Devising a methodology for prototyping convex-concave parts using reverse-engineering technology providing the predefined geometric accuracy of their manufacturing
DOI:
https://doi.org/10.15587/1729-4061.2024.308047Keywords:
reverse engineering, methodology, parts, digital layout, 3D scanning, 3D printing, geometric accuracyAbstract
The object of this paper is the geometric accuracy of the acquired portrait from the 3D printed full-scale sample in the reduced size of the convex-concave parts compared to the correspondingly reduced ideal one.
The subject of research is reverse engineering and additive technology for manufacturing convex-concave parts for mechanical engineering (ME). A new prototyping methodology for convex-concave parts of mechanical engineering objects has proposed. Underlying the methodology is the use of the scaled (by reducing in size) ideal portrait of the 3D scanned original part. The decision to start the production is made by comparing the geometry of the portrait acquired from the 3D printed sample in reduced size with the ideal one, provided that the values are within the tolerance range. The following results were obtained. A design and technological analysis of the blade of the pumped hydroelectric power station was performed, after which a 3D scanner and a 3D printer were selected. A 3D scan of the blade with the formation of a portrait in the STL format file was implemented, as well as its refinement into an ideal one. From the geometric features and shapes of the blade, as well as the technical characteristics of the 3D printer, the percentage of reducing the sample for printing (by 75 % of the original dimensions) was calculated. According to the rated dimensions of the original part and the reduced sample, the tolerance field was set for the size: 0.6 mm and 0.25 mm, respectively, at 12 quality of the part’s manufacturing accuracy. Inspection of the printed sample and comparison with the correspondingly reduced ideal portrait revealed a deviation from –0.123 to +0.120 mm, which is within the defined tolerance field for the manufactured reduced sample. The results of experimental studies confirmed the adequacy of the proposed methodology for prototyping the mechanical engineering parts and verified the theoretical foundations of reverse engineering for convex-concave parts of any large size by using a proportional reduction in the size of finished portraits
References
- Javaid, M., Haleem, A., Pratap Singh, R., Suman, R. (2021). Industrial perspectives of 3D scanning: Features, roles and it’s analytical applications. Sensors International, 2, 100114. https://doi.org/10.1016/j.sintl.2021.100114
- Helle, R. H., Lemu, H. G. (2021). A case study on use of 3D scanning for reverse engineering and quality control. Materials Today: Proceedings, 45, 5255–5262. https://doi.org/10.1016/j.matpr.2021.01.828
- Buonamici, F., Carfagni, M., Furferi, R., Governi, L., Lapini, A., Volpe, Y. (2017). Reverse engineering modeling methods and tools: a survey. Computer-Aided Design and Applications, 15 (3), 443–464. https://doi.org/10.1080/16864360.2017.1397894
- Maiorova, K., Sikulskyi, V., Vorobiov, I., Kapinus, O., Knyr, A. (2023). Study of a Geometry Accuracy of the Bracket-Type Parts Using Reverse Engineering and Additive Manufacturing Technologies. Lecture Notes in Networks and Systems, 146–158. https://doi.org/10.1007/978-3-031-36201-9_13
- Tretiak, O., Serhiienko, S., Zhukov, A., Gakal, P., Don, Y., Arefieva, M. et al. (2023). Peculiarities of the Design of Housing Parts of Large Direct Current Machines. SAE International Journal of Materials and Manufacturing, 17 (1). https://doi.org/10.4271/05-17-01-0005
- Tretiak, O., Kritskiy, D., Kobzar, I., Arefieva, M., Nazarenko, V. (2022). The Methods of Three-Dimensional Modeling of the Hydrogenerator Thrust Bearing. Computation, 10 (9), 152. https://doi.org/10.3390/computation10090152
- Ward, R., Sun, C., Dominguez-Caballero, J., Ojo, S., Ayvar-Soberanis, S., Curtis, D., Ozturk, E. (2021). Machining Digital Twin using real-time model-based simulations and lookahead function for closed loop machining control. The International Journal of Advanced Manufacturing Technology, 117 (11-12), 3615–3629. https://doi.org/10.1007/s00170-021-07867-w
- Pliuhin, V., Zaklinskyy, S., Plankovskyy, S., Tsegelnyk, Y., Aksonov, O., Kombarov, V. (2023). A digital twin design of induction motor with squirrel-cage rotor for insulation condition prediction. International Journal of Mechatronics and Applied Mechanics, 14, 185–191. https://doi.org/10.17683/ijomam/issue14.22
