineral commodity summaries 2020. doi: https://doi.org/10.3133/mcs2020
- Cardarelli, F. (2008). Materials handbook: a concise desktop reference. Springer. doi: https://doi.org/10.1007/978-1-84628-669-8
- Ito, M., Morita, K. (2004). The solubility of MgO in molten MgCl2-CaCl2 salt. Materials transactions, 45 (8), 2712–2718. doi: https://doi.org/10.2320/matertrans.45.2712
- Chen, G. Z., Fray, D. J., Farthing, T. W. (2000). Direct electrochemical reduction of titanium dioxide to titanium in molten calcium chloride. Nature, 407 (6802), 361–364. https://doi.org/10.1038/35030069
- Dring, K. (2006). Electrochemical Reduction of Titanium Dioxide in Molten Calcium Chloride. Available at: http://hdl.handle.net/10044/1/8135
- Suzuki, R. O., Natsui, S., Kikuchi, T. (2020). OS process. Extractive Metallurgy of Titanium, 287–313. doi: https://doi.org/10.1016/b978-0-12-817200-1.00012-0
- Suzuki, R. O. (2005). Calciothermic reduction of TiO2 and in situ electrolysis of CaO in the molten CaCl2. Journal of Physics and Chemistry of Solids, 66 (2-4), 461–465. doi: https://doi.org/10.1016/j.jpcs.2004.06.041
- Fray, D. J., Chen, G. Z. (2001). The use of electro-deoxidation to reduce titanium dioxide and other metal oxides. Proceedings of the Fourth International Conference on Materials Engineering for Resources. Available at: https://nottingham-repository.worktribe.com/output/3214612
- Ono, K., Okabe, T., Ogawa, M., Suzuki, R. (1990). Production of titanium powders by the calciothermic reduction of TiO2. Tetsu-to-Hagane, 76 (4), 568–575. doi: https://doi.org/10.2355/tetsutohagane1955.76.4_568
- Sittig, C., Textor, M., Spencer, N. D., Wieland, M., Vallotton, P. H. (1999). Surface characterization. Journal of Materials Science: Materials in Medicine, 10 (1), 35–46. doi: https://doi.org/10.1023/a:1008840026907
- Prando, D., Brenna, A., Diamanti, M. V., Beretta, S., Bolzoni, F., Ormellese, M., Pedeferri, M. (2017). Corrosion of titanium: Part 2: Effects of surface treatments. Journal of Applied Biomaterials & Functional Materials, 16 (1), 3–13. doi: https://doi.org/10.5301/jabfm.5000396
