Optimization of the technological process of threshing combine harvester
DOI:
https://doi.org/10.15587/1729-4061.2023.285697Keywords:
combine harvester, feeder house, technological process, optimization, working body, biomassAbstract
To improve the operational quality of paddy combine it was proposed to include additional innovative operations in plant process of pre-threshing preparation of rice biomass with anticipating seeds selection which increases seeds separation, reduces injuries, forms stable operation of threshing-separating device of combine harvester.
Retrofit feeder house is a solution to ensure the stable uniform feed of assorted biomass into the threshing separation device. Equipped with tool package – harvester feeder house turned to the running control equipment for incoming flow of biomass.
The movement of threshed heap inside the modified geometry of feeder house with tools effectively affect on caulis, panicle of rice – screed, and brings the biomass vibration mode i. e., lead to the dynamic separation of rice headed seeds to threshing rotor. Vibration (tossing) of biomass make it possible for free rice seeds pass through caulis to the bottom of feeder house.
Development program of innovative driving devices of multifunctional rice seed harvester combine considered the development of preproduction explorational program ensuring the information on harvest loss during various rice harvesting, their separation between main harvester aggregates – collector, auger, elevator, threshing mill. It is proposed to combine, in a single complex, all the control parameters, subordinating their actions, into an active control device of the technological process, affecting the shapes of rolls formed from various varieties and yields of rice
References
- Fu, J., Xie, G., Ji, C., Wang, W., Zhou, Y., Zhang, G. et al. (2021). Study on the Distribution Pattern of Threshed Mixture by Drum-Shape Bar-Tooth Longitudinal Axial Flow Threshing and Separating Device. Agriculture, 11 (8), 756. doi: https://doi.org/10.3390/agriculture11080756
- Hou, J., Li, C., Lou, W., Zhou, K., Li, Y., Li, T. (2023). Design and Test of Floating Clamping Device for Garlic Combine Harvester. Nongye Jixie Xuebao/Transactions of the Chinese Society of Agricultural Machinery, 54 (1). Available at: http://www.nyjxxb.net/index.php/journal/article/view/1533/
- Zhang, H., Tang, Z., Li, Y., Liu, X., Ren, H. (2020). Lightweight Threshing Rack under Multisource Excitation Based on Modal Optimization Method. Advances in Materials Science and Engineering, 2020, 1–17. doi: https://doi.org/10.1155/2020/2029501
- Tang, Z., Li, X., Chen, X., Chen, Y. (2019). Design of Negative Pressure Spiral Feeding Device for Tangential and Longitudinal Axial Intersection of Combine Harvester. Advances in Materials Science and Engineering, 2019, 1–12. doi: https://doi.org/10.1155/2019/1647230
- Chen, S., Zhou, Y., Tang, Z., Lu, S. (2020). Modal vibration response of rice combine harvester frame under multi-source excitation. Biosystems Engineering, 194, 177–195. doi: https://doi.org/10.1016/j.biosystemseng.2020.04.002
- Hrynkiv, A., Rogovskii, I., Aulin, V., Lysenko, S., Titova, L., Zagurskiy, O., Kolosok, I. (2020). Development of a system for determining the informativeness of the diagnosing parameters for a cylinderpiston group in the diesel engine during operation. Eastern-European Journal of Enterprise Technologies, 3 (5 (105)), 19–29. doi: https://doi.org/10.15587/1729-4061.2020.206073
- Mirzazadeh, A., Abdollahpour, S., Mahmoudi, A., Ramazani, B. (2012). Intelligent modeling of material separation in combine harvester’s thresher by ANN. International Journal of Agriculture and Crop Sciences, 4 (23), 1767–1777. Available at: https://www.researchgate.net/publication/302498474_Intelligent_modeling_of_material_separation_in_combine_harvester's_thresher_by_ANN
- Liang, Z., Li, Y., Xu, L. (2018). Grain Sieve Loss Fuzzy Control System in Rice Combine Harvesters. Applied Sciences, 9 (1), 114. doi: https://doi.org/10.3390/app9010114
- Burlaka, O. A., Yakhin, S. V., Padalka, V. V., Burlaka, A. О. (2021). 100 tons per hour, what is next? Let us compare and analyze characteristics of the latest models of highly productive combine harvesters. Bulletin of Poltava State Agrarian Academy, 3, 274–288. doi: https://doi.org/10.31210/visnyk2021.03.34
- Yakhin, S. V., Burlaka, O. A. (2020). Research on the influence of the operating modes of combine harvester’s transportation lines on the quality of grain threshing. Bulletin of Poltava State Agrarian Academy, 3, 269–279. doi: https://doi.org/10.31210/visnyk2020.03.31
- Pat. No. 19347 KZ (2008). Feeder house rice grain harvester. published: 15.05.2008, Bul. No. 5.