- Sikulskyi, V., Maiorova, K., Shypul, O., Nikichanov, V., Tryfonov, O., Voronko, I., Kapinus, O. (2024). Algorithm for Selecting the Optimal Technology for Rapid Manufacturing and/or Repair of Parts. Integrated Computer Technologies in Mechanical Engineering - 2023. https://doi.org/10.1007/978-3-031-61415-6_3
- Lazarević, D., Nedić, B., Jović, S., Šarkoćević, Ž., Blagojević, M. (2019). Optical inspection of cutting parts by 3D scanning. Physica A: Statistical Mechanics and Its Applications, 531, 121583. https://doi.org/10.1016/j.physa.2019.121583
- Zong, Y., Liang, J., Pai, W., Ye, M., Ren, M., Zhao, J. et al. (2022). A high-efficiency and high-precision automatic 3D scanning system for industrial parts based on a scanning path planning algorithm. Optics and Lasers in Engineering, 158, 107176. https://doi.org/10.1016/j.optlaseng.2022.107176
- Vorobiov, I., Maiorova, K., Voronko, I., Skyba, O., Komisarov, O. (2024). Mathematical models creation for calculating dimensional accuracy at the construction stages of an analytical standard using the chain method. Technology Audit and Production Reserves, 1 (1 (75)), 26–34. https://doi.org/10.15587/2706-5448.2024.297732
- Saiga, K., Ullah, A. S., Kubo, A., Tashi. (2021). A Sustainable Reverse Engineering Process. Procedia CIRP, 98, 517–522. https://doi.org/10.1016/j.procir.2021.01.144
- Maiorova, K., Kapinus, O., Skyba, O. (2024). Study of the features of permanent and usual reverse-engineering methods of details of complex shapes. Technology Audit and Production Reserves, 1 (1 (75)), 19–25. https://doi.org/10.15587/2706-5448.2024.297768
- Durupt, A., Bricogne, M., Remy, S., Troussier, N., Rowson, H., Belkadi, F. (2018). An extended framework for knowledge modelling and reuse in reverse engineering projects. Proceedings of the Institution of Mechanical Engineers, Part B: Journal of Engineering Manufacture, 233 (5), 1377–1389. https://doi.org/10.1177/0954405418789973
- Montlahuc, J., Ali Shah, G., Polette, A., Pernot, J.-P. (2019). As-scanned Point Clouds Generation for Virtual Reverse Engineer-ing of CAD Assembly Models. Computer-Aided Design and Applications, 16 (6), 1171–1182. https://doi.org/10.14733/cadaps.2019.1171-1182
- Kyaw, A. C., Nagengast, N., Usma-Mansfield, C., Fuss, F. K. (2023). A Combined Reverse Engineering and Multi-Criteria Decision-Making Approach for Remanufacturing a Classic Car Part. Procedia CIRP, 119, 222–228. https://doi.org/10.1016/j.procir.2023.02.133
- Loska, A., Palka, D., Bień, A., Substelny, K. (2022). A way of supporting the servicing of production machines using reverse engineering and 3d printing techniques. Technologia i Automatyzacja Montażu, 1, 28–36. https://doi.org/10.7862/tiam.2022.1.3
- Childs, P. R. N. (2019). Mechanical Design Engineering Handbook. Butterworth-Heinemann. https://doi.org/10.1016/c2016-0-05252-x
- Stark, R. (2022). Major Technology 6: Digital Mock-Up – DMU. Virtual Product Creation in Industry, 273–304. https://doi.org/10.1007/978-3-662-64301-3_12
- Technical specifications. Artec Leo. Available at: https://www.artec3d.com/portable-3d-scanners/artec-spider#specifications
- Agoston, M. K. (2005). Springer Computer Graphics and Geometric Modeling. Springer-Verlag. https://doi.org/10.1007/b138805
- Langetepe, E., Zachmann, G. (2006). Geometric Data Structures for Computer Graphics. A K Peters/CRC Press. https://doi.org/10.1201/9780367803735
- Zhang, C., Pinquié, R., Polette, A., Carasi, G., De Charnace, H., Pernot, J.-P. (2023). Automatic 3D CAD models reconstruction from 2D orthographic drawings. Computers & Graphics, 114, 179–189. https://doi.org/10.1016/j.cag.2023.05.021
- Agarwal, P. K., Arge, L., Danner, A. (2006). From Point Cloud to Grid DEM: A Scalable Approach. Progress in Spatial Data Handling, 771–788. https://doi.org/10.1007/3-540-35589-8_48
- D Printer Creatbot F430. Available at: https://3ddevice.com.ua/en/product/3d-printer-creatbot-f430/
- Pajerová, N., Koptiš, M. (2024). Shape functions to scanner comparison. The International Journal of Advanced Manufacturing Technology, 132 (7-8), 3889–3902. https://doi.org/10.1007/s00170-024-13520-z
- Sullivan, J. M. (2008). Curvatures of Smooth and Discrete Surfaces. Oberwolfach Seminars, 175–188. https://doi.org/10.1007/978-3-7643-8621-4_9
- Burns, M. (1993). Automated Fabrication: Improving Productivity in Manufacturing. Prentice Hall.