- Fuentes, E., Alves, S., López-Ortega, A., Mendizabal, L., Sáenz de Viteri, V. (2019). Advanced Surface Treatments on Titanium and Titanium Alloys Focused on Electrochemical and Physical Technologies for Biomedical Applications. Biomaterial-Supported Tissue Reconstruction or Regeneration. doi: https://doi.org/10.5772/intechopen.85095
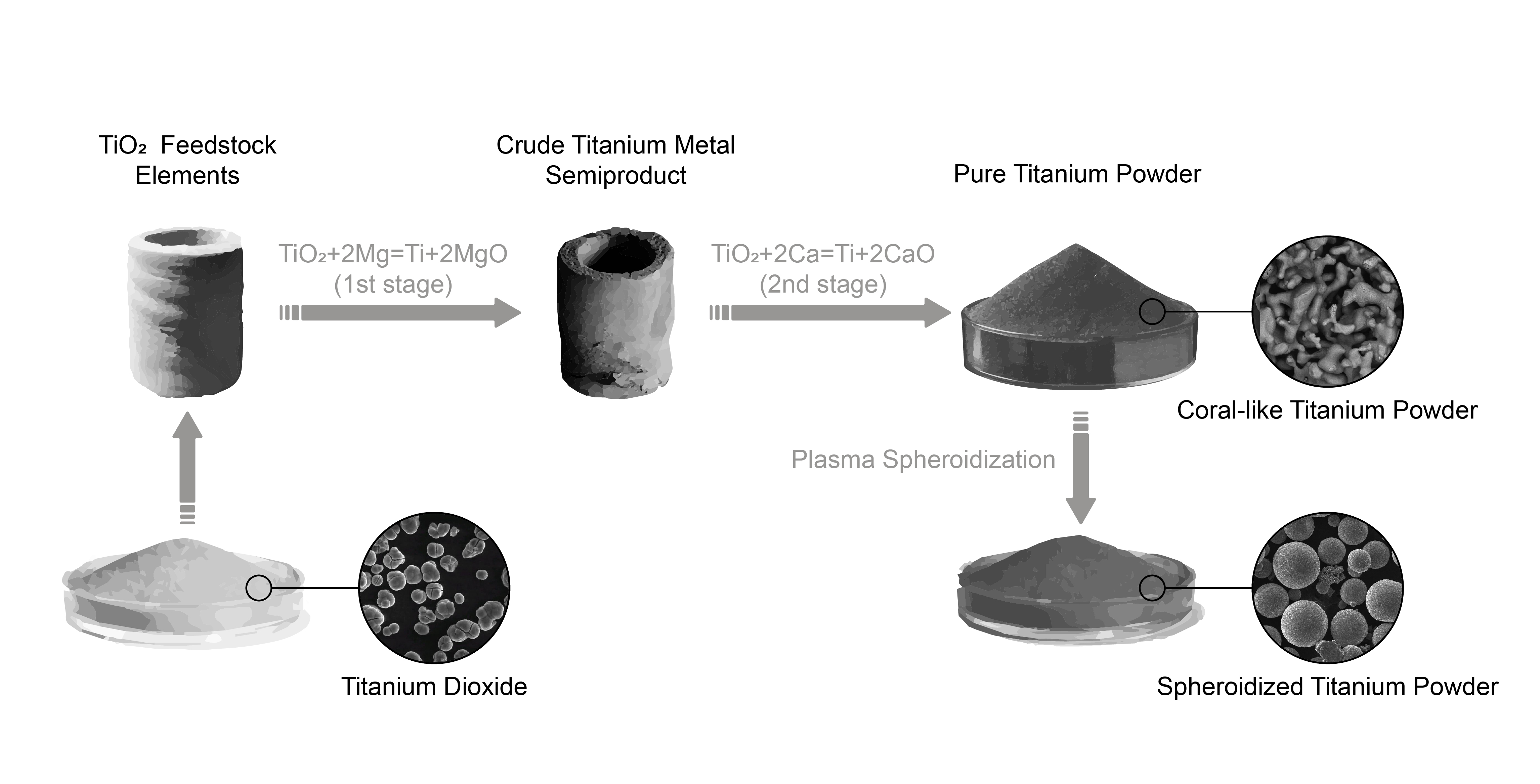
Downloads
Published
How to Cite
Issue
Section
License
Copyright (c) 2023 Andrii Gonchar, Viktor Troshchylo, Andriy Brodskyy, Volodymyr Yarovynskyi, Oleksandr Chukhmanov

This work is licensed under a Creative Commons Attribution 4.0 International License.
The consolidation and conditions for the transfer of copyright (identification of authorship) is carried out in the License Agreement. In particular, the authors reserve the right to the authorship of their manuscript and transfer the first publication of this work to the journal under the terms of the Creative Commons CC BY license. At the same time, they have the right to conclude on their own additional agreements concerning the non-exclusive distribution of the work in the form in which it was published by this journal, but provided that the link to the first publication of the article in this journal is preserved.
A license agreement is a document in which the author warrants that he/she owns all copyright for the work (manuscript, article, etc.).
The authors, signing the License Agreement with TECHNOLOGY CENTER PC, have all rights to the further use of their work, provided that they link to our edition in which the work was published.
According to the terms of the License Agreement, the Publisher TECHNOLOGY CENTER PC does not take away your copyrights and receives permission from the authors to use and dissemination of the publication through the world's scientific resources (own electronic resources, scientometric databases, repositories, libraries, etc.).
In the absence of a signed License Agreement or in the absence of this agreement of identifiers allowing to identify the identity of the author, the editors have no right to work with the manuscript.
It is important to remember that there is another type of agreement between authors and publishers – when copyright is transferred from the authors to the publisher. In this case, the authors lose ownership of their work and may not use it in any way.