- Rogovskii, I. L., Martiniuk, D. I., Voinash, S. A., Luchinovich, A. A., Sokolova, V. A., Ivanov, A. M., Churakov, A. V. (2021). Modeling the throughput capacity of threshing-separating apparatus of grain harvester’s combines. IOP Conference Series: Earth and Environmental Science, 677 (4), 042098. doi: https://doi.org/10.1088/1755-1315/677/4/042098
- Li, F., Li, Y. M. (2015). Optimization and simulation research of the airway of tangential-axial combine Harvester cleaning room. J. Agric. Mech. Res., 2, 75–78.
- Sadykov, Zh. S., Espolov, T. I. et al. (2008). Pat. No. 19347 KZ. Method for determining the coefficient of biomass leveling and a device for its implementation. published: 25.03.2008.
- Xiao, Y., Wang, S., Liao, M., Liang, J., Zhang, J. (2016). Simulation Analysis on Airflow Field of Plot Harvester. Proceedings of the 2016 International Conference on Mechatronics Engineering and Information Technology. doi: https://doi.org/10.2991/icmeit-16.2016.10
- Du, X., Ni, K., Chen, J., Wu, C., Zhao, Y. (2013). Numerical Simulation and Experiment of Gas-solid Two-phase Flow in a Cross-flow Grain Cleaning Device. Nongye Gongcheng Xuebao/Transactions of the Chinese Society of Agricultural Engineering. doi: https://doi.org/10.13031/aim.20131586235
- Levchenko, I., Hradovych, N., Borkovska, V., Britchenko, I. (2022). Devising a procedure of state financial protectionism in the agricultural industry in the context of regionalization. Eastern-European Journal of Enterprise Technologies, 2 (13 (116)), 6–14. doi: https://doi.org/10.15587/1729-4061.2022.255045
- Liang, Z., Li, Y., De Baerdemaeker, J., Xu, L., Saeys, W. (2019). Development and testing of a multi-duct cleaning device for tangential-longitudinal flow rice combine harvesters. Biosystems Engineering, 182, 95–106. doi: https://doi.org/10.1016/j.biosystemseng.2019.04.004
- Umbetkulov, Y., Yeleukulov, Y., Atalykova, A., Smailova, G., Iskakova, G., Zhauyt, A., Ibrayev, G.-G. A. (2018). Dynamic force analysis of a six-link planar mechanism. MATEC Web of Conferences, 251, 04028. doi: https://doi.org/10.1051/matecconf/201825104028
- Tang, Z., Li, Y., Li, X., Xu, T. (2019). Structural damage modes for rice stalks undergoing threshing. Biosystems Engineering, 186, 323–336. doi: https://doi.org/10.1016/j.biosystemseng.2019.08.005
- Umbetaliev, N. A., Seytimov, S., Kulshikova, E. S., Bayzakova, Zh. S. (2018). Controlling the technological process of harvesting rice. Internauka: electronic scientific journal, 43 (77).
- Utepov, E. B., Ten, E. B., Zhumadilova, Zh. O., Smailova, G. A., Shevtsova, V. S., Abuova, R. Zh., Isakhanova, A. B. (2017). Damping Metallic Materials with a Nanostructured Coating. Metallurgist, 60 (9-10), 961–966. doi: https://doi.org/10.1007/s11015-017-0392-1
- Biaou, O, Moreira, J, Hounhouigan, J., Amponsah, S. (2016). Effect of threshing drum speed and crop weight on paddy grain quality in axial- flow thresher (ASI). Journal of Multidisciplinary Engineering Science and Technology, 3 (1), 3716–3721. Available at: https://www.researchgate.net/publication/305618996_Effect_Of_Threshing_Drum_Speed_And_Crop_Weight_On_Paddy_Grain_Quality_In_Axial-_Flow_Thresher_ASI
- Gbabo, A., Gana, I. M., Amoto, M. S. (2013). Design, fabrication and testing of a millet thresher. Net Journal of Agricultural Science, 1 (4), 100–106. Available at: https://www.netjournals.org/z_NJAS_13_033.html
- Sessiz, A. et al. (2021). Performance Evaluation of Axial-Flow and Tangential Flow Threshing Units For Rice. 11th International Congress on echanization and Energy in Agriculture. Istanbul. Available at: https://www.researchgate.net/publication/301296333_Performance_Evaluation_of_Axial-Flow_and_Tangential_Flow_Threshing_Units_For_Rice
- Umbetaliev, N. A. (2010). Test results of the modernized rice harvester. Bulletin of Science of the Kazakh Agrotechnical University named after. S. Seifullina, 1 (58), 142–145.