- Szilvśi-Nagy, M., Mátyási, Gy. (2003). Analysis of STL files. Mathematical and Computer Modelling, 38 (7-9), 945–960. https://doi.org/10.1016/s0895-7177(03)90079-3
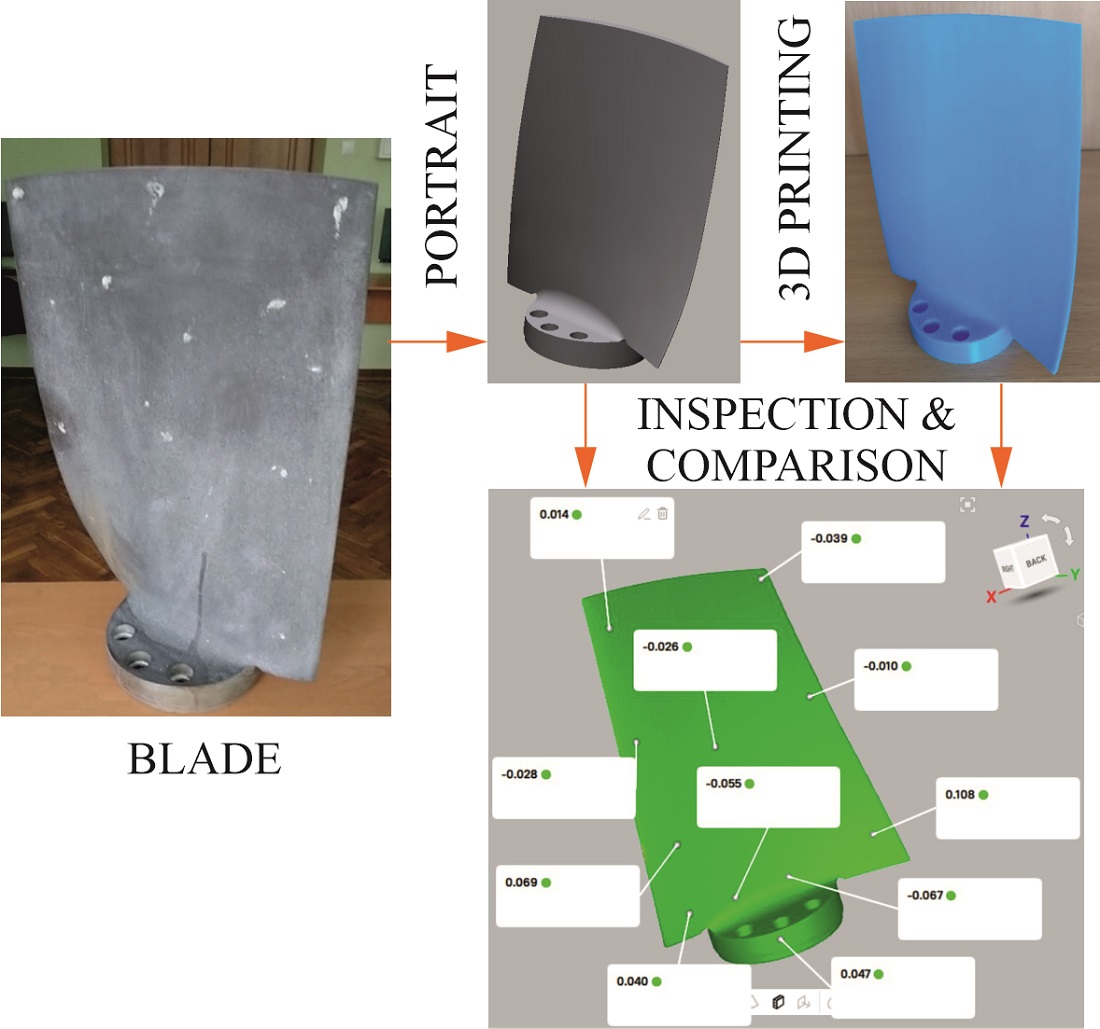
Downloads
Published
How to Cite
Issue
Section
License
Copyright (c) 2024 Kateryna Maiorova, Oleksandra Kapinus, Viacheslav Nikichanov, Oleksandr Skyba, Artem Suslov

This work is licensed under a Creative Commons Attribution 4.0 International License.
The consolidation and conditions for the transfer of copyright (identification of authorship) is carried out in the License Agreement. In particular, the authors reserve the right to the authorship of their manuscript and transfer the first publication of this work to the journal under the terms of the Creative Commons CC BY license. At the same time, they have the right to conclude on their own additional agreements concerning the non-exclusive distribution of the work in the form in which it was published by this journal, but provided that the link to the first publication of the article in this journal is preserved.
A license agreement is a document in which the author warrants that he/she owns all copyright for the work (manuscript, article, etc.).
The authors, signing the License Agreement with TECHNOLOGY CENTER PC, have all rights to the further use of their work, provided that they link to our edition in which the work was published.
According to the terms of the License Agreement, the Publisher TECHNOLOGY CENTER PC does not take away your copyrights and receives permission from the authors to use and dissemination of the publication through the world's scientific resources (own electronic resources, scientometric databases, repositories, libraries, etc.).
In the absence of a signed License Agreement or in the absence of this agreement of identifiers allowing to identify the identity of the author, the editors have no right to work with the manuscript.
It is important to remember that there is another type of agreement between authors and publishers – when copyright is transferred from the authors to the publisher. In this case, the authors lose ownership of their work and may not use it in any way.