- Guo, X. F., Wang, W. B., Guo, S. L., Chen, S. J. (2018). Modal analysis and experimental research on potato harvester rack. Mechanical Design & Manufacturing, 7, 154–157.
- Abdeen, M. A., Salem, A. E., Zhang, G. (2021). Longitudinal Axial Flow Rice Thresher Performance Optimization Using the Taguchi Technique. Agriculture, 11 (2), 88. doi: https://doi.org/10.3390/agriculture11020088
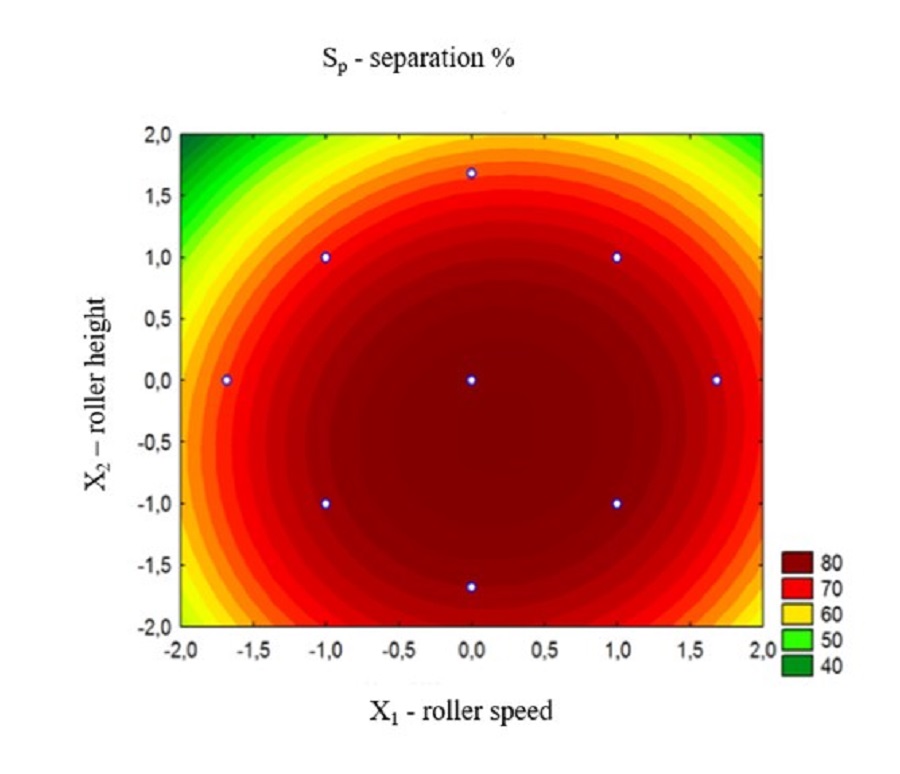
Downloads
Published
How to Cite
Issue
Section
License
Copyright (c) 2023 Nukhtar Umbataliyev, Gulbarshyn Smailova, Meirambay Toilybayev, Kazybek Sansyzbayev, Sholpan Koshanova, Sholpan Bekmukhanbetova

This work is licensed under a Creative Commons Attribution 4.0 International License.
The consolidation and conditions for the transfer of copyright (identification of authorship) is carried out in the License Agreement. In particular, the authors reserve the right to the authorship of their manuscript and transfer the first publication of this work to the journal under the terms of the Creative Commons CC BY license. At the same time, they have the right to conclude on their own additional agreements concerning the non-exclusive distribution of the work in the form in which it was published by this journal, but provided that the link to the first publication of the article in this journal is preserved.
A license agreement is a document in which the author warrants that he/she owns all copyright for the work (manuscript, article, etc.).
The authors, signing the License Agreement with TECHNOLOGY CENTER PC, have all rights to the further use of their work, provided that they link to our edition in which the work was published.
According to the terms of the License Agreement, the Publisher TECHNOLOGY CENTER PC does not take away your copyrights and receives permission from the authors to use and dissemination of the publication through the world's scientific resources (own electronic resources, scientometric databases, repositories, libraries, etc.).
In the absence of a signed License Agreement or in the absence of this agreement of identifiers allowing to identify the identity of the author, the editors have no right to work with the manuscript.
It is important to remember that there is another type of agreement between authors and publishers – when copyright is transferred from the authors to the publisher. In this case, the authors lose ownership of their work and may not use it in any